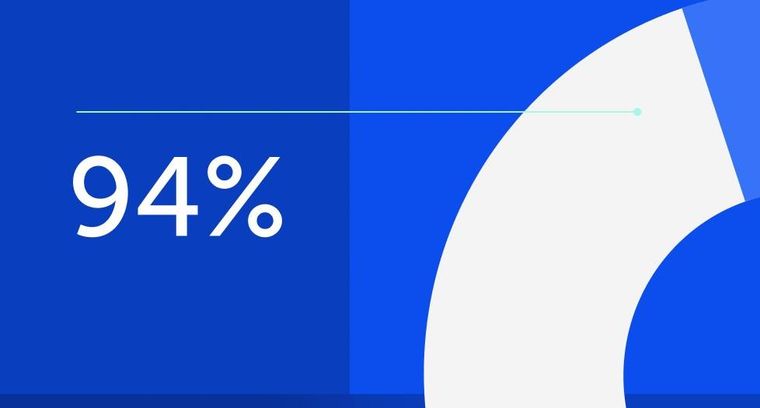
94% of researchers rate our articles as excellent or good
Learn more about the work of our research integrity team to safeguard the quality of each article we publish.
Find out more
REVIEW article
Front. Mater., 27 August 2019
Sec. Polymeric and Composite Materials
Volume 6 - 2019 | https://doi.org/10.3389/fmats.2019.00206
This article is part of the Research TopicBiodegradable Matrices and Composites View all 25 articles
Results of the studies dealing with the toughness of polylactic acid/polycaprolactone (PLA/PCL) blends are analyzed with respect to the PCL particle size, PLA matrix crystallinity, and presence of a compatibilizer. It is shown that a high toughness or even “super-toughness” of PLA/PCL blends without a compatibilizer can be achieved for blends with the proper size of PCL particles. Nevertheless, the window for obtaining the super-tough PLA/PCL blends is quite narrow, as the final impact strength is very sensitive to multiple parameters: namely the blend composition, PLA matrix crystallinity, and PCL particle size. Available literature data suggest that the optimal composition for PLA/PCL blends is around 80/20 (w/w). The PLA/PCL(80/20) blends keep high stiffness of PLA matrix and the concentration of PCL particles is sufficient to achieve high toughness. The PLA/PCL(80/20) blends with low-crystallinity PLA matrix (below ca 10%) exhibit the highest toughness for bigger PCL particles (weight average diameter above 1 μm), while the blends with high-crystallinity PLA matrix (above ca 30%) exhibit the highest toughness for smaller PCL particles (weight average diameter below 0.5 μm). The addition of a compatibilizer may improve the toughness only on condition that it helps to achieve a suitable particle size. The toughness of both non-compatibilized and compatibilized PLA/PCL blends with optimized morphology can be more than 15 times higher in comparison with neat PLA.
Poly(lactic acid) (PLA) is frequently reported as one of the most promising biodegradable polymers synthesized from natural resources as it can be used in many technical applications, especially in packaging (Lunt, 1998; Garlotta, 2002; Auras et al., 2004; Averous and Pollet, 2012). At the same time medical grade PLA continues to be a favorable material for many medical applications such as the tissue engineering (Patrício et al., 2013) and bone fixation devices (Todo et al., 2007) due to its well documented biocompatibility, full biodegradability, and high stiffness resulting from the relatively high glass transition temperature (Tg) (Fambri and Migliaresi, 2010). Preparation from natural resources and biodegradability suggest PLA as substitution of some plastics made from fossil fuels in a broad range of applications. However, brittleness is a strong drawback for practical applications of neat PLA. Various methods of PLA toughening were summarized by Krishnan et al. (2016). Generally, most efficient method for an improvement of toughness of a brittle polymer is its blending with soft, ductile polymers (Bucknall, 2000; Horak et al., 2005). Poly(ε-caprolactone) (PCL) is soft, biocompatible and biodegradable semicrystalline polyester (Pitt, 1990; Krishnan et al., 2016) with a rubbery amorphous phase at room temperature as its Tg is around −60°C and its melting temperature is in the range of 55–70°C. Therefore, PLA/PCL blends should keep favorable biocompatibility and biodegradability and should show enhanced impact strength with respect to neat PLA. The main objective of the preparation of PLA/PCL blends, where PLA is a major component, is the substantial enhancement of PLA toughness with minimum reduction of its stiffness.
Further problem for many technical applications of PLA and PLA/PCL blends is their mechanical performance at elevated temperature. Commercial grades of PLA are mixtures of L-isomer and a small amount of D-isomer (Standau et al., 2019). Therefore, commercial PLA's are semicrystalline with melting temperature, Tm, between 140 and 180°C in dependence on the enantiomeric purity (Fambri and Migliaresi, 2010) and glass transition temperature, Tg, which usually ranges from 55 to 65°C (Auras et al., 2004; Krishnan et al., 2016). However, the rate of the PLA crystallization is slow (Auras et al., 2004; Liu et al., 2014; Murariu et al., 2015; Zhang et al., 2018), frequently slower than the cooling rate used in common polymer processing devices (Zhang et al., 2018). Consequently, the crystallinity of PLA in its blends processed by common procedures tends to be very low, typically lower than 10% (Bai et al., 2012, 2013; Ostafinska et al., 2015, 2017). Therefore, the softening temperature of products prepared from neat PLA and PLA/PCL blends at common processing conditions is controlled by the Tg of PLA. At room temperature, the differences between the moduli of PLA with a low (below 10%) and high crystallinity (above 30%) are not critical. The same is true for PLA/PCL blends. It follows from the literature data (Perego et al., 1996; Kelnar et al., 2016) that the ratio of moduli of materials containing PLA with a high and with a low crystallinity does not exceed 1.25. At elevated temperatures, however, the moduli of low- and high-crystallinity PLA may differ significantly: Bai et al. (2013) found that the modulus of PLA/PCL (80/20) blends with a high-crystallinity PLA matrix was 20 times higher than the modulus of an analogous blend with a low-crystallinity of PLA matrix at the temperature of 80°C. Our measurements at the same temperature led to even higher moduli ratio of 100 for neat PLA and the ratio of 75 for PLA/PCL (80/20) blend. These results discriminate PLA and PLA/PCL blends with a low crystallinity of PLA for many technical applications where good mechanical properties of the material at elevated temperatures are required. Crystallinity of PLA can be enhanced by the annealing during processing and/or by the addition of a convenient nucleation agent.
This review is focused mostly on the toughening of the most common, commercially available PLA polymers, which consist of L-isomer with a small amount of D-isomer, as described above. Other PLA polymers include poly(L-lactic acid) with 100% enantiomeric purity (PLLA), which is polymerized from the pure L-isomer, poly(D-lactic acid) (PDLA), prepared from pure D-isomer, and poly(D,L-lactide) (PDLLA), which derives from a mixture of the L- and D-isomers. Pure PLLA and PDLA can achieve a higher crystallinity than common commercial PLA (Nakajima et al., 2017) but their rate of crystallization is still quite low. PDLLA cannot crystalize. PLLA and PDLLA are commonly used in biomedical applications. We use the above abbreviations in the relation to samples described in the literature. However, it should be mentioned that some authors describe PLA containing small fracture of D-isomer as PLLA.
The impact strength of polymer blends depends on the size distribution of the dispersed particles of the soft polymer in the matrix of the brittle one (Bucknall and Paul, 2009, 2013). Generally, super-tough polymer blends can be obtained only for a certain range, often quite narrow, of sizes of soft polymer particles. The theory of impact behavior of polymer blends is quite complex (Bucknall and Paul, 2013). The lower bound of the suitable particle sizes is given by the minimal size of soft particles needed for their efficient cavitation. The upper bound for a certain blend composition is given by inter-droplet distance which should be shorter than a critical distance for development of cracks or shear bands in the polymer matrix. The optimum particle size depends on dominating mechanism of energy dissipation in the matrix (multiple crazing or shear yielding). Small elastomer particles (weight-average diameter, dw, in the range 0.2–0.4 μm) are efficient when shear yielding dominates the toughening mechanism, e.g., for ductile matrices of polypropylene or polyamide, whereas larger particles (dw between 2 and 3 μm) are more effective when multiple crazing dominates, e.g., for brittle matrices of polystyrene or poly(methyl methacrylate) (Bucknall and Paul, 2009). Thus, the optimum particle size distribution depends on the structure of the matrix, especially on its crystallinity.
