- 1Fraunhofer Institute for Process Engineering and Packaging IVV, Freising, Germany
- 2Faculty of Life Sciences, Albstadt-Sigmaringen University, Sigmaringen, Germany
Chemical grafting with fatty acid chlorides is known to reduce the surface energy of polymer substrates. The aim of this study was to evaluate the effect of different grafting parameters on functional properties such as the surface energy of grafted substrates and adhesion of acrylic pressure sensitive adhesives (PSA) on those substrates in dependence of storage time. Therefore, two substrates, paper and polyethylene terephthalate (PET), were coated with polyvinyl alcohol (PVOH). The PVOH showed similar degrees of hydrolysis but different molecular weights. Fatty acid chlorides (palmitoyl chloride, stearoyl chloride) were grafted on pure PET, pure paper, PVOH coated paper, and PVOH coated PET. On these samples, roughness was measured and peel strength and surface energy were determined over storage time. Peel strength was observed to increase with roughness. The chain length of fatty acid chlorides and storage time did not majorly influence peel strength.
Introduction
The chemical grafting method used here is based on the esterification of fatty acid chlorides with hydroxyl groups under gaseous conditions. In the present study, the hydroxyl groups are provided by either cellulosic fibers or a polyvinyl alcohol (PVOH) layer. During the esterification of the carbonyl group of a fatty acid chloride with the hydroxyl group, hydrogen chloride is formed (Stinga, 2008). Further detailed information about chemical grafting can be found in different previously published studies (Stinga, 2008; Schmid et al., 2012).
Chemical grafting is one method to achieve hydrophobic surfaces and a low surface energy (Stinga, 2008). A low surface energy (and especially low polar contributions to it), is reported to affect peel strength toward the PSA of the top liner (Mangipudi et al., 1994; Owen, 1998; Madeira et al., 2018), especially for polar acrylic pressure sensitive adhesives (Figure 1) (Kowalski et al., 2013). Therefore, grafting of fatty acids might be a suitable treatment for paper and PET to be used as release liners for PSAs. However, low surface energy alone does not guarantee perfect release performance. Other important factors influencing adhesion and peel strength (which were not further evaluated in this study) are fluidity, strength and exact chemical composition of the release agent as well as roughness, modulus and flexibility of the substrate, peel velocity, and peel geometry (Newby et al., 1995; Zhang Newby and Chaudhury, 1997; Gordon et al., 1998; Hose, 2007; Mohammed et al., 2016).
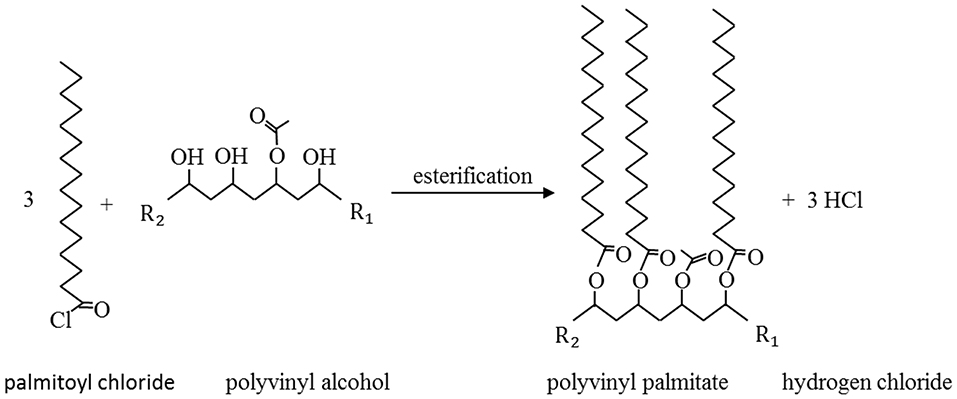
Figure 1. Esterification of palmitoyl chloride and polyvinyl alcohol. R1 and R2 illustrate the continuation of PVOH chain. Adapted from Haas et al. (2017).
Release liners protect the sticky PSA, which is attached to the top liner, from dirt and humidity until its application (Figure 2). As release liners are single use materials, they are typically thrown away after their use. Attempts to feed materials back into the recycling stream are ongoing (FINAT, 2017). However, the recycling process of release liners is costly (Laufenberg GmbH, 2017), requires decent presorting in order to generate high-quality recycled materials and also separation steps to delaminate different layers (Kaiser et al., 2018). Therefore, silicone release liners are partially incinerated or landfilled.
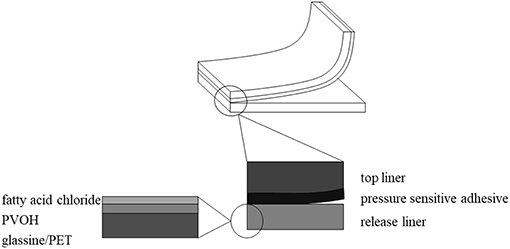
Figure 2. Schematic representation of a structure showing top liner, pressure sensitive adhesive, and a release liner. The zoom in on the left shows the structure of the release liner varying in substrate type, PVOH type and fatty acid chloride chain length.
In this study the applicability of two substrates, PET and glassine, in combination with grafted fatty acids as possible release liner materials is tested. Glassine is a renewable, biodegradable and recyclable raw material (CPI: Confederation of Paper Industries, 2019). PET also can potentially biodegrade (Yoshida et al., 2016) and can definitely be recycled at low cost (Awaja and Pavel, 2005). The grafting of fatty acids can be directly done on the substrate or on an intermediate PVOH layer. By applying fatty acid chlorides through chemical grafting on both substrates, the silicone layer could be replaced and therefore the recycling process could possibly be eased.
