- Department of Earth and Environmental Science, University of Pennsylvania, Philadelphia, PA, United States
3D printing has made it possible to recreate, actuate, and modify replicas of ancient life in transformative ways—revolutionizing studies of ancient life. While 3D printing has previously been emphasized as an educational tool in paleontology, it has also created a wide array of experimental opportunities previously unavailable to investigators. Although 3D printing has been used extensively for experimental studies in many STEM fields, the biases of the fossil record and constraints of the fossilization process create unique challenges for paleontological studies. Here, we outline a guide for using this technology for experimental paleontology: from designing a virtual model to choosing the most effective printing material—highlighting successful employment of these methods by previous investigators. As it can be challenging to adopt new methods in a meaningful way, we hope that this paper will serve as a useful tool for current and future paleontologists who seek to apply these techniques.
Introduction
The fossilization process renders once dynamic, living taxa into static, geologic forms. Paleontologists are challenged to work within these limitations to reconstruct complex organisms and investigate related questions of functional morphology, paleoecology, and macroevolutionary processes. 3D printing, which has been widely used in related fields for years (e.g., Weber, 2001; Igic et al., 2015; Fiorenza et al., 2018) recently began to make a concerted appearance in experimental paleontology. This time lag, and lack of paleontological literature using this approach, likely reflects the unique limitations of historical sciences and the fossilization process. As a result, much of the literature on 3D printing in paleontology is still limited to conference abstracts (see topical session: Applications of 3D Printing and Other 3D Methods to Experimental Paleontology, Geological Society of America 2018). Although we, the authors of this paper, study fundamentally different taxa we found common challenges adopting 3D printing techniques to study functional morphology. In its limited scope, this mini-review provides a broad introduction to many potential uses of 3D printing in experimental paleontology. We outline a generalized approach to guide those new to using 3D printing.
3D Replicas in Paleontology
Three-dimensional representations of fossil organisms have classically been integral to paleontological research. Early researchers used molds and casts to share fossil replicas with other investigators and the public (Vernon, 1957; Waters and Savage, 1971). Later, digital replicas generated by surface and Computed-tomography (CT) scanning were used for visualizing fossils in three dimensions (see Cunningham et al., 2014 for review). These virtual techniques allowed investigators to examine minute details of biological structures and provided insights to fossil interiors, previously unseen barring destructive sampling (see Rivera and Sumner, 2014; Schemm-Gregory, 2014). Today, researchers can render virtual files tangible once again, by converting scans to formats that allow modification and 3D printing for education and further study (Teshima et al., 2010; Rahman et al., 2012; Cunningham et al., 2014; Hasiuk, 2014). Furthermore, the falling costs of printers has made 3D printing a viable option for explicit experimental paleontological study.
3D printing is advantageous for paleontologists who wish to replicate and modify fossils. Specifically, printing enables investigators to remove and reform fossils from their matrix and permits the manipulation of taphonomically distorted specimens. Additionally, the ability to alter existing taxa or create new, hypothetical forms allows the study of non-existent morphologies, optimization, and evolutionary constraint (see Porter et al., 2015). Paleontologists have 3D printed numerous vertebrate morphologies including dinosaurs, fishes, marine reptiles, and mammals (Balanoff and Rowe, 2002; Bristowe et al., 2004; Schilling et al., 2013; Mitsopoulou et al., 2015; Das et al., 2017; Muscutt et al., 2017; White et al., 2017; Clark, 2018; Grant et al., 2018; Voegele et al., 2018) as well as invertebrates like mollusks, trilobites, brachiopods, and echinoderms (Huynh et al., 2013; Pearson, 2017; Anderson et al., 2018; DiMarco et al., 2018; Garcia et al., 2018; Johnson et al., 2018; Morse et al., 2018; Peterman and Ciampaglio, 2018; Dievert et al., 2019). Designing meaningful physical models for experimentation requires thoughtful printing choices to isolate variables. Here we describe a generalized workflow for 3D printing in experimental paleontology, including creating a printable model of the taxa of interest, choosing materials, pre-processing prints, and finally printing and post-processing physical models.
A Generalized Workflow for 3D Printing in Experimental Paleontology
Model Creation
There are many different approaches to using 3D printing to test paleontological hypotheses. However, typically, the first step is to create a virtual model that accurately captures the morphology of interest (Figure 1). Subsequent decisions regarding printing material and methods rely heavily on the parameters of this virtual model. Such models are mainly derived from surface scans, internal scans, computer-generated models, or some combination of these methods (Figures 2A–D). Each model type has benefits that may be useful for various experiments.