In order to achieve optimal particle size distribution for toughening, it is necessary to understand the relation among the processing conditions of PLA/PCL blends, the rheological properties of the components and the resulting morphology of the blends. Polymer blends are mostly prepared by melt mixing in extruders or batch mixers. They are further processed by injection molding, extrusion, blow molding or compression molding. The phase structure of polymer blends is formed and developed during their compounding and processing. Evolution of the phase structure in flowing molten polymer blends has been studied intensively experimentally (mostly for blends of synthetic polymers) and theoretically during last 40 years (Horak et al., 2005; Huang, 2011; Fortelny and Juza, 2019). Evolution of the droplets-in-matrix morphology (which is typical of PLA/PCL blends discussed in this contribution) during simple shear or elongational flow is qualitatively well understood. However, quantitative prediction of particle size distribution in real systems is extremely challenging due to complexity of the flow fields in mixing and processing devices and complex rheological behavior of molten polymers. The results of previous studies can be briefly summarized as follows: (i) The particle sizes in the blends containing the same components and prepared at the same conditions increase with the concentration of the minor component. (ii) The smallest particle size is usually obtained when viscosities of the dispersed phase and matrix are comparable. (iii) The particle size increases with interfacial tension between the blend components. (iv) The particle size in molten blends increases in quiescent state and in slow flow, which means that an increase in the particle size appears during compression molding. (v) Addition of a compatibilizer decreases the size of the dispersed particles during mixing and stabilizes the blend morphology at processing; this effect is stronger for blends with a higher content of the dispersed phase.
This review aims at the evaluation of the results of studies of the morphology, compatibility and mechanical properties of PLA/PCL blends with respect to the control of the blend toughness and crystallinity. The conclusions of this contribution should answer the question if and how the blending of PLA with PCL can lead to the material with required mechanical properties.
Many papers have been focused on the morphology and mechanical properties of PLA/PCL blends. As for the stiffness, all studies are in agreement that the modulus and yield strength of PLA/PCL blends decreases with the PCL content. This behavior is typical of the blends combining stiff and soft polymers (Horak et al., 2005) and thus the stiffness is not discussed in the following text. However, the results related to the toughening of PLA by means of blending with PCL seem to be contradictory at first sight. These results are discussed below. The ratios of toughness, aBl/aPLA, and elongation at break, εBl//εPLA, of PLA/PCL blends to neat PLA together with crystallinity of PLA, , and average diameter of PCL particles, d, are summarized in Table 1.
Table 1. Ratio of toughness, aBl/aPLA, and ratio of elongation at break, εBl/εPLA, of PLA/PCL blends and neat PLA as a function of diameter of PCL particles, d, and crystallinity of PLA matrix, .
None or weak enhancement in the toughness of PLA by its blending with PCL has been found in a major part of previous studies. López-Rodríguez et al. (2006) found very small increase in strain at break (to 1.3%) together with strong decrease in strength at yield and strength at break for PLLA/PCL (80/20) blends in comparison with neat PLLA. Carmona et al. (2015) found only a small increase in elongation at break for an extrusion prepared PLA/PCL (50/50) blend with respect to PLA but strong decrease with respect to PCL. Gardella et al. (2014) and Monticelli et al. (2014) obtained the same elongation at break for PLA/PCL (70/30) blend prepared in a batch mixer as for neat PLA. The blend contained remarkable amount of large PCL particles.
Tsuji and Ikada (1996) studied the morphology and the properties of the blends of poly(D,L-lactide) containing 50% of D-isomer (PDLLA) with PCL, which were prepared by solution casting. They found that the dependence of the elongation at break on the PDLLA/PCL composition is non-monotonic with a minimum around 50/50 composition. Similar dependence of the elongation at break on the composition of the blends prepared from 100% L-isomer of PLA (PLLA) with PCL was obtained by Tsuji et al. (2003). Simoes et al. (2009) found negligible increase in elongation at break and about twice larger Charpy impact strength for PLA/PCL (75/25) blends in comparison with neat PLA. Mittal et al. (2015) found only a small increase in the value of elongation at break of the PLA/PCL (50/50) blends with respect to neat PLA, deeply below the additive value.
Vilay et al. (2009) studied the morphology, thermal behavior, and mechanical properties of PLLA/PCL blends. They found only weak increase in the elongation at break with the increasing content of PCL in the PLLA/PCL blends. Similar result for elongation at break was obtained also by Finotti et al. (2016) for PLA/PCL blends with commercial PLA. Only very small increase in the impact strength was found for PLLA/PCL (85/15) blends having crystallinity of PLLA matrix about 25% by Todo et al. (2007). Authors of the above studies and authors of a review considering these results (Imre and Pukánszky, 2013) concluded that PLA and PCL are incompatible polymers, i.e., that their large interfacial tension results in coarse morphologies and inferior mechanical performance. Therefore, the compatibilization was regarded as necessary for the preparation of PLA/PCL blends with high toughness.
Recently, Kassos et al. (2019) studied the effect of concentration of PCL on mechanical properties of samples of PLA/PCL blends prepared by the mixing in a twin screw extruder, followed by an injection molding. They found that the notched Izod impact strength increased with increasing content of PCL. However, this increase was quite weak: The impact strength of PLA/PCL (70/30) was about twice of that for neat PLA. Moreover, they observed strange dependence of elongation at break on PCL concentration: After strong increase for PLA/PCL (95/5) blend, the elongation at break decreased for higher amounts of PCL (compositions 80/20 and 70/30) to the values comparable with neat PLA.
Surprisingly enough, the results of a few other studies are in a partial or full contradiction with the conclusions in the previous section. Takayama et al. (2011) studied the character of the fracture in PLA/PCL blends without and with a compatibilizer. They found ductile character of the fracture in the quenched PLA/PCL blends. On the other hand, brittle fracture was detected for PLA/PCL blends annealed with the aim to enhance crystallinity of PLA. Yeh et al. (2009) found a steep increase in the strain at break with the content of PCL above 10% for PLA/PCL blends. Similar dependence of the strain at break on the content of PCL in PLA/PCL blends was found also Zhao and Zhao (2016) for injection molded samples.
Ferri et al. (2016) studied elongation at break and unnotched Charpy impact strength of PLA/PCL blends containing up to 30% of PCL. The blends were prepared by extrusion followed by injection molding. The authors found substantial increase in the elongation at break but no enhancement of the impact strength of the blends with respect to neat PLA. Quiles-Carrillo et al. (2018) studied the toughness of PLA blends containing 40% of a mixture of PCL with thermoplastic starch (TPS). They found substantial increase in the elongation at break for the blends having content of TPS up to 20%. On the other hand, the notched Charpy impact strength of PLA/PCL (60/40) blend was only about 3 times higher than that of the neat PLA.
Bai et al. (2012) studied the effect of the crystallinity of the PLA matrix on the impact strength of PLA/PCL blends. The samples of these blends were prepared by the extrusion followed by the injection molding using a HAAKE MiniJet. The crystallinity of PLA was controlled by the concentration of a nucleation agent [N,N',N” tricyclohexyl-1,3,5-benzene-tricarboxylamide (TMC)] and by the temperature of the mold. It was found that the notched Izod impact strength of neat PLA was almost independent of its crystallinity. On the other hand, the impact strength of PLA/PCL blends grew with the crystallinity of PLA. The rate of this growth increased with the increasing content of PCL in the blends. The PLA/PCL (80/20) blend with the PLA crystallinity about 50% showed the impact strength more than 13 times higher in comparison with neat PLA.
In their further paper, Bai et al. (2013) studied the dependence of the impact strength on the size of PCL particles in PLA/PCL (80/20) blends with a low and high crystallinity of the PLA matrix. The blends were prepared by the same technology as in the preceding paper (Bai et al., 2012). The PCL particle size distribution and the PLA crystallization were controlled by the addition of TMC and the variation of the extruder screw rotation speed, by the mold temperature and by the annealing time in the mold. The dependence of the notched Izod impact strength on the weight average of the PCL droplet diameter, dw, differed for the blends with low- and high-crystallinity PLA matrix. For the blends with the low PLA crystallinity (6.5–9.5%), the maximum impact strength was achieved for dw between 0.7 and 1.1 μm. For the blends with the high PLA crystallinity (46–48%), the maximum of the impact strength was found for dw between 0.3 and 0.5 μm. This was is in quite good agreement with the value of dw between 0.2 and 0.4 μm referred for blends with semicrystalline matrixes elsewhere (Bucknall and Paul, 2009). These dependences are reproduced in Figure 1. It should be mentioned that the maximum value of the impact strength achieved for the blends with the high PLA crystallinity was almost two times higher than that of the blends with a low PLA crystallinity.