Various studies were carried out in order to find grafting parameters, which decrease surface energy and increase hydrophobicity. It was shown that an increasing grafting temperature and an increasing degree of PVOH hydrolysis decrease the surface energy (Schmid et al., 2012) and that a longer fatty acid chain leads to greater hydrophobicity (Schmid et al., 2014). In 2018 a patent about the inhibition of discoloration of PVOH coated, grafted papers was published and is still active (KNU Industry Cooperation Foundation, 2018). In this patent, paper as a substrate with a PVOH coating was grafted with fatty acid chloride as well.
In this study, the influence of different parameters on the peel strength and the surface energy was analyzed. The different parameters are: type of substrate, presence of a PVOH layer, type of PVOH (degree of hydrolysis and molecular weight), length of fatty acid chain, type of PSA (pt or pp) and storage time.
The following experimental design shows the different variations and also explains the abbreviations used in this publication. Two different substrates (S) were used: Glassine and PET. On this, PVOH coatings (C) were applied: The first number in Kuraray Poval 28-99 and 4-98 describes the viscosity (mPa·s) at 4% w/w concentration and 20°C and the second one the degree of hydrolysis of polyvinyl acetate. The grafting process was performed with two fatty acid chlorides (FA): C16 and C18 (palmitoyl and stearoyl chloride). Finally, two acrylic commercially available model PSAs were applied, that are commonly used as e.g., address labels: pt and pp (perfect tack and perfect peel) (Figure 3).
Materials and Methods
Chemicals
Palmitoyl chloride (C16) and stearoyl chloride (C18) were purchased from Merck KGaA (Darmstadt, Germany) and TCI Deutschland GmbH (Eschborn, Germany) in order to generate a solution with petroleum ether [boiling point 40–60°C (1,013 hPa)] (Merck KGaA, Darmstadt, Germany). For the coating two types of PVOH, Kuraray Poval 28-99 and Kuraray Poval 4-98, were kindly provided by Kuraray Europe GmbH (Frankfurt/Main, Germany).
Preparation of Aqueous PVOH Solution
For the preparation of a PVOH solution, 15 and 10% w/w, respectively of the PVOH granulate (Kuraray Poval 4-98 and Kuraray Poval 28-99), was poured into a high performance disperser (Thermomix TM31 supplied by Vorwerk & Co. KG, Wuppertal, Germany) together with distilled water and mixed at 500 rpm. Then, the solution was heated up for 40 min at 90°C at 500 rpm. For cooling down, the speed was set at 300 rpm until room temperature is reached. Afterwards the solution was treated in an ultrasonic bath to reduce foam. For storage, the solution was kept in a glass bottle at 8°C.
PVOH Coating
The PVOH solution was applied to the substrate by a rod coater CUF5 from Sumet Systems GmbH (Denklingen, Germany). Glassine (40 g/m2) was kindly provided by HERA Papierverarbeitung GmbH & Co. KG (Nidda, Germany). The polyethylene terephthalate film (Hostaphan, 12 μm) was purchased from Mitsubishi Polyester Film GmbH (Wiesbaden, Germany) and was Corona treated prior to PVOH coating. After fixing the rod on the substrate, 4 ml of PVOH solution were distributed on the substrate along the rod using a pipette. The substrate was coated at a speed of 4 m/min causing the solution to distribute all over the substrate. The application pressure was 40 N and the dryer was set at 115°C for 6 min.
Determination of Optimum PVOH Layer Thickness and Concentration of PVOH Solution
As different rods generate different PVOH layer thicknesses, pre-tests were made in order to find the minimum rod size, with which a homogenous and leak-proof surface can be achieved on paper. For Kuraray Poval 4-98 and 28-99 two different rod sizes (0.33 and 0.45) were tested. Rod size 0.33 generates a wet film layer of ~33 μm and rod size 0.45 a wet film layer of ~51 μm. The samples produced with these rod sizes were analyzed by using the standard staining test: On each DIN A4-sized sample, five squares (7.5 × 7.5 cm) were coated with Sudan red-colored peanut oil and covered with two layers of oil-soaked kitchen paper. The samples were stored for 24 h at 23°C and 50% relative humidity. Defects in the PVOH coating allow the colored peanut oil to diffuse through the coating, which can be easily visually checked. It was found that optimum results can be obtained with Kuraray Poval 4-98 set at 15% w/w with rod size 0.45 and Kuraray Poval 28-99 at 10% w/w and rod size 0.45.
Preparation of Fatty Acid Chloride Solution
A ratio of 5% w/w fatty acid chloride and 95% w/w petroleum ether were mixed together in a glass basin and stored in a clean container in a fridge at 8°C.
Chemical Grafting by Transfer Method
The transfer method for grafting sheets was first introduced by Stinga (2008) and was further described in several studies (Schmid et al., 2012, 2014). Filter paper No. 2 from Whatman GmbH (Dassel, Germany) was immersed into the fatty acid chloride solution twice and then dried for 2 min under a hood. Meanwhile the PVOH coated substrate was laid down onto a stainless steel platter with the coated side up. Then the dried filter paper was put on top of it and was fixed with a clip on each side. This assembly was now put into an oven from Heraeus Holding GmbH (Hanau, Germany). The grafting parameters were adapted to the fatty acid chloride: For palmityol chloride (C16) conditions were set at 150°C for 10 min. For making up stearoyl chloride's (C18) higher boiling point and lower vapor pressure, conditions were set at a higher temperature for a shorter period of time: 170°C for 8 min.
