- Instituto de Tecnología Química, Universitat Politècnica de València, Consejo Superior de Investigaciones Científicas, Valencia, Spain
Increased availability of methane from shale gas and stranded gas deposits in the recent years may facilitate the production of ethylene by means of potentially more competitive routes than the state-of-the-art steam cracking processes. One appealing route is the oxidative coupling of methane (OCM), which is considered in this work for the production of ethylene by means of the use of catalytic membrane reactors (CMR) based on Ba0.5Sr0.5Co0.8Fe0.2O3−δ (BSCF) ceramic material. In a first approach, a screening of 15 formulations as catalysts for the ethylene-ethane production was conducted on CMR consisting of disk-shaped planar BSCF membranes. At 900°C, the maximum C2 selectivity was 70%, reached with Ba0.5Sr0.5FeO3−δ and La0.5Ce0.1Sr0.4Co0.8Fe0.2O3−δ catalysts. On the other hand, low CH4 conversions (XCH4) resulted in C2 yields below 3%. Operation at 1,000°C significantly shifted XCH4 for all the activated membranes due to the decrease in CH4/O2 ratios, thus obtaining C2 yields close to 9% and productivities of ca. 1.2 ml·min−1·cm−2 with Ce0.9Gd0.1O2−δ and Ba0.5Sr0.5Co0.8Fe0.2O3−δ impregnated with Mn-Na2WO4 catalysts. The performance of OCM reaction was also studied in a tubular catalytic membrane reactor. Tubular configuration improved C2 yield by minimizing CH4/O2 ratios up to 1.7, obtaining a maximum of 15.6% at 900°C with a BSCF capillary membrane activated with a packed bed of 2 wt% Mn/5 wt% Na2WO4 on SiO2 catalyst.
Introduction
Ethylene is the most demanded organic compound worldwide, with a yearly production of 150 Mton in 2016 (Reporters, 2016). It is probably the most important basic petrochemical since it is used for producing other essential chemicals in nowadays economy, such as polyethylene, ethylene oxide, acetaldehyde or alcohols. Currently, ethylene is mainly produced by steam cracking of hydrocarbon feedstocks (naphta, gasoil, and condensates). Amongst all the existing feedstocks, ethane cracking is the most preferred, since almost no coproducts are obtained. Steam cracking is a non-catalytic process run at very high temperatures (typically 850°C). The main drawbacks are the process complexity and the downstream processing, the high energy requirements due to the endothermic reaction, and the operation complications due to the high coke formation rate. Despite the high maturity of the technology no major advances are foreseen for overcoming these weaknesses.
In the past recent years, ethylene production is focused on the use of light alkanes such as propane, ethane, and methane, mainly due to the more economic availability from shale gas and stranded gas exploitations that facilitate cost-competitive routes for the production of light olefins. Therefore, by considering these available feedstocks, several routes are being studied and developed for the production of ethylene from ethane such as the oxidative de-hydrogenation of ethane (ODHE) (Bhasin et al., 2001; Grubert et al., 2003), and from methane such as methanol-to-olefins reaction (Keil, 1999; Chen et al., 2005), Fischer-Tropsch synthesis (Lunsford, 2000), and the Oxidative Coupling of Methane (OCM) (Keller and Bhasin, 1982; Ito and Lunsford, 1985; Amenomiya et al., 1990; Lunsford, 1995). Amongst these, the use of CH4 for the production of valuable chemicals is preferred due to economic reasons (Mleczko and Baerns, 1995; Mleczko et al., 1996), and in particular OCM is considered one of the most attractive options as a direct route for the direct conversion of CH4 into C2H4.
The first works on OCM were reported in the early 80′s by Keller and Bhasin (1982). Since then, OCM has attracted much attention from both the academia and industry. A big number of developments were mainly focused on catalysts that maximize C2H4 yields and optimizing the reactor design for managing heat and streams (Otsuka et al., 1986; Hutchings et al., 1989; Amenomiya et al., 1990; Maitra, 1993; Mleczko et al., 1996). With regard to OCM reaction mechanism, Stansch et al. (1997) presented a kinetic model (Figure 1) where C2H4 formation mechanism involves a dehydrogenation step to form the radical species, first producing C2H6 by coupling (step 2) and then C2H4 by ethane dehydrogenation (steps 5 and 7). Since CH4 is a very stable molecule, the CH4 activation for the coupling requires breaking a strong C-H bond (ca. 439 kJ·mol−1). Issues such as thermodynamic limitations for CH4 conversion, low C2 selectivity and catalysts deactivation due to coke formation, make OCM practically and commercially inviable (Karakaya et al., 2017). The techno-economical threshold for considering OCM as commercially available is set at 30% C2 yield per single-pass (Farrell et al., 2016; Spallina et al., 2017).
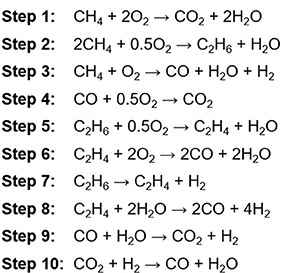
Figure 1. Simplified OCM reaction mechanism presented by Stansch et al. (1997).
Catalytic Membrane Reactor (CMR) technology (Aseem and Harold, 2018) with the integration of Oxygen Transport Membranes (OTMs) (Tenelshof et al., 1995; Zeng et al., 1998; Akin and Lin, 2002; Sunarso et al., 2008) is a suitable option for overcoming these drawbacks. As can be seen in the model depicted in Figure 1, the OCM reaction performance is affected by several secondary reactions leading to undesirable COx formation, mainly due to an O2 feeding excess. Therefore, one of the main aspects of OTMs for their application in OCM reaction is the dosing of O2 in a controlled manner by tuning parameters such as temperature, pO2 at feed side, residence time and space velocity by reactant gas stream flow variation, etc. Therefore, by adjusting conveniently the CH4/O2 stoichiometry the complete oxidation of CH4 to COx can be avoided, while increasing C2 selectivity. In addition, higher conversion can be reached without safety problems related to flammability limits in conventional co-feeding reactors.
Several research groups have performed OCM reactions by considering different OTM materials, geometries and catalysts for improving the reaction toward C2 formation. In Table 1, some of the reported results are summarized. Tubular geometries are preferred for conducting OCM in CMRs, with a special emphasis in the use of catalysts that improve C2 selectivity. Amongst all the considered cases, the best results have been obtained by Othman et al. reaching a C2 yield of 39% on a LSCF hollow fiber activated with Bi1.5Y0.3Sm0.2O3−δ catalyst.