Figure 1. Comparison of dependences of the impact strength on the size of PCL particles in PLA/PCL(80/20) blends with almost amorphous and with highly crystalline PLA matrices. Reprinted with permission from Bai et al. (2013). Copyright 2013, Elsevier.
Urquijo et al. (2015) studied the dependence of morphology and mechanical properties on the PCL content in PLA/PCL blends prepared by extrusion followed by injection molding. They detected a fine morphology of the PLA/PCL blends and a good adhesion between the PLA and PCL phases. The elongation at break was strongly enhanced by the addition of 10% of PCL and did not change with further increase in the PCL amount till 40%. The notched Izod impact strength increased monotonically with the increasing content of PCL in the blends. The values of the ratios aBl/aPLA and εBl/εPLA for PLA/PCL (80/20) blends can be found in Table 1. However, the ratio of the impact strength of the PLA/PCL (80/20) blend to that of neat PLA was substantially lower (almost 3 times) than the maximum ratio observed by Bai et al. (2013) for PLA/PCL blends with a low-crystallinity PLA matrix. This could be attributed to the fact that the PCL particle size in the study of Urquijo et al. (2015) was below the optimum size reported by Bai et al. (2013) for the blends with the similar PLA crystallinity.
Ostafinska et al. (2015) studied the dependence of the morphology and mechanical properties of the PLA/PCL blends (with almost the same viscosities of the PLA and PCL components) on the content of PCL for the blends prepared by the melt-mixing in a batch mixer followed by the compression molding. The crystallinity of PLA in these blends was between 6.4 and 9.7%. It was found that PLA/PCL blends with PCL content till 30% formed typical droplets-in-matrix morphology, where the size of PCL particles increased with the PCL concentration, while the PCL content above 40% resulted in coarse co-continuous morphology, as evidenced Figure 2. Charpy notched impact strength of PLA/PCL blends steeply increased with the content of PCL up to 20%. Further increase in the amount of PCL led to a decrease in the impact strength of the PLA/PCL blends. The impact strength of PLA/PCL (80/20) blend was more than 16 times higher in comparison with neat PLA (Figure 3). This was even higher than the maximum ratio achieved by Bai et al. (2013) for the blends with the high crystallinity of PLA (Table 1). The decrease in the impact strength with the increasing content of PCL for the blends with the PCL content above 20% appeared simultaneously with the steep increase in the average particle size, which was accompanied by the increasing width of the particle size distribution.
Figure 2. SEM micrographs showing morphology of compression molded PLA/PCL blends with composition (wt.%/wt%): (A) 90/10, (B) 80/20, (C) 70/30, and (D) 60/40. The samples were smoothed and PCL was etched off as described in Ostafinska et al. (2015). Note the scale change in the last micrograph with coarse continuous morphology of PCL phase.
Figure 3. Charpy notched impact strength of PLA/PCL blends as a function of their composition; error bars represent standard deviations. Adapted with permission from Ostafinska et al. (2015).
Further paper of Ostafinska et al. (2017) was focused on the effect of melt viscosity of the PLA matrix on the morphology and toughness of PLA/PCL (80/20) blends, prepared by same procedure as in their preceding paper (Ostafinska et al., 2015). It was found that the number and volume averages of diameters of the PCL droplets increased with the decreasing viscosity, i.e., molecular weight, of the PLA matrix (Figure 4). Neat samples of PLA had similar impact strength and their viscosity decreased in in the following order: PLA1 > PLA2 > PLA3, where PLA1 was identical with PLA used in the preceding study (Ostafinska et al., 2015) and had almost the same viscosity as PCL. The toughness of the blends was characterized not only by the Charpy notched impact strength, but also by the instrumented impact testing. Both Charpy notched impact strength (determined from non-instrumented impact testing) and total fracture energy (determined from instrumented impact testing) decreased with the increasing size of PCL particles (Figure 5). PLA1/PCL blend showed super-tough behavior (i.e., the blend toughness was higher than the toughness of either of its two components) but PLA3/PCL blend showed toughness only slightly enhanced in comparison with neat PLA3. The toughness of PLA2/PCL blend was in between the values found for the PLA1/PCL and PLA/PCL blends. Detailed analysis of load-deflection diagrams from instrumented impact testing (Figure 6) revealed that the particle morphology influenced not only final total values of fracture energy, but also the entire character of fracture. The fracture mechanism changed from elastic-plastic with stable crack propagation (Figure 6A; blend PLA1/PCL), to elastic-plastic stable followed by unstable crack propagation (Figure 6B; blend PLA2/PCL), and finally to linear elastic or brittle (Figure 6C; blend PLA3/PCL).
Figure 4. SEM micrographs (A–C) and corresponding particle size distributions (D–F) of PLA/PCL (80/20) blends prepared from three different PLAs with decreasing viscosity [η(PLA1) > η(PLA2) > η(PLA3)]. The abbreviations 2dN% and 2dV% denote number and volume distributions, respectively. Reprinted with permission from Ostafinska et al. (2017). Copyright 2017, Elsevier.
Figure 5. The values of (A) non-instrumented and (B) instrumented Charpy notched impact strength for PLA/PCL(80/20) blends with decreasing viscosity of the matrix, whose morphology is shown in Figure 4. Adapted with permission from Ostafinska et al. (2017).
Figure 6. Load-deflection curves (F-f diagrams) of PLA/PCL(80/20) blends from the instrumented Charpy notched-impact test. The blends were prepared from the three different types of PLA with decreasing viscosity as described in Ostafinska et al. (2017): (A) the highest viscosity of PLA, (B) a medium viscosity of PLA, and (C) the lowest viscosity of PLA. Morphology of the blends and their integral impact strength are shown in Figures 4, 5, respectively. Ael, Apl, and AR represent elastic, plastic and residual part of total fracture energy, respectively. Fg and fg are the characteristic load and deflection values at yield, corresponding to the transition from elastic to elastic-plastic behavior, respectively; Fm and fm are the characteristic load and deflection values corresponding to the onset of crack propagation, respectively. Adapted with permission from Ostafinska et al. (2017).
Recently, we tried to obtain PLA/PCL (80/20) blends with a sufficient toughness and an enhanced crystallinity by the addition of talc as a nucleation agent and/or by the modification of thermal treatment during the compression molding, using sample preparation procedure analogous to that described in Ostafinska et al. (2015) and Ostafinska et al. (2017). We found that the annealing time necessary for enhancement of PLA crystallinity above 40% in blends without talc is detrimental for the impact strength of PLA/PCL (80/20) blends. On the other hand, after addition of 1% of talc, the crystallinity of about 36% and Charpy notched impact strength almost 10 times higher in comparison with neat PLA were obtained (Table 1, the last row). This impact strength was substantially lower than that for PLA/PCL (80/20) blends having PLA crystallinity below 10% (compare Table 1 and Figure 3) but it could be sufficient for a number of applications.
The explanation of different results of previous studies is somewhat complicated by the fact that the authors used various grades of PLA and various methods of the PLA/PCL blends preparation, such as direct continuous or discontinuous melt blending, or solution mixing. On the other hand, neither the small differences in the content of D-isomer in PLA, nor differences in molecular weights of PLA and/or PCL should have a decisive effect to the interfacial tension and adhesion between PLA and PCL. Therefore, the PLA/PCL blends cannot be considered as incompatible in the sense that they cannot exhibit good mechanical performance. However, differences in the molecular weights have strong impact to the rheological properties of polymers, which together with compounding and processing conditions control the size of PCL particles. As mentioned in the introduction, it is well known that the toughness of polymer blends depends critically on the size of the dispersed particles of a blend soft component (Bucknall, 2000; Horak et al., 2005; Bucknall and Paul, 2009, 2013). The optimum particle size for the maximization of the impact strength at a certain volume fraction of the dispersed phase is a function of the dominating toughening mechanism which depends on the crystallinity of the matrix. An analysis of the above results lead us to the conclusion that different toughening mechanisms are dominating in PLA/PCL blends with a low crystallinity PLA (till about 10%) and with a high crystallinity PLA (above 30%). Therefore, the optimum size of PCL particles is substantially different for the blends with a low and with a high crystallinity of PLA.
