- 1Dipartimento di Ingegneria Civile e Ambientale, Università di Perugia, UdR INSTM, Terni, Italy
- 2Departamento de Nanomateriales Poliméricos y Biomateriales, Instituto de Ciencia y Tecnología de Polímeros, ICTP-CSIC, Madrid, Spain
Elastomers are traditionally used in industrial components due to their low cost, flexibility, good processability and light weight solutions as metal parts replacement. Nowadays, some critical aspects remain unsolved mainly if their application in extreme environments is demanded; for example the development of high performance elastomeric materials working in high pressure and temperature environments like those of oil and gas extraction environment is still challenging; moreover, in extreme locations where also the extreme conditions such icing problems become hazardous, the extraction activities are limited as well as in transportation where bearing seals mounted on aircraft components are subjected to icing problems a solution is required. All these applications will require the exploitation of new and novel polymers and new and novel reinforcement systems. Carbon nanotubes (CNTs) are being evaluated and are in some use today, but graphene nanoplatelets (GNPs) and its many derivatives offer an opportunity to develop novel high performance materials crucial to nowadays and future industrial applications. In a growing fields of applications such elastomeric nanocomposites target the permeability reduction to prevent blistering, the reduction of the stress cracking, and the capability to retain tensile strength at high temperature and pressure. This perspective will address this need by indicating new multifunctional elastomeric nanocomposites (elastomer plus carbon nanotubes and graphite nanoplatelets) combined with superior barrier and mechanical properties.
Introduction
Elastomeric applications are subjected to fatigue cracks, blistering, and swelling. Such mechanical and chemical damages limit their original functions and can be a serious issue in terms of safety hazards when the elastomers are used as seals and hoses. The occurrence of the first cracks makes the material susceptible to further damage. For this reason, the first issue that a materials scientist has to take in consideration when designing and realizing elastomers, are the hostile conditions to which they are exposed when operating in extreme environments and the subsequent innovations that have been developed for their use. High performance elastomers in rubber based fuel line and sealing components that operate in hostile environments in contact with oil and gas are required (Baird et al., 1998; Campion, 2003; Vega-Cantú et al., 2003; Mody et al., 2013); the resistance to both high pressure and temperature is a serious technological challenge in such field, since it is difficult to improve significantly both properties (Baudet et al., 2011) (Figure 1). In oil field applications, elastomers are subjected to dramatic swelling and rapid gas decompression that hinder their stability for long periods of time.
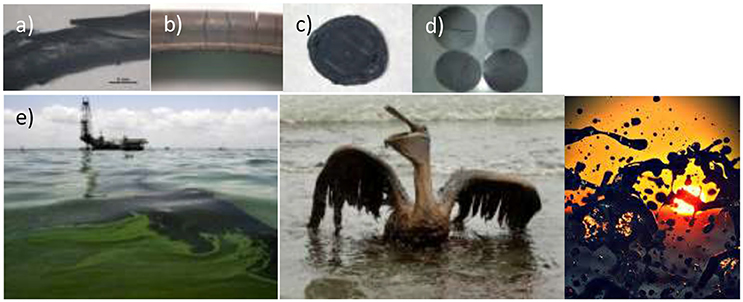
Figure 1. Effects of operating severe conditions on traditional O-rings: (a) rupturing due to low mechanical strength to withstand the pressures and strains, (b) breaking due to low thermal stability, (c) resistance to excessive swelling behavior, (d) resistance to explosive decompression (courtesy of John Kerwin Precision Polymer Engineering Ltd). (e) Effects on the environment of O-ring breaking.
Developing advanced rubber nanocomposites using multifunctional fillers is one of the main challenge nowadays. The replacement of conventional fillers (e.g., carbon black) with carbon nanotubes (CNTs) and graphene nanoplatelets (GNPs) could be a viable solution for the development of graphite-based elastomer composites with improved mechanical and oil/gas barrier properties.