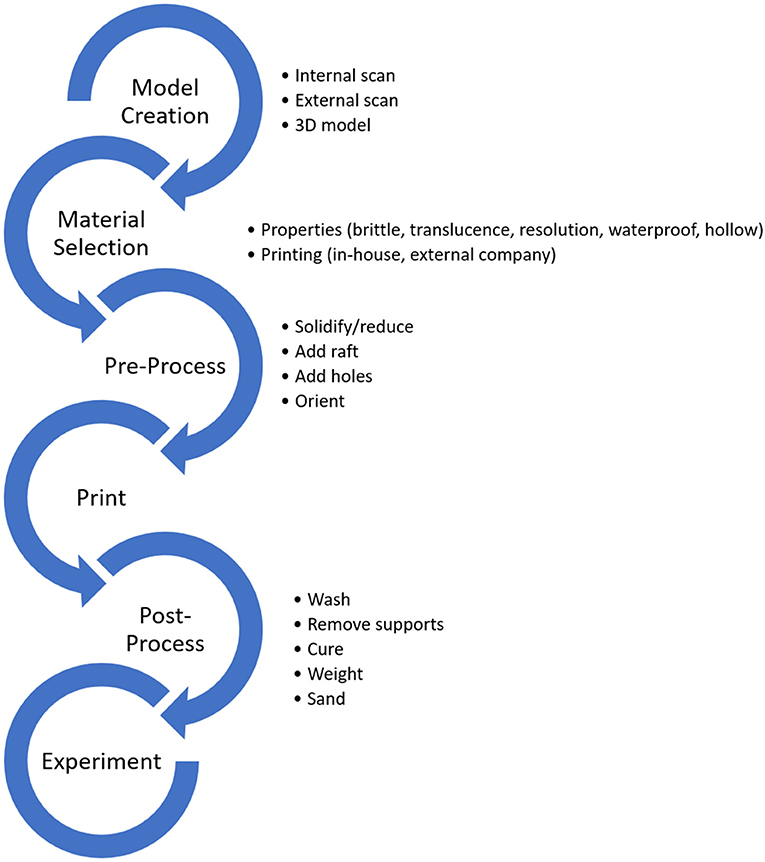
Figure 1. A general workflow for 3D printing for experimental paleontology. Critical decisions are outlined next to each step.
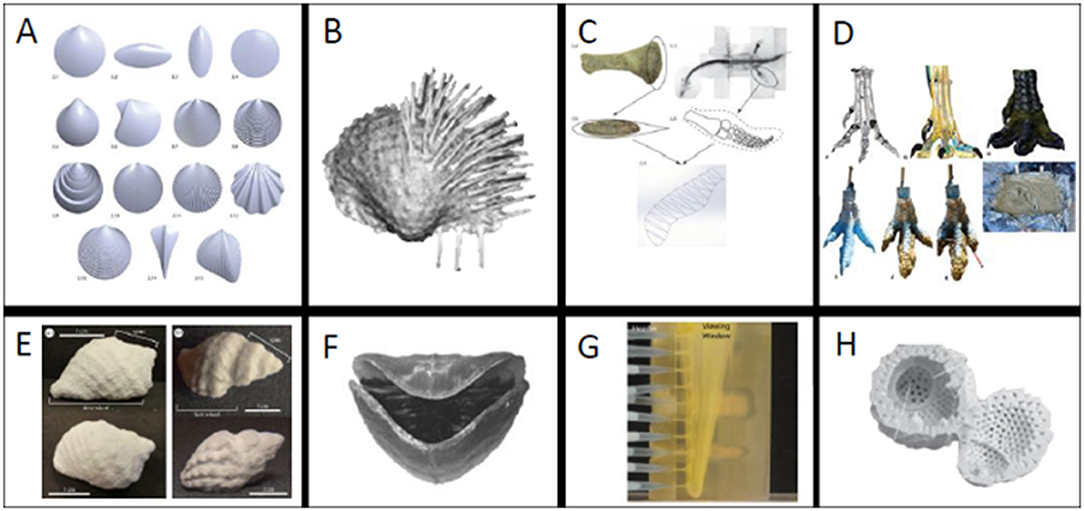
Figure 2. (A–D) Examples of models derived fully or in part using 3D software and (E–H) examples of different 3D printing materials. (A) Mathematically rendered bivalves, (B) scanned brachiopod with spines added in 3D program, (C) plesiosaur flipper reconstructed from bone measurements, (D) Theropod foot created with scan and Rhinoceros 5.0 [A from Germann et al. (2014) (used with permission via CC BY license, Palaeontological Association), B from Garcia et al. (2018) (used with permission from Elsevier), C from (Muscutt et al., 2017) (used with permission from the Royal Society), D from (White et al., 2017) (used with permission from permission via CC BY license, PeerJ) ]. (E) Composite powder snail shell (F) ABS brachiopod (G) Tranluscent ABS polymer blastoid (H) plaster radiolarian [E from (Crofts and Summers, 2014) (used with permission from How to best smash a snail: the effect of tooth shape on crushing load.), F from (Dievert et al., 2019) (used with permission from Elsevier), G (Huynh et al., 2013) (used with permission via CC BY license, Paleontological Society), H (Ishida and Kishimoto, 2015) (used with permission via CC BY license, Volumnia Jurassica). (Images not to scale).
