- Department of Mechanical Engineering, National University of Singapore, Singapore, Singapore
In this study, the design and development of a new Mg-based multicomponent alloy (ρth = 2.33 g/cc; ρex = 2.15 g/cc) has been presented which exhibits excellent mechanical properties in hot extruded condition. Mg80Al5Cu5Mn5Zn5 alloy was designed and synthesized using disintegrated melt deposition technique followed by hot extrusion. The alloy was designed in such a way that the concentration of each alloying element remained ≥5 at % with Mg (80 at %) as base metal. Significantly high hardness (196 HV) was realized in Mg80Al5Cu5Mn5Zn5 alloy. Compression results showed substantially high ultimate compressive strength (UCS) 616 MPa of this alloy with a reasonably high ductility of 16.9%. This alloy also exhibited superior combination of tensile strengths (TYS- 211 MPa, UTS- 318 MPa) and ductility (8.2%). Overall combination of hardness, tensile and compression properties showed the current new lightweight alloy system as an alternative to most of the commercially used Al-based alloys.
Introduction
High-performance materials are the key drivers to boost the safety and performance of devices in multiple engineering sectors. Lightweight materials assist in enhancing the efficiency of a vehicle by reducing the vehicle weight, thus reducing the energy requirements for operations. In general, 10% reduction in weight of a vehicle can reduce 6–8% fuel requirement, which is an important aspect of reducing the existing problem of carbon footprint (Cheah, 2010). The main drawback of the existing lightweight materials is either their limited properties or high manufacturing cost. Thus, continuous efforts have been made by researchers to develop new types of lightweight alloys, which are low in cost and capable to meet properties requirements (Miller et al., 2000). Over past three decades, efforts have been made to replace steel and iron with aluminum (Al) and magnesium (Mg) based materials.
In general, the basic principles of designing an alloy involves the application of the fundamental principles of chemistry and thermodynamic parameters (enthalpy, entropy, free energy, and so on), to decide whether certain elements are suitable for alloying or not. According to the entropy of mixing or Configurational Entropy, alloys can be classified as low, medium, and high entropy alloys (Yeh, 2013; Gao et al., 2016). If the CE of an alloy is <1.0 R (8.314 J/mol.K) then it is considered as a low-entropy alloy (LEA) and most of the conventional Fe-, Al-, Cu-, Mg-base alloys belongs to this category. If an alloy is having Configurational Entropy ≥1.0 R and ≤ 1.5 R then this is considered as a medium-entropy alloy (MEA) and bulk metallic glasses (BMGs) belong to this category. If for an alloy, Configurational Entropy is ≥1.5 R then it is considered as a high-entropy alloy (HEA). HEAs contains at least five principle elements, each having atomic percentage between 5 and 35%, to maximize the configurational entropy. This results in a simple solid solution structure with excellent properties (Cantor et al., 2004; Yeh et al., 2004; Varalakshmi et al., 2010; Senkov et al., 2011; Gao et al., 2016).
Most of the conventional alloys or LEAs have one dominant principal element as the amount of other alloying elements are in small quantity. Therefore, most of the lightweight conventional alloys possess good ductility but poor strength, which is not desirable for many structural applications. For example, Mg (density 1.74 g/cc) is lightest structural material and termed as “next generation material.” However, the utilization of Mg and its alloys in critical engineering applications is still limited due to its low absolute strength, ductility, and creep resistance (Friedrich, 2006; King, 2007; Alam et al., 2011; Kumar et al., 2017). Although a variety of Mg and Al-base lightweight alloys have already been developed, alloys with better structural properties are still required to fulfill the current and future material requirements. On the other side, BMGs (MEAs) and recently develop HEAs possess very high compressive strength and hardness but no significant tensile response and poor ductility for their use in wide spectrum of structural applications. Thus, it requires a new strategy to design lightweight alloys, which overcome this barrier of strength and ductility.
