- 1Laboratory for Chemical Technology, Department of Materials, Textiles and Chemical Engineering, Ghent University, Ghent, Belgium
- 2Dow Benelux BV, PSPH R&D, Terneuzen, Netherlands
The discovery and development of efficient technologies that enable the use of CO2 as a starting material for chemical synthesis (at scale) is probably one of the biggest scientific challenges of our time. But a key question is if the cure will not be worse than the disease? In this work, the economic feasibility of the electrochemical reduction of CO2 to ethylene is assessed and it is demonstrated that from a Capital expenditure and Operational expenditure point of view the electrochemical production of ethylene from CO2 is not feasible under the current market conditions. Even in the case that the renewable electricity price would be zero, the feasibility is hampered by the state-of-the-art catalyst performance (selectivity) and the cost of the electrochemical reactor. Turning the installation on and off, if this would be even practically possible, is not interesting because our study shows that because of the high Capital expenditure, the payback time of the process would become unacceptably high. Finally, because of the high electricity requirement, this Carbon Capture and Utilization process has a lower CO2 avoidance potential than the substitution of gray electricity by green electricity. This means that today the available green electricity would best be used to close coal and gas based power plants instead of powering the electrochemical conversion of CO2 to ethylene.
Introduction
Climate change, of which greenhouse gas emission is the main driver, is one of the most urgent challenges humanity is currently facing. As depicted in Figure 1, the atmospheric CO2 concentration has been rising rapidly since the start of the measurements in March 1958, with an average increase of approximately 2 ppm per year over the past decade (Tans, 2019). In 2016, the atmospheric CO2 concentration stayed above the symbolic 400 ppm mark all year round for the first time, corresponding to a 30% increase compared to the pre-industrial (before circa 1750) levels of 270 ppm (Betts et al., 2016). The Paris Agreement under the United Nations Framework Convention on Climate Change adopted in 2015 illustrates the worldwide commitment to reduce greenhouse gas emissions to mitigate global warming, but this will require an order-of-magnitude increase in public and private investments in research and development between 2019 and 2030 (Rockström et al., 2017).
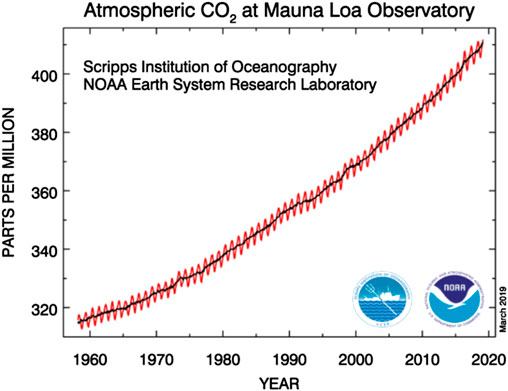
FIGURE 1. Concentrations of CO2 in the atmosphere measured at Mauna Loa Observatory (Hawaii) since the beginning of the measurements in March 1958 (316 ppm) (Tans, 2019).
Strategies to reduce CO2 emissions can be divided in four categories that focus on either avoidance of CO2 emissions or binding the emitted CO2 in a natural or non-natural sink. The first category is improving energy efficiency, which currently provides the greatest return on investment and has already been successfully applied in many industrial contexts. Although this approach still has potential, annual improvements of 1–2% will not be sufficient to meet the climate targets. The second category, using non- or low-carbon energy sources, (e.g., solar, wind, geothermal), is at large scale still challenging due to the fluctuating nature of the energy supply and the slow rate at which the electricity production is becoming more renewable. Carbon Capture and Sequestration (CCS), i.e., a series of technologies combining CO2 capture from large point sources such as power plants, transportation to a storage site, and sequestration into a (natural) sink, is the third category, but its potential is currently rather limited due to technical and economic hurdles (Spigarelli and Kawatra, 2013; Leung et al., 2014). The fourth category is Carbon Capture and Utilization (CCU), in which CO2 is converted to (high-value) products. This category can be considered as a special case of the third category with the utilization part acting as a non-natural sink (Whipple and Kenis, 2010; Kuhl et al., 2014; Schouten et al., 2014).