Surface scans render exterior geometry by two main means: laser projection or a series of photographs taken at different angles (Sutton et al., 2014). Therefore, surface scans are incredibly useful tools to record and replicate fossils that cannot be moved from their current location. For example, Grant et al. (2018) used surface scanning to create prints of dinosaur tracks that could be widely distributed for educational purposes (see also Grant et al., 2016). Moreover, scans of external morphology are tremendously useful for kinematic studies of geometry, where the investigator is concerned only with the boundaries defined by shape (Clark, 2018; Garcia et al., 2018; Grant et al., 2018). Clark (2018) laser-scanned and 3D printed Allosaurus teeth to study relationships between tooth shape and ability to puncture prey by relating tooth morphology to puncture depth. In this case, a surface scan was sufficient; however, studies seeking to isolate internal morphology cannot be captured with a laser scanner.
Internal scans (e.g., Computed-tomography, Magnetic Resonance Imaging, Synchrotron) in general use magnetic energy (MRI) or X-rays (CT and Synchrotron) to generate images of sub-surface structures. CT scans and related methods are useful primarily for developing models of internal structures which may not be readily visible and cases in which the fossil is embedded in a matrix that must be differentiated from the specimen (Crofts and Summers, 2014; Kolmann et al., 2015; Pearson, 2017; Anderson et al., 2018; DiMarco et al., 2018; Morse et al., 2018). Internal scans produce images slices that are later used to outline and excise morphologies of interest from unneeded morphologies or sediment (i.e., segmentation). This is done using visualization software, some of which are open source.
Internal scans have permitted studies of the form and function of previously inaccessible morphologies. DiMarco et al. (2018) CT scanned and printed baculite septa to study the capability of complex septa to resist crushing by a predator. CT scans allowed the investigators to isolate the chamber walls of shelled cephalopods and artificially create simple alternative walls for comparison. Ishida and Kishimoto (2015) instead used x-rays to print and study models of radiolarians to examine miniscule morphologies (Figure 2H). Morse et al. (2018) combined data from microCT scans and serial grinding of concavo-convex brachiopods to study the relationship between hinge morphology and life position.
Internal scans are useful for creating 3D printed replicas of specimens that cannot be studied otherwise due to their hidden nature. For example, Schilling et al. (2013) demonstrated the utility of CT scanning by segmenting a dinosaur vertebra out of surrounding matrix and 3D printing it. Likewise, Lak et al. (2008) used phase-contrast X-ray synchrotron imaging to identify fossils preserved in opaque amber, which could later be 3D printed for examination. Rather than scanning some investigators elect to create their models entirely in 3D modeling programs.
3D printing provides is the ability to physically test questions motivated by idealized and hypothetical morphologies; which may be later compared to realized forms in the fossil record or modern taxa. This can be achieved using mathematical models (Germann et al., 2014; Johnson et al., 2018) and designs based on morphological measurements (Muscutt et al., 2017) (Figure 2C). Such models can be constructed in many 3D programs, some of which are open access (e.g., Meshmixer1, Blender2, and Fusion 3603. Johnson et al. (2018) and Germann et al. (2014) (Figure 2A) used different mathematical models to design mollusk shells for studies of functional morphology. Johnson et al. (2018) employed equations that described gastropod shells as a surface rotating around an axis in a logarithmic spiral following the mathematical model of Raup (1966) (see also Raup and Michelson, 1965). The strength of these shell geometries was then physically tested in a compression apparatus to evaluate their adaptive value against shell-crushing predators. To study the functional morphology of burrowing bivalves, Germann et al. (2014) created shells with varying shapes and ornamentations. These shells were 3D printed to test the burrowing capabilities of different shell morphologies. Models for 3D printing have also been created based on metrics from vertebrate fossil specimens. For example, Muscutt et al. (2017) used profile and planform geometries of plesiosaur flippers to generate and print rigid plastic flippers. They then used these flippers for hydrodynamic tests to study the efficiency and effectiveness of propulsion using these shapes (Figure 2C). Additionally, it can be useful to combine multiple model creation methods. For example, White et al. (2017) used CT data to create a model Theropod foot in Rhinoceros 5.0 (Figure 2D). They 3D printed this foot to create a mold that was later filled with silicon to test its footprint in a simulated paleo-sediment. 3D modeling programs can also be used to modify shapes or add taphonomically-lost features.