Therefore, in this work, we have adopted an approach of multicomponent alloy (MCA) to design Mg-based Mg80Al5Cu5Mn5Zn5 alloy. The reason for selecting this approach was to create a more disordered structure compared to conventional Mg alloy by using a higher amount of alloying elements (Al, Cu, Mn, Zn each 5 at %). This disordered structure is targeted to increase the overall entropy of the alloy leading eventually to formation of high strength phases embedded in a comparatively ductile phase. This combination of hard and soft phases is expected to exhibit a good combination of high strength and ductility. So the main objective of this work is to develop a new light weight multicomponent alloy system with better structural properties than the commonly used lightweight Mg alloys and Al alloys.
Materials and Processing
In this work, Mg80Al5Cu5Mn5Zn5 alloy was synthesized by using disintegrated melt deposition (DMD) technique, which is already established and ensures good microstructural and mechanical properties of Al-based and Mg-based alloys and their composites (Gupta and Wong, 2005; Nguyen and Gupta, 2008; Paramsothy et al., 2009; Meenashisundaram et al., 2014). This solidification-based technique is followed by hot extrusion to homogenize the microstructure for relatively superior mechanical performance.
Magnesium turnings (99.9% purity) (Acros Organics, USA), Al & Zn granules (99% purity) (Sigma Aldrich, USA), and Cu (99% purity) & Mn (99.95% purity) powders (~ 40 μm) (Alfa Aesar, USA) were used as starting material. Initially, all the elements in predetermined composition were superheated to 850°C in an inert argon gas atmosphere in a graphite crucible using electrical resistance furnace. The superheated melt was then stirred at 500 rpm for 10 min using a stainless steel impeller with twin blade (pitch 45°). The molten melt was poured through a nozzle of 10 mm diameter at the bottom of the crucible to the mold below the crucible. Two jets of argon gas, oriented normal to the melt stream were used to disintegrate the molten metal before it enters the mold to assist in realizing refined cast microstructure. The disintegrated melt was then deposited in the cylindrical mold of 40 mm diameter. This ingot was later machined to 36 mm diameter and 45 mm length for the secondary processing. Secondary processing involved the homogenization of ingot at 400°C for 1 h in a constant temperature furnace followed by hot extrusion at 350°C temperature using 150-ton hydraulic extrusion press. The extrusion ratio of 20.25:1 was set to obtain rods of diameter 8 mm.
Characterization
The microstructure of alloy was characterized using, scanning electron microscopes (JEOL JSM-6010 and Hitachi FESEM-S4300) equipped with energy dispersive spectrometric analysis (EDS). X-Ray diffraction analysis was conducted using an automated Shimadzu LAB-XRD- 6000 (Cu Kα: λ = 1.54056 A°) spectrometer with a scan speed of 2°/min. The density of extruded samples was measured using Archimedes principle. Microhardness of samples was measured using a Shimadzu HMV automatic digital microhardness tester (Kyoto, Japan) with a Vickers indenter (pyramidal shaped diamond indenter with a phase angle of 136°). An indenting load of 25 gf was used for a dwell time of 15 s. The test was performed as per ASTM E384-11e1. At least three samples were tested with minimum 10 repeatable values. The tensile properties were measured at ambient temperature in accordance with ASTM E8/E8M-15a. A fully automated servo-hydraulic mechanical testing machine, MTS-810 was used to test tensile specimens of diameter 5 mm and gauge length 25 mm using a strain rate of 1.693 × 10−4 s−1. Clip type, Instron 2630-100 series extensometer was used to measure the tensile fracture strain. The compression properties were also measured using the same equipment at an ambient temperature in accordance with ASTM E9-09 using a strain rate of 8.334 × 10−5 s−1. The specimens of 8 mm diameter, with length to diameter ratio of one were used. At least five different samples were tested to ensure repeatability of results. Fractured surfaces of all samples (under tensile and compressive load) were analyzed using Hitachi S-4300 FESEM.