CO2 is a thermodynamically very stable molecule and thus a substantial input of energy combined with effective reaction conditions and active catalysts are required for its conversion, c.f. Figure 2. To obtain the desired overall negative CO2 balance, the energy required for its conversion should originate from non- or low carbon energy sources. Hence, the development of CO2 conversion processes has focused on minimizing the required energy input by using the non or low-carbon energy sources in the most efficient way possible. According to a recent study (Voltachem, 2016), the development of new products through the application of innovative technologies powered by renewable energy is one of the main drivers for “electrification” of the chemical industry, i.e., replacing thermal and chemical energy by electrical energy. Other main drivers are economic benefits and improved sustainability through the reduction of feedstocks, by-products, waste, energy use, solvents, and CO2.
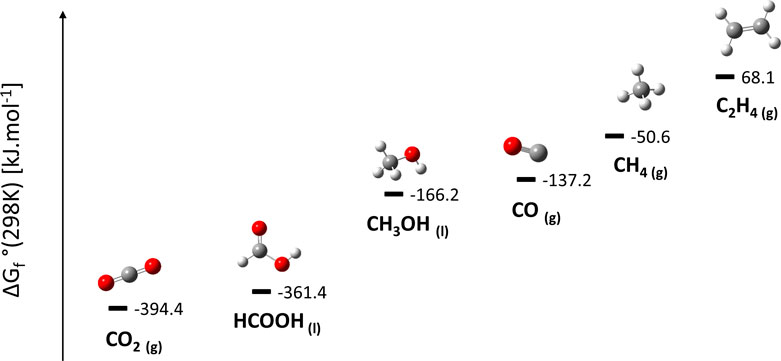
FIGURE 2. Standard Gibbs free energy of formation (at 298 K), expressed in kJ mol−1, of CO2 and possible reduction products.
Among all the proposed methods for converting CO2, which have as common advantage the ease of integration of non- or low carbon energy sources, electrochemical methods are considered to be the most promising (Endrődi et al., 2017), as several advantages have been claimed compared to the other methods: 1) they can be conducted at ambient conditions (allowing for rapid changes in the production rate as the availability of the renewable energy changes), 2) by a careful selection of the electrocatalyst, electrolyte and operating conditions, it is possible to drive the electrochemical conversion of CO2 toward the desired products, 3) the chemical consumption can be minimized by recycling the electrolytes, 4) the reaction systems are compact, modular and hence scale-up is relatively straightforward, and 5) the electrons are directly used for product formation. However, there are clear challenges for electrification, such as the overall high cost of electricity, the large investment costs, the often poor selectivities and low conversions related to low reaction rates (resulting in large reactor volumes needed for a world-scale plant), the technical and economic feasibility of turning plants on and off safely on short notice, etc. This implies that there is a lot of skepticism whether electrification of the chemical industry is actually feasible (Van Geem et al., 2019; Gani et al., 2020) or whether it is another hype like the numerous ones that have been presented in the last two decades (Banholzer, 2012; Banholzer and Jones, 2013).
The goal of this study is to explore whether the electrochemical conversion of CO2 can be a viable alternative production route of ethylene, which is the key building block of the chemical industry and representative for products with a reasonably high added value. First, a short overview is given of the CO2 reduction process and the performance trends with the focus on ethylene formation. Next, a techno-economic model is developed for a CO2 conversion plant integrated with CO2 capture from a blast-furnace flue gas stream. With this model, the economic competitiveness of this alternative ethylene production route is compared against the current state of the art for ethylene production, i.e., naphtha-based steam cracking, under both current and future conditions. Finally, the CO2 avoidance potential of the process is assessed based on a Life Cycle Analysis, adopting a cradle-to-gate boundary.
Methodology
Electrochemical Conversion of CO2
The electrochemical reduction of CO2 is a complex conversion consisting of multiple elementary proton-electron reactions leading to the (co-)formation of various products of which ethylene has the highest commercial value. As depicted in Figure 3, CO2 is converted at the negatively charged cathode to primarily CO, methane, ethylene and formic acid, while H2O is oxidized into O2 at the anode. The half-cell reactions for the electrochemical reduction of CO2 and the corresponding formal reduction potential are summarized in Table 1 (Bard et al., 1985). For all possible reduction products, the reaction proceeds via CO as intermediate species (Hori, 2008). In aqueous environment, the hydrogen evolution reaction competes with the reduction of CO2. Aside from the employed electrocatalyst and electrode potential, the product distribution obtained from the electrochemical reduction of CO2 depends on the choice of electrolyte, the electrolyte concentration, the concentration of dissolved CO2 and the reaction conditions, i.e., pressure and temperature.