Oxygen transport membranes consist of gastight Mixed Ionic Electronic Conductors (MIEC) that diffuse oxygen through vacancies in the crystal lattice, and simultaneously transport electrons in the opposite direction, thus obviating the need for an external electrical short circuit. Their major advantage is an infinite oxygen selectivity, assuming no leakage through the membrane layer or the sealing, and resulting in high purity oxygen that can be directly provided to oxyfuel power plants or chemical processes. Oxygen permeation through the bulk material is governed by the Wagner equation1, favored by increasing temperatures and chemical gradients across the membrane. On the other hand, thin membranes (below 50 μm) are strongly limited by the surface exchange kinetics of molecular oxygen.
In addition to the benefits of OTMs application in the conduction of OCM reaction, the possibility of adding catalytic layers consisting of MIEC active materials may produce an increase in the rate of surface reactions (Lobera et al., 2012b). The use of catalysts based on perovskites and fluorite compounds is of great interest due to their ionic-electronic conductive properties allowing the presence of ionic oxygen species at the materials surface. Therefore, the OCM reaction can take place all over the catalytic layer at the active sites localized on the oxygen vacancies on the surface of catalyst particles. Nano-structured materials leading to highly porous catalytic layers may improve the OCM performance by ensuring a proper gas diffusion media as well as a high specific surface area. Additionally, by properly doping with metal cations presenting different ionic radii, oxidation states and redox behavior, it is possible to improve the catalytic activity by increasing the number of oxygen vacancies and by varying the O-cation bond strength (Sunarso et al., 2008).
The present work is focused on the development of catalytic membrane reactors (CMR) for the production of C2H4 through the OCM reaction. For that aim, a screening of 15 catalyst formulations was performed on Ba0.5Sr0.5Co0.8Fe0.2O3−δ (BSCF) planar membranes, following the CH4 conversion, C2+ selectivity, C2+ yield, and C2+ production. The catalyst study was mainly focused on the use of different MIEC catalysts and by considering state-of-the-art OCM catalysts. Furthermore, a study on the influence of reactor geometry on OCM performance was conducted by considering a BSCF capillary activated with a Mn-Na2WO4 on SiO2 catalytic packed bed.
Experimental
Dense Ba0.5Sr0.5Co0.8Fe0.2O3−δ planar membranes of 15 mm diameter and 0.8 mm thickness were prepared by uniaxial pressing at 150 kN, and subsequently sintered in air for 5 h at 1,100°C. BSCF powder was provided by Fraunhofer Institute for Ceramic Technologies and Systems (IKTS, Germany). The catalysts for the activation of membranes can be grouped in (i) MIEC perovskites, (ii) lanthanide doped cerias, (iii) MgO, and (iv) LaSr/CaO. The catalysts based on MIEC perovskites consisted of ABO3−δ formulations, obtained by doping A- and B- sites according to A0.6Sr0.4Co0.5Fe0.5O3−δ and Ba0.6Sr0.4BO3−δ formulations where A = La, Pr, Ba, Ce, Sm, and Nd and B = Fe and Co. MIEC catalysts powders were synthesized by Pechini method. For each catalyst, metal precursor nitrates were mixed in distilled water in order to obtain a clear solution. After complete dissolution, citric acid was added as a chelating agent, and ethylene glycol was added to polymerize with the chelating agent and produce an organometallic polymer (in a molar ratio 1:2:4 with respect to nitrates solution, citric acid, and ethylene glycol, respectively). This complexation was followed by dehydration at low temperature (up to 270°C) and finally, thermal decomposition of the precursors at 600°C formed the desired structural phases. Regarding the fluorite compounds, two different catalyst based on the system Ce1−xLnxO2−δ (x = 0.1; Ln = Tb, and Gd) were prepared by co-precipitation method. This technique consists of the dissolution of commercial lanthanide nitrates mixture in distilled water at 50°C. (NH4)2CO3 solution in a 1:1.5 molar ratio was dropped to achieve the total precipitation of the mixed cations. The resulting precursor powder was dried at 100°C after filtration and rinsing. MgO powders were supplied by Sigma-Aldrich. LaSr/CaO catalyst was prepared by co-precipitation method being the nominal composition 10 wt% La, 20 wt% Sr on CaO.
Catalytic activation of planar membranes was conducted by screen printing catalyst porous layers on one of the sides of the membrane, which will be exposed to the reaction. The screen printing ink consists of the ceramic powder, an organic binder (ethylcellulose) and a plasticizer (terpineol), mixed and subsequently refined in a three-roll mill. The ink is printed on the membrane surface through a 9 mm diameter mesh. Finally, the coated membranes were calcined in air at T = 1,010–1,050°C for 2 h.
The OCM experimental setup is illustrated in Figure 2. Gold O-ring gaskets were used for membranes sealing. Synthetic air (200 ml·min−1) was fed into the feed side while a dilution of 10% methane in argon (100 ml·min−1) was used as the sweep gas on the reaction side.
BSCF membranes with tubular geometry were acquired from Fraunhofer IKTS. BSCF capillaries were manufactured by plastic extrusion as described in Schulz et al. (2012), obtaining tubes with a length of 220 mm, an outer diameter of 3.25 mm, and an inner diameter of 2.55 mm, resulting in a wall thickness of 0.35 mm. The capillaries were dead-ended (sealed at one tube end). The capillary capping was made by joining a flat small disk by reactive air brazing (Erskine et al., 2002). Catalytic activation of BSCF capillary was done with a packed-bed consisting of 255 mg of Mn-Na2WO4/SiO2 catalyst (dp = 0.4–0.6 mm) and SiC in a relation 50% v/v. The experimental set-up used for conducting the tests on BSCF capillaries is depicted in Figure 3. The capillary exposed area was ~3.15 cm2, corresponding to a capillary length of 3 cm. The contact of the rest of the capillary with the reactant gases was avoided by placing a quartz tube–acting as liner- above the packed-bed all along the capillary. This quartz tube presents an inner diameter of 3.75 mm, being sufficient for wrapping completely the BSCF capillary. Top and bottom inlets of the tube were blocked, thus avoiding the reactant gases to be in contact with the membrane. This was done mainly for performing the OCM tests in the 3 cm-long isothermal zone of the used furnace, thus ensuring a constant temperature in all the reaction media. Same gas stream compositions and flow rates were used as for the tests using planar membranes.