Results and Discussion
Figure 1 shows the results for microstructural characterization of extruded Mg80Al5Cu5Mn5Zn5 alloy using SEM, XRD, and EDS analysis techniques. It is clear from the SEM micrograph (Figure 1A) that the alloy demonstrates a multiphase structure. Three different types of phase morphology were observed, the base matrix (dark gray), polyhedron shape phases (light gray) and scattered, and irregular shape phases. From the XRD results (Figure 1B), the matching peaks are identified as that of Mg (dominating hcp base structure) and the secondary phases of Al6Mn phase and Al2CuMg phase. EDS analysis (Figures 1C–E) conducted on the phases (see 1, 2, and 3 marked locations in SEM micrograph, Figure 1A) revealed the presence of Mg, Zn, and Mn in base matrix (location 1), Al and Mn at polyhedral phase (location 2) and Al, Cu, and Mg at scattered phase (location 3), confirming further the results of XRD.
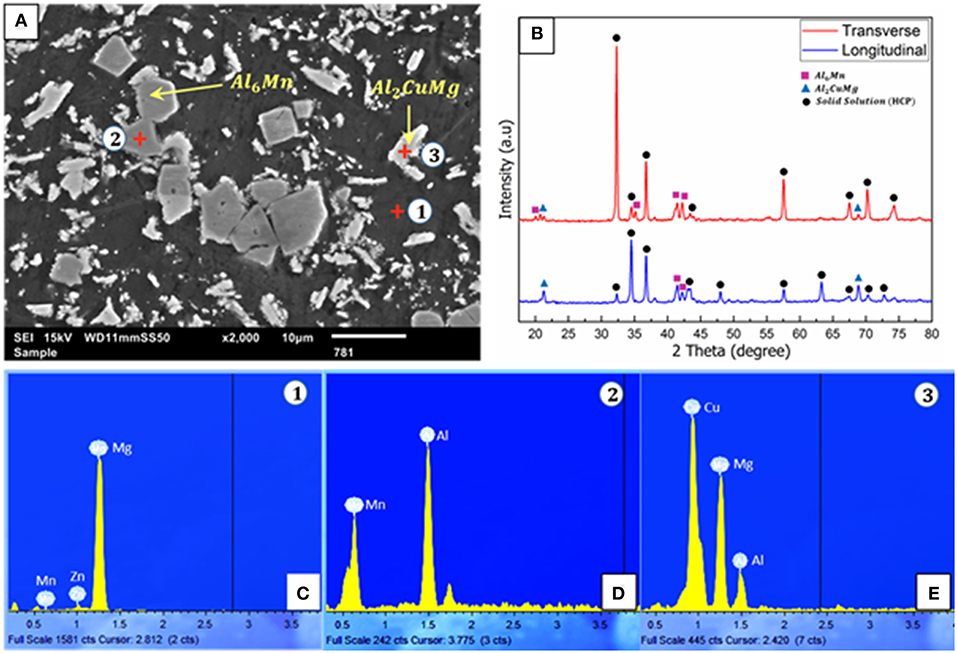
Figure 1. SEM, XRD, and EDS results of Mg80Al5Cu5Mn5Zn5 MCA. (A) SEM micrograph reveals the presence of three phases, base matrix, polyhedron phase, and smaller scattered precipitates. (B) XRD results revealing the presence of Mg hcp structure as a dominating phase together with the presence of Al6Mn and Al2CuMg phase. (C–E) EDS spectrums taken on three different phase location (1, 2, and 3) in SEM micrograph (A), further verified the presence of Mg-base solid solution matrix with Al6Mn and Al2CuMg as embedded phases.
Table 1 summarizes the results of the mechanical characterization studies of Mg80Al5Cu5Mn5Zn5 alloy under compression and tensile loading, hardness, and density measurement. The hardness results of Mg80Al5Cu5Mn5Zn5 MCA show significantly high hardness value of the alloy when compared to Mg based (Paramsothy et al., 2012) and Al based alloys (Committee, 1990; Knowles et al., 2014; Table 1). It is understandable that both solid solution phase and intermetallic phases contributed to high hardness. These results also suggest that these materials are likely to exhibit superior tribological response (sliding wear) as per Archard's law. Further work is continuing in this area.