Garcia et al. (2018) combined surface scanning and 3D program editing to replace missing brachiopod spines, which are fragile and often not preserved, and study stability and scour (Figure 2B). The final printed brachiopod was created by mirroring the valve that was well enough preserved for use. While neontological studies are have different constraints, we highly recommend exploring this literature for applications relevant to the fossil record (e.g., Mehrabani et al., 2014; Wen et al., 2014; Porter et al., 2015; Walker and Humphries, 2019).
Material Selection
Once a model is in a 3D printable format, a printing material must be chosen. There is an ever-growing variety of materials available for 3D printing including plastics, steel, aluminum, sandstone, thermoplastic polyurethane, photopolymer resin, and composite powders (see Shapeways4 and Bluedge5). The methods used to create prints using these different materials are variable (e.g., Fused Deposition Modeling (FDM), Polyjet Technology, and Binder Jetting, Selective Laser Sintering (SLS), and Selective Laser Melting) (Bluedge5 and Shapeways4, see Walker and Humphries, 2019) as are their resolutions and capabilities. Many different materials have been used in previous paleontological and biological studies, primarily plastics (Huynh et al., 2013; Germann et al., 2014; Mehrabani et al., 2014; Porter et al., 2015; Muscutt et al., 2017; Pearson, 2017; Anderson et al., 2018; Garcia et al., 2018; Voegele et al., 2018; Dievert et al., 2019), powders (Schilling et al., 2013; Crofts and Summers, 2014; Ishida and Kishimoto, 2015; Kolmann et al., 2015; Johnson et al., 2018), and resins (Jonsson et al., 2017; DiMarco et al., 2018). The cost of printers and materials varies widely. Printers themselves can vary significantly in cost [e.g., as of June 2019 printers from two prominent companies ranged from $1,299.00 to 6,499.00 (MakerBot) and $3,500 to 9,999.00 (Formlabs)]. Some printers also require additional post-processing equipment (e.g., Formlabs). Materials that can be used for inhouse printers also vary widely in cost (as of June 2019 a small spool of material for MakerBot was $16 while an XXL spool was $225 and FormLabs materials ranged from $149.00 to $399.00 per liter) (see Walker and Humphries, 2019 for additional review of materials and costs). The cost of printing with an external company often varies with the material and size of the print. It can be useful to get an estimate early in the process to approximate final costs.
Just as model creation is critical to accurately representing morphology, the properties of the chosen printing material will impact the fidelity and applicability of the study. The material selected will determine important limitations for the model and the necessary pre-processing before printing. For instance, if one seeks to create a hollow model from power or resin, often a built-in hole is required to release excess material which otherwise will become trapped inside. Added holes in biological models may have little to no effect on kinematic studies but an appreciable influence on kinetic studies (e.g., holes behave as stress concentrators in compression). Print thickness and precision is also tightly linked to the printing material. For example, we have found differences in the ability to print thin shell walls with rigid resins (successful print) and other resins (e.g., holes, wall collapse, failure to complete print). Here we discuss some common applications of materials for paleontological studies of functional morphology.
Powder has been demonstrated to be a useful material for tests of shape and strength for brittle biological morphologies. Crofts and Summers (2014), Kolmann et al. (2015), and Johnson et al. (2018) used composite powder to print gastropod shells and retain their brittle nature. In each study, the prints were used to isolate different morphologies involved in the interactions of shell-crushing predators and their prey. Crofts and Summers (2014) used 3D printed replicas of CT scanned gastropods to test the efficacy of different predator dentitions and found that idealized crushing morphologies contain biological tradeoffs that make them unlikely to occur in nature (Figure 2E). Kolmann et al. (2015) instead used the same shell prints to test relationships between crushing ability and stingray jaw morphology and found that jaw morphology was not predictive of performance. Rather than using scans, Johnson et al. (2018) created mathematically idealized 3D printed gastropods to test relationships between shell shape and strength to resist crushing by a predator. Powder composite prints were critical to all these experiments to realistically isolate the influence of geometry on systems involving brittle prey while negating the effects of microstructure. However, powder prints are not the optimal choice for all experiments.
Plastics have been a popular choice to study functional morphology in hydrodynamic studies (Huynh et al., 2013; Muscutt et al., 2017; Pearson, 2017; Anderson et al., 2018; Garcia et al., 2018; Peterman and Ciampaglio, 2018; Dievert et al., 2019). This is likely because of their comparatively low cost and easy accessibility compared to other waterproof materials. Anderson et al. (2018) used plastic prints of turritelline gastropods to study the influence of shell ornamentation on fluid flow on partially buried snails. Dievert et al. (2019) tested the influence of shape and orientation on brachiopod feeding; using a translucent plastic to visualize fluid flow within the valves (Figure 2F). Dievert et al. (2019) also printed dissolvable supports for the delicate brachidia inside their shells. Plastics were the most viable option for these tests, which required a rigid shell but not a brittle material.