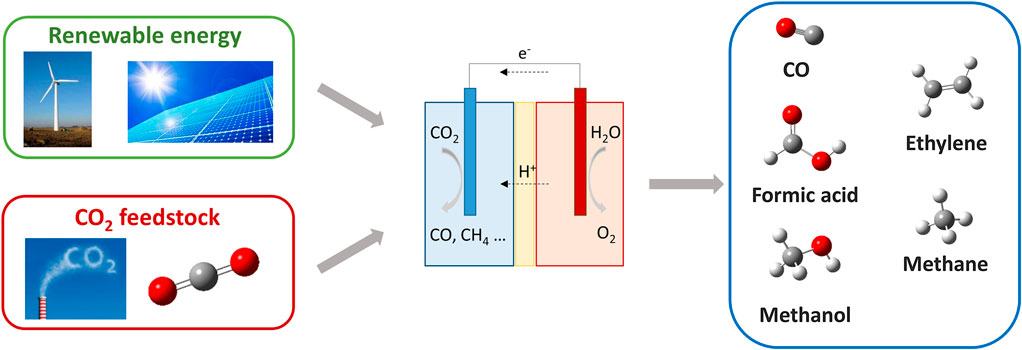
FIGURE 3. Schematic representation of the production of high-value chemicals by the electrochemical reduction of CO2 making use of renewable energy sources.
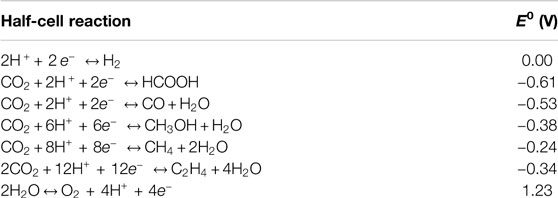
TABLE 1. Half-cell reactions and the corresponding formal redox potential E0 (V) for the electrochemical reduction of CO2. All potentials are referenced against the standard hydrogen electrode (Bard et al., 1985).
To evaluate the technological performance of this electrochemical process and enable a meaningful comparison between different electrocatalysts, several figures of merit are commonly used (Pander III et al., 2017). Because the reduction of CO2 has to overcome a kinetic energy barrier, the cell potential at which the redox reaction is experimentally observed (E), is higher than the reversible cell potential (E0) and the difference between the two is denoted as the overpotential
Minimizing the overpotential of the desired electrochemical reaction minimizes the required energy input. The Faradaic efficiency
With
In general terms, the lower the overpotential and the higher the Faradaic efficiency, the higher the energy efficiency of the process. Finally, the current density
Process Conditions and Selectivity
To enable a feasible large-scale implementation of an electrochemical CO2 reduction process, the development of an active, selective, stable, and relatively low-cost electrocatalyst is a prerequisite. Over the last few years, many researchers focused on the exploration of different electrocatalysts with the aim of addressing the key challenges of this electrochemical process (Hori et al., 1985; Hara et al., 1997; Hori, 2008; Rakowski Dubois and Dubois, 2009; Peterson and Nørskov, 2012; Schneider et al., 2012; Qiao et al., 2014; Kortlever et al., 2015; Mao and Hatton, 2015; Engelbrecht et al., 2016; Kortlever et al., 2016; Wu et al., 2016; Tao et al., 2017): 1) reduce the overpotential (or increase energy efficiency), 2) increase the selectivity (or Faradaic efficiency), 3) increase current density, and 4) expand catalyst lifetime (less than 100 h) with order of magnitude. While new studies reporting improved Faradaic efficiencies and lower overpotentials are consistently being published, the important question remains what the performance of the reduction process should be to enable implementation of a feasible large-scale industrial process. As a rule of thumb, industrial reactors are typically operated at geometric current densities above 100 mA cm−2 with at least 50% Faradaic efficiency for the required products, in order to minimize investment costs as much as possible (Oloman and Li, 2008). In Figure 4, an overview is given of the electrochemical performances for CO2 reduction to ethylene from a selection of studies reported in the open literature published in the period from 1986 to 2017. The overpotential, which determines the energy efficiency of the process, ranges from −0.8 to −2.4 V. While significant progress has been made over the last few years, the performance of state-of-the art technologies seems to be currently not yet at the level required for an economically viable large-scale process, indicated by the green zone and applying the rule of thumb specified above.