Based on the density of current Mg MCA (2.15 g/cc), comparison of tensile properties was made with Al alloys with density, 2.7–2.8 g/cc. As there was no heat treatment performed on this alloy, all the alloys chosen for the comparison point of view are taken in extruded conditions, without any heat treatment. Mg MCA developed in this study exhibited high tensile yield strength (211 MPa) and ultimate tensile strength (318 MPa) with a fracture strain of 8.2%. The tensile strengths of this Mg MCA are superior to Al-base alloys (see Table 1) reported in literature while maintaining the reasonable fracture strain value.
When compared to as-extruded Mg and Mg based alloys which were processed using the same fabrication technique (Sankaranarayanan et al., 2011; Paramsothy et al., 2012), the current Mg based MCA showed higher yield and ultimate tensile strengths with comparable failure strain considering the standard deviation. The compression results of Mg80Al5Cu5Mn5Zn5 alloy showed substantially high ultimate compressive strength (UCS) 616 MPa, which is 61, 21 and 19% higher than the strength of pure Mg, AZ31, and ZK60 with a marginally lower ductility.
Figure 2 shows the mechanical behavior of Mg80Al5Cu5Mn5Zn5 alloy. Engineering stress and strain response in compression and tension are shown in Figure 2A. Compression response of alloy shows evidence of significant strain hardening prior to fracture. Here, yield strength was calculated using 0.2% offset strain criterion in both compression and tensile testing. To further compare the compression response of Mg80Al5Cu5Mn5Zn5 alloy over previously reported Mg alloys, ultimate compression strength and strain data are plotted in Figure 2B. The present MCA stands far above the reported Mg-based alloys in terms of strength while maintaining appreciable ductility (~17%). Figures 2C,D shows the fractured sample during the tensile and compression testing, respectively. Tensile sample fractured in a near cup and cone mode revealing a relatively ductile character, while the compression failure occurred at 45° to compression axis resembling a ductile shear failure. To understand the failure mechanisms in tension and compression, fractography using SEM was performed on fractured surfaces. Figure 3 shows the SEM fractography for samples failed under compressive and tensile loadings. The shear bands observed in compression fractograph clearly indicate the ductile failure under compression stress (Figure 3A). Tensile fractography also shows the dimple shaped features similar to common ductile fracture, except the presence of cleavage fracture at few locations. Cracking of hard icosahedral Al6Mn phase was also observed (Figure 3B).

Figure 2. Mechanical behavior of Mg80Al5Cu5Mn5Zn5 alloy. (A) Engineering stress vs. strain graphs. Table (Inset) contains the engineering stress and strain values observed in compression and tension. Standard deviation results indicate the consistency and reliability of material. (B) Comparison of stress and strain with other Mg alloys reveals the superiority of Mg80Al5Cu5Mn5Zn5 MCA. (C,D) Fractured samples during tensile and compression tests.
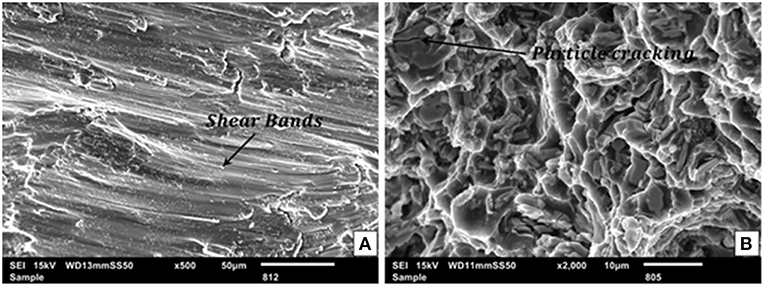
Figure 3. SEM fractographs of Mg80Al5Cu5Mn5Zn5 alloy in compression and tension. (A) Reveals the dominating shear failure in compression. (B) Shows ductile failure of the matrix under tension and cracked hard phase (Al6Mn).
The large improvement in the mechanical properties of Mg80Al5Cu5Mn5Zn5 MCA arises from the plastic deformation and strain hardening processes. By observing the SEM micrograph (Figure 1A) it is clear that the alloy contains a base hcp crystalline structure (Mg-rich solid solution) and two other dispersed hard phases Al6Mn and Al2CuMg. During compression, when load is applied on material good amount of plasticity was observed due to continuous solid solution base matrix. On the other hand, in tension, when material is subjected to stress, comparatively less amount of plastic deformation was observed due to less number of possible slip systems available in hcp structure. Due to the presence of secondary phases, high yield and ultimate tensile strength was achieved effectively but material failed at a fracture strain of ~8.2%.