Pre-processing
Once materials have been chosen, the digital model must be prepared to be printed according to the requirements of the printer. While pre-processing requires some knowledge of the best practice for specific printers and material, there are commonly shared challenges including solidifying, repairing holes/instabilities, choosing a possible printing orientation, and creating sufficient supports.
In this phase, meshes may be refined and smoothed to preserve shape and reduce complexity. Solidifying and repairing holes can reduce printing errors in specimens which may be taphonomically incomplete. Printing files can also be made water-tight in select printing programs; while this method may increase the amount of material needed and overall printing time, we have found it may decrease printer error by reducing the need for complex supports.
The optimal printing orientations can typically be determined using printer-specific software; however, some manual manipulation may be necessary for complex prints requiring specific supports. For example, some printing programs, like Preform and Netfabb, allow the user to change the density, location, and size of supports for ease of removal during post-processing. Depending on the material chosen and the desired morphology, hollow prints can contain both internal and external supports. When appropriate, making a model hollow can also reduce printing costs and time.
Once mesh repairs and supports are complete, the model must be globally scaled to an appropriate size for the printing bed. In some cases, if the desired size is larger than the bed, the investigator may be tasked with printing a model in multiple parts which can later be combined (e.g., White et al., 2017). Beyond the size limitations of the printing bed, experiments may require models to be a specific size to be meaningful for the test being conducted. For example, Huynh et al. (2013) scaled their models of spiraculate blastoid hydrospires to 72 times the original size to conduct fluid tests on prints made of a translucent ABS polymer (Figure 2G). While Huynh et al. (2013) had to scale their morphology to create an observable experiment, Garcia et al. (2018) had to scale brachiopods by a factor of 1.5 to reach maximum printer resolution. There are also biological reasons for scaling in the pre-processing phase. Johnson et al. (2018) scaled various shell shapes to be the same height in one dimension to make informed comparisons about defenses against crushing predation. Since shell crushing predators are limited by gape-size, this scaling was critical to their experimental design (Wainwright, 1987).
Post-processing
Post-processing can be used to clean the model and change the material properties of the final print. Common post-processing techniques for cleaning the model include sanding down elements and support removal to increase model fidelity. To obtain relevant material properties, different techniques can be necessary. The duration and combination of alcohol washes, photo-curing, and baking change fundamental properties (e.g., tensile, flexural, and impact strength, and heat deflection temperature) of the final print. Generally, information about changes in material properties with post-processing treatments is found on the manufacture's website. Investigators may also seek additional post-processing beyond factory recommendations for experimental models. For example, print weight has been an important consideration in previous studies. Garcia et al. (2018) added iron shavings to make their printed brachiopods the density of calcium carbonate before subjecting them to tests underwater. Similarly, to compare results of virtual hydrodynamics models of orthoconic cephalopods to physical models Peterman and Ciampaglio (2018) distributed mass appropriately during post-processing to make the prints neutrally buoyant. Post-processing is a critical final step to maintain the desired qualities of the final model, and therefore, cannot be overlooked.
Discussion and Conclusions
Geologic constraints obscure the wealth of information that lies in the fossil record. However, 3D printing has vastly expanded the possibilities for experimental tests on the functional morphology of fossilized taxa. New innovations in the properties of printed materials, methods of printing, and advances in bioinspired materials (Gbureck et al., 2007; Dorozhkin, 2010; Dimas et al., 2013; Murphy and Atala, 2014; Chia and Wu, 2015) hold promise for increasing the accuracy and precision of paleontological studies (see Walker and Humphries, 2019 for review). With increasing, accessibility to 3D-printing paleontologists can now investigate extinct taxa as if they were extant, conduct tests on hypothetical morphologies, and validate virtual experiments. Moving forward novel 3D printing techniques will allow us to re-examine existing hypotheses and develop new hypotheses to understand form-function relationships that were previously inaccessible.
Author Contributions
EJ collected primary sources. EJ and AC created workflow and wrote the paper.
Conflict of Interest
The authors declare that the research was conducted in the absence of any commercial or financial relationships that could be construed as a potential conflict of interest.
Acknowledgments
We would like to thank Peter Dodson, our reviewers: TV and RH, and our editor: MS, for helpful comments on this manuscript. We also thank Hermann Pfefferkorn for his support in our research program and Brendan Anderson for helpful conversations. Our thanks to Annelise Leonhart and David Vann for technical support on our 3D projects. This project was supported by internal funding through the Greg and Susan J. Walker Foundation and the Summer Research Stipend in Paleontology (Department of Earth and Environmental Science at the University of Pennsylvania). We also thank the Delaware Valley Paleontological Society for support through the Paul Bond Scholarship fund. This research was in part supported by funding to EJ through the NSF GRFP.