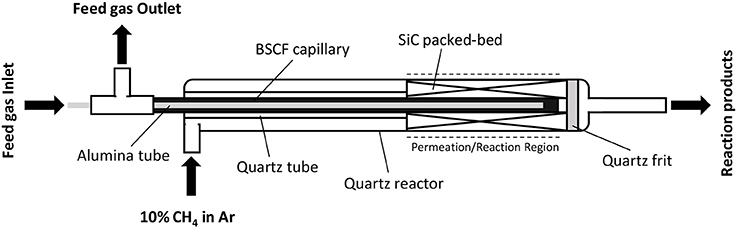
Figure 3. Simplified diagram of the lab-scale reactor for the conduction of capillary membrane studies.
Complete analysis of gases at both sides of the membrane was performed by gas chromatography (micro-GC Varian CP-4900 equipped with Molsieve5A, Pora-Plot-Q glass capillary, and CP-Sil modules). The flow and composition of the gas streams were individually controlled. Membrane gas-leak-free conditions were confirmed by continuously monitoring the N2 concentration in the gas stream exiting the catalyst chamber. An acceptable sealing was achieved when the ratio between the oxygen flow leak and the oxygen flux was lower than 1%. The temperature was measured by a thermocouple attached to the membrane (reaction side). A proportional–integral–derivative (PID) controller maintained temperature variations within 2°C of the set point. For evaluating the reaction performance, parameters such as methane conversion (XCH4), C2+-hydrocarbons selectivity (SC2+) and yield (YC2+), and ethylene productivity are determined from GC compounds analysis. The equations for the determination of these parameters are herein presented:
Where i includes all the species with carbon atoms in the products gas stream, F is the flow rate of the species expressed in mol·min−1, ni is the number of carbon atoms of component i, is the initial CH4 flow rate (in ml·min−1) and Aeffective is the effective membrane area for OCM reaction.
Results and Discussion
In a first approach, the OCM reaction was studied on BSCF disk-shaped planar membranes with thicknesses of 0.8 mm. As previously observed (Lobera et al., 2011, 2012a,b, 2017), surface catalytic activation of oxygen membranes produces a performance improvement of the chemical reactions, especially ethylene production. This is mainly due to the presence of active elements towards CH4 activation. Therefore, by considering catalyst particles with high O2− mobility and redox properties, products selectivity and yield can be significantly increased. Furthermore, the presence of porous structures increases the specific surface area, enlarging the number of active sites and improving gas flow dynamics for a better gas diffusion. Then, the activation of a BSCF membrane with several known active catalysts was considered (Lobera et al., 2011, 2012a,b, 2017). On Table 2, all the tested membranes are listed indicating the specifications of the catalytic layers.
All the catalysts were subjected to the same conditions of temperature and pO2, necessary to seal the membrane and be used as a CMR for OCM, so the final microstructure depends on the sintering behavior of each catalyst material under these preparation and sealing conditions. Figure 4, shows SEM images of some of the activated BSCF membranes. As expected, different layer morphologies are obtained depending on the deposited material, which will also play a role on the catalytic performance of each porous layer. A highly porous structure of 15 μm is obtained when depositing a BSCF layer and subsequently sintering at 1,010°C (Figure 4b). NdSCF, SmSCF, and LaCeSCF catalysts (Figures 4c,e,f) present a layer thickness in the range of 12–15 μm and also lower porosity degree than BSCF layer. LaSr/CaO activation (Figure 4d) layer, on the other hand, resulted in negligible porosity.
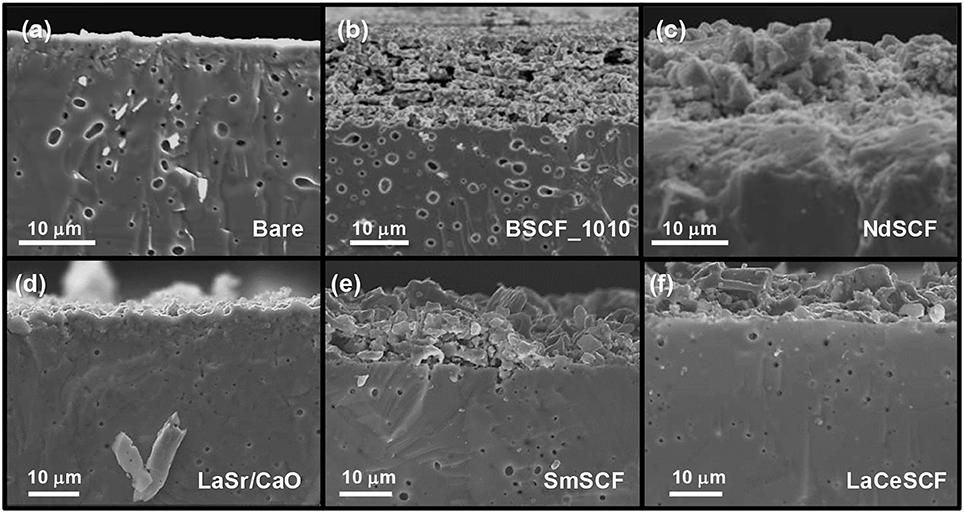
Figure 4. SEM images of different BSCF-coated membranes: (a) bare, (b) BSCF initially sintered at 1,010°C, (c) NdSCF, (d) LaSr/CaO, (e) SmSCF, and (f) LaCeSCF.