Chemical Grafting by Direct Method
The direct method is applicable for substrates having hydroxyl groups on their surface, for example paper. The paper was then directly immerged into the solution without using a filter paper. The rest of the procedure was the same as described in section Chemical Grafting by Transfer Method.
Determination of Surface Energy
Surface energy was measured according to DIN 55660-2 (Deutsches Institut für Normung, 2011). Used test liquids were water, diiodmethane and ethylene glycol. The droplet volume was set at 3 μl. For every test liquid, measuring was done at five different points of the sample. The analyzer DSA 100 (Krüss GmbH, Hamburg, Germany) measures the contact angle by tangent-1 method. The surface energy and disperse and polar parts were calculated by Owens-Wendt-Rabel-and-Kaelble (OWRK) method (Deutsches Institut für Normung, 2011). Measuring was done once a week for a period of 3 weeks.
Determination of Peel Strength
The two substrates, glassine and PET, were laminated with two different types of label. The labels, Premium and Special, were purchased from HERMA GmbH (Filderstadt, Germany), providing either “perfect tack” (pt) or “perfect peel” (pp) (HERMA GmbH, 2014a,b). In the following, the two types of labels are referred to as pt and pp, respectively. As benchmark release liners, a PET release liner provided by HERMA GmbH (Filderstadt, Germany) and the original release liners of pp and pt were used.
For applying the labels on the substrate a hard rubber roller was used to eliminate bubbles in between the label and the release liner. The substrate was then cut into stripes with a width of 15 mm. The upper 4 cm of the stripe were ultimately detached and pulled apart as preparation for the following testing. The samples were stored at 25°C and relative humidity of 50% (Deutsches Institut für Normung, 2017).
For each variation (S/C/FA/ PSA) five samples were measured. Coated samples without grafting were not analyzed because the study focused on differences within grafted samples and not the difference between grafted and ungrafted. Measuring was done with the tensile testing machine from Doli Elektronik GmbH (München, Germany) according to DIN 55543-5 (Deutsches Institut für Normung, 2017). The release liner was fixed at the upper clamp and the label at the lower clamp. The test device was equipped with a 50 N load cell and peel velocity was set at 50 mm/min and measuring length at 50 mm. During testing, the strip was held with tweezers so that a 90° angle was ensured during the measurement. The adhesion strength was measured at day 1, 2, 3, 7/8, and 20/21 with day 1 being 1 day after the top liner was placed on the release liner.
Determination of Roughness
For measuring roughness Rq (root-mean-square roughness) (Carl Zeiss Industrielle Messtechnik GmbH, 2016), the Hommel Tester W55 from Jenoptik Metrology Germany GmbH (Villingen-Schwenningen, Germany) was used. As the chain length of fatty acid chlorides does not influence roughness, due to its size in nanometer scale (Haas et al., 2017), only variations with one type of FA (C16) were tested. Consequently, for each, PET and glassine, the roughness of three variations was measured (noPVOH, 28-99, 4-98). The measuring interval was set to be 5 mm with a cut off length c of 0.8. For each variation, five measurements in machine and cross direction were carried out.
Determination of Thickness
Sample preparation was done with a microtome cutter (Autocut 2055 from Leica Microsystems GmbH, Wetzlar, Germany) cutting samples into slices in profile. Samples were analyzed with a light microscope (DFC295 from Leica Microsystems GmbH, Wetzlar, Germany) looking at structure and thickness of layers.
Determination of Surface Weight
Samples were stored at 50% RH and 23°C for 24 h before measurement. Measurement of surface weight was done by scaling 10 cm2 sized PVOH coated and uncoated samples with an analytical balance (DFC295 from Sartorius AG, Göttingen, Germany). The weight of the PVOH layer was calculated as the differenct between the area weight of the coated and uncoated sample. Surface weight is given in g/m2.
Statistical Evaluation
In order to analyze the measurement results, means and standard deviations were calculated. For evaluating the influence of peel strength over storage time, the results were checked for homogenity of variance according to Levene-Test and for normal distribution according Kolmogorov-Smirnov (α = 0.05) (Feldman and Valdez-Flores, 2009). To compare two means of independent samples with same parameters, a two-sample t-test was carried out (p-value: 0.05) by using Visual Xsel 13.0 software (CRGRAPH GbR, Starnberg, Germany).
Results and Discussion
Thickness and Coating Weight of PVOH Layer
The thickness of PET substrate was ~12 μm, whereas glassine varies from 34 to 43 μm (Tables 1, 2). The thickness of PVOH layer on glassine was ~3–5 μm and PET ~2–3 μm. This is due to inter-fiber voids absorbing a huge amount of PVOH in the case of glassine.
Alteration of Surface Energy
Surface energy was measured on PET/FA and G/FA over storage time (Figure 4 and Supplementary Tables 1, 2). For each substrate (S) there are six different variations differing in coating (C) type (noPVOH, 4-98, 28-99) and fatty acid chloride (FA). For clarity, each variation receives a code with abbreviations, following the order of S/C/FA. No statistical evaluation was done because the amount of values needed for the calculation did not fulfill the requirements of a multi-t-test. Conclusions drawn from Figure 4 are explained in the following subsections.