For example, we believe that the discrepancy between the strong enhancement of elongation at break and rather small enhancement of impact strength, observed by Urquijo et al. (2015) for PLA/PCL blends with a low crystallinity of PLA, results from unfavorable size of PCL particles and not from the incompatibility of PLA and PCL grades used in given study. According to results of Bai et al. (2013), the PCL particles in the study of Urquijo et al. (2015) seem to be too small for efficient improvement of the impact strength. However, their concentration and fine dispersion are sufficient to improve maximum elongation of the blend. We conclude that a too rough phase structure of PLA/PCL blends leads to insufficient improvement both impact strength and elongation at break. On the other hand, a very fine phase structure (such as that observed by Urquijo et al., 2015) can lead to the insufficient impact strength (especially for the blends with a low crystallinity of PLA), but the extensibility can be quite large.
The dependence of the impact strength of PLA/PCL (80/20) blends on the size of PCL particles was well documented by Bai et al. (2013). Moreover, the results of Bai et al. (2013) were confirmed by later studies of Ostafinska et al. (2015, 2017): The average size of the PCL droplets in super-tough PLA/PCL (80/20) blends with low crystallinity PLA matrix detected in Ostafinska et al. (2015, 2017) was in a good agreement with results in Bai et al. (2013). The weight average of the particle diameter, dw = 0.8 μm obtained for the maximum impact strength in Bai et al. (2013) corresponded quite well to the diameter number average, dn = 0.6 μm, and diameter volume average, dV = 1.3 μm, determined in Ostafinska et al. (2015). It should be mentioned that zones with different particle size appear in PLA/PCL blends prepared by the methods, which are supposed to yield the samples with uniform phase structure (Fortelny et al., 2015; Ostafinska et al., 2015, 2017). Therefore, the droplet size distribution in references (Ostafinska et al., 2015, 2017) was evaluated by MDISTR program package (Slouf et al., 2015), which takes this nonuniformity into account. The non-uniformity of the phase structure negatively affects the reliability of conventional methods of determination of the average droplet size based on evaluation of several hundreds of particles (Fortelny et al., 2008). Further complication for determination of optimum size of PCL particles is obvious non-uniformity in the morphology of samples prepared by injection molding. Morphology of these samples changes from shell to core and depends on the sample shape and dimensions. Therefore, it can be only estimated that dw somewhat below 0.5 μm is optimal for PCL particles in PLA/PCL (80/20) blends with a high crystallinity of PLA. PCL particles with dw somewhat above 1 μm seems to be most efficient for toughening of PLA/PCL (80/20) blends with a low crystallinity of PLA.
Nevertheless, it is apparent that the relatively low impact strength of the PLA/PCL blends in Urquijo et al. (2015) could be explained as a consequence of smaller size of PCL droplets than was optimal for the blends with a low PLA crystallinity. On the other hand, the brittle behavior of the PLA/PCL (70/30) blends obtained in Gardella et al. (2014) and Monticelli et al. (2014) and the decrease of toughness in the blends with content of PCL above 20% detected in Ostafinska et al. (2015) were apparently caused by too large size of the PCL droplets and by their broad size distribution.
It can be concluded that PLA and PCL are not incompatible because their blends can exhibit good mechanical properties. It means that the value of the interfacial tension between PLA and PCL does not prevent the preparation of PLA/PCL blends with a fine phase structure and a sufficient adhesion at the interface. On the other hand, the toughness of the PLA/PCL blends is extremely sensitive to the size of PCL particles. This was confirmed by the fact that an increase of number average diameter, dn, from 0.6 to 0.9 μm and of volume average diameter, dV, from 2.2 to 3.6 μm for PLA/PCL (80/20) blends led to the decrease in the Charpy notch impact strength from 38 to 6 kJ/m2 and to the change in the character of the blend fracture from ductile to brittle (Ostafinska et al., 2017). Therefore, the size of PCL particles must be carefully controlled during the processing of PLA/PCL blends that should exhibit high toughness. It is not an easy task, especially for the blends where enhanced crystallinity of PLA is required. These blends should contain small PCL particles (with dw below about 0.5 μm) and simultaneously their preparation requires elevated temperature and longer time in a hot press or a mold even if a nucleation agent is added (Bai et al., 2013). Unfortunately, an increase in the PCL particle size during melt annealing is quite rapid; dV increased about twice during compression molding of PLA/PCL (80/20) blend and even stronger increase in the size of PCL particles was detected for blends with a higher content of PCL (Fortelny et al., 2015).
Most of the studies dealing with the effect of a compatibilizer on the structure and properties of PCL/PLA blends have been inspired by the assumption that the addition of a compatibilizer is necessary for the preparation of the blends with high toughness. Nevertheless, as explained and evidenced in the previous section, a compatibilization is not necessary for the tough PLA/PCL blends. On the other hand, compatibilizers can help with a preparation of the polymer blends with a fine phase structure for broader range of rheological properties of the components and for broader range of mixing conditions. It is also very important that compatibilizer can efficiently suppress changes in the phase structure during polymer blends processing (Macosko et al., 1996; Marić and Macosko, 2002; Horak et al., 2005).
There are three methods of compatibilization of immiscible polymer blends (Huang, 2011). At physical (or additive) compatibilization (Horak et al., 2005; Huang, 2011), block or graft copolymers with blocks identical, miscible or similar with the blend components are added to the blend during a compounding. At reactive compatibilization (Horak et al., 2005; Huang, 2011), copolymers (mostly grafted) are formed during the blend melt-mixing due to chemical reactions between functional groups on the blend components; the newly-formed copolymers act as compatibilizers. Addition of an admixture of functionalized components and/or initiation by reactive low-molecular-weight agents is frequently applied at reactive compatibilization. More recently it was found that also some nanofillers can serve as efficient compatibilizers for polymer blends besides of block and graft copolymers (Ray et al., 2004; Huang, 2011; de Luna and Filippone, 2016). The effects of various types of compatibilizers are discussed below. The ratios of values of the impact strength (a) and of the elongation at break (ε) for both compatibilized and non-compatibilized (neat) blends, acomp/aneat, and, εcomp/εneat, respectively, are summarized in Table 2.
Table 2. Ratios of toughness, acomp/aneat, and elongation at break, εcomp/εneat, of compatibilized and neat blends for various compatibilizers.
Several papers were focused on compatibilization of PLA/PCL blends with various premade PLA-PCL block copolymers, and those detailing the effects on mechanical properties are summarized in Table 2. Dell'Erba et al. (2001) showed that the addition of PLLA-b-PCL-b-PLLA triblock copolymer to PLLA/PCL blends substantially reduced the size of PCL particles. Mechanical properties of PLLA/PCL/PLLA-b-PCL-b-PLLA blends were not studied in this paper. Wu et al. (2010) studied the effect of diblock PCL-b-PLA and triblock PLA-b-PCL-b-PLA copolymers on the morphology and the viscoelastic properties of PLA/PCL (30/70) blends. They found that the both copolymers improved the interfacial properties and substantially reduced the size of PCL particles. The compatibilization of PLA/PCL blends by PCL-b-PLA block copolymer was studied also by Kim et al. (2000). However, the study was focused on the crystallinity of the blend components and did not provide the mechanical properties of the compatibilized blends. Recently, Xiang et al. (2019) studied compatibilization efficiency of PLLA-b-PCL block copolymers having various compositions and molecular weights for PLLA/PCL (80/20) blends prepared in a batch mixer. Addition of 5% of these copolymers caused reduction of the PCL particle size and substantially enhanced elongation at break. PLLA-b-PCL copolymers with similar contents of PLLA and PCL and with large molecular weights showed the largest effects. Impact strength of the blends was not determined in this study.
Further studies dealt with compatibilization of PLA/PCL by premade block copolymers having blocks miscible with the blend components. Maglio et al. (2004) studied the effect of PLLA-b-PCL-b-PLLA and diblock copolymer of PLLA with poly(ethylene oxide) (PEO) on the size of PCL droplets in PLLA/PCL (70/30) blends. They found that the addition of 2% of PLLA-b-PCL-b-PLLA or PLLA-b-PEO substantially reduced the size of PCL particles; PLLA-b-PEO was more efficient than PLLA-b-PCL-b-PLLA copolymer. Mechanical properties of the compatibilized blends were not characterized. Vilay et al. (2010) studied the compatibilization efficiency of a copolymer of PEO and poly(propylene oxide) (PPO) (triblock copolymer PEO-b-PPO-b-PEO) for PLLA/PCL (70/30) blends. They found that the addition of the copolymer reduced the size of PCL particles and enhanced interfacial adhesion. Fracture energy of PLLA/PCL/PEO-b-PPO-b-PEO blends steeply increased with the content of PEO-b-PPO-b-PEO. Wachirahuttapong et al. (2016) studied the effect of triblock copolymer poly(ethylene glycol)-poly(propylene glycol)-poly(ethylene glycol) (PEG-b-PPG-b-PEG) on the morphology and mechanical properties of PLA/PCL blends. They assumed that PEG-b-PPG-b-PEG copolymer behaved as plasticizer in PLA/PCL blends and, therefore, reduced size of PCL particles in blends with low PCL contents. The elongation at break increased with the amount of added PEG-b-PPG-b-PEG. Na et al. (2002) studied the structure, the thermodynamic properties, and the mechanical properties of PLLA/PCL and PDLLA/PCL blends compatibilized with PCL-b-PEG. They showed that PCL-b-PEG copolymers can be an efficient compatibilizer for PLA/PCL but detected only a moderate improvement in the elongation at break. The largest εcomp/εneat was achieved for PDLLA/PCL (80/20) compatibilized with 10% of PCL-b-PEG.