The activated BSCF membranes were tested at 900°C. Gas feed rate was 200 ml·min−1 of synthetic air (21% O2) and, as sweep gas, a reactant gas stream consisting of 100 ml·min−1 of 10% CH4 in argon was employed in the reaction chamber. Under these conditions, the O2 resulting from membranes permeation was in the range of 1.16–1.68 ml·min−1·cm−2, corresponding therefore to CH4/O2 ratios of 7.5–11. The obtained results are shown in Figure 5, where CH4 conversion, selectivity toward C2+ production, C2+ yield, and C2+ productivity are presented for each catalyst. The best results are obtained with the BSF_1010 activated membrane, reaching nearly 70% of C2+ selectivity, two fold the C2+ selectivity obtained with a non-activated BSCF membrane. Similar results were also observed in an ODHE catalytic study conducted on BSCF membranes where, despite the lower reducibility of BSF, higher C2+ selectivity was obtained (Lobera et al., 2012a). This can be related to a more suitable capability of BSF for conducting the coupling regardless its lower redox properties leading to a lower CH4 abstraction and subsequently, to a lower methane conversion. LaCeSCF and BaLaPrSCF activated membranes also present higher C2+ selectivity than BSCF (SC2+ in the range of 27–34%), with values of 64.7 and 58.2%, respectively. This improvement is ascribed to the incorporation of cations with mixed valence (Ce and Pr) in the A lattice position, that results in the modification in the redox behavior. The latter seems to alleviate the acidity increase resulting from the doping with cations presenting higher oxidation states (Zhou et al., 2008) that would lead to secondary reactions and to a loss in C2+. This gain in catalyst basicity is observed for SmSCF, which yields better C2+ selectivity than BSCF, being above 55%, whereas a more basic NdSCF performs similarly to BSCF. With regard to the lanthanide-doped cerias (CeTbO and CeGdO) the better performance is attributed to the combination of high oxygen-ion mobility and their better red-ox properties (Balaguer et al., 2011). The performance of LaSr/CaO catalyst regarding SC2+ is lower than the observed in the literature (Wang et al., 2005; Olivier et al., 2009) due to the lower surface specific area that the catalytic layer presents in this work (Figure 4d), resulting in a lesser number of accessible active sites, as well as a hindrance for the gas diffusion on the catalytic media. The low selectivity (13–15%) observed for the membranes activated with MgO interlayer is expected from to the low activity of MgO in the formation of CH3· radicals (Pak et al., 1998) and the observed deactivation of MgO catalysts with OCM reaction time (Wang et al., 1995; Pak et al., 1998). It is also significant the low C2+ selectivity observed for the membrane activated with Mn-Na2WO4 on SiO2 catalyst. Only a SC2+ of 30% is obtained, when previous studies show C2+ selectivity of up to 80% (Farrell et al., 2016). The reason for such a low result can stem from the reaction between SiO2 and BSCF leading to the formation of a SiO2 layer on membrane surface and to the partial blocking of O2 permeation (Thaler et al., 2016). Moreover, SiO2 sintering and transition to α-Cristobalite from amorphous silica (catalyst support) also results in a loss of selectivity (Palermo et al., 1998; Asadi et al., 2012). It is worthy to mention that BSCF membrane activation with a BSCF porous layer does not entail a performance improvement in all the systems. Some of them present lower C2+ selectivity as compared with the bare membrane, which can be related with a gas diffusion hindrance resulting from the layer deposition, thus preventing CH4 to reach the active sites or due to a fast recombination of surface O2− into gaseous O2, which would react with CH4 causing combustion, and making these catalysts not useful for the system in a first approach. Concerning CH4 conversion (Figure 5A) the obtained results are in the range of 2–8%, with MgO and MgO_Mn-Na2WO4 yielding the highest methane conversion rates, in spite of their low C2+ selectivity. Moreover, the use of 2 wt% Mn/5 wt% Na2WO4 on SiO2 as catalyst coated on top of the 3 BSCF_1010 layer rises XCH4 from 2 to 7%, while maintaining SC2+. This important increase in conversion may arise from the high activity of Mn-Na2WO4 on SiO2, in spite of the low C2+ production. Ceria based catalysts also present high conversion rates. Activation with CeTbO and CeGdO results in XCH4 of 5.3 and 6.5%, being higher than most of the tested perovskite catalysts. Again, the better redox properties and the higher ionic conductivity favor the conduction of OCM reaction.
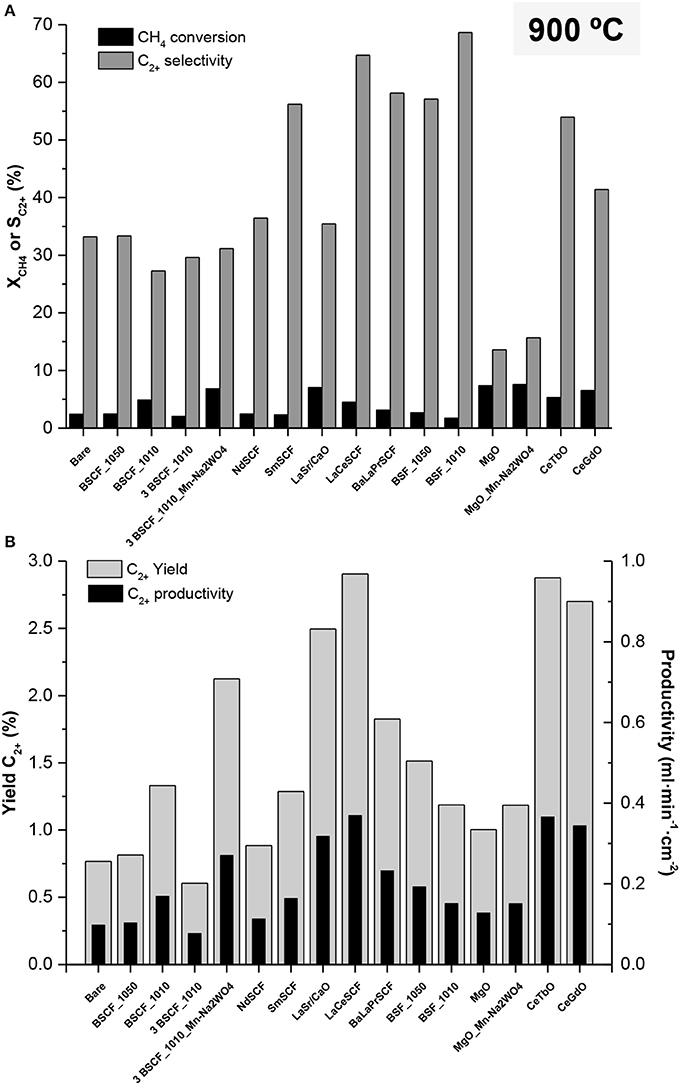
Figure 5. (A) CH4 conversion and selectivity to C2+-hydrocarbon and (B) yield to C2+-hydrocarbon for different planar BSCF membrane reactors at 900°C. 10% of CH4, Q(CH4+Ar) = 100 ml·min−1, QAir = 200 ml·min−1 (pO2 = 0.21 bar).
The highest C2+ yields at 900°C (Figure 5B) range among 2.5–3% and correspond to CeTbO, CeGdO, LaCeSCF, and LaSr/CaO catalysts. On the other hand, maximum C2+ productivities correspond to LaCeSCF and CeTbO activated membranes. Their C2+ productivities of 0.37 mlC2+·min−1·cm−2 represent nearly a four-fold improvement with respect to the non-activated membrane.