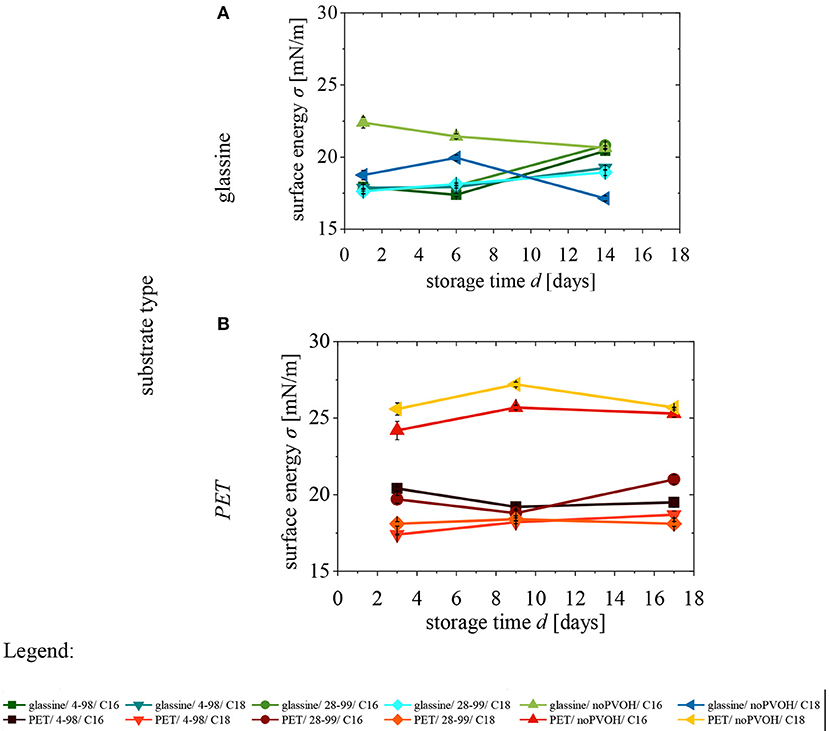
Figure 4. Surface energy of (A) glassine and (B) PET over storage time. Error bars show standard deviations. n = 5 (Supplementary Tables 3, 4).
Influence of Substrate Type on Surface Energy After Grafting
For PVOH coated samples, the substrate (S) has no influence on the surface energy. This is because the PVOH layer is thick enough (~2–5 μm) to cover the entire substrate.
PET/noPVOH/FA shows higher surface energy than G/noPVOH/FA. This can be explained as follows: Glassine has many hydroxyl groups leading to a high grafting density and thus to a low surface energy. In comparison, PET only can have carbonyl- or carboxyl groups on its surface after corona treatment (Lindner et al., 2018). Despite the corona treatment, there are much less hydroxyl groups available than on glassine. Thus, the effect of grafting is less effective on PET than on glassine and the final grafting density on PET is much lower than on glassine, which leads to a relatively higher surface energy (Schmid et al., 2012, 2014; Haas et al., 2017). Although the grafting density of pure PET is low, there is still an effect of chemical grafting visible as the surface energy reduces from PET/noPVOH/noFA (~50 mN/m) (Lindner et al., 2018) to PET/noPVOH/FA (~25 mN/m).
Summarizing it can be concluded that the substrate type only has an influence on surface energy for noPVOH samples: the lower the availability of hydroxyl groups, the lower is the grafting density of the substrate, and the higher is the surface energy.
Influence of PVOH Coating on Surface Energy After Grafting
S/PVOH/FA show a lower surface energy than S/noPVOH/FA samples (Figure 4B) (with one exception being G/noPVOH/C18 (), day 14). This can be explained as follows: In both cases, glassine and PET, the PVOH coating shows more hydroxyl groups than the pure substrate. More hydroxyl groups lead to a higher grafting density and thus to a lower surface energy. As glassine possesses more hydroxyl groups than PET, the difference between G/PVOH/FA and G/noPVOH/FA is lower than between PET/PVOH/FA and PET/noPVOH/FA.
Influence of PVOH Type on Surface Energy After Grafting
For both substrates, PET and glassine, there is no obvious difference between the two types of PVOH, 4-98 and 28-99, regarding the surface energy after grafting. Thus, as already expected, a small increase of degree of hydrolysis, by only 1% from 98 to 99%, does not affect the surface energy, even though there is a great difference in molecular weight. Based on these observations it can be concluded, that the PVOH type does not influence surface energy of S/PVOH/FA samples.
Influence of Fatty Acid Chloride Chain Length on Surface Energy Over Storage Time
S/PVOH/FA samples with C18 show a lower surface energy than samples with C16. This is in line with a previous study (Schmid et al., 2014), which showed that a lower surface energy is caused by a longer chain length of fatty acid chlorides. However, in the case of glassine substrates, this applies only at the end of the storage time. Before that point, C16 has equal or lower surface energy than C18.
For S/noPVOH/FA, similar observations can be made: G/noPVOH/C18 () (Figure 4A), has a lower surface energy than G/noPVOH/C16 (
). PET/noPVOH/C18 (
) is an exception here, as it has a higher surface energy than PET/noPVOH/C16 (
). This is probably due to inhomogenous sample surface properties and PET's low ability to bind fatty acid chlorides.
To sum it up, surface energy is decreasing with longer chain length of fatty acid chlorides.