Finotti et al. (2016) studied the compatibilization of PLA/PCL blends by low-molecular-weight block copolymers of ε-caprolactone with tetra-methylene ether glycol or aliphatic polycarbonate. The addition of 5% of the copolymers substantially reduced the size of PCL droplets in the PLA/PCL (80/20) blends. The elongation at break of PLA/PCL was relatively low but it increased with the PCL content. Surprisingly, the compatibilized PLA/PCL (95/5) blends showed a high elongation at break, which was much larger than that for the compatibilized PLA/PCL (80/20) blends. Dias and Chinelatto (2019) compatibilized PLA/PCL (75/25) with low-molecular-weight triblock copolymer ε-caprolactone-tetrahydrofuran-ε-caprolactone. Addition of the copolymer did not lead to the reduction of the size of PCL particles and had negligible effect on the Izod impact strength of the blend. On the other hand, strain at break increased substantially with copolymer content in the blend. Song et al. (2018) found a decrease in the size of PCL particles and substantial increase in elongation at break for PLA/PCL (80/20) and (70/30) blends after addition of a small amount of polyoxymethylene (POM). They explained compatibilization effect of POM as a consequence of hydrogen bonds formation between POM and PLA and PCL chains. The authors did not study the effect of POM on the impact strength of PLA/PCL blends.
The reactive compatibilization of PLA/PCL blends was studied quite intensively by various authors for composition with PCL in the range 15–30% by wt., as summarized in Table 2. Gardella et al. (2014) studied the effect of the substitution of a part of PLA by maleic-anhydride-grafted polylactide (PLA-g-MA) on the morphology and toughness of PLA/PCL (70/30) blends. It was found that the average size and the width of the size distribution of PCL particles decreased with the amount of PLA substituted with PLA-g-MA. Also the melting enthalpy of PLA increased with the amount of PLA-g-MA. However, the highest increase in the elongation at break with respect to the neat PLA/PCL (70/30) was observed when just 10% of PLA was substituted with PLA-g-MA, whereas higher contents of PLA-g-MA led to surprising decrease in the elongation at break.
Takayama et al. (2011) added 1% of lysine triisocyanate (LTI) to PLA/PCL (85/15) blends. They found that PLA/PCL/LTI contained smaller PCL particles and had a higher fracture energy than the original PLA/PCL blend. Annealing of the compatibilized PLA/PCL/LTI blend lead to an increase in the PLA crystallinity and caused an increase in the fracture energy. On the other hand, annealing of the non-compatibilized PLA/PCL blend was followed by a pronounced decrease in its fracture energy. Harada et al. (2008) compared efficiency of 4 isocyanates at reactive compatibilization of PLA/PCL blends. They found that LTI is the most efficient compatibilizer. Addition of LTI during compounding led to a remarkable reduction of the size of PCL particles and to a strong increase in the notched and unnotched Charpy impact strengths and in the elongation at break.
Chee et al. (2013) studied the reactive compatibilization of a PLA/PCL blend by the addition of glycidyl methacrylate (GMA) at blending. They found that the elongation at break and the unnotched Izod impact strength of PLA/PCL (85/15) blend increased with the amount of added GMA until 3%. For more than 3% of GMA, the blend impact strength and the elongation at break decreased with the amount of GMA. Shin and Han (2013) studied the effects of the addition of GMA and of the following irradiation of PLA/PCL/GMA blends. They found that the addition of GMA without the following irradiation led to a decrease in the size of the PCL droplets and to an increase in the elongation at break of the PLA/PCL blends. The ratio εcomp/εneat ≈ 6 was achieved for PLA/PCL/GMA blends without irradiation. The stiffness of PLA/PCL/GMA blends increased and their elongation at break decreased with the applied irradiation dose due to induced crosslinking.
Semba et al. (2007) studied the effect of dicumyl peroxide (DCP) and the split of feeding on the mechanical properties of PLA/PCL (70/30) blends prepared by a compounding in a twin screw extruder followed by an injection molding. They found that the elongation at break of the PLA/PCL blend was substantially large than that of the neat PLA. It was further enhanced by the addition of DCP. Only slight dependence of the elongation at break on the feeding procedure was detected. Notched Izod impact strength of PLA/PCL blend was less than twice of that for neat PLA. Addition of DCP enhanced notch Izod impact strength to the value about three times larger than that for neat PLA. The differences among the final properties for the samples prepared by various feeding procedures were lower than those caused by the DCP addition.
Various nanofillers were added to PLA/PCL blends with the aim to improve their toughness. Monticelli et al. (2014) compatibilized PLA/PCL (70/30) blends with functionalized polyhedral oligomeric silsequioxane (POSS) molecules. POSS's having different functional groups and POSS's grafted with PCL-b-PLA block copolymers were employed. It was found that the POSS's containing a hydroxyl group and especially the POSS's grafted with PCL-b-PLA reduced the size of the PCL particles and improved the adhesion between PLA and PCL. Only the addition of POSS-g-PCL-b-PLA led to remarkable improvement in the elongation at break but still to insufficient value (only to 2.5 times of neat PLA as shown in Table 2). Impact strength of these blends was not measured.
Urquijo et al. (2016) studied the effect of organically modified montmorillonite (OMMT) on the structure and the mechanical properties of PLA/PCL (80/20) blends. They found that the stiffness of PLA/PCL/OMMT nanocomposites increased, while the elongation at break and notched Izod impact strength decreased with the increasing content of OMMT. The decrease in the elongation at break was from 140% for PLA/PCL (80/20) to 15% for PLA/PCL/OMMT (80/20/6). The notched Izod impact strength decreased from about 30 J/m for neat blend to about 15 J/m for composite containing almost 6% of OMMT. Sabet and Katbab (2009) showed that addition of modified montmorillonite reduced size of the PCL particles in PLA/PCL (80/20) blends. The effect was strengthened by further addition of maleic anhydride grafted polypropylene. The toughness of PLA/PCL blends was not determined in this paper.
Forouharshad et al. (2015) studied the effect of the addition of high surface area graphite (HSAG) on the morphology and the properties of PLA/PCL. They found a decrease in the PCL particle size and a rather small increase in elongation at break of the blends as a consequence of the addition of HSAG. This increase was insufficient for practical applications because the achieved elongation at break for PLA/PCL (70/30) blend was equal to neat PLA only.
Analysis of the above-mentioned results leads us to the conclusion that the improvement of the toughness of PLA/PCL blends by the addition of a compatibilizer is caused mostly by the fact that the compatibilizer influences the average size of the PCL particles. In numerous compatibilized PLA/PCL blends studied previously, the toughness had not been improved significantly after the addition of a compatibilizer (Table 2). It seems that the optimum size of the PCL droplets with respect to the crystallinity of PLA (for pure PLLA and PLA with a low content of D-isomer) is decisive also for toughness of PLA/PCL blends regardless of the compatibilization. However, the compatibilization can help to obtain tough PLA/PCL blends with inconvenient rheological properties of their molten components, when the PCL particles are too big to achieve the high toughness. This is especially important for the blends with a high crystallinity of PLA matrix, where small PCL particles are needed for achievement of high impact strength of PLA/PCL blends. Moreover, a proper compatibilizer can stabilize the size of the PCL particles in the PLA/PCL blends during their further processing.
