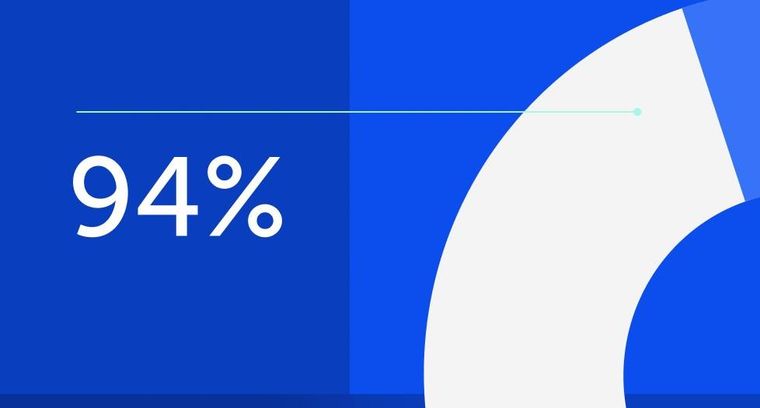
94% of researchers rate our articles as excellent or good
Learn more about the work of our research integrity team to safeguard the quality of each article we publish.
Find out more
ORIGINAL RESEARCH article
Front. Mater., 08 May 2019
Sec. Structural Materials
Volume 6 - 2019 | https://doi.org/10.3389/fmats.2019.00067
This article is part of the Research TopicAdvanced Corrosion Wear Resistant Alloys and their Characterization for High-Temperature ApplicationsView all 9 articles
In this paper, NiCrAlY coating was prepared by atmospheric plasma spraying (APS), and the influence of heat treatment on the mechanical property, tribological property, and oxidation resistance property of coating was researched. The coating was heat-treated at 900 and 1,100°C, respectively. The microstructure of coating became more homogeneous after heat treatment. Meanwhile, heat treatment could effectively increase the microhardness and adhesive strength as well as decrease the porosity of coating. The coating presented the highest adhesive strength of 62.1 MPa and the lowest porosity of 3.06%, as well as excellent tribological property and oxidation resistance property at 900°C after 1,100°C heat treatment.
Over the past few decades, MCrAlY (M = Nickel or/and Cobalt) coatings act as a kind of representative metal-based protective coating that are widely used in several industries such as gas turbines and aircraft engines (Zhao et al., 2004; Vilar et al., 2009; Tahari et al., 2012; Di Leo et al., 2014; Yaghtin et al., 2014; Li et al., 2016, 2017c; Amann et al., 2018). These coatings are often used to prevent the hot parts of rotary and static blades and other components in the high-temperature section of gas turbines. However, the coatings often have poor wear resistance at high temperature. Because the gas turbine engines are exposed in the dusty environment, the stability and lifetime of coatings could deteriorate (Zhao et al., 2004; Li et al., 2017c). Therefore, these coatings should show an excellent mechanical strength, wear resistance, hardness, and oxidation resistance at high temperature (Hou et al., 2015). The plasma-sprayed coatings often present a lamellar structure and contain many defects such as pores and cracks, which would deteriorate the properties of coatings (Li et al., 2017a). In recent years, some researchers investigated the influence of heat treatment on the microstructure and mechanical property of composite coatings, and the results show that heat treatment could make the microstructure of coatings more homogeneous, effectively decrease the defects, and improve the mechanical properties of coatings (Poza and Grant, 2006; Dellacorte and Edmonds, 2009; Peng et al., 2013; Liu et al., 2014; Chraska et al., 2015; Ghadami et al., 2015; Matthews, 2015; Pan et al., 2015; Shao et al., 2015; Wang et al., 2015b; Li et al., 2017b; Kar et al., 2018). Poza and Grant prepared the CoNiCrAlY coating by vacuum plasma spraying (VPS), and heat treatment effectively improved the adhesive strength of the coating (Poza and Grant, 2006). Meanwhile, the MCrAlY coating should show the excellent oxidational resistance properties at high temperature, which could guarantee the stability and lifetime of coatings (Karaoglanli, 2015; Karaoglanli and Turk, 2017). So, it is significant to research the effect of heat treatment on the microstructure, mechanical property, and oxidation resistance property of coatings.