Further OCM tests were performed at 1,000°C maintaining the same feed and reactant gas flow rates as in the previous tests conducted at 900°C. Nevertheless, and due to the increase in temperature, the O2 permeation of the membranes also increased (up to 2.2–2.6 ml·min−1·cm−2). This led to lower CH4/O2 ratios in the range of 4.8–5.6, and subsequently, to a significant increase in CH4 conversion for all the catalysts, with a maximum XCH4 of 18.5% for the 3 BSCF_1010 Mn-Na2WO4 activated membrane (Figure 6A). The increase in temperature and the subsequent reduction in CH4/O2 ratios also allowed an improvement in C2+ selectivity (74%) for most of the catalysts, presenting values above 50%. This gain in XCH4 and SC2+ can also be ascribed to the higher generation of when operating at higher temperatures (Xu and Thomson, 1997). Again, the highest C2+ selectivity is reached with BSF_1010 catalytic layer. As can be seen in Figure 6B, operation at 1,000°C produces an important shift in C2+ yield and productivity, with a peak yield of nearly 9% when considering CeTbO activation. C2+ yields >8.7% are also obtained with CeGdO and 3 BSCF_1010 Mn-Na2WO4 catalysts. A maximum of C2+ productivity of 1.14 mlC2+·min−1·cm−2 is obtained with CeTbO. According to the 30% yield target established for considering OCM reaction as techno-economically viable, the obtained results are far below this threshold, despite the good C2+ selectivities obtained for some of the catalysts.
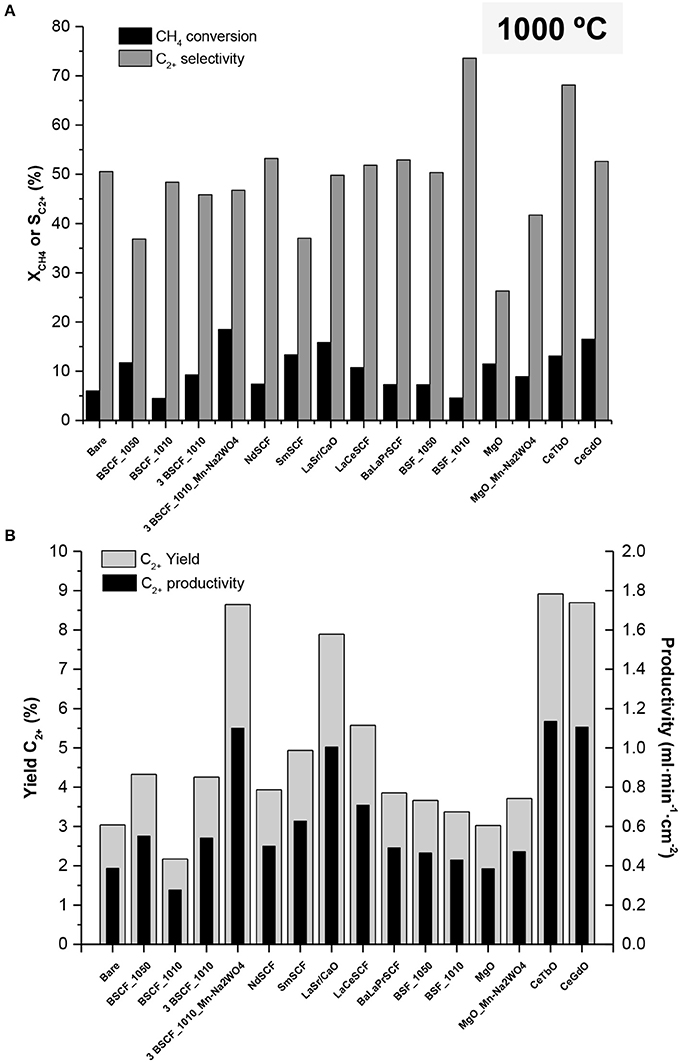
Figure 6. (A) CH4 conversion and selectivity to C2+-hydrocarbon and (B) yield to C2+-hydrocarbon for different planar BSCF membrane reactors at 1,000°C. 10% of CH4, Q(CH4+Ar) = 100 ml·min−1, QAir = 200 ml·min−1 (pO2 = 0.21 bar).
In a previous study, Zeng and Lin observed a relation between CMR configuration and OCM reaction performance, reporting an improvement in C2+ yield from 11 to 17% by increasing membrane surface area to reactor volume ratio (Zeng and Lin, 2001). Indeed, issues such as reactor design/configuration and inadequate reactant gas distribution can prevent the proper access of CH4 molecules to the active sites, thus limiting methane conversion rates. Therefore, OCM studies on BSCF tubular membranes reactor were also considered. Tubular designs provide a distributed feed of O2 along the reactor length and a higher surface reaction area, leading to higher CH4 conversion rates per membrane unit length, and increasing C2+ yields. A catalytic packed-bed consisting of 50% vol. 2% Mn, 5% Na2WO4 on SiO2 and SiC was prepared for the activation of a BSCF capillary. OCM tests were carried out at 900°C, 200 ml·min−1 of synthetic air feed, and using a stream of 10% CH4 in argon as reactant gas. The reactant gas flow rates varied from 50 to 600 ml·min−1, corresponding to CH4/O2 ratios of 1 and 2.7, respectively. As a result, XCH4 progressively decreased (Figure 7) when increasing reactant flow rate, thus evidencing the effect of the higher CH4/O2 ratio. Nevertheless, the lower residence time resulting from the increase in reactant gas flow rate is also expected to affect negatively CH4 reaction. Differently, C2+ selectivity progressively improves with increasing reactant gas flow rate, with a maximum of ca. 45% at 600 ml·min−1. The highest C2+ yield is achieved at 100 ml·min−1 with a value of 15.6% at a CH4 conversion of 54% and a C2+ selectivity of 29%. Concerning C2+ productivity, 0.9 ml·min1·cm−2 are obtained with a flow rate of 400 ml·min−1. On the other hand, low space velocities involve higher SCO2, due to a higher CH4 oxidation toward CO2 at higher residence times. As the main interest of this reaction is the production of C2+, then the most suitable conditions would be set at low space velocities, with flow rates in the range of 50–200 ml·min−1.
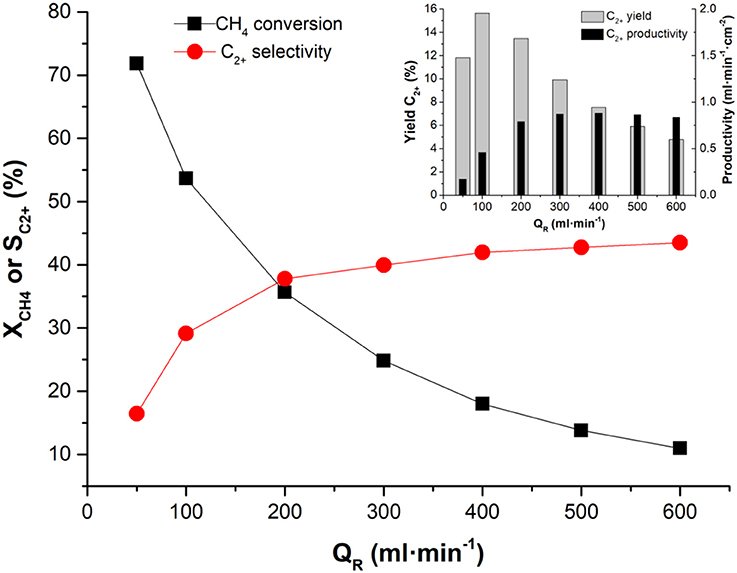
Figure 7. Effect of the variation of reactant gas flow rate on XCH4 and SC2+, and on YC2+ and C2+H4 productivity (Inset). Test conducted at 900°C with 200 ml·min−1 synthetic air feeding and 10% CH4 in Ar.