The analysis of literature suggests that the size distribution of PCL particles is decisive for the toughness of PLA/PCL blends independently of the presence of a compatibilizer. The optimum size of the PCL particles depends on the degree of crystallinity of PLA. The impact strength of the PLA/PCL blends with a certain composition is extremely sensitive to the size of PCL particles (Ostafinska et al., 2017). Therefore, the optimum PCL particle size for the blends with a certain composition and given crystallinity of the PLA matrix should be known in order to prepare the PLA/PCL blend with the maximum impact strength. This requirement is of unusually high importance for PLA/PCL blends in comparison with common blends of synthetic polymers, such as polypropylene/ethylenepropylene rubber blends (Pitt, 1990), due to a quite narrow window of the size of PCL particles for which sufficiently high impact strength of PLA/PCL blends can be achieved. The determination of the optimum size of the PCL particles is not a trivial task. The droplet size in samples prepared by some processing methods, e.g., by injection molding, obviously varies and depends on specific locations of the specimen. Moreover, the PLA/PCL blends showed non-uniform phase structure (with different zones containing smaller or bigger particles) even in samples prepared by compression molding, which was expected to show a weak dependence of droplet size on the specific location within the final specimen (Ostafinska et al., 2015, 2017).
Our analysis of the results for PLA/PCL blends with a low crystallinity of PLA matrix (up to ~10%) confirmed that previous authors prepared blends containing PCL droplets with various sizes, which ranged from quite small (diameters below 0.5 μm) to fairly large (diameters above 3 μm). The size of the PCL particles depended on the choice of the rheological properties of the blend components (through their molecular weights) and on the methods of the blend mixing and processing. The application of an efficient compatibilization method could reduce the size of PCL particles and stabilize the morphology of PLA/PCL blends during further processing.
The preparation of the PLA/PCL blends with a high crystallinity of PLA matrix (for high stiffness at elevated temperatures) and the optimum size of PCL particles (for high toughness) seems to be even more difficult task. The optimum size of the PCL particles in the PLA/PCL blends with high-crystallinity matrix is lower in comparison to the blends with a low-crystallinity matrix. For the blends without a compatibilizer, the small PCL particles can be obtained only by intensive mixing followed by fast injection molding. It should be mentioned that not all commercial grades of PLA are designed for injection molding. There is a certain necessary time of annealing in the temperature range above Tg of PLA needed for its crystallization even for the blends containing efficient nucleation agents (Bai et al., 2012, 2013). Moreover, even short annealing of the PLA/PCL blends usually leads to an increase in the size of PCL particles because PLA matrix at higher temperatures above its Tg softens and PCL minority phase above its Tm melts, which results in the reorganization of PCL particles. Therefore, choice of efficient method of preparation of PLA/PCL blends with enhanced crystallinity of PLA and optimum size of PCL particles is very challenging. Detailed information about the crystallization of PLA during various temperature regimes is necessary for the optimization of the blend preparation method. The compatibilization of PLA/PCL blends with a high crystallinity of PLA seems to be more important than in the case of the blends with a low crystallinity of PLA.
The structure and the properties of the matrix are decisive for the optimal size distribution of soft (elastomer) dispersed particles serving for the improvement of the matrix toughness (Bucknall, 2000; Horak et al., 2005). Therefore, the dependences of the toughness of blends of PLA with other elastomeric biopolymers on the size of elastomeric droplets are expected to be similar to those for PLA/PCL blends.
PLA and PCL are immiscible polymers but their interfacial tension is quite low. Therefore, PLA/PCL blends having good mechanical properties, namely the high impact strength, can be prepared without the addition of a compatibilizer.
The toughness of the PLA/PCL blends is highly sensitive to the size of PCL particles. The optimum size of PCL particles decreases with the crystallinity of PLA matrix.
The compatibilization of the PLA/PCL blends can stabilize their phase structure during the processing and help with the optimization of the PCL particle size. This holds especially in the case of the unfavorable rheological properties of the PLA and PCL components and/or the unfavorable methods of the PLA/PCL preparation.
The determination of the optimum size of PCL particles as a function of PLA crystallinity and establishing the efficient methods for reproducible preparation of the stable PLA/PCL blends with the required size of PCL particles are challenges for future research.
IF summarized literature and wrote a major part of the manuscript with contributions of AU, LF, and MS. MS initiated the project focused on biodegradable PLA/PCL blends, prepared images for the manuscript, and finalized the manuscript.
Financial support through grants TN01000008 (TA CR), TE01020118 (TA CR) and POLYMAT LO1507 (MEYS CR, program NPU I) is gratefully acknowledged.
The authors declare that the research was conducted in the absence of any commercial or financial relationships that could be construed as a potential conflict of interest.
Auras, R., Harte, B., and Selke, S. (2004). An overview of polylactides as packaging materials. Macromol. Biosci 4, 835–864. doi: 10.1002/mabi.200400043
Averous, L., and Pollet, E. (2012). Environmental Silicate Nano-Biocomposites. London: Springer, 13–39.
Bai, H., Huang, C., Xiu, H., Gao, Y., Zhang, Q., and Fu, Q. (2013). Toughening of poly(L-lactide) with poly(epsilon-caprolactone): combined effects of matrix crystallization and impact modifier particle size. Polymer 54, 5257–5266. doi: 10.1016/j.polymer.2013.07.051
Bai, H., Xiu, H., Gao, J., Deng, H., Zhang, Q., Yang, M., et al. (2012). Tailoring impact toughness of poly(L-lactide)/poly(epsilon-caprolactone) (PLLA/PCL) blends by controlling crystallizatior of PLLA matrix. ACS Appl. Mater. Interfaces 4, 897–905. doi: 10.1021/am201564f
Bucknall, C. B. (2000). Deformation mechanisms in rubber-toughened polymers, in The Polymer Blends, V. 2: Performance, eds. Bucknall, C. B., and Paul, D. R. (New York: John Wiley & Sons, 83–136.
Bucknall, C. B., and Paul, D. R. (2009). Notched impact behavior of polymer blends: part 1: new model for particle size dependence. Polymer 50, 5539–5548. doi: 10.1016/j.polymer.2009.09.059
Bucknall, C. B., and Paul, D. R. (2013). Notched impact behaviour of polymer blends: part 2: dependence of critical particle size on rubber particle volume fraction. Polymer 54, 320–329. doi: 10.1016/j.polymer.2012.11.019
Carmona, V. B., Correa, A. C., Marconcini, J. M., and Mattoso, L. H. C. (2015). Properties of a biodegradable ternary blend of thermoplastic starch (TPS), poly(epsilon-caprolactone) (PCL) and poly(lactic acid) (PLA). J. Polym. Environ. 23, 83–89. doi: 10.1007/s10924-014-0666-7
Chee, W. K., Ibrahim, N. A., Zainuddin, N., Rahman, M. F. A., and Chieng, B. W. (2013). Impact toughness and ductility enhancement of biodegradable poly(lactic acid)/poly(ε-caprolactone) blends via addition of glycidyl methacrylate. Adv. Mater. Sci. Eng. 2013:976373. doi: 10.1155/2013/976373
de Luna, M. S., and Filippone, G. (2016). Effects of nanoparticles on the morphology of immiscible polymer blends - challenges and opportunities. Europ. Polym. J. 79, 198–218. doi: 10.1016/j.eurpolymj.2016.02.023
Dell'Erba, R., Groenickx, G., Maglio, G., Malinconico, M., and Migliozzi, A. (2001). Immiscible polymer blends of semicrystalline biocompatible components: thermal properties and phase morphology analysis of PLLA/PCL blends. Polymer 42, 7831–7840. doi: 10.1016/S0032-3861(01)00269-5