Influence of Storage Time on Surface Energy
No obvious correlation between storage time and surface energy can be identified (Figures 4A,B).
Alteration of Peel Strength
The following four graphs show the peel strength over a storage time of 3 weeks (Figure 5 and Supplementary Tables 3, 4). For clarity, the results are divided into substrate (S; rows) and pressure sensitive adhesive type (PSA; columns). C16 is marked as symbol without filling and C18 as symbol with filling. For comparison, benchmarks for PET and glassine release liners were measured at only 1 day and added here (PET: and glassine:
). Furthermore, each variation receives a code with abbreviations, following the order of S/PSA/C/FA. Conclusions drawn from Figure 5 are explained in the following subsections.
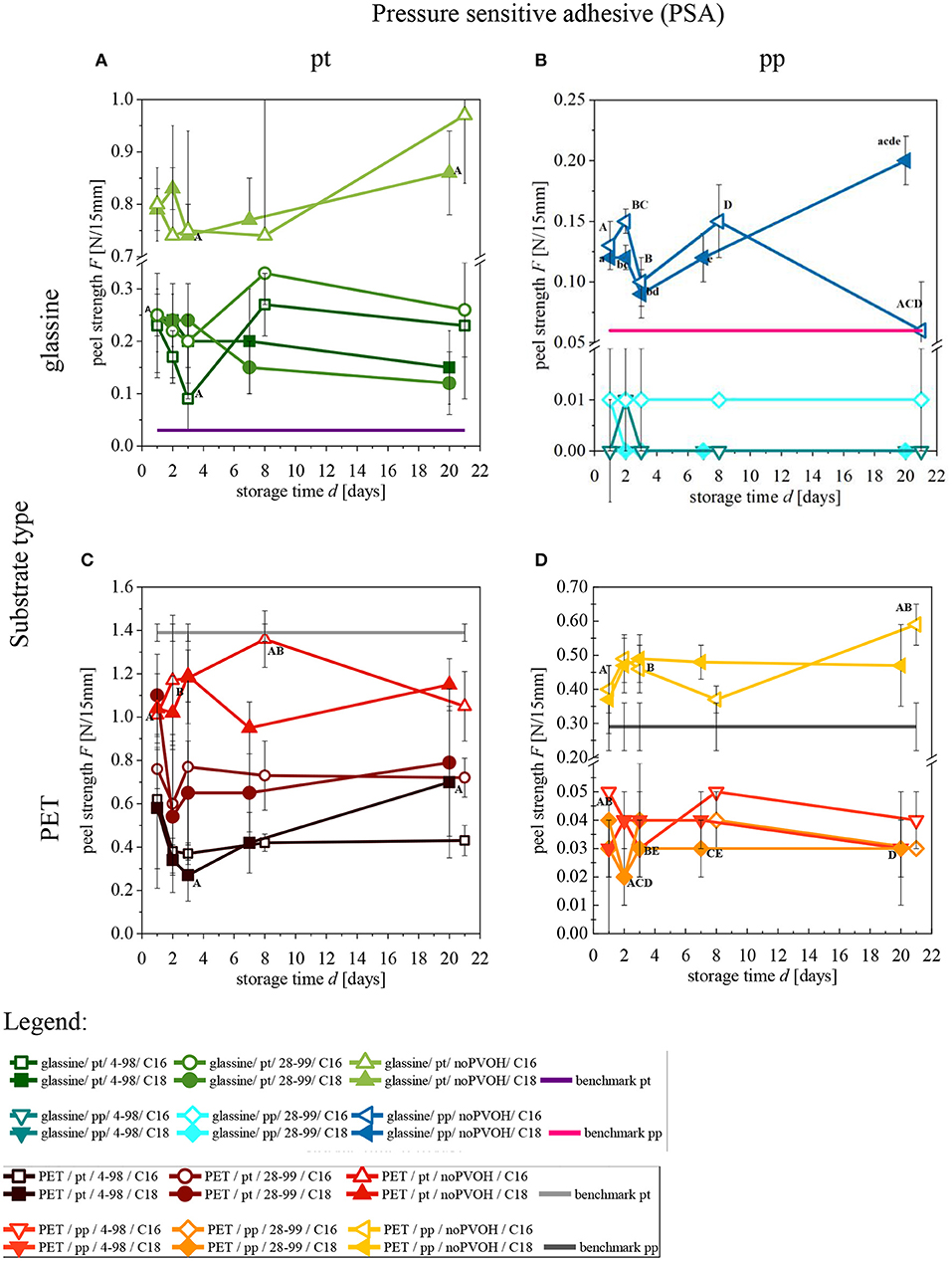
Figure 5. Peel strength of (A) G/pt/PVOH/FA (B) G/pp/PVOH/FA (C) PET/pt/PVOH/FA (D) PET/pp/PVOH/FA over storage time. Same letters indicate statistically significant difference (p < 0.05, two-sample t-test). Levene-Test and Kolmogorov-Smirnov was carried out. n = 5. Error bars show standard deviations.
Influence of the Substrate Type on Peel Strength
When comparing samples, which only differ in substrate type (Figures 5A,B vs. C,D), it is obvious that PET always shows higher peel strength by a factor of ~1.5–3 than glassine. This can partially be explained by the differences in modulus and thickness of the different substrates themselves, as those are known to affect measured peel values (Kim et al., 1989; Zhang Newby and Chaudhury, 1997). Moreover, PET has a higher surface energy than glassine, resulting in more ionic interactions and a greater adhesion strength of the PSA to the release liner (Kowalski et al., 2013).