If overall properties, hardness, tensile, and compression are compared with other alloys, this alloy possesses a much better overall combination of structural properties. One important aspect of the weight critical industries such as automotive industry is that the material should exhibit almost symmetric tensile/compressive behavior (~1). It is well-known that Mg and conventional wrought Mg alloys exhibit strong basal texture through secondary processing such as extrusion and rolling which leads to severe yield asymmetry (Kim et al., 2005; del Valle and Ruano, 2009; Yin et al., 2009; Gupta and Ling, 2011). The compression to tension yield asymmetry ratio (C/T ratio) of current MCA, pure Mg, and various wrought Mg alloys are listed in Table 2 (Gupta and Ling, 2011; Sankaranarayanan et al., 2011; Paramsothy et al., 2012). The C/T ratio in Mg MCA was measured to be 0.9 (~1) (Table 2 and Figure 2A) exhibiting nearly symmetric yield strength under tension and compression as compared to Mg and wrought Mg alloys with C/T ratio between 0.5 and 0.7 showing asymmetric yield strengths. A minimal yield asymmetry is often looked for material selection in transportation sector.
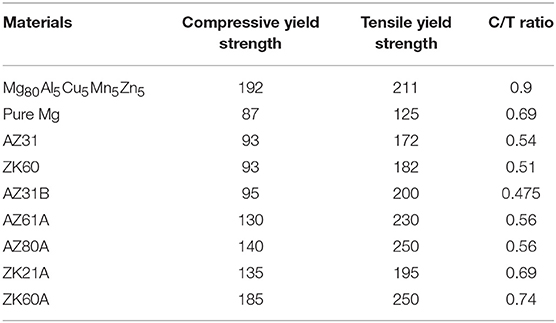
Table 2. List of wrought Mg and alloys with their respective compression to tension asymmetry (C/T) ratio.
The XRD pattern of Mg MCA taken along transverse and longitudinal to the extrusion direction is shown in Figure 1B. It can be seen from the XRD pattern under longitudinal condition that there was relatively strong basal texture showing highest intensity of the peak related to basal plane. Under this condition, compressive stress parallel to the basal plane favors {1 0 1 2} twinning and this induces yielding at low stress level under compression. However, as seen in Figure 2A, yielding was not initiated at a lower stress showing the difficulty of plastic deformation induced by twinning in the current alloy system. Twinning for initial yielding was inhibited by the presence of different types of second phases. This phenomenon led to the realization of yield asymmetry ratio of 0.9 which is closer to 1, in Mg MCA showing the similar strength level under both tension and compression. In a related study (Hidalgo-Manrique et al., 2017), it was reported that the creation of precipitates through heat treatment prevent twin initiation and thereby reduce the yielding asymmetry by increasing the compressive yield strength. In the current study, the compressive yield strength was increased through the presence of second phases due to the addition of multiple alloying elements in Mg matrix without the additional step of heat treatment.
Conclusions
In this work, the effects of multicomponent alloying (Al, Cu, Mn, Zn, each 5 at %) on microstructural and mechanical properties of Mg were investigated. Following conclusions can be drawn:
Microstructural characterization concluded that Al6Mn and Al2CuMg dispersed hard phases are embedded in the soft Mg base hcp solid solution phase to give rise to superior combination of strength and ductility.
Significantly high hardness (196 HV) was realized in Mg80Al5Cu5Mn5Zn5 alloy that is two to four times higher when compared to commercially used alloys.
Compression characterization results concluded that the Mg80Al5Cu5Mn5Zn5 alloy shows superior combination of compressive strength (616 MPa) and ductility (16.9%) when compared to conventional Mg alloys.
Tensile characterization results showed that Mg80Al5Cu5Mn5Zn5 alloy exhibits higher ultimate tensile strength (318 MPa) with a reasonable ductility (8.2%) when compared to conventional Mg and Al base alloys in as-extruded condition.