Finally, Figure 8 summarizes and compares the results obtained for both planar and tubular BSCF CMRs considered in the present work, represented by the SC2+ as a function of the converted CH4. These results were obtained at 900°C and reactant gas flow rates in the range of 100–300 ml·min−1. Under such conditions, planar membranes show CH4/O2 ratios in the range of 7.5–11, whereas tubular configuration presents much lower ratios of 1.7–2.4. Indeed, significant shift in XCH4 is visible when comparing planar and tubular CMRs activated with Mn-Na2WO4/SiO2 catalyst due to the higher availability of O2. While SC2+ of 30–40% was obtained for both cases, CH4 conversion increased from 4 to 7% up to 60% when conducting OCM in the tubular reactor. This is due to the higher membrane surface area to reactor volume ratio of tubular configurations that allows the dosing of higher amounts of O2. This eventually improves OCM performance by boosting CH4 conversion, achieving C2+ yields of 15.6%. The best results regarding selectivity toward C2+ production correspond to planar membranes activated with BSF, LaCeSCF, and SmSCF, presenting selectivity of ca. 65–70%. Nevertheless, the low XCH4 rates lead to poor C2+ yields -ranging from 0.5 to 2.5%, which are very low for practical consideration. The better performance observed with the tubular CMR is mainly ascribed to the lower CH4/O2 ratios used during the tests, which results from the increase of membrane surface area with respect to reactor volume. Therefore, for a given reactor geometry, the increase of this parameter and the selection of operation conditions resulting in higher CH4/O2 ratios can lead to the achievement of higher C2+ yields. For our reactor, the high conversions of nearly 60% obtained with the tubular CMR combined with the high C2+ selectivity of catalysts like LaCeSCF or SmSCF set a promising scenario for reaching the considered C2+ yield target of 30% if these catalysts are used for the activation of BSCF capillary membranes.
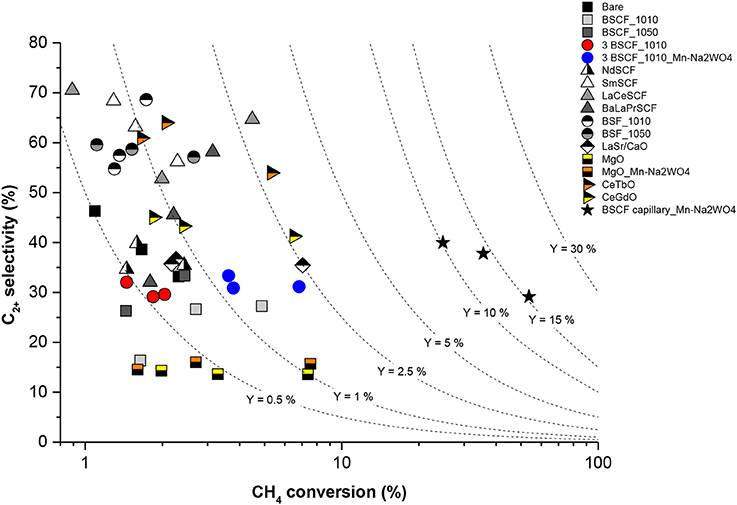
Figure 8. C2+ hydrocarbon selectivity in dependence of methane conversion for different activated BSCF membranes. Test conditions: 900°C, synthetic air feeding (200 ml·min−1), 10% CH4 in argon as reactant gas (100–300 ml·min−1).
Conclusions
A study on oxidative coupling of methane for the production of ethylene was conducted considering CMR based on BSCF. In a first approach, a catalytic screening in CMR for OCM was conducted on disk-shaped planar BSCF membranes. The catalytic activation of membranes with 15 different catalysts allowed the identification of the most active compounds on these temperature conditions for the maximization of C2+ production. The highest C2+ selectivity at 900°C was 70%, reached with BSF and LaCeSCF catalysts. Despite the good selectivity, the low CH4 conversions resulted in C2+ yields below 3% for this CMR configuration. Operation at higher temperatures (e.g., 1,000°C) produced a significant improvement in XCH4 for all the activated membranes due to the decrease in CH4/O2 ratios, thus obtaining much higher C2+ yields of up to nearly 9% and productivities of ca. 1.2 ml·min−1·cm−2 with CeGdO and 3 BSCF_1010 Mn-Na2WO4 catalysts. Conduction of OCM reaction on a catalytic membrane reactor with tubular geometry permitted the achievement of CH4/O2 ratios of 1.7–2.5 that improved C2+ yield, with a maximum of 15.6% at 900°C for a BSCF capillary activated with 2 wt% Mn/5 wt% Na2WO4 on SiO2 catalyst. This improvement is ascribed to the combined effect of the catalyst high activity toward CH4 conversion and the higher membrane surface area available for the conduction of OCM reaction and favorable geometry, resulting in lower CH4/O2. Therefore, the selection of the most active catalysts under CMR conditions, the operation with low CH4/O2 ratios, and the addressing of actions for the improvement of CMR design would allow achieving higher C2+, approaching techno-economic targets.
Author Contributions
JS: project manager; JS, ML, MB, and JG-F: manuscript writing and results interpretation; ML, MB, and JG-F: experiments.
Conflict of Interest Statement
The authors declare that the research was conducted in the absence of any commercial or financial relationships that could be construed as a potential conflict of interest.
Acknowledgments
Financial support by the Spanish Government (ENE2014-57651 and SEV-2012-0267 grants) and by the EU through FP7 GREEN-CC Project (GA 608524), is gratefully acknowledged. The authors want also acknowledge the Electron Microscopy Service from the Universitat Politècnica de València for their support in the SEM analysis performed in this work.
Footnotes
1. ^
where J(O2) is the oxygen permeation, R is the gas constant, T is the temperature, F is the Faraday′s constant, L is the membrane thickness, pO2” and pO2' stand for the O2 partial pressures at feed and permeate sides, respectively, and σamb is the ambipolar conductivity of the membrane material.