The present work aimed to investigate the effect of heat treatment on the microstructure, mechanical property, tribological property, and oxidation resistance property of the NiCrAlY coating.
The NiCrAlY coating was fabricated by APS (SulZer Metco 9 M, US). The Ni22Cr10Al1.0Y feedstock powder was gained from Metco. The substrate material (Inconel 718) was grit blasted with alumina powders prior to deposition. The size of the alumina powder was about 100 μm. The thickness of the NiCrAlY coating was about 300 μm. The spray parameters are listed in Table 1. The vacuum furnace was used to treat the samples, and the dynamic vacuum was about 10−1 Pa. The samples were heat-treated at 900 and 1,100°C for 1 h, respectively.
The processes of microhardness, adhesive strength, and tribological property tests have been described in detail elsewhere (Li et al., 2016). The microstructures of coatings were characterized by field emission scanning electron microscopy (FE-SEM; Tescan Mira 3) and high-resolution transmission electron microscope (HRTEM; FEI Tecnai G2 F30, USA). The cross-sectional samples were prepared by mechanical polishing. First, the samples were mechanically grounded with 100, 400, 800, 1,000, and 1,500 grit emery paper, respectively, and then polished by cloth. The composition and structure of coatings were examined by an X-ray diffractometer (Philips X'Pert-MRD) utilizing Cu-Ka radiation, and operating voltage was 40 kV. The Jade software was used to analyze the XRD image. The porosity of coatings was measured with an image analyzer. The Chinese national standards (GB/T 13303-91) were used for the oxidation experiment. Before the experiment, all the crucibles were dried in a muffle furnace at 1,050°C and held for 6 h, which could make the weight of the crucibles not change in the experiment. The test temperatures of the oxidation experiment were selected at 900 and 1,000°C in the muffle furnace. The weight of the specimen was measured after every 20 h during oxidation and then removed from the furnace directly into atmosphere and cooled down to room temperature. Each temperature was repeated at least three times for the oxidation experiment test in order to ensure the repeatability of the experimental results and then worked out the average value and obtained the curves.
Figure 1 presents the SEM morphology and XRD patterns of the NiCrAlY powder. It can be clearly seen that the powder is spherical in shape with sizes of 53–106 μm (Figure 1a). The spherical shape powder has an excellent flowability, which is very useful for the feeding rate during the spray process. The XRD analysis indicates that the NiCrAlY powder consists of Ni3Al, NiAl, and Ni-based solid solution phases, which have good crystallinity (Figure 1b).
Figure 2 shows the XRD patterns of the NiCrAlY coating. The coating mainly contains the NiAl (JCPDS file no. 20-0019), Ni (JCPDS file no. 45-1027), and Ni3Al (JCPDS file no. 09-0097) phases. After heat treatment, the Y2O3 (JCPDS file no. 43-1036) and Cr phases (JCPDS file no. 06-0694) appear in the coating. The Y2O3 usually acts as the oxide dispersive strengthening phase, which could effectively improve the microhardness of the coating. After 1,100°C heat treatment, the NiAl phase is substituted by the Ni3Al phase. This result, probably due to the NiAl phase, would be expected in thermodynamic equilibrium conditions (Bolelli et al., 2015) and solidified in the matrix.
Figure 2. XRD patterns of NiCrAlY coating: (a) as-sprayed, (b) heat-treated at 900°C, and (c) heat-treated at 1,100°C.
Figure 3 shows the cross-sectional microstructures of coatings at different heat treatment temperatures. The as-sprayed coating contains many pores and cracks, while they lessened after heat treatment. Heat treatment can obviously reduce the cracks and pores of the coating, which could effectively improve the density, and decrease the porosity of the coating. After 1,100°C heat treatment, the coating has less cracks and pores. The microstructure of the coating becomes smooth after heat treatment, which means heat treatment could significantly influence the microstructure of the coating. It is generally accepted that the mechanical properties of thermal sprayed coatings are highly dependent on the intrinsic property and microstructure. Compared with the microstructure of as-sprayed coating (Figure 4a), the microstructure of the coating becomes more homogeneous, and more precipitated phase offers after 1,100°C heat treatment (Figure 4b). Figures 4c, d, respectively, present the HRTEM image and corresponding SAED pattern of the coating after 1,100°C heat treatment. The lattice distance is 0.207 nm in the HRTEM image (Figure 4c), consisting of the (111) plane of cubic phase Ni3Al (JCPDS file no. 09-0097), which corresponds to the XRD analysis in Figure 2. The diffraction spots in the SAED pattern of coating (Figure 4d) originate from the Ni3Al cubic phase, oriented along its [112] axis.