Footnotes
1. ^Meshmixer (Latest Update April 2018: v. 3.5) http://www.meshmixer.com
2. ^Blender (Latest Update July 2019: v. 2.80) https://www.blender.org
3. ^Fusion-360 (Latest Update September 2019: v. 2.0.6503) https://www.autodesk.com/products/fusion-360/overview#banner).
References
Anderson, B. M., Miller, J., and Allmon, W. D. (2018). “When theoretical morphology gets real: 3-D printing of idealized turritellid gastropod shells to better understand the function of sculpture and whorl shape, in Conference Annual Meeting (Indianapolis, IN: Geological Society of America). doi: 10.1130/abs/2018AM-319161
Balanoff, A., and Rowe, T. B. (2002). Osteological description of an elephant bird embryo using computed tomography and rapid prototyping, with a discussion of growth rates in Aepyornis. J. Vertebr. Paleonto. 27, 1–53. doi: 10.1671/0272-4634(2007)27[1:ODOAES]2.0.CO;2
Bristowe, A., Parrott, A., Hack, J., Pencharz, M., and Raath, M. A. (2004). A nondestructive investigation of the skull of the small theropod dinosaur, Coelophysis rhodesiensis, using CT scans and rapid prototyping. Palaeontol. Afr. 40, 159–163.
Chia, H. N., and Wu, B. M. (2015). Recent advances in 3D printing of biomaterials. J. Biol. Eng. 9:4. doi: 10.1186/s13036-015-0001-4
Clark, T. (2018). “The varying dentition of Allosaurus: a functional morphology experiment,” in GSA Annual Meeting (Indianapolis, IN: Geological Society of America). doi: 10.1130/abs/2018AM-318484
Crofts, S. B., and Summers, A. P. (2014). How to best smash a snail: the effect of tooth shape on crushing load. J. R. Soc. Interface 11:20131053. doi: 10.1098/rsif.2013.1053
Cunningham, J. A., Rahman, I. A., Lautenschlager, S., Rayfield, E. J., and Donoghue, P. C. (2014). A virtual world of paleontology. Trends Ecol. Evol. 29, 347–357. doi: 10.1016/j.tree.2014.04.004
Das, A. J., Murmann, D. C., Cohrn, K., and Raskar, R. (2017). A method for rapid 3D scanning and replication of large paleontological specimens. PLoS ONE 12:e0179264. doi: 10.1371/journal.pone.0179264
Dievert, R. V., Barclay, K. M., Molinaro, D. J., and Leighton, L. R. (2019). Evaluating the effects of morphology and orientation on feeding in atrypide brachiopods using 3-D printed models. Palaeogeogr. Palaeoclimatol. Palaeoecol. 527, 77–86. doi: 10.1016/j.palaeo.2019.04.020
DiMarco, B., Johnson, E. H., Carter, A. M., Sime, J. A., and Sallan, L. (2018). “Exploring the function of suture complexity with experimental compression of 3D printed ammonoids,” in GSA Annual Meeting (Indianapolis, IN: Geological Society of America). doi: 10.1130/abs/2018AM-321099
Dimas, L. S., Bratzel, G. H., Eylon, I., and Buehler, M. J. (2013). Tough composites inspired by mineralized natural materials: computation, 3D printing, and testing. Adv. Funct. Mater. 23, 4629–4638. doi: 10.1002/adfm.201300215
Dorozhkin, S. V. (2010). Bioceramics of calcium orthophosphates. Biomaterials 31, 1465–1485. doi: 10.1016/j.biomaterials.2009.11.050
Fiorenza, L., Yong, R., Ranjitkar, S., Hughes, T., Quayle, M., McMenamin, P. G., et al. (2018). The use of 3D printing in dental anthropology collections. Am. J. Phys. Anthropol. 167, 400–406. doi: 10.1002/ajpa.23640
Garcia, E. A., Molinaro, D. J., and Leighton, L. R. (2018). Testing the function of productide brachiopod spines on arenaceous substrates using 3D printed models. Palaeogeogr. Palaeoclimatol. Palaeoecol. 511, 541–549. doi: 10.1016/j.palaeo.2018.09.020
Gbureck, U., Hölzel, T., Klammert, U., Würzler, K., Müller, F. A., and Barralet, J. E. (2007). Resorbable dicalcium phosphate bone substitutes prepared by 3D powder printing. Adv. Funct. Mater. 17, 3940–3945. doi: 10.1002/adfm.200700019