Materials Point of View
Elastomers are high elastic materials that can be largely deformed before returning to their original shape. This makes rubbers a valuable solution for sealing applications where their compression set behavior is the main advantage with respect to the metal based counterparts. The hidden strength of such polymers relies on their cross-linked structure that rescale the ultimate strain as ≈ N∧1/2 with N the number of bonds. Thus, elastomers are susceptible to gas permeation in the high pressure environment. Moreover, the thermal aging can reduce the number of crosslink inducing a degradation of the mechanical properties. Butadiene–acrylonitrile rubber (NBR) (Wrana et al., 2001) reinforced with carbon black is a low cost solution for automotive rubber products due to the possibility to be processed with traditional melt mixing and compression molding techniques retaining a good resistance to lubricants and greases. Moreover, the physical and chemical resistance can be tuned by changing the acrylonitrile content (ACN) between 18 and 50%. The appropriate acrylonitrile content makes the NBR matrix able to be used in fuel and oil handling hose, seals, and water handling applications. Low ACN content ensures higher elongations at break, but reduces the resistance to oils and fuels. Nevertheless, it has found that wide application of such materials as intake manifold etc… suffers of several limitations due to the limited physical properties of NBR elastomers such as very aggressive corrosion against bio-fuels. NBR is generally not resistant to aromatic and chlorinated hydrocarbons, fuels with a high aromatic content, polar solvents, glycol-based brake fluids, and non-flammable hydraulic fluids. NBR has also low resistance to ozone and aging. Fluorocarbon rubber (FKM) (Kader et al., 2006; Rooj et al., 2011) (typically containing 65% fluorine) and more recently perfluoroelastomers (FFKM) (typically containing 71% fluorine) provide materials with excellent high temperature and chemical resistance. FKM is a polymer widely used in aerospace, automotive, chemical, and petroleum industries. FKM materials are resistant to high temperatures and show a reduced swelling when treated with chemical agents. Moreover, they have an excellent resistance to aging and ozone and a low gas permeability. On the contrary, FKM materials suffer the exposition to, steam, polar solvents and glycol-based brake fluids. Since the ability to preserve mechanical strength at high temperatures and pressure is mandatory, it is inevitable the need for the development of new solutions for such materials.
Addressing the Challenges
The nano- and micro- scale dimensions of CNTs and GNPs affect the polymer composite properties due to dimensions that are comparable to those of the polymer matrix chains; these nano-scale interactions is the main advantage with respect to the conventional 3D fillers. The shape factor of graphitic inclusions ensure a larger contact area resulting in a higher mechanical strength. When an optimal concentration for single inclusion phase and the synergy between different, assumed immiscible, phases is reached, the strength of polymer composites is increased (Sengupta et al., 2011). Taking into account that very low concentration is needed to reach the percolation threshold (theoretically ca. 0.01 %) and the good thermal conductivity of graphene, GNPs and CNTs, increase of the thermal conductivity of the composite compared to the pure matrix, is an obvious advantage against degradation due to thermal loading. 1D fillers (CNTs) as well as 2D fillers are very effective in improving the barrier properties of a rubber nanocomposite, by increasing the crosslink density and reducing the swelling caused by the molecular diffusion through the matrix. Permeability of graphitic-based elastomer composites can be further decreased by the preferential orientation of the high aspect ratio inclusions, also resulting to enhanced oxidation resistance and low gas permeability.
GNPs and CNTs single inclusions and their synergy (assumed immiscible), causes a sensible increase of tensile strength and fracture strength when a retardation of agglomeration is considered according to a basic model predicted (Prasad et al., 2009) by the following relation:
where Mh is the measured value for the composite and p and q represent the enhancement in tensile strength of NBR due to the single reinforcement addition. The reinforcing effect of both nanoparticles (Valentini et al., 2018) was recently reported in terms of both elongation at break and tensile strength for nanocomposites containing 5 phr of GNPs and CNTs, respectively. It was also found that the classical rule of mixture does not apply, showing that the in our composite strength the two fillers do not act in synergy. This is due to the fact that an agglomeration of the phase takes place and thus the composite mechanical resistance does not depend linearly on the volume fraction of the phase itself. As proof of this concept it was observed that at a given point a decrease of the total resistance was observed.