Figure 3. SEM morphologies of polished cross section of NiCrAlY coating: (a) as-sprayed, (b) 900°C heat treatment, and (c) 1,100°C heat treatment.
Figure 4. TEM morphologies and corresponding SAED patterns of NiCrAlY coating: (a) as-sprayed, (b–d) 1,100°C heat treatment.
The microhardness of the NiCrAlY coating at different heat treatment temperatures is presented in Table 2. The microhardness of the coating increases with the rise of the treating temperature, which is due to the second phase precipitate after heat treatment. After 1,100°C heat treatment, the coating shows the highest hardness of 371.1 HV (Vickers hardness). This is probably due to the microstructure of the coating becoming more homogeneous, and the Y2O3 oxide dispersive strengthening phase is precipitated (Figure 2).
The adhesive strength and porosity of the NiCrAlY coating at different heat treatment temperatures are given in Figure 5. Heat treatment could efficiently improve the adhesive strength of the coating and the highest adhesive strength of 62.1 MPa after 1,100°C heat treatment. The enhanced adhesive strength of the coating after heat treatment is closely related to the homogeneous microstructure and interfacial diffusion of bond coating and substrate. In the process of the tests, the break occurred between the interface of the bond coating and substrate. Figure 6 presents the interface morphologies of the coating and the corresponding element maps. It can obviously be seen that the interface of the as-sprayed coating is very clear and has many pore distribution. So, the coating has lower adhesive strength. After 1,100°C heat treatment, the interface area of the bond coating and substrate becomes broad, and the pores are reduced. The element diffusion between the bond coating and the substrate could be clearly seen in the element maps in Figure 6b. Therefore, the coating shows the highest adhesive strength after 1,100°C heat treatment. The porosity of coating decreases with the increase in treating temperature, and the coating holds the lowest porosity of 3.06% after 1,100°C heat treatment. Heat treatment can make the total sample shrink and reduce the residual porosity (Dellacorte and Edmonds, 2009; Chraska et al., 2015), which could improve the density of the coating. It is very beneficial to adhesive strength enhancement and might contribute to the improvement of the tribological property of the NiCrAlY coating. The porosity estimation of the coating at different heat treatment temperatures is shown in Figure 7. The pores and cracks are larger in the as-sprayed coating than in the others (Figure 3). The pores and cracks of the coating obviously reduce during heat treatment, which is probably due to the element diffusion and the pores and cracks shrink. The coating shows the least pores and cracks and the surface of the coating is the smoothest after 1,100°C heat treatment. So, the coating shows the lowest porosity of 3.06% after 1,100°C heat treatment (Figure 5).
Figure 6. Interface morphologies of NiCrAlY coating and corresponding element maps: (a) as-sprayed, (b) 1,100°C heat treatment.
Figure 7. Porosity estimation of NiCrAlY coating: (a,a′) as-sprayed, (b,b′) 900°C heat treatment, and (c,c′) 1,100°C heat treatment.
Figure 8 presents the friction coefficient of the NiCrAlY coating at different heat treatment temperatures. The friction coefficient of the coating decreases with the increase in temperature. After 1,100°C heat treatment, the coating shows the lowest friction coefficient at all test temperatures. The reason is probably due to the cracks and pores of the coating are reduced and the microstructure of the coating becomes homogeneous after heat treatment (Figure 3).
In order to illustrate the evolution of the friction coefficient of the coating at different temperatures, the friction coefficients corresponding to rotating time curves of the coating after 1,100°C heat treatment at different temperatures are presented in Figure 9. The curves of the friction coefficient reach a steady condition after a short running-in period. In combination with the homogeneous microstructure (Figure 3c) and excellent mechanical property, this could be reasonably ascribed to the steady friction process of coating.