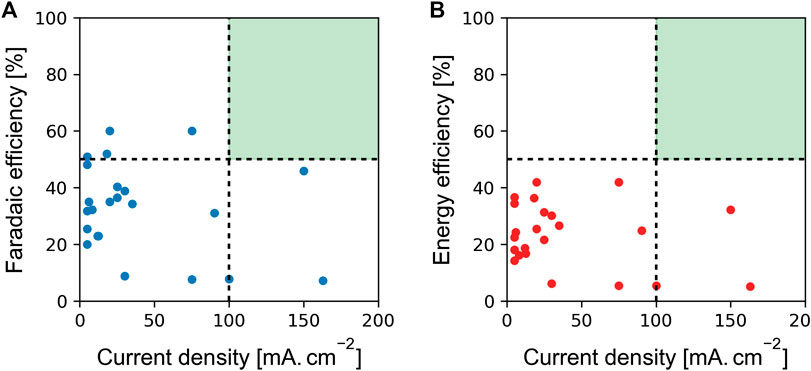
FIGURE 4. Summary of the electrochemical performance of CO2 reduction to ethylene from a selection of studies reported in the open literature published in the period from 1986 to 2019: Faradaic efficiencies (A) and energy efficiencies (B) as a function of current density (mA cm−2) (Hori et al., 1985; Kaneco et al., 1999; Ogura et al., 2004; Hori, 2008; Engelbrecht et al., 2016; Ma et al., 2016; Mistry et al., 2016; Wu et al., 2016; Ke et al., 2017; Peng et al., 2017; Gao et al., 2019).
Aside from activity and selectivity issues, rapid deactivation of the catalysts, which leads to a shift in the product distribution favoring the hydrogen evolution reaction, is also one of the main challenges. In most cases, the catalyst lifetime is under 100 h (Qiao et al., 2014). The factors influencing the catalyst lifetime have so far not been analyzed in detail, also because most experiments are performed in a limited time span focusing on improving the initial catalyst performance. Although the exact cause for catalyst deactivation is not always clear, several hypotheses have been suggested, including electrolyte trace impurity deposition, accumulation of adsorbed or insoluble reaction by-products and morphological changes of the catalyst. A lifetime in the order of magnitude of thousands of hours is required for a viable large-scale process. Otherwise, frequent regeneration of the electrodes should be foreseen in the process (Dominguez-Ramos et al., 2015; Martin et al., 2015).
It is clear that several technological breakthroughs are needed before the electrochemical reduction of CO2 can become industrially feasible. A roadmap for the electrochemical reduction of CO2 has recently been developed within EU’s Energy program, proposing both short-term and long-term practical goals (Koper and Roldan, 2019). In the next 5 years, significant progress should be made on the development of CO2 electrocatalysts and electrolyzers, operating at relevant current densities (>100 mA cm−2), with high Faradaic efficiency for high-value products such as ethylene, at lower overpotential (2.0–2.2 V), and good stability (>100 h). In the long term, the integration with downstream operations as well as integration with upstream CO2 capture should be considered.