Recently, the synergistic properties of NBR/CNTs/GNPs and ethylene-propylene-diene terpolymer rubber/carbon black/GNPs nanocomposites have been explored (Valentini et al., 2016, 2017, 2018). It was found that the combined effect of CNTs/GNPs hybrid filler, exhibited astonishing improvements in terms of mechanical properties, barrier properties, and thermal conductivity. In this regard, extreme-performance rubber nanocomposites, reinforced with CNTs and carbon black fillers, exhibiting a “cellulation” structure (i.e., three-dimensional interconnections of the bound rubber along the carbon tubes) have been developed (Endo et al., 2008). Seals based on these nanotube-based rubber composites were able to resist temperatures up to 260°C and pressures as high as 239 MPa (Endo et al., 2008). Very recently, it was reported how the assembly of graphene hybrid structures provided high electrical and tribological performances. Instead of making a polymer composite in which the fillers are dispersed in the host polymer (Wan et al., 2017), sequentially bridged graphene layers lead to ssignificant improvement in electrical conductivity and lowered friction. Such, hybrid filler formulation and properties might provide the solution of the problems facing by several industries for developing rubber composites.
Counterintuitive Solutions
In rubber industry most of the efforts done are focused on testing and increasing the oil resistance of rubber compounds. Recently the industry is looking for swollen elastomers that in the past render the rubber unusable for practical applications. Whereas for such elastomers the mechanical strength is not great, recently it was found that composites reinforced with graphene, carbon nanotubes, and a mix of them after immersion in several fluids, experienced both a swelling and a reduction of the cross-link density that reduces ice adhesion (Figure 2). In general, the adhesion of ice on stiff substrate without interfacial defects are hard be separated. However, if one of the solids is deformable, then they can be separated imposing a differential deformation. Kim et al. (Chaudhury and Kim, 2007) found that the easy release from a polymeric film was attributed to the critical shear stress of fracture that rescales with the shear modulus of an elastomeric surface. Thus, once ice adheres to a low cross-link elastomer, the ice detaches from the ice-elastomer interface at low shear stresses (Golovin et al., 2016). For elastomers, it is known that the modulus is related to the cross-link density that can be calculated by the well-known Flory formula (Flory, 1953); durable anti-icing material via swelling cross-linked poly(dimethylsiloxane) was reported (Wang et al., 2015) while Golovin et al. (Golovin and Tuteja, 2017) recently predicted the icephobicity of different types of polymers by filling a polymer with oil. They optimized the polymer/plasticizer (i.e., oil) combinations to obtain low ice adhesion and good mechanical durability. Scaling laws from fracture mechanics, revealed a clear synergy between swelling and nanocarbon phase in the icephobic nature of the composite, dictated by a competition between elastic modulus and adsorption energy. These findings could find an upscale in component validation readily applied to different areas where de-icing demands handling of large amount of environmental harmful agents. Another counterintuitive application of elastomers relies in their expansion capability. Rubber-like materials are those that once compressed along an axis expand in directions orthogonal to the applied load (e.g., positive Poisson's ratio) being the Poisson's ratio values for the majority of them about 0.5. Designed mechanical instabilities on soft materials have been used to realize materials with a negative Poisson's ratio (i.e., the so called auxetic behavior) that will contract (expand) in the transverse direction when compressed (stretched) (Bertoldi et al., 2010; Valentini et al. 2017). Such materials may find in perspective practical applications; for example, once infiltrated in a cavity with a smaller dimension auxetic materials can be used as swell tools that expand by means of tensile stress to conform to the wellbore and to remain anchored to it (Mody et al., 2013). For such applications it is required to maintain an expansion above 300% at high temperature (≈150°C). Moreover, from a practical perspective, rubber-based materials with such reversible auxetic architectures can find applications in broad fields from energy absorbing materials to tunable membrane filters.

Figure 2. (a) Measurements of adhesive strength of a glass prism frozen on swollen elastomer. The inset shows the glass prism frozen on elastomer. (b) Mechanical properties and predictive model of ice adhesion as a function of different adsorbed liquid where ΦLIQUID = volume fraction of absorbed liquid, S = swelling, τICE LIQUID = strength adhesion of ice on swollen rubber and τICE NO LIQUID = strength adhesion of ice on un-swollen rubber.
Conclusion and Perspectives
Common challenges for developing materials in extreme environment promote the opportunities to discover crossover solutions; for example, sealing materials being developed in the energy sector for ultra-high-temperature applications are generating interest in aerospace. These new technologies will have an impact on several areas by:
- Increasing the competitiveness of European industry through the use of CNTs and GNPs for a new generation of customized elastomeric nanocomposites to be used in extreme environments, thus paving the way to deeper knowledge and hands-on expertise in cost-effective mass-scale nanostructured carbon production. Hence, helping European Industry to become leader in graphitic materials technologies supporting worldwide customers with specialized, value-added, groundbreaking solutions for their advanced applications in several sectors (oil and gas, automotive, aeronautics).