Figure 9. The friction vs. rotating time curves of coating heat-treated at 1,100°C tested at different friction test temperatures.
Figure 10 presents the wear rate of the NiCrAlY coating at different heat treatment temperatures. The variation trend of the wear rate vs. temperature is similar with that of the friction coefficient. The wear rate of all the coatings decreases consecutively with the temperature increase. After 1,100°C heat treatment, the coating also exhibits the lowest wear rate at all test temperatures. At room temperature, the wear rate of the coating sharply decreases through heat treatment. It is closely related to the homogeneous and dense microstructure of the coating after heat treatment.
The worn surface morphologies of the coating at different test temperatures are presented in Figure 11. At 25°C, the worn surface of the as-sprayed NiCrAlY coating is covered with grooves and brittle fracture (Figure 11a), the friction coefficient (Figure 8), and wear rate (Figure 10) of the coating are higher. It is due to the severe abrasive action between the tribological pairs of coating disk and alumina ball, and the wear mechanism is abrasive wear (Wang et al., 2015a). While for the 900 and 1,100°C heat treatment coatings, the worn surfaces have no obvious grooves and delamination and become very smooth (Figures 11d,g). In the as-sprayed coating, the main damage is intergranular fracture, and contact fatigue makes the grains pull out. Obviously, the damage in the rough regions of the as-sprayed coating is more serious than that in the coating through 900 and 1,100°C heat treatments. The worn surface of 1,100°C heat treatment coating is the smoothest at room temperature (Figure 11g). After heat treatment, the microstructure of the coating becomes more homogeneous. So, the coating shows excellent tribological property. At 500°C, the worn surfaces of all the coatings become smoother, and some wear debris could be seen on the worn surface (Figures 11b,e,h). The wear mechanism is mainly microplowing and delamination. At 900°C, the worn surfaces of the coatings are covered with the glaze film and have obvious plastic deformation (Figures 11c,f,i; Liu et al., 2013; Krishna et al., 2015). After 1,100°C heat treatment, the worn surface of the coating is covered with a continuous glaze film. So, the coating has the lowest friction coefficient (Figure 8) and wear rate (Figure 10). With the increase in temperature, the worn surfaces of the coatings become smooth and are covered with the glaze film. So, the friction coefficient and wear rate of the coatings decrease with the friction test temperature increasing. Based on the discussion above, it can be concluded heat treatment can effectively improve the tribological property of coatings at all test temperatures. The coating through 1,100°C heat treatment exhibits superior tribological property at all test temperatures.
Figure 11. SEM morphologies of worn surfaces of NiCrAlY coating (a–c) as-sprayed, (d–f) 900°C, and (g–I) 1,100°C heat treatments at different friction test temperatures.
In order to further investigate the wear mechanism of coating at different friction test temperatures, element maps of worn surfaces are conducted. Figure 12 presents the SEM morphologies of the worn surfaces of the NiCrAlY coating after 1,100°C heat treatment at different friction test temperatures and corresponding element maps. At room temperature, the elements distribute uniformity on the worn surface. The worn surface has no obviously oxide layer and is covered with some grooves. At 500°C, the worn surface of the coating is covered with a discontinuous glaze layer. After 900°C friction test, the worn surface is covered with a continuous oxide layer. The oxide layer mainly contains Y and O elements from element maps, which could effectively improve the tribological property of the coating. So, the coating has the lowest friction coefficient (Figure 8) and wear rate (Figure 10) at 900°C.
Figure 12. SEM morphologies of worn surfaces of NiCrAlY coating after 1,100°C heat treatment at different friction test temperatures and corresponding element maps: (a) room temperature, (b) 500°C, and (c) 900°C.