Dias, P., and Chinelatto, M. A. (2019). Effect of poly(ε-caprolactone-b-tetrahydrofuran) triblock copolymer concentration on morphological, thermal and mechanical properties of immiscible PLA/PCL blends. J. Renew. Mater. 7, 129–138. doi: 10.32604/jrm.2019.00037
Fambri, L., and Migliaresi, C. (2010). Crystallization and thermal properties, in Poly(lactic acid): Synthesis, Structures, Properties, Processing, and Applications, eds R. Auras, L. T. Lim, S. E. M. Selke, and H. Tsuji (Hoboken, NJ: John Wiley & Sons), 113–124. doi: 10.1002/9780470649848.ch9
Ferri, J. M., Fenollar, O., Jorda-Vilaplana, A., Garcia-Sanoguera, D., and Balart, R. (2016). Effect of miscibility on mechanical and thermal properties of poly(lactic acid)/polycaprolactone blends. Polym. Int. 65, 453–463. doi: 10.1002/pi.5079
Finotti, P. F. M., Costa, L. C., and Chinelatto, M. A. (2016). Effect of chemical structure of compatibilizers on the thermal, mechanical and morphological properties of immiscible PLA/PCL blends. Macromol. Symp. 368, 24–29. doi: 10.1002/masy.201600056
Forouharshad, M., Gardella, L., Furfaro, D., Galimberti, M., and Monticelli, O. (2015). A low-environmental-impact approach for novel bio-composites on PLLA/PCL blends and high surface area graphite. Eur. Polym. J. 70, 28–36. doi: 10.1016/j.eurpolymj.2015.06.016
Fortelny, I., and Juza, J. (2019). Description of the droplet size evolution in flowing immiscible polymer blends. Polymers 11, 1–31. doi: 10.3390/polym11050761
Fortelny, I., Lapcikova, M., Lednicky, F., Stary, Z., and Krulis, Z. (2008). Nonuniformity of phase structure in immiscible polymer blends. Polym. Eng. Sci. 48, 564–571. doi: 10.1002/pen.20985
Fortelny, I., Ostafinska, A., Michalkova, D., Juza, J., Mikesova, J., and Slouf, M. (2015). Phase structure evolution during mixing and processing of poly(lactic acid)/polycaprolactone (PLA/PCL) blends. Polym. Bull. 72, 2931–2947. doi: 10.1007/s00289-015-1445-x
Gardella, L., Calabrese, M., and Monticelli, O. (2014). PLA maleation: an easy and effective method to modify the properties of PLA/PCL immiscible blends. Colloid Polym. Sci. 292, 2391–2398. doi: 10.1007/s00396-014-3328-3
Garlotta, D. (2002). A literature rewiew of poly(lactic acid). J. Polym. Environ. 9, 63–81 doi: 10.1023/A:1020200822435
Harada, M., Iida, K., Okamoto, K., Hayashi, H., and Hirano, K. (2008). Reactive compatibilization of biodegradable poly(lactic acid)/poly(ε-caprolactone) blends with reactive processing agents. Polym. Eng. Sci. 48, 1359–1368. doi: 10.1002/pen.21088
Horak, Z., Fortelny, I., Kolarik, J., Hlavata, D., and Sikora, A. (2005). Polymer blends, in The Encyclopedia of Polymer Science and Technology, ed. Kroschwitz, J. (New York, NY: John Wiley & Sons), 1–59. doi: 10.1002/0471440264.pst276
Huang, H.-X. (2011). Macro, micro and nanostructured morphologies of multiphase polymer systems, in The Handbook of Multiphase Polymer Systems, eds. Boudenne, A., Ibos, L., Candau, Y., and Thomas, S. (Chichester, UK: John Wiley & Sons), 161–249. doi: 10.1002/9781119972020.ch6
Imre, B., and Pukánszky, B. (2013). Compatibilization in bio-based and biodegradable polymer blends. Europ. Polym. J. 49, 1215–1233. doi: 10.1016/j.eurpolymj.2013.01.019
Kassos, N., Kelly, A. L., Gough, T., and Gill, A. A. (2019). Synergistic toughening and compatibisation effect of poly(butylene succinate) in PLA/poly-caprolactone blends. Mater. Res. Express 6:035313. doi: 10.1088/2053-1591/aaf7c1
Kelnar, I., Fortelny, I., Kapralkova, L., Kratochvil, J., Angelov, B., and Nevoralova, M. (2016). Effect of layered silicates on fibril formation and properties of PCL/PLA microfibrillar composites. J. Appl. Pol. Sci. 133, 1–9. doi: 10.1002/app.43061
Kim, C.-H., Cho, K. Y., Choi, E.-J., and Park, J.-K. (2000). Effect of P(/LA-co-ϵCL) on the compatibility and crystallization behavior of PCL/PLLA blends. J. Appl. Polym. Sci. 77, 226–231. doi: 10.1002/(SICI)1097-4628(20000705)77:1<226::AID-APP29>3.0.CO;2-8
Krishnan, S., Pandey, P., Mohanty, S., and Nayak, S. K. (2016). Toughening of polylactic acid: an overview of research progress. Polym.-Plast. Technol. Eng. 55, 1623–1652. doi: 10.1080/03602559.2015.1098698
Liu, G., Zhang, X., and Wang, D. (2014). Tailoring crystallization: towards high-performance poly(lactic acid). Adv. Mater. 26, 6905–6911. doi: 10.1002/adma.201305413
López-Rodríguez, N., López-Arraiza, A., Meaurio, E., and Sarasua, J. R. (2006). Crystallization, morphology, and mechanical behavior of poly(lactide)/poly(ε-caprolactone) blends. Polym. Eng. Sci. 46, 1299–1308. doi: 10.1002/pen.20609
Lunt, J. (1998). Large-scale production, properties and commercial applications of polylactic acid polymers. Polym. Degrad. Stab. 59,145–152. doi: 10.1016/S0141-3910(97)00148-1
Macosko, C. W., Guegan, P., Khandpur, A. K., Nakayama, A., Marechal, P., and Inoue, T. (1996). Compatibilizers for melt blending: premade block copolymers. Macromolecules 29, 5590–5598. doi: 10.1021/ma9602482
Maglio, G., Malinconico, M., Migliozzi, A., and Groeninckx, G. (2004). Immiscible poly(L-lactide)/poly(ε-caprolactone) blends: influence of the addition of a poly(L-lactide)-b-poly(oxyethylene) block copolymer on thermal behavior and morphology. Macromol. Chem. Phys. 205, 946–950. doi: 10.1002/macp.200300150
Marić, M., and Macosko, C. W. (2002). Block copolymer compatibilizers for polystyrene/poly(dimethylsiloxane) blends. J. Polym. Sci. [B]. 40, 346–357. doi: 10.1002/polb.10098
Mittal, V., Akhtar, T., and Matsko, N. (2015). Mechanical, thermal, rheological and morphological properties of binary and ternary blends of PLA, TPS and PCL. Macromol. Mater. Eng. 300, 423–435. doi: 10.1002/mame.201400332
Monticelli, O., Calabrese, M., Gardella, L., Fina, A., and Gioffredi, E. (2014). Silsesquioxanes: novel compatibilizing agents for tuning the microstructure and properties of PLA/PCL immiscible blends. Eur. Polym. J. 58, 69–78. doi: 10.1016/j.eurpolymj.2014.06.021
Murariu, M., Dechief, A.-L., Ramy-Ratiarison, R., Paint, Y., Raques, J.-M., and Dubois, P. (2015). Recent advances in production of poly(lactic acid) (PLA) nanocomposites: a versatile method to tune crystallization properties of PLA. Nanocomposites 1, 71–82. doi: 10.1179/2055033214Y.0000000008
Na, Y., He, Y., Shuai, X., Kikkawa, Y., Doi, Y., and Inoue, Y. (2002). Compatibilization effect of poly(ε-caprolactone)-b-poly(ethylene glycol) block copolymers and phase morphology analysis in immiscible poly(lactide)/poly(ε-caprolactone) blends. Biomacromolecules 3, 1179–1186. doi: 10.1021/bm020050r
Nakajima, H., Dijkstra, P., and Loos, K. (2017). The recent development in biobased polymers toward general and engineering applications; polymers that are upgraded from biodegradable polymers, analogous to petroleum-derived polymers, and newly developed. Polymers 9:523. doi: 10.3390/polym9100523
Ostafinska, A., Fortelny, I., Hodan, J., Krejcikova, S., Nevoralova, M., Kredatusova, J., et al. (2017). Strong synergistic effects in PLA/PCL blends: impact of PLA matrix viscosity. J. Mech. Behavior Biomed. Mater. 69, 229–241. doi: 10.1016/j.jmbbm.2017.01.015
Ostafinska, A., Fortelny, I., Nevoralova, M., Hodan, J., Kredatusova, J., and Slouf, M. (2015). Synergistic effects in mechanical properties of PLA/PCL blends with optimized composition, processing, and morphology. RSC Adv. 5, 98971–98982. doi: 10.1039/C5RA21178F
Patrício, T., Glória, A., and Bártolo, P. (2013). Mechanical and biological behaviour of PCL and PCL/PLA scaffolds for tissue engineering applications. Chem. Eng. Trans. 32, 1645–1650. doi: 10.3303/CET1332275
Perego, G., Cella, G. D., and Bastioli, C. (1996). Effect of molecular weight and crystallinity on poly(lactic acid) mechanical properties. J. Appl. Pol. Sci. 59, 37–43. doi: 10.1002/(SICI)1097-4628(19960103)59:1<37::AID-APP6>3.0.CO;2-N
Pitt, C. G. (1990). Poly- ε-caprolactone and its copolymers, in The Biodegradable Polymers as Drug Delivery Systems, eds. Langer, R., and Chasin, M. (New York, NY: Marcel Dekker, 71–120.