Influence of the Presence or Absence of the PVOH Coating on Peel Strength
Two major effects of the PVOH coating were expected:
a) the higher provision of hydroxyl groups (compared to the pure substrate), results in a higher grafting density and a lower surface energy, leading to a lower peel strength; this effect is mainly expected to be seen on PET
b) a smoothening effect especially, resulting in a smaller specific surface and lower peel strength; this effect is mainly expected to be seen on glassine
It can be observed, that the presence or absence of PVOH has a big influence on the peel strength of both substrates, PET and glassine. S/PVOH/FA/PSA show lower peel strength than S/noPVOH/FA/PSA. The effect of the PVOH coating on peel strength is higher on PET compared to glassine, indicating that effect (a) is stronger than effect (b).
The effect of a PVOH coating is more prominent for pp in comparison to pt (Figure 5D). In the case of pp, samples with PVOH (e.g., PET/pp/28-99/C18 ), have a peel strength of ~0.03 N/15mm, whereas same samples without PVOH (e.g., PET/pp/noPVOH/C18
), have a peel strength of ~0.5 N/15 mm (factor of 17). In contrast, pt samples (
,
) only show a difference by factor of ~2. Same observations can be made for glassine (Figure 5A).
One reason for this is the low adhesion strength of the PSA pp, which is designed to peel off easily (HERMA GmbH, 2014a). Samples with PVOH show lower adhesion strength presumably because of their lower surface energy and the greater repellence of the polar acrylate PSA. Combining this low adhesion strength with the PSA pp, it is clear that this combination results in the lowest peel strength of all. In contrast, noPVOH samples have a higher surface energy. That is why noPVOH samples have a higher adhesion strength and higher peel strength. To put it all in a nutshell, S/PVOH/FA show lower peel strengths than S/noPVOH/FA.
Influence of the PVOH Type on Peel Strength
The PVOH type does not influence peel strength for pp, but influences peel strength for pt. This is probably because pp causes such low peel strength on both samples, so that PVOH type does not influence the outcome. Concluding, the PVOH type only influences peel strength for PSA types with high adhesion (pt). In this case, the effect might be explained by the higher viscosity of the PVOH 28-99 (see also section Influence of Substrate Roughness on Peel Strength).
Influence of the Fatty Acid Chlorides Chain Length on Peel Strength
It was assumed that the lower surface energy of C18 compared to C16 also leads to a lower adhesion strength and lower peel strength. Although a higher peel strength of C16 compared to C18 could be derived from the Figure 5, the differences are not statistically significant, showing that the low difference in surface energy does not have a major effect (Ekeland et al., 2005).
Influence of Pressure Sensitive Adhesive Type on Peel Strength
pp samples (Figures 5B,D) show a lower peel strength than pt samples (Figures 5A,C). This can be explained by the manufacturer's developed high final adhesion of pt.
PVOH-coated substrates show lower peel strength by the factor of ~20 when peeled off from pp compared to pt. For noPVOH samples, the difference in peel strength is only by a factor of ~3–8. Consequently, the effect of low adhesion strength of pp is not that prominent for noPVOH samples.
For pt, samples with G/PVOH/FA are close to the benchmark (), whereas for pp, samples with G/noPVOH/FA are closest to benchmark (
). Although G/noPVOH/FA shows good results, the substrate surface is brittle due to high temperatures during the grafting process.
Influence of Storage Time on Peel Strength
Storage time was analyzed because it was reported that the PSA can spread over time, resulting into a larger adhesion area and increased peel strength (Asahara et al., 2003). However, there is no significant influence of storage time on peel strength observable. There are almost no significant differences (p < 0.5) between measurements over storage time and if there are, it is mostly on noPVOH samples. This is probably because there is no PVOH layer compensating the unevenness of the substrate. The findings of Asahara et al. (2003) of increasing peel strength caused by increasing contact time, cannot be observed in this study.
Influence of Substrate Roughness on Peel Strength
The influence of substrate roughness on peel strength can be seen in two graphs for pt (Figure 6A) and pp (Figure 6B). Both graphs have in common, that with increasing roughness, peel strength is increasing as well. This can be explained as an increasing roughness leads to an increase in specific surface area which accordingly increases peel adhesion strength (Gent and Lin, 1990; Uehara and Sakurai, 2002). Another reason could be mechanical clamping, which increases peel strength or the change of the viscoelastic properties of the PVOH (Mese and Guzel, 2008).
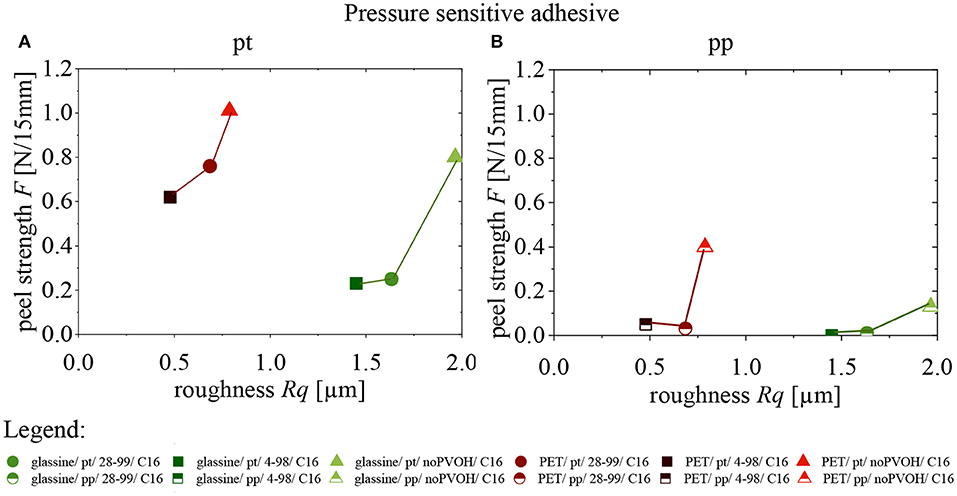
Figure 6. Influence of substrate roughness on peel strength of two PSA (A) pt (B) pp. Lines are only added for clarity. n = 5.