The coating has a homogeneous and dense microstructure as well as excellent mechanical property after 1,100°C heat treatment. So, the oxidation resistance of coating after 1,100°C heat treatment is investigated. Figure 13 gives the mass gain vs. time curve of the coating for 100 h at 900 and 1,000°C. The curves reach a steady condition after 40 h of oxidation experiment. It is probably due to the surface of coating forming an oxidation layer. The coating shows excellent oxidation resistance at 900°C, and the mass gain is 1.50 mg/cm2 after 100 h of the oxidation experiment. However, the coating presents a higher oxidation rate at 1,000°C. The mass gain of the sample is up to 6.01 mg/cm2 after 100 h of the oxidation experiment, and the oxidation resistance of the coating becomes bad. It is probably due to Ni and Cr occurring oxidation on the coating surface, and the coating has a higher oxidation rate at 1,000°C.
Figure 13. Curves of coating heat treatment at 1,100°C oxidized for 100 h at different test temperatures.
In order to further investigate the microstructure and phase changes of coating at different temperatures oxidized for 100 h, element maps of surfaces are conducted. Figure 14 shows the SEM morphologies of coating surfaces after 1,100°C heat treatment at different temperatures oxidized for 100 h and corresponding element maps. The elements distribute uniformity, and the surface has no big particles after 900°C oxidized for 100 h. The coating shows excellent oxidation resistance. However, the surface is covered with some big particles and becomes more rough at 1,000°C oxidized for 100 h. The coating has severe oxidation. These big particles mainly contain the Y element from element maps. At the same time, the Ni and Cr elements occur oxidation and form NiO and Cr2O3. So, the coating has a higher oxidation rate at 1,000°C.
Figure 14. SEM morphologies of NiCrAlY coating surfaces after 1,100°C heat treatment at (a) 900°C and (b) 1,000°C oxidized for 100 h and corresponding element maps.
In this work, the effect of heat treatment on the microstructure, microhardness, porosity, adhesive strength, tribological property, and oxidation resistance property of the NiCrAlY coating by APS was investigated. The main conclusions can be drawn as follows:
1. Heat treatment could obviously reduce the porosity of coating, which could effectively improve the density, adhesive strength, and microhardness of the NiCrAlY coating.
2. After 1,100°C heat treatment, the microstructure of the coating became more homogeneous, and more Y2O3 oxide dispersive strengthening phase was precipitated; the coating had the highest adhesive strength, microhardness, and excellent tribological property at a wide range of temperature.
3. The coating heat-treated at 1,100°C presented excellent oxidation resistance property at 900°C.
BL wrote this article. SM modified this article. YG provided the ways of this article. CL fabricated the NiCrAlY coating. HG helped BL to analyse the results. QZ polished the NiCrAlY coating. YK burnished the NiCrAlY coating. JJ analyzed the mechanism.
The authors declare that the research was conducted in the absence of any commercial or financial relationships that could be construed as a potential conflict of interest.
This work was supported by the National Natural Science Foundation of China (grant nos. 51805408, 51771143, and 51665026), the Shaanxi Province Postdoctoral Science Foundation, the Fundamental Research Funds for the Central Universities (xzy012019010), and the Guangxi Innovation Driven Development Project (GUIKEAA18242001).
Amann, T., Gatti, F., Oberle, N., Kailer, A., and Rühe, J. (2018). Galvanically induced potentials to enable minimal tribochemical wear of stainless steel lubricated with sodium chloride and ionic liquid aqueous solution. Friction 6, 230–242. doi: 10.1007/s40544-017-0198-y
Bolelli, G., Candeli, A., Lusvarghi, L., Ravaux, A., Cazes, K., Denoirjean, A., et al. (2015). Tribology of NiCrAlY+Al2O3 composite coatings by plasma spraying with hybrid feeding of dry powder+suspension. Wear 344–345, 69–85. doi: 10.1016/j.wear.2015.10.014
Chraska, T., Pala, Z., Mušálek, R., Medrický, J., and Vilémová, M. (2015). Post-treatment of plasma-sprayed amorphous ceramic coatings by spark plasma sintering. J. Therm. Spray Technol. 24, 637–643. doi: 10.1007/s11666-015-0225-3
Dellacorte, C., and Edmonds, B. (2009). NASA PS400: A New High Temperature Solid Lubricant Coating for High Temperature Wear Applications. Washington, DC: National Aeronautics and Space Administration; Glenn Research Center.