Conceptual Process Design
In Figure 5, a conceptual process scheme for the electrocatalytic conversion of CO2 is depicted. The first step of the process is the capture of CO2 from the flue gas stream and transport to the conversion unit. The CO2 source for this study is considered to be blast furnace gas, which contains ∼22 mol% CO, ∼22 mol% CO2, ∼5 mol% H2, and ∼51 mol% N2. The CO2 is captured via chemical absorption with monoethanolamine (MEA) as solvent. The blast furnace technology will continue to dominate steel production in the coming decade and the only way to substantially reduce the associated CO2 emissions is to combine it with CCS or CCU options. In an absorber column the CO2-containing gas stream is contacted with a solvent, after which it is desorbed again from the solvent in a stripper column. As MEA can undergo degradation and is also lost via the gasses that are vented into the atmosphere, a make-up of this chemical is required. Chemical absorption with MEA results in a high CO2 purity product stream (>98 wt%), with H2O as the main impurity, while traces of N2 and MEA can also be present (Li et al., 2016). Gaseous impurities can have an effect on the electrolysis process in different ways, i.e., they can act as 1) as diluents (e.g., N2), 2) as reducible species (e.g., O2), and 3) as catalyst poisoning species (e.g., NO2, SO2, H2S, organic gases) (Zhai et al., 2019). To enable industrial application, the influence of gaseous impurities on the electrolysis process needs to be better understood to avoid catalyst degradation. The captured CO2 is combined with a possible recycle stream and sent to the reactor in which the electrochemical reduction takes place. At the cathode, CO2 is reduced resulting in the formation of the main products CO, ethylene, methane, hydrogen and formic acid, while at the anode H2O is oxidized into O2. The global reaction for the production of ethylene is:
The product stream that leaves the cathode compartment of the reactor is sent to a flash vessel. The obtained liquid stream contains mainly electrolyte and unconverted CO2 and can be sent back to the reactor. In order to avoid the accumulation of liquid byproducts (i.e., formic acid), part of this stream is purged. The gas stream contains ethylene, unconverted CO2, and significant amounts of other byproducts, such as CO and H2. A gas purification section is required which serves two main goals: separation of the unconverted CO2 for re-use and purification of the desired products (in this case ethylene), and byproducts.
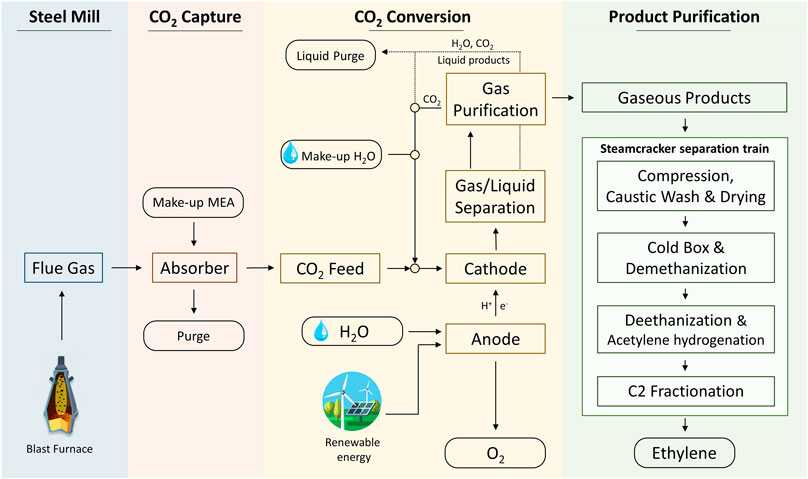
FIGURE 5. Envisioned process scheme for the electrochemical conversion of a CO2-containing flue gas stream to high-value chemicals.
Economic Analysis
To assess the actual economic feasibility of this alternative production route for ethylene, the CAPEX and OPEX have been estimated. A grass-roots plant is considered, built in Northwestern Europe. Cost calculations are thus based on European prices. Cost functions are introduced to estimate the CAPEX and OPEX for the different steps of the electrochemical conversion process, i.e., CO2 capture, CO2 conversion and product separation and purification. Because of the large scale of this industrial process, the feasibility study is done for the replacement of a part of the installed production capacity based on fossil fuels, i.e., steam cracking of naphtha. This means it is assumed that the gaseous product stream, after CO2 removal, is further processed on the separation section of an existing steam cracking facility. No costs have thus been estimated for the product separation and purification steps, except for capturing and recycling of the unconverted CO2. Using estimates from literature data for the specific capital cost and energy requirement, the CAPEX and OPEX are written as a function of four different parameters for the different steps. These parameters, which are related to both the process and to external factors, are: (carbon-based) product selectivity, (single-pass) conversion, CO2 value, and electricity price. All other parameters appearing in the cost functions are rewritten as a function of these four critical parameters.