The current alloy system showed a symmetric tensile/compression yielding behavior which is an important aspect of the weight critical industrial application. This yield symmetry was achieved in the current as-extruded alloy without performing additional heat treatment.
Data Availability
All datasets generated for this study are included in the manuscript/supplementary files.
Author Contributions
AK and MG designed the experiments. AK conducted the all necessary experiments under MG guidance. KT and AK wrote the manuscript. All authors commented on the manuscript.
Funding
The authors would like to acknowledge Ministry of Education Academic Research Funding (WBS# R-265-000-586-114) Singapore for the financial support in carrying out this research work.
Conflict of Interest Statement
The authors declare that the research was conducted in the absence of any commercial or financial relationships that could be construed as a potential conflict of interest.
References
Alam, M. E., Han, S., Nguyen, Q. B., Salem Hamouda, A. M., and Gupta, M. (2011). Development of new magnesium based alloys and their nanocomposites. J. Alloys Compd. 509, 8522–8529. doi: 10.1016/j.jallcom.2011.06.020
Cantor, B., Chang, I. T. H., Knight, P., and Vincent, A. J. B. (2004). Microstructural development in equiatomic multicomponent alloys. Mater. Sci. Eng. A 375–−377, 213–218. doi: 10.1016/j.msea.2003.10.257
Cheah, L.W. (2010). Cars on a Diet: The Material and Energy Impacts of Passenger Vehicle Weight Reduction in the US. Massachusetts Institute of Technology (MIT).
Committee, A. I. H. (1990). Properties and Selection: Nonferrous Alloys and Special-Purpose Materials. Ohio: ASM International.
del Valle, J. A., and Ruano, O. A. (2009). Effect of annealing treatments on the anisotropy of a magnesium alloy sheet processed by severe rolling. Mater. Lett. 63, 1551–1554. doi: 10.1016/j.matlet.2009.04.014
Friedrich, H. E, and Mordike, B.L. (2006). Magnesium Technology: Metallurgy, Design Data, Applications. Heidelberg: Springer, Berlin.
Gao, M. C., Yeh, J. W., Liaw, P. K., and Zhang, Y. (2016). High-Entropy Alloys: Fundamentals and Applications. Cham: Springer International Publishing. doi: 10.1007/978-3-319-27013-5
Gupta, M., and Ling, S. N. M. (2011). Magnesium, Magnesium Alloys, and Magnesium Composites. Hoboken, NJ: Wiley. doi: 10.1002/9780470905098
Gupta, M., and Wong, W. (2005). Enhancing overall mechanical performance of metallic materials using two-directional microwave assisted rapid sintering. Scr. Mater. 52, 479–483. doi: 10.1016/j.scriptamat.2004.11.006
Hidalgo-Manrique, P., Robson, J. D., and Pérez-Prado, M. T. (2017). Precipitation strengthening and reversed yield stress asymmetry in Mg alloys containing rare-earth elements: a quantitative study. Acta Mater. 124, 456–467. doi: 10.1016/j.actamat.2016.11.019
Kim, S.-H., You, B.-S., Dong Yim, C., and Seo, Y.-M. (2005). Texture and microstructure changes in asymmetrically hot rolled AZ31 magnesium alloy sheets. Mater. Lett. 59, 3876–3880. doi: 10.1016/j.matlet.2005.07.024
King, J. F. (2007). Magnesium: commodity or exotic? Mater. Sci. Technol. 23, 1–14. doi: 10.1179/174328407X154374
Knowles, A. J., Jiang, X., Galano, M., and Audebert, F. (2014). Microstructure and mechanical properties of 6061 Al alloy based composites with SiC nanoparticles. J. Alloys Compd. 615, S401–S405. doi: 10.1016/j.jallcom.2014.01.134