Di Leo, C., Luk-Cyr, J., Liu, H., Loeffel, K., Al-Athel, K., and Anand, L. (2014). A new methodology for characterizing traction-separation relations for interfacial delamination of thermal barrier coatings. Acta Mater. 71, 306–318. doi: 10.1016/j.actamat.2014.02.034
Ghadami, F., Sohi, M., and Ghadami, S. (2015). Effect of bond coat and post-heat treatment on the adhesion of air plasma sprayed WC-Co coatings. Surf. Coat. Technol. 261, 289–294. doi: 10.1016/j.surfcoat.2014.11.016
Hou, G., An, Y., Zhao, X., Zhou, H., and Chen, J. (2015). Effect of alumina dispersion on oxidation behavior as well as friction and wear behavior of HVOF-sprayed CoCrAlYTaCSi coating at elevated temperature up to 1000°C. Acta Mater. 95, 164–175. doi: 10.1016/j.actamat.2015.05.025
Kar, S., Bandyopadhyay, P., and Paul, S. (2018). Effect of arc-current and spray distance on elastic modulus and fracture toughness of plasma-sprayed chromium oxide coatings. Friction 6, 387–394. doi: 10.1007/s40544-017-0166-6
Karaoglanli, A. (2015). Effects of plastic deformation on isothermal oxidation behavior of CoNiCrAlY coatings. Sci. Adv. Mater. 7, 173–177. doi: 10.1166/sam.2015.2099
Karaoglanli, A., and Turk, A. (2017). Isothermal oxidation behavior and kinetics of thermal barrier coatings produced by cold gas dynamic spray technique. Surf. Coat. Technol. 318, 72–81. doi: 10.1016/j.surfcoat.2016.12.021
Krishna, L., Gupta, P., and Sundararajan, G. (2015). The influence of phase gradient within the micro arc oxidation (MAO) coatings on mechanical and tribological behaviors. Surf. Coat. Technol. 269, 54–63. doi: 10.1016/j.surfcoat.2015.02.047
Li, B., Gao, Y., Han, M., Guo, H., Jia, J., Wang, W., et al. (2017a). Tribological properties of NiAl matrix composite coatings synthesized by plasma spraying method. J. Mater. Res. 32, 1674–1681. doi: 10.1557/jmr.2017.136
Li, B., Gao, Y., Jia, J., Han, M., Guo, H., and Wang, W. (2016). Influence of heat treatments on the microstructure as well as mechanical and tribological properties of NiCrAlY-Mo-Ag coatings. J. Alloys Compd. 686, 503–510. doi: 10.1016/j.jallcom.2016.06.075
Li, B., Jia, J., Gao, Y., Han, M., and Wang, W. (2017b). Microstructural and tribological characterization of NiAl matrix self-lubricating composite coatings by atmospheric plasma spraying. Tribol. Int. 109, 563–570. doi: 10.1016/j.triboint.2017.01.031
Li, B., Jia, J., Han, M., Gao, Y., Wang, W., and Li, C. (2017c). Microstructure, mechanical and tribological properties of plasma-sprayed NiCrAlY-Mo-Ag coatings from conventional and nanostructured powders. Surf. Coat. Technol. 324, 552–559. doi: 10.1016/j.surfcoat.2017.06.034
Liu, E., Gao, Y., Wang, W., Zhang, X., Wang, X., Yi, G., et al. (2013). Effect of Ag2Mo2O7 incorporation on the tribological characteristics of adaptive Ni-based composite at elevated temperatures. Tribol. Trans. 56, 469–479. doi: 10.1080/10402004.2012.763004
Liu, Y., Jeng, M., Hwang, J., and Chang, C. (2014). A study on wear resistance of HVOF-sprayed Ni-MoS2 self-lubricating composite coatings. J. Therm. Spray Technol. 24, 489–495. doi: 10.1007/s11666-014-0208-9
Matthews, S. (2015). Carbide Dissolution/carbon loss as a function of spray distance in unshrouded/shrouded plasma sprayed Cr3C2-NiCr coatings. J. Therm. Spray Technol. 24, 552–569. doi: 10.1007/s11666-014-0210-2
Pan, J., Cheng, Y., and Yang, J. (2015). Effect of heat treatment on the lubricating properties of lithium lubricating grease. RSC Adv. 5, 58686–58693. doi: 10.1039/C5RA08917D