References
Akin, F. T., and Lin, Y. S. (2002). Oxidative coupling of methane in dense ceramic membrane reactor with high yields. AIChE J. 48, 2298–2306. doi: 10.1002/aic.690481019
Amenomiya, Y., Birss, V. I., Goledzinowski, M., Galuszka, J., and Sanger, A. R. (1990). Conversion of methane by oxidative coupling. Catal. Rev. Sci. Eng. 32, 163–227. doi: 10.1080/01614949009351351
Asadi, A. A., Behrouzifar, A., Iravaninia, M., Mohammadi, T., and Pak, A. (2012). Preparation and oxygen permeation of La0.6Sr0.4Co0.2Fe0.8O3−d (LSCF) perovskite-type membranes: experimental study and mathematical modeling. Indus. Eng. Chem. Res. 51, 3069–3080. doi: 10.1021/ie202434k
Aseem, A., and Harold, M. P. (2018). C-2 yield enhancement during oxidative coupling of methane in a nonpermselective porous membrane reactor. Chem. Eng. Sci. 175, 199–207. doi: 10.1016/j.ces.2017.09.035
Balaguer, M., Solis, C., and Serra, J. M. (2011). Study of the transport properties of the mixed ionic electronic conductor Ce1−xTbxO2−d + Co (x = 0.1, 0.2) and evaluation as oxygen-transport membrane. Chem. Mater. 23, 2333–2343. doi: 10.1021/cm103581w
Bhasin, M. M., McCain, J. H., Vora, B. V., Imai, T., and Pujadó, P. R. (2001). Dehydrogenation and oxydehydrogenation of paraffins to olefins. Appl. Catal. A Gen. 221, 397–419. doi: 10.1016/S0926-860X(01)00816-X
Bhatia, S., Thien, C. Y., and Mohamed, A. R. (2009). Oxidative coupling of methane (OCM) in a catalytic membrane reactor and comparison of its performance with other catalytic reactors. Chem. Eng. J. 148, 525–532. doi: 10.1016/j.cej.2009.01.008
Chen, J. Q., Bozzano, A., Glover, B., Fuglerud, T., and Kvisle, S. (2005). Recent advancements in ethylene and propylene production using the UOP/Hydro MTO process. Catal. Today 106, 103–107. doi: 10.1016/j.cattod.2005.07.178
Czuprat, O., Schiestel, T., Voss, H., and Caro, J. (2010). Oxidative coupling of methane in a BCFZ perovskite hollow fiber membrane reactor. Indus. Eng. Chem. Res. 49, 10230–10236. doi: 10.1021/ie100282g
Erskine, K. M., Meier, A. M., and Pilgrim, S. M. (2002). Brazing perovskite ceramics with silver/copper oxide braze alloys. J. Mater. Sci. 37, 1705–1709. doi: 10.1023/A:1014912923977
Farrell, B. L., Igenegbai, V. O., and Linic, S. (2016). A viewpoint on direct methane conversion to ethane and ethylene using oxidative coupling on solid catalysts. ACS Catal. 6, 4340–4346. doi: 10.1021/acscatal.6b01087
Grubert, G., Kondratenko, E., Kolf, S., Baerns, M., van Geem, P., and Parton, R. (2003). Fundamental insights into the oxidative dehydrogenation of ethane to ethylene over catalytic materials discovered by an evolutionary approach. Catal. Today 81, 337–345. doi: 10.1016/S0920-5861(03)00132-9
Hutchings, G. J., Scurrell, M. S., and Woodhouse, J. R. (1989). Oxidative coupling of methane using oxide catalysts. Chem. Soc. Rev. 18, 251–283. doi: 10.1039/cs9891800251
Ito, T., and Lunsford, J. H. (1985). Synthesis of ethylene and ethane by partial oxidation of methane over lithium-doped magnesium-oxide. Nature 314, 721–722. doi: 10.1038/314721b0
Karakaya, C., Zhu, H., Zohour, B., Senkan, S., and Kee, R. J. (2017). Detailed reaction mechanisms for the oxidative coupling of methane over La2O3/CeO2 nanofiber fabric catalysts. Chemcatchem 9, 4538–4551. doi: 10.1002/cctc.201701172
Keil, F. J. (1999). Methanol-to-hydrocarbons: process technology. Micropor. Mesopor. Mater. 29, 49–66. doi: 10.1016/S1387-1811(98)00320-5
Keller, G. E., and Bhasin, M. M. (1982). Synthesis of ethylene via oxidative coupling of methane: I. Determination of active catalysts. J. Catal. 73, 9–19. doi: 10.1016/0021-9517(82)90075-6
Lobera, M. P., Balaguer, M., Garcia-Fayos, J., and Serra, J. M. (2012a). Rare earth-doped ceria catalysts for ODHE reaction in a catalytic modified MIEC membrane reactor. Chemcatchem 4, 2102–2111. doi: 10.1002/cctc.201200212
Lobera, M. P., Balaguer, M., García-Fayos, J., and Serra, J. M. (2017). Catalytic oxide-ion conducting materials for surface activation of Ba0.5Sr0.5Co0.8Fe0.2O3−δ membranes. ChemistrySelect 2, 2949–2955. doi: 10.1002/slct.201700530
Lobera, M. P., Escolástico, S., Garcia-Fayos, J., and Serra, J. M. (2012b). Ethylene production by ODHE in catalytically modified Ba0.5Sr0.5Co0.8Fe0.2O3−d membrane reactors. Chemsuschem 5, 1587–1596. doi: 10.1002/cssc.201100747
Lobera, M. P., Escolastico, S., and Serra, J. M. (2011). High ethylene production through oxidative dehydrogenation of ethane membrane reactors based on fast oxygen-ion conductors. Chemcatchem 3, 1503–1508. doi: 10.1002/cctc.201100055
Lunsford, J. H. (1995). The catalytic oxidative coupling of methane. Angew. Chem. Int. Edn. Engl. 34, 970–980. doi: 10.1002/anie.199509701
Lunsford, J. H. (2000). Catalytic conversion of methane to more useful chemicals and fuels: a challenge for the 21st century. Catal. Today 63, 165–174. doi: 10.1016/S0920-5861(00)00456-9
Maitra, A. M. (1993). Critical performance evaluation of catalysts and mechanistic implications for oxidative coupling of methane. Appl. Catal. Gen. 104, 11–59.