Quiles-Carrillo, L., Montanes, N., Pineiro, F., Jorda-Vilaplana, A., and Torres-Giner, S. (2018). Ductility and toughness improvement of injection-molded compostable pieces of polylactide by melt blending with poly(ε-caprolactone) and thermoplastic starch. Materials 11:2138. doi: 10.3390/ma11112138
Ray, S. S., Pouliot, S., Bousmina, M., and Utracki, L. A. (2004). Role of organically modified layered silicate as an active interfacial modifier in immiscible polystyrene/polypropylene blends. Polymer 45, 8403–8413. doi: 10.1016/j.polymer.2004.10.009
Sabet, S. S., and Katbab, A. A. (2009). Interfacially compatibilized poly(lactic acid)/polycaprolactone/organoclay nanocomposites with improved biodegradability and barrier properties: effect of the compatibilizer structural parameters and feeding route. J. Appl. Polym. Sci. 111, 1954–1963. doi: 10.1002/app.29210
Semba, T., Kitagawa, K., Ishiaku, U. S., Kotaki, M., and Hamada, H. (2007). Effect of compounding procedure on mechanical properties and dispersed phase morphology of poly(lactic acid)/polycaprolactone) blends containing peroxide. J. Appl. Polym. Sci. 103, 1066–1074. doi: 10.1002/app.25311
Shin, Y. B., and Han, D. H. (2013). Compatibilization of immiscible poly(lactic acid)/poly(e-caprolactone) blend through electron-beam irradiation with the addition of a compatibilizing agent. Radiat. Phys. Chem. 83, 98–104. doi: 10.1016/j.radphyschem.2012.10.001
Simoes, C. L., Viana, J. C., and Cunha, A. M. (2009). Mechanical properties of poly(ε-caprolactone) and poly(lactic acid) blends. J. Appl. Polym. Sci. 112, 345–352. doi: 10.1002/app.29425
Slouf, M., Ostafinska, A., Nevoralova, M., and Fortelny, I. (2015). Morphological analysis of polymer systems with broad particle size distribution. Polym. Test. 42, 8–16. doi: 10.1016/j.polymertesting.2014.12.012
Song, Z., Huang, X., Lu, X., Lv, Q., Xu, N., Pang, S., et al. (2018). Improvement of microstructures and properties of poly(lactic acid)/poly(e-caprolactone) blends compatibilized with polyoxymethylene. J. Appl. Pol. Sci. 135, 1–13. doi: 10.1002/app.46536
Standau, T., Zhao, C., Castellon, S. M., Bonten, C., and Altstadt, V. (2019) Chemical modification foam processing of polylactide (PLA). Polymers. 11, 1–38. doi: 10.3390/polym11020306
Takayama, T., Todo, M., and Tsuji, H. (2011). Effect of annealing on the mechanical properties of PLA/PCL and PLA/PCL/LTI polymer blends. J. Mech. Behav. Biomed. Mater. 4, 255–260. doi: 10.1016/j.jmbbm.2010.10.003
Todo, M., Park, S.-D., Takayama, T., and Arakawa, K. (2007). Fracture micromechanisms of bioabsorbable PLLA/PCL polymer blends. Eng. Frac. Mech. 74, 1872–1883. doi: 10.1016/j.engfracmech.2006.05.021
Tsuji, H., and Ikada, Y. (1996). Blends of aliphatic polyesters. I. Physical properties and morphologies of solution-cast blends from poly(DL-lactide) and poly(ε-caprolactone). J. Appl. Polym. Sci. 60, 2367–2375. doi: 10.1002/(SICI)1097-4628(19960627)60:13<2367::AID-APP8>3.0.CO;2-C
Tsuji, H., Yamada, T., Suzuki, M., and Itsuo, S. (2003). Blends of aliphatic polyesters. Part 7. Effect of poly(L-lactide- co-ε-caprolactone) on morphology, structure, crystallization, and physical properties of blends of poly(L-lactide) and poly(ε-caprolactone). Polym. Int. 52, 269–275. doi: 10.1002/pi.1093
Urquijo, J., Dagreou, S., Guerrica-Echevarria, G., and Eguiazabal, J. I. (2016). Structure and properties of poly(lactic acid)/poly(ε-caprolactone) nanocomposites with kinetically induced nanoclay location. J. Appl. Polym. Sci. 133:43815. doi: 10.1002/app.43815
Urquijo, J., Guerrica-Echavarria, G., and Eguiazabal, J. I. (2015). Melt processed PLA/PCL blends: effect of processing method on phase structure, morphology, and mechanical properties. J. Appl. Polym. Sci. 132:42641. doi: 10.1002/app.42641
Vilay, V., Mariatti, M., Ahmad, Z., Pasomsouk, K., and Todo, M. (2009). Characterization of the mechanical and thermal properties and morphological behavior of biodegradable poly(L-lactide)/poly(epsilon-caprolactone) and poly(L-lactide)/poly(butylene succinate-co-L-lactate) polymeric blends. J. Appl. Polym. Sci. 114, 1784–1792. doi: 10.1002/app.30683
Vilay, V., Mariatti, M., Ahmad, Z., Pasomsouk, K., and Todo, M. (2010). Improvement of microstructures and properties of biodegradable PLLA and PCL blends compatibilized with a triblock copolymer. Mater. Eng. Sci. A 527, 6930–6937. doi: 10.1016/j.msea.2010.07.079
Wachirahuttapong, S., Thongpin, C., and Sambatsompop, N. (2016). Effect of PCL and compatibility contents on the morphology, crystallization and mechanical properties of PLA/PCL blends. Energy Procedia 89, 198–206. doi: 10.1016/j.egypro.2016.05.026
Wu, D., Zhang, Y., Yuan, L., Zhang, M., and Zhou, W. (2010). Viscoelastic interfacial properties of compatibilized poly(epsilon-caprolactone)/polylactide blend. J. Polym. Sci. [B]. 48, 756–765. doi: 10.1002/polb.21952
Xiang, W., Feng, L., Bian, X., Zhang, B., Sun, B., Liu, Y., et al. (2019). Toughening modification of PLLA with PCL in the presence of PCL-b-PLLA diblock copolymers as compatibilizer. Polym. Adv. Technol. 30, 963–972. doi: 10.1002/pat.4530
Yeh, J.-T., Wu, C.-J., Tsou, C.-H., Chai, W.-L., Chow, J.-D., Huang, C.-Y., et al. (2009). Study on the crystallization, miscibility, morphology, properties of poly(lactic acid)/poly(ε-caprolactone) blends. Polym.-Plast. Technol. Eng. 48, 571–578. doi: 10.1080/03602550902824390
Zhang, M., Shi, X., Dia, X., Huo, C., Xie, J., Li, X., et al. (2018). Improving the crystallization and fire resistance of poly(lactic acid) with nano-ZIF-8@GO. J. Mater. Sci. 53, 7083–7093. doi: 10.1007/s10853-018-2049-2
Keywords: biopolymer blends, poly(lactic acid), polycaprolactone, impact strength, crystallinity, particle size distribution
Citation: Fortelny I, Ujcic A, Fambri L and Slouf M (2019) Phase Structure, Compatibility, and Toughness of PLA/PCL Blends: A Review. Front. Mater. 6:206. doi: 10.3389/fmats.2019.00206
Received: 26 June 2019; Accepted: 09 August 2019;
Published: 27 August 2019.
Edited by:
Alfonso Maffezzoli, University of Salento, ItalyReviewed by:
Veronique Michaud, École Polytechnique Fédérale de Lausanne, SwitzerlandCopyright © 2019 Fortelny, Ujcic, Fambri and Slouf. This is an open-access article distributed under the terms of the Creative Commons Attribution License (CC BY). The use, distribution or reproduction in other forums is permitted, provided the original author(s) and the copyright owner(s) are credited and that the original publication in this journal is cited, in accordance with accepted academic practice. No use, distribution or reproduction is permitted which does not comply with these terms.
*Correspondence: Miroslav Slouf, c2xvdWZAaW1jLmNhcy5jeg==
Disclaimer: All claims expressed in this article are solely those of the authors and do not necessarily represent those of their affiliated organizations, or those of the publisher, the editors and the reviewers. Any product that may be evaluated in this article or claim that may be made by its manufacturer is not guaranteed or endorsed by the publisher.
Research integrity at Frontiers
Learn more about the work of our research integrity team to safeguard the quality of each article we publish.