For both, PET and glassine, the highest value of roughness can be seen for samples having no PVOH: glassine () and PET (
). That is because a PVOH-layer reduces surface roughness.
The differences in roughness between samples with PVOH 4-98 and 28-99 can be explained by the higher viscosity of 28-99, which leads to a more uneven coating distribution during rod coating.
Although substrate roughness seems to increase peel strength, this only applies for comparisons within one substrate: PET films are much smoother than glassine but still show higher peel strength. This can partially be explained by the differences in modulus and thickness of the different substrates themselves, as those are known to affect measured peel values (Kim et al., 1989; Zhang Newby and Chaudhury, 1997).
Conclusions
The following conclusions are also summarized in Table 3. The chemical grafting process resulted in lower grafting density for noPVOH samples compared to PVOH coated samples. This presumably leads to noPVOH samples showing a higher peel strength. Therefore, a PVOH layer should be applied if lower surface energy and peel strength are desired.
The PVOH molecular weight does not influence the surface energy and peel strength after grafting, but roughness. In that case, a higher viscosity of PVOH leads to higher roughness.
A longer chain length of fatty acid chlorides decrease surface energy but shows no influence on peel strength or roughness. Storage time did not influence surface energy or peel strength drastically.
This work demonstrated that grafting with fatty acids could potentially be a sustainable alternative for release liners for e.g., address labels with acrylate based PSAs. In the future, other PSAs based on e.g., natural rubber should also be tested in combination with grafted PVOH and paper. Further measurements should be done in order to evaluate, if the PVOH layer could be thinner and still lead to similar functionalities. Furthermore, for the esterification, phenols could be used instead of alcoholes.
Data Availability Statement
All datasets generated for this study are included in the article/Supplementary Material.
Author Contributions
EG conducted the experiments, prepared the data, and original draft. MS conceptualized the work, revised the manuscript. ML supervised the project, conceptualized the work, reviewed and edited the manuscript. All of them developed the methodology in close collaboration.
Conflict of Interest
The authors declare that the research was conducted in the absence of any commercial or financial relationships that could be construed as a potential conflict of interest.
Supplementary Material
The Supplementary Material for this article can be found online at: https://www.frontiersin.org/articles/10.3389/fmats.2019.00335/full#supplementary-material
References
Asahara, J., Hori, N., Takemura, A., and Ono, H. (2003). Crosslinked acrylic pressure-sensitive adhesives. I. Effect of the crosslinking reaction on the peel strength. J. Appl. Polym. Sci. 87, 1493–1499. doi: 10.1002/app.11529
Awaja, F., and Pavel, D. (2005). Recycling of PET. Eur. Polym. J. 41, 1453–1477. doi: 10.1016/j.eurpolymj.2005.02.005
CPI: Confederation of Paper Industries (2019). Paper and Board Packaging Recyclability Guidelines. Swindon.
Deutsches Institut für Normung (2011). Standard DIN 55660-2: Paints and Varnishes - Wettability - Part 2: Determination of the Free Surface Energy of Solid Surfaces by Measuring the Contact Angle. Berlin.
Deutsches Institut für Normung (2017). Standard DIN 55543-5: Packaging Test - Test Methods for Packaging Films - Part 5: Determination of Adhesion Strength. Berlin.
Ekeland, R., Tonge, S., and Gordon, V. (2005). Release Force Understanding-Recent Findings. Midland, MI: Dow Corning Corporation.
Feldman, R. M., and Valdez-Flores, C. (2009). Applied Probability and Stochastic Processes. Boca Raton, FL: Springer Science & Business Media.
FINAT (2017). Release Liner Recycling Possibilites. The Hague: The Association for the European Self-Adhesive Labelling and Adjacent Narrow Web Converting Industries.
Gent, A. N., and Lin, C. W. (1990). Model studies of the effect of surface roughness and mechanical interlocking on adhesion. J. Adhes. 32, 113–125. doi: 10.1080/00218469008030185
Gordon, G. V., Perz, S. V., Tabler, R. L., Stasser, J. L., Owen, M. J., and Tonge, J. S. (1998). Silicone Release Coatings: A Closer Look at Release Mechanisms. Midland, MI: Dow Corning Corporation.
Haas, A., Schlemmer, D., Grupa, U., and Schmid, M. (2017). Effect of chemical grafting parameters on the manufacture of functionalized PVOH films having controlled water solubility. Front. Chem. 5:38. doi: 10.3389/fchem.2017.00038
Hose, R. (2007). BOND It: Nachschlagewerk zur Klebtechnik. Windach: DELO-Industrie-Klebstoffe GmbH Co. KG.