Germann, D. P., Schatz, W., and Hotz, P. E. (2014). Artificially evolved functional shell morphology of burrowing bivalves. Palaeontol Electron. 17, 1–25. doi: 10.26879/394
Grant, C., Hastings, A., and Ziegler, M. J. (2018). “iDigFossils: engaging K−12 students in integrated STEM using 3D models of triassic dinosaur foot prints from culpepper,” in GSA Annual Meeting (Indianapolis, IN: Geological Society of America). doi: 10.1130/abs/2018AM-317698
Grant, C. A., MacFadden, B. J., Antonenko, P., and Perez, V. J. (2016). 3-D fossils for K−12 education: a case example using the giant extinct shark Carcharocles megalodon. Paleontol. Soc. Papers 22, 197–209. doi: 10.1017/scs.2017.15
Hasiuk, F. J. (2014). Making things geological: 3-D printing in the geosciences. GSA Today 24:28. doi: 10.1130/GSATG211GW.1
Huynh, T. L., Evangelista, D., and Marshall, C. R. (2013). Visualizing the fluid flow through the complex skeletonized respiratory structures of a blastoid echinoderm. Palaeontol. Electron. 18, 1–17. doi: 10.26879/492
Igic, B., Nunez, V., Voss, H. U., Croston, R., Aidala, Z., López, A. V., et al. (2015). Using 3D printed eggs to examine the egg-rejection behaviour of wild birds. PeerJ. 3:e965. doi: 10.7717/peerj.965
Ishida, N., and Kishimoto, N. (2015). Three-dimensional imaging of the Jurassic radiolarian Protunuma ochiensis Matsuoka: an experimental study using high-resolution X-ray micro-computed tomography. Volumina Jurassica 13, 77–82. doi: 10.5604/17313708
Johnson, E. H., Allmon, W. D., Jerolmack, D. J., Sipzner, D., and Sallan, L. (2018). “3D printing reveals strengths and weaknesses of prey shape during the mesozoic marine revolution,” in GSA Annual Meeting (Indianapolis, IN: Geological Society of America). doi: 10.1130/abs/2018AM-323716
Jonsson, T., Chivers, B. D., Brown, K. R., Sarria-S, F. A., Walker, M., and Montealegre-Z, F. (2017). Chamber music: an unusual Helmholtz resonator for song amplification in a Neotropical bush-cricket (Orthoptera, Tettigoniidae). J. Exp. Biol. 220, 2900–2907. doi: 10.1242/jeb.160234
Kolmann, M. A., Crofts, S. B., Dean, M. N., Summers, A. P., and Lovejoy, N. R. (2015). Morphology does not predict performance: jaw curvature and prey crushing in durophagous stingrays. J. Exp. Biol. 218, 3941–3949. doi: 10.1242/jeb.127340
Lak, M., Néraudeau, D., Nel, A., Cloetens, P., Perrichot, V., and Tafforeau, P. (2008). Phase contrast X-ray synchrotron imaging: opening access to fossil inclusions in opaque amber. Microsc. Microanal. 14, 251–259. doi: 10.1017/S1431927608080264
Mehrabani, H., Ray, N., Tse, K., and Evangelista, D. (2014). Bio-inspired design of ice-retardant devices based on benthic marine invertebrates: the effect of surface texture. PeerJ. 2:e588. doi: 10.7717/peerj.588
Mitsopoulou, V., Michailidis, D., Theodorou, E., Isidorou, S., Roussiakis, S., Vasilopoulos, T., et al. (2015). Digitizing, modelling and 3D printing of skeletal digital models of Palaeoloxodon tiliensis (Tilos, Dodecanese, Greece). Quat. Int. 379, 4–13. doi: 10.1016/j.quaint.2015.06.068
Morse, A., Dattilo, B., Dewing, K., and Hagadorn, J. W. (2018). “Mind the gape: the solution to the life habits of Rafinesquina alternata may turn on a 3D-printed hinge,” in GSA Annual Meeting (Indianapolis, IN: Geological Society of America). doi: 10.1130/abs/2018AM-323792
Murphy, S. V., and Atala, A. (2014). 3D bioprinting of tissues and organs. Nat. Biotechnol. 32:773. doi: 10.1038/nbt.2958
Muscutt, L. E., Dyke, G., Weymouth, G. D., Naish, D., Palmer, C., and Ganapathisubramani, B. (2017). The four-flipper swimming method of plesiosaurs enabled efficient and effective locomotion. Proc. R. Soc. B Biol. Sci. 284:20170951. doi: 10.1098/rspb.2017.0951
Pearson, K. (2017). Experimental biomechanics of trinucleid fringe pits (Trilobita) (Doctoral dissertation), Oberlin College.