- Developing new tools for the design of high-performing elastomeric nanocomposites, which will allow to increase efficiency of production processes.
- Enabling a more widespread use of a high % of ethanol in petrol through the validation of a new generation of ethanol resistant vehicle components (Londo et al., 2010). The widespread diffusion of high percentage (>10%) ethanol blended gasoline is connected to their capability to lower CO2 emissions, on the other hand, a market barrier is the risk to damage plastic and rubber components in cars and handheld products. Low permeation rate and a reduced interaction with the solvent (lower swelling) leads to the competitiveness of such polymers with new biofuels.
- Opening the market to new products i.e. advanced sealings, corrosion resistant hoses made of GNP/CNT-containing premixes, will reduce number of failures in mineral processing operations. Thus the development of new composites based on the use of GICs will support and strengthen the oil and gas extraction industry as it faces increasing technical challenges to sustain the growing worldwide demand for energy. Thus the development of reliable, high-performing elastomeric materials will continue to have a crucial role for industrial players.
Author Contributions
All authors listed have made a substantial, direct and intellectual contribution to the work, and approved it for publication.
Funding
MAL-M thanks support from the MINECO project MAT2016-81138-R. LV is supported by the Italian Ministry of Education, University and Research (MIUR) under the Departments of Excellence grant L.232/2016.
Conflict of Interest Statement
The authors declare that the research was conducted in the absence of any commercial or financial relationships that could be construed as a potential conflict of interest.
References
Baird, T., Fields, T., Drummond, R., Mathison, D., Langseth, B., Martin, A., et al. (1998). High-pressure, high-temperature well logging, perforating and testing. Oilfield Rev. 10, 50–67.
Baudet, C., Grandidier, J. C., and Cangémi, L. (2011). A damage model for the blistering of polyvinylidene fluoride subjected to carbon dioxide decompression. J. Mech. Phys. Sol. 59, 1909–1926. doi: 10.1016/j.jmps.2011.04.010
Bertoldi, K., Reis, P. M., Willshaw, S., and Mullin, T. (2010). Negative poisson's ratio behavior induced by an elastic instability. Adv. Mater. 22, 361–366. doi: 10.1002/adma.200901956
Campion, R. P. (2003). Durability review of elastomers for severe fluid duties. Rubber Chem. Technol. 76, 719–746. doi: 10.5254/1.3547764
Chaudhury, M. K., and Kim, K. H. (2007). Shear-induced adhesive failure of a rigid slab in contact with a thin confined film. Eur. Phys. J. 23, 175–183. doi: 10.1140/epje/i2007-10171-x
Endo, M., Noguchi, T., Ito, M., Takeuchi, K., Hayashi, T., Kim, Y. A., et al. (2008). Extreme-performance rubber nanocomposites for probing and excavating deep oil resources using multi-walled carbon nanotubes. Adv. Funct. Mater. 18, 3403–3409. doi: 10.1002/adfm.200801136
Golovin, K., Kobaku, S. P., Lee, D. H., Di Loreto, E. T., Mabry, J. M., and Tuteja, A. (2016). Designing durable icephobic surfaces. Sci. Adv. 2, 1501496–1501512. doi: 10.1126/sciadv.1501496
Golovin, K., and Tuteja, A. (2017). A predictive framework for the design and fabrication of icephobic polymers. Sci. Adv. 3, 1701617–1701619. doi: 10.1126/sciadv.1701617
Kader, M. A., Lyu, M. Y., and Nah, C. (2006). A study on melt processing and thermal properties of fluoroelastomer nanocomposites. Compos. Sci. Technol. 66, 1431–1443. doi: 10.1016/j.compscitech.2005.09.001
Londo, M., Lensink, S., Wakker, A., Fischer, G., Prieler, S., van Velthuizen, H., et al. (2010). The REFUEL EU road map for biofuels in transport: application of the project's tools to some short-term policy issues. Biomass Bioenergy 34, 244–250. doi: 10.1016/j.biombioe.2009.07.005