Mleczko, L., and Baerns, M. (1995). Catalytic oxidative coupling of methane - reaction-engineering aspects and process schemes. Fuel Process. Technol. 42, 217–248. doi: 10.1016/0378-3820(94)00121-9
Mleczko, L., Pannek, U., Niemi, V. M., and Hiltunen, J. (1996). Oxidative coupling of methane in a fluidized-bed reactor over a highly active and selective catalyst. Indus. Eng. Chem. Res. 35, 54–61. doi: 10.1021/ie950145s
Olivier, L., Haag, S., Mirodatos, C., and van Veen, A. C. (2009). Oxidative coupling of methane using catalyst modified dense perovskite membrane reactors. Catal. Today 142, 34–41. doi: 10.1016/j.cattod.2009.01.009
Othman, N. H., Wu, Z., and Li, K. (2015). An oxygen permeable membrane microreactor with an in-situ deposited Bi1.5Y0.3Sm0.2O3−δ catalyst for oxidative coupling of methane. J. Membr. Sci. 488, 182–193. doi: 10.1016/j.memsci.2015.04.027
Otsuka, K., Jinno, K., and Morikawa, A. (1986). Active and selective catalysts for the synthesis of C2H4 and C2H6 via oxidative coupling of methane. J. Catal. 100, 353–359. doi: 10.1016/0021-9517(86)90102-8
Pak, S., Qiu, P., and Lunsford, J. H. (1998). Elementary reactions in the oxidative coupling of methane over Mn/Na2WO4/SiO2and Mn/Na2WO4/MgO catalysts. J. Catal. 179, 222–230. doi: 10.1006/jcat.1998.2228
Palermo, A., Holgado Vazquez, J. P., Lee, A. F., Tikhov, M. S., and Lambert, R. M. (1998). Critical influence of the amorphous silica-to-cristobalite phase transition on the performance of Mn/Na2WO4/SiO2 catalysts for the oxidative coupling of methane. J. Catal. 177, 259–266. doi: 10.1006/jcat.1998.2109
Reporters, P. (2016). The Ethylene Technology Report 2016. Available online at: www.researchandmarkets.com
Schulz, M., Pippardt, U., Kiesel, L., Ritter, K., and Kriegel, R. (2012). Oxygen permeation of various archetypes of oxygen membranes based on BSCF. AIChE J. 58, 3195–3202. doi: 10.1002/aic.13843
Spallina, V., Velarde, I. C. J., Jimenez, A. M., Godini, H. R., Gallucci, F. M., and Annaland, V. S. (2017). Techno-economic assessment of different routes for olefins production through the oxidative coupling of methane (OCM): advances in benchmark technologies. Energy Convers. Manage. 154, 244–261. doi: 10.1016/j.enconman.2017.10.061
Stansch, Z., Mleczko, L., and Baerns, M. (1997). Comprehensive kinetics of oxidative coupling of methane over the La2O3/CaO catalyst. Indus. Eng. Chem. Res. 36, 2568–2579. doi: 10.1021/ie960562k
Sunarso, J., Baumann, S., Serra, J. M., Meulenberg, W. A., Liu, S., Lin, Y. S., et al. (2008). Mixed ionic-electronic conducting (MIEC) ceramic-based membranes for oxygen separation. J. Membr. Sci. 320, 13–41. doi: 10.1016/j.memsci.2008.03.074
Tan, X., and Li, K. (2006). Oxidative coupling of methane in a perovskite hollow-fiber membrane reactor. Indus. Eng. Chem. Res. 45, 142–149. doi: 10.1021/ie0506320
Tan, X., Pang, Z., Gu, Z., and Liu, S. (2007). Catalytic perovskite hollow fibre membrane reactors for methane oxidative coupling. J. Membr. Sci. 302, 109–114. doi: 10.1016/j.memsci.2007.06.033
Tenelshof, J. E. H., Bouwmeester, J. M., and Verweij, H. (1995). Oxidative coupling of methane in a mixed-conducting perovskite membrane reactor. Appl. Catal. Gen. 130, 195–212.
Thaler, F., Müller, M., and Spatschek, R. (2016). Oxygen permeation through perovskitic membranes: the influence of steam in the sweep on the permeation performance. AIMS Mater. Sci. 3, 1126–1137. doi: 10.3934/matersci.2016.3.1126
Wang, D. J., Rosynek, M. P., and Lunsford, J. H. (1995). Oxidative coupling of methane over oxide-supported sodium-manganese catalysts. J. Catal. 155, 390–402. doi: 10.1006/jcat.1995.1221
Wang, H., Cong, Y., and Yang, W. (2005). Oxidative coupling of methane in Ba0.5Sr0.5Co0.8Fe0.2O3−δ tubular membrane reactors. Catal. Today 104, 160–167. doi: 10.1016/j.cattod.2005.03.079
Xu, S. J., and Thomson, W. J. (1997). Perovskite-type oxide membranes for the oxidative coupling of methane. AIChE J. 43, 2731–2740. doi: 10.1002/aic.690431319
Zeng, Y., and Lin, Y. S. (2001). Oxidative coupling of methane on improved bismuth oxide membrane reactors. AIChE J. 47, 436–444. doi: 10.1002/aic.690470220
Zeng, Y., Lin, Y. S., and Swartz, S. L. (1998). Perovskite-type ceramic membrane: synthesis, oxygen permeation and membrane reactor performance for oxidative coupling of methane. J. Membr. Sci. 150, 87–98. doi: 10.1016/S0376-7388(98)00182-3
Keywords: catalytic membrane reactor, oxygen transport membrane, BSCF, OCM, ethylene production, ionic conductor
Citation: Garcia-Fayos J, Lobera MP, Balaguer M and Serra JM (2018) Catalyst Screening for Oxidative Coupling of Methane Integrated in Membrane Reactors. Front. Mater. 5:31. doi: 10.3389/fmats.2018.00031
Received: 19 February 2018; Accepted: 11 May 2018;
Published: 03 August 2018.
Edited by:
David Alfredo Pacheco Tanaka, Tecnalia, SpainReviewed by:
Jose A. Medrano, Eindhoven University of Technology, NetherlandsTridib Kumar Sinha, Gyeongsang National University, South Korea
Copyright © 2018 Garcia-Fayos, Lobera, Balaguer and Serra. This is an open-access article distributed under the terms of the Creative Commons Attribution License (CC BY). The use, distribution or reproduction in other forums is permitted, provided the original author(s) and the copyright owner(s) are credited and that the original publication in this journal is cited, in accordance with accepted academic practice. No use, distribution or reproduction is permitted which does not comply with these terms.
*Correspondence: Jose M. Serra, am1zZXJyYUBpdHEudXB2LmVz