Kaiser, K., Schmid, M., and Schlummer, M. (2018). Recycling of polymer-based multilayer packaging: a review. Recycling 3:1. doi: 10.3390/recycling3010001
Kim, J., Kim, K., and Kim, Y. (1989). Mechanical effects in peel adhesion test. J. Adhes. Sci. Technol. 3, 175–187. doi: 10.1163/156856189X.00146
KNU Industry Cooperation Foundation (2018). PVA Method for Inhibiting the Discoloration of Hydrophobic PVA Coated Paper Manufactured by Gas Grafting. Chuncheon.
Kowalski, A., Czech, Z., and Byczynski, Ł. (2013). How does the surface free energy influence the tack of acrylic pressure-sensitive adhesives. (PSAs)? J. Coat. Technol. Res. 10, 879–885. doi: 10.1007/s11998-013-9522-2
Lindner, M., Rodler, N., Jesdinszki, M., Schmid, M., and Sängerlaub, S. (2018). Surface energy of corona treated PP, PE and PET films, its alteration as function of storage time and the effect of various corona dosages on their bond strength after lamination. J. Appl. Polym. Sci. 135:45842. doi: 10.1002/app.45842
Madeira, D. M., Vieira, O., Pinheiro, L. A., and de Melo Carvalho, B. (2018). Correlation between surface energy and adhesion force of polyethylene/paperboard: a predictive tool for quality control in laminated packaging. Int. J. Chem. Eng. 2018:2709037. doi: 10.1155/2018/2709037
Mangipudi, V., Tirrell, M., and Pcius, A. V. (1994). Direct measurement of molecular level adhesion between poly(ethylene terephthalate) and polyethylene films: determination of surface and interfacial energies. J. Adhes. Sci. Technol. 8, 1251–1270. doi: 10.1163/156856194X00591
Mese, A., and Guzel, K. G. (2008). Effect of storage duration on the hardness and tensile bond strength of silicone- and acrylic resin-based resilient denture liners to a processed denture base acrylic resin. J. Prosthet. Dent. 99, 153–159. doi: 10.1016/S0022-3913(08)60032-3
Mohammed, I., Charalambides, M., and Kinloch, A. (2016). Modeling the effect of rate and geometry on peeling and tack of pressure-sensitive adhesives. J. Non Newtonian Fluid Mech. 233, 85–94. doi: 10.1016/j.jnnfm.2016.01.016
Newby, B. M. Z., Chaudhury, M. K., and Brown, H. R. (1995). Macroscopic evidence of the effect of interfacial slippage on adhesion. Science 269, 1407–1409. doi: 10.1126/science.269.5229.1407
Owen, M. J. (1998). “Surface properties of silicone release coatings,” in First International Congress on Adhesion Science and Technology–Invited Papers: Festschrift in Honor of Dr. KL Mittal on the Occasion of His 50th Birthday. Utrecht.
Schmid, M., Benz, A., Stinga, C., Samain, D., and Zeyer, K. P. (2012). Fundamental investigations regarding barrier properties of grafted PVOH layers. Int. J. Polym. Sci. 2012:637837. doi: 10.1155/2012/637837
Schmid, M., Sängerlaub, S., Miesbauer, O., Jost, V., Werthan, J., Stinga, C., et al. (2014). Water repellence and oxygen and water vapor barrier of PVOH-coated substrates before and after surface esterification. Polymers 6, 2764–2783. doi: 10.3390/polym6112764
Stinga, N. C. (2008). Utilisation de la Chimie Chromatogénique pour la Conception et la Réalisation de Matériaux Cellulosiques Barrières à l'eau, aux Graisses et aux Gaz. Grenoble: Université Joseph-Fourier-Grenoble I.
Uehara, K., and Sakurai, M. (2002). Bonding strength of adhesives and surface roughness of joined parts. J. Mater. Process. Technol. 127, 178–181. doi: 10.1016/S0924-0136(02)00122-X
Yoshida, S., Hiraga, K., Takehana, T., Taniguchi, I., Yamaji, H., Maeda, Y., et al. (2016). A bacterium that degrades and assimilates poly(ethylene terephthalate). Science 351, 1196–1199. doi: 10.1126/science.aad6359
Keywords: fatty acid chloride, polyvinyl alcohol, surface energy, peel strength, polyethylene terephthalate
Citation: Germek E, Schmid M and Lindner M (2020) Grafting of Fatty Acids on Polyvinyl Alcohol: Effects on Surface Energy and Adhesion Strength of Acrylic Pressure Sensitive Adhesives. Front. Mater. 6:335. doi: 10.3389/fmats.2019.00335
Received: 23 September 2019; Accepted: 06 December 2019;
Published: 15 January 2020.
Edited by:
Seunghwa Ryu, Korea Advanced Institute of Science and Technology (KAIST), South KoreaReviewed by:
Fei Hang, South China University of Technology, ChinaPaolo S. Valvo, University of Pisa, Italy
Copyright © 2020 Germek, Schmid and Lindner. This is an open-access article distributed under the terms of the Creative Commons Attribution License (CC BY). The use, distribution or reproduction in other forums is permitted, provided the original author(s) and the copyright owner(s) are credited and that the original publication in this journal is cited, in accordance with accepted academic practice. No use, distribution or reproduction is permitted which does not comply with these terms.
*Correspondence: Martina Lindner, bWFydGluYS5saW5kbmVyQGl2di5mcmF1bmhvZmVyLmRl