Mody, R., Gerrard, D., and Goodson, J. (2013). Elastomers in the oil field. Rubber Chem. Technol. 86, 449–469. doi: 10.5254/rct.13.86999
Prasad, K. E., Das, B., Maitra, U., Ramamurty, U., and Rao, C. N. R. (2009). Extraordinary synergy in the mechanical properties of polymer matrix composites reinforced with 2 nanocarbons. Proc. Natl. Acad. Sci. U.S.A. 1060, 13186–13189. doi: 10.1073/pnas.0905844106
Rooj, S., Das, A., and Heinrich, G. (2011). Tube-like natural halloysite/?uoroelastomer nanocomposites with simultaneous enhanced mechanical, dynamic mechanical and thermal properties. Eur. Polym. J. 47, 1746–1755. doi: 10.1016/j.eurpolymj.2011.06.007
Sengupta, R., Bhattacharya, M., Bandyopadhyay, S., and Bhowmick, A. K. (2011). A review on the mechanical and electrical properties of graphite and modified graphite reinforced polymer composites. Prog. Polym. Sci. 36, 638–670. doi: 10.1016/j.progpolymsci.2010.11.003
Valentini, L., Bittolo Bon, S., Hernández, M., Lopez-Manchado, M. A., and Pugno, N. M. (2018). Nitrile butadiene rubber composites reinforced with reduced graphene oxide and carbon nanotubes show superior mechanical, electrical and icephobic properties. Comp. Sci. and Technol. doi: 10.1016/j.compscitech.2018.01.050. [Epub ahead of print].
Valentini, L., Bittolo Bon, S., Lopez-Manchado, M. A., Verdejo, R., Pappalardo, L., Bolognini, A., et al. (2016). Synergistic effect of graphene nanoplatelets and carbon black in multifunctional EPDM nanocomposites. Comp. Sci. Technol. 128, 123–130. doi: 10.1016/j.compscitech.2016.03.024
Valentini, L., Bittolo Bon, S., and Pugno, N. M. (2017). Graphene and carbon nanotube auxetic rubber bionic composites with negative variation of the electrical resistance and comparison with their nonbionic counterparts. Adv. Funct. Mater. 27:1606526. doi: 10.1002/adfm.201606526
Vega-Cantú, Y., Hauge, R., Norman, L., and Billups, W. E. (2003). Enhancement of the chemical resistance of nitrile rubber by direct fluorination. J. Appl. Pol. Sci. 89, 971–979. doi: 10.1002/app.12212
Wan, S., Li, Y., Mu, J., Aliev, A. E., Fang, S., Kotov, N. A., et al. (2017). Sequentially bridged graphene sheets with high strength, toughness, and electrical conductivity. Proc. Natl. Acad. Sci. U.S.A. 115, 5359–5364. doi: 10.1073/pnas.1719111115
Wang, Y., Yao, X., Chen, J., He, Z., Liu, J., Li, Q., et al. (2015). Organogel as durable anti-icing coatings. Sci. China Mater. 58, 559–565. doi: 10.1007/s40843-015-0069-7
Keywords: elastomer, graphitic nanomaterials, carbon nanotubes, graphene, fluid susceptibility, anti-icing properties, mechanical properties
Citation: Valentini L and Lopez-Manchado MA (2018) Rubber Nanocomposites for Extreme Environments: Critics and Counterintuitive Solutions. Front. Mater. 5:49. doi: 10.3389/fmats.2018.00049
Received: 04 June 2018; Accepted: 31 July 2018;
Published: 21 August 2018.
Edited by:
Kyriaki Kalaitzidou, George W. Woodruff School of Mechanical Engineering and Georgia Institute of Technology, United StatesReviewed by:
Scheyla Kuester, École de Technologie Supérieure, CanadaKenan Song, Massachusetts Institute of Technology, United States
Copyright © 2018 Valentini and Lopez-Manchado. This is an open-access article distributed under the terms of the Creative Commons Attribution License (CC BY). The use, distribution or reproduction in other forums is permitted, provided the original author(s) and the copyright owner(s) are credited and that the original publication in this journal is cited, in accordance with accepted academic practice. No use, distribution or reproduction is permitted which does not comply with these terms.
*Correspondence: Luca Valentini, bHVjYS52YWxlbnRpbmlAdW5pcGcuaXQ=