Peterman, D., and Ciampaglio, C. N. (2018). “How stable were orthoconic cephalopods? Hydrodynamic analyses of restoring moments from neutrally buoyant, 3D printed models of ectocochleate cephalopods,” in GSA Annual Meeting (Indianapolis, IN: Geological Society of America). doi: 10.1130/abs/2018AM-317321
Porter, M. M., Adriaens, D., Hatton, R. L., Meyers, M. A., and McKittrick, J. (2015). Why the seahorse tail is square. Science 349:aaa6683. doi: 10.1126/science.aaa6683
Rahman, I. A., Adcock, K., and Garwood, R. J. (2012). Virtual fossils: a new resource for science communication in paleontology. Evol. Educ. Outreach 5, 635–641. doi: 10.1007/s12052-012-0458-2
Raup, D. M. (1966). Geometric analysis of shell coiling: general problems. J. Paleontol. 40, 1178–1190.
Raup, D. M., and Michelson, A. (1965). Theoretical morphology of the coiled shell. Science 147, 1294–1295. doi: 10.1126/science.147.3663.1294
Rivera, M. J., and Sumner, D. Y. (2014). Unraveling the three-dimensional morphology of Archean microbialites. J. Paleontol. 88, 719–726. doi: 10.1666/13-084
Schemm-Gregory, M. (2014). A new Givetian athyridid species from northwest Africa discovered by three-dimensional reconstruction of shell morphology of internal molds. J. Paleontol. 88, 708–718. doi: 10.1666/13-086
Schilling, R., Jastram, B., Wings, O., Schwarz-Wings, D., and Issever, A. S. (2013). Reviving the dinosaur: virtual reconstruction and three-dimensional printing of a dinosaur vertebra. Radiology 270, 864–871. doi: 10.1148/radiol.13130666
Sutton, M., Rahman, I., and Garwood, R. (2014). Techniques for Virtual Palaeontology. West Sussex: John Wiley & Sons. doi: 10.1002/9781118591192
Teshima, Y., Matsuoka, A., Fujiyoshi, M., Ikegami, Y., Kaneko, T., Oouchi, S., et al. (2010). “Enlarged skeleton models of plankton for tactile teaching.” in International Conference on Computers for Handicapped Persons (Berlin; Heidelberg: Springer), 523–526. doi: 10.1007/978-3-642-14100-3_78
Vernon, R. O. (1957). New technique for casting fossils and forming molds. J. Paleontol. 31, 461–463.
Voegele, K. K., McDevitt, D. G., Tangorra, J., and Lacovara, K. J. (2018). “Comparison of digital and 3D printed robotic models of the elbow of the sauropod dinosaur Dreadnoughtus schrani,” in GSA Annual Meeting (Indianapolis, IN: Geological Society of America). doi: 10.1130/abs/2018AM-321567
Wainwright, P. C. (1987). Biomechanical limits to ecological performance: mollusc-crushing by the Caribbean hogfish, Lachnolaimus maximus (Labridae). J. Zool. 213, 283–297. doi: 10.1111/j.1469-7998.1987.tb03704.x
Walker, M., and Humphries, S. (2019). 3D Printing: applications in evolution and ecology. Ecol. Evol. 9, 4289–4301. doi: 10.1002/ece3.5050
Waters, B. T., and Savage, D. E. (1971). Making duplicates of small vertebrate fossils for teaching and for re-search collections. Curator. 14, 123–132. doi: 10.1111/j.2151-6952.1971.tb00428.x
Weber, G. W. (2001). Virtual anthropology (VA): a call for glasnost in paleoanthropology. Anat Rec. 265, 193–201. doi: 10.1002/ar.1153
Wen, L., Weaver, J. C., and Lauder, G. V. (2014). Biomimetic shark skin: design, fabrication and hydrodynamic function. J. Exp. Biol. 217, 1656–1666. doi: 10.1242/jeb.097097
Keywords: 3D printing, functional morphology, paleontology, modeling, methods, evolution
Citation: Johnson EH and Carter AM (2019) Defossilization: A Review of 3D Printing in Experimental Paleontology. Front. Ecol. Evol. 7:430. doi: 10.3389/fevo.2019.00430
Received: 06 August 2019; Accepted: 23 October 2019;
Published: 08 November 2019.
Edited by:
Mary Teresa Silcox, University of Toronto Scarborough, CanadaReviewed by:
Tamas Bence Viola, University of Toronto, CanadaRobert Hoppa, University of Manitoba, Canada
Copyright © 2019 Johnson and Carter. This is an open-access article distributed under the terms of the Creative Commons Attribution License (CC BY). The use, distribution or reproduction in other forums is permitted, provided the original author(s) and the copyright owner(s) are credited and that the original publication in this journal is cited, in accordance with accepted academic practice. No use, distribution or reproduction is permitted which does not comply with these terms.
*Correspondence: Erynn H. Johnson, ZXJ5bm5qQHNhcy51cGVubi5lZHU=
†These authors have contributed equally to this work