Kumar, A., Meenashisundaram, G. K., Manakari, V., Parande, G., and Gupta, M. (2017). Lanthanum effect on improving CTE, damping, hardness and tensile response of Mg-3Al alloy. J. Alloys Compd. 695, 3612–3620. doi: 10.1016/j.jallcom.2016.11.400
Meenashisundaram, G. K., Seetharaman, S., and Gupta, M. (2014). Enhancing overall tensile and compressive response of pure Mg using nano-TiB2 particulates. Mater. Charact. 94, 178–188. doi: 10.1016/j.matchar.2014.05.021
Miller, W. S., Zhuang, L., Bottema, J., Wittebrood, A. J., De Smet, P., Haszler, A., et al. (2000). Recent development in aluminium alloys for the automotive industry. Mater. Sci. Eng. A 280, 37–49. doi: 10.1016/S0921-5093(99)00653-X
Nguyen, Q. B., and Gupta, M. (2008). Enhancing compressive response of AZ31B magnesium alloy using alumina nanoparticulates. Compos. Sci. Technol. 68, 2185–2192. doi: 10.1016/j.compscitech.2008.04.020
Paramsothy, M., Chan, J., Kwok, R., and Gupta, M. (2012). Al2O3 nanoparticle addition to commercial magnesium alloys: multiple beneficial effects. Nanomaterials 2, 147–162. doi: 10.3390/nano2020147
Paramsothy, M., Hassan, S. F., Srikanth, N., and Gupta, M. (2009). Enhancing tensile/compressive response of magnesium alloy AZ31 by integrating with Al2O3 nanoparticles. Mater. Sci. Eng. A 527, 162–168. doi: 10.1016/j.msea.2009.07.054
Sankaranarayanan, S., Jayalakshmi, S., and Gupta, M. (2011). Effect of ball milling the hybrid reinforcements on the microstructure and mechanical properties of Mg–(Ti + n-Al2O3) composites. J. Alloys Compd. 509, 7229–7237. doi: 10.1016/j.jallcom.2011.04.083
Senkov, O., Wilks, G., Scott, J., and Miracle, D. (2011). Mechanical properties of Nb 25 Mo 25 Ta 25 W 25 and V 20 Nb 20 Mo 20 Ta 20 W 20 refractory high entropy alloys. Intermetallics 19, 698–706. doi: 10.1016/j.intermet.2011.01.004
Varalakshmi, S., Kamaraj, M., and Murty, B. S. (2010). Processing and properties of nanocrystalline CuNiCoZnAlTi high entropy alloys by mechanical alloying. Mater. Sci. Eng. A. 527, 1027–1030. doi: 10.1016/j.msea.2009.09.019
Yeh, J.-W. (2013). Alloy design strategies and future trends in high-entropy alloys. JOM 65, 1759–1771. doi: 10.1007/s11837-013-0761-6
Yeh, J.-W., Chen, S.-K., Lin, S.-J., Gan, J.-Y., Chin, T.-S., Shun, T.-T., et al. (2004). Nanostructured high-entropy alloys with multiple principal elements: novel alloy design concepts and outcomes. Adv. Eng. Mater. 6, 299–303. doi: 10.1002/adem.200300567
Keywords: multicomponent alloy, magnesium, microstructure, mechanical properties, yield asymmetry
Citation: Tun KS, Kumar A and Gupta M (2019) Introducing a High Performance Mg-Based Multicomponent Alloy as an Alternative to Al-Alloys. Front. Mater. 6:215. doi: 10.3389/fmats.2019.00215
Received: 02 July 2019; Accepted: 20 August 2019;
Published: 06 September 2019.
Edited by:
Hajo Dieringa, Helmholtz Centre for Materials and Coastal Research (HZG), GermanyReviewed by:
Wenxiang Xu, Hohai University, ChinaSubodh Kumar, Indian Institute of Science (IISc), India
Copyright © 2019 Tun, Kumar and Gupta. This is an open-access article distributed under the terms of the Creative Commons Attribution License (CC BY). The use, distribution or reproduction in other forums is permitted, provided the original author(s) and the copyright owner(s) are credited and that the original publication in this journal is cited, in accordance with accepted academic practice. No use, distribution or reproduction is permitted which does not comply with these terms.
*Correspondence: Manoj Gupta, mpegm@nus.edu.sg