Peng, X., Xia, C., Dai, X., Wu, A., Dong, L., Li, D., et al. (2013). Study on the interface reaction behavior of NiCrAlY coating on titanium alloy. Surf. Coat. Technol. 232, 254–263. doi: 10.1016/j.surfcoat.2013.05.024
Poza, P., and Grant, P. (2006). Microstructure evolution of vacuum plasma sprayed CoNiCrAlY coatings after heat treatment and isothermal oxidation. Surf. Coat. Technol. 201, 2887–2896. doi: 10.1016/j.surfcoat.2006.06.001
Shao, F., Yang, K., Zhao, H., Liu, C., Wang, L., and Tao, S. (2015). Effects of inorganic sealant and brief heat treatments on corrosion behavior of plasma sprayed Cr2O3-Al2O3 composite ceramic coatings. Surf. Coat. Technol. 276, 8–15. doi: 10.1016/j.surfcoat.2015.06.045
Tahari, M., Shamanian, M., and Salehi, M. (2012). Microstructural and morphological evaluation of MCrAlY/YSZ composite produced by mechanical alloying method. J. Alloys Compd. 525, 44–52. doi: 10.1016/j.jallcom.2012.01.161
Vilar, R., Santos, E., Ferreira, P., Franco, N., and da Silva, R. (2009). Structure of NiCrAlY coatings deposited on single-crystal alloy turbine blade material by laser cladding. Acta Mater. 57, 5292–5302. doi: 10.1016/j.actamat.2009.06.049
Wang, J., Shan, Y., Guo, H., Li, B., Wang, W., and Jia, J. (2015a). Friction and wear characteristics of hot-pressed NiCr-Mo/MoO3/Ag self-lubrication composites at elevated temperatures up to 900°C. Tribol. Lett. 59:48. doi: 10.1007/s11249-015-0574-6
Wang, J., Shinozaki, N., Zeng, Z., Sakoda, N., and Fukami, N. (2015b). Penetration treatment of plasma spray SUS316L stainless steel coatings by molten MnO-SiO2 oxides. Appl. Surf. Sci. 325, 132–138. doi: 10.1016/j.apsusc.2014.10.179
Yaghtin, A., Javadpour, S., and Shariat, M. (2014). Hot corrosion of nanostructured CoNiCrAlYSi coatings deposited by high velocity oxy fuel process. J. Alloys Compd. 584, 303–307. doi: 10.1016/j.jallcom.2013.09.047
Keywords: microstructure, heat treatment, mechanical property, tribological property, oxidation resistance property
Citation: Li B, Ma S, Gao Y, Li C, Guo H, Zheng Q, Kang Y and Jia J (2019) Mechanical, Tribological, and Oxidation Resistance Properties of NiCrAlY Coating by Atmospheric Plasma Spraying. Front. Mater. 6:67. doi: 10.3389/fmats.2019.00067
Received: 30 January 2019; Accepted: 01 April 2019;
Published: 08 May 2019.
Edited by:
Hanguang Fu, Beijing University of Technology, ChinaReviewed by:
Yulong An, Lanzhou Institute of Chemical Physics (CAS), ChinaCopyright © 2019 Li, Ma, Gao, Li, Guo, Zheng, Kang and Jia. This is an open-access article distributed under the terms of the Creative Commons Attribution License (CC BY). The use, distribution or reproduction in other forums is permitted, provided the original author(s) and the copyright owner(s) are credited and that the original publication in this journal is cited, in accordance with accepted academic practice. No use, distribution or reproduction is permitted which does not comply with these terms.
*Correspondence: Bo Li, bGlibzYxNkBtYWlsLnhqdHUuZWR1LmNu
Shengqiang Ma, c2hlbmdxaWFuZzAxMkAxNjMuY29t
Disclaimer: All claims expressed in this article are solely those of the authors and do not necessarily represent those of their affiliated organizations, or those of the publisher, the editors and the reviewers. Any product that may be evaluated in this article or claim that may be made by its manufacturer is not guaranteed or endorsed by the publisher.
Research integrity at Frontiers
Learn more about the work of our research integrity team to safeguard the quality of each article we publish.