Capital Expenditure Estimation
The estimated CAPEX for the CO2 capture plant is based on a specific capital cost of 70 €/metric ton CO2/year (Kuramochi et al., 2011). For the installed cost of the electrochemical reactors, a value of 66 million € is reported in literature, for the conversion of 100 metric ton CO2 per day (Oloman and Li, 2008). This value corresponds to 70 electrochemical flow reactors each with 100 cells of 0.5 m2. No economies of scale are taken into account for the electrochemical reduction of CO2, due to the modular character of the electrochemical cells. To improve the overall conversion of the electrochemical process, unconverted CO2 is separated from the gaseous products and recycled back to the reactor. This is done via an additional MEA absorption system, for which the same specific capital cost of 70 €/metric ton CO2/year is taken (Kuramochi et al., 2011). Because the assumption is made that the gaseous product stream, after CO2 removal, is further processed in the separation section of the existing steam cracking facility, no costs are associated to further product separation and purification steps. The maintenance cost is estimated as 2.5% of the CAPEX.
Operational Expenditure Estimation
The main energy contribution for the CO2 capture process is the generation of steam required for the desorption process. This energy is provided making use of natural gas with an efficiency of 85% and a thermal energy price of 8.3 €/GJ (Eurostat (2019)). Mechanical energy required for the pumps and compressors, is assumed to be delivered by electromotors. The thermal and electrical energy requirements for the MEA absorption system are taken from Kuramochi et al. (2011), i.e., 3.2 and 0.50 GJ/metric ton CO2, respectively. The cost of MEA losses is assumed to be 4.6 €/metric ton CO2 (Karl et al., 2011). With respect to the OPEX of the electrochemical reactor, there are two main contributions: the usage of chemicals and the consumption of energy (i.e., electricity). The energy required for the conversion of CO2 is among others determined by the selectivity or equivalently the Faradaic efficiency of the desired reaction, in this case the conversion to ethylene. For a Faradaic efficiency of 60%, approximately 20 MW h per metric ton of converted CO2 is required. The specific energy consumption decreases with a factor two when considering the limiting case of a Faradaic efficiency of 100% (Agarwal et al., 2011). This confirms the importance of technological advancements regarding the energy efficiency of the process to enable large-scale industrial production. With respect to the cost of chemicals, the critical assumption is made that the electrolytes can be fully recycled, which means that the main cost is included in the CAPEX, and in the OPEX only recycling costs need to be taken into account.
Economic Analysis
For the case study, an annual ethylene production of 105 metric ton is considered, which corresponds to approximately 5–20% of a typical ethylene production site based on fossil feedstocks. At 100% conversion and selectivity, the electrocatalytic conversion of CO2 would require 3.14 × 105 metric ton of CO2 per year, which corresponds to about 5–10% of the CO2 emissions of that same ethylene production site. As a base case, the production of polymer-grade ethylene based on a fossil feedstock, i.e., steam cracking of naphtha, is taken, as this is and will remain the predominant process for the production of olefins in the coming decades (Amghizar et al., 2017). For this process, a yield of high-value chemicals (HVC) of 55 wt% is assumed, with an ethylene and propylene yield of, respectively, 30 and 15 wt% (after hydrogenation of acetylene, methyl acetylene and propadiene). The detailed effluent composition obtained from Zimmermann and Walzl (2000) can be found in the Supplementary Material.
The estimated CAPEX and OPEX for the furnace section of a naphtha-based steam cracker located in Europe are equal to respectively 500 and 225 €/metric ton ethylene (Brown, 2019, Personal Communication). This corresponds to an energy requirement of approximately 9 GJ/metric ton HVC or 16 GJ/metric ton ethylene for the furnace section, in agreement with the value reported by Ren et al. (2008). Process upsets, technical issues, and turnarounds, are accounted for via the plant annual uptime, which is equal to 8,440 h per year or 96.3%. An overview of the main techno economic assumptions can be found in the Supplementary Material.
The revenues for the electrochemical process result from the sale of ethylene. Note that high-purity O2 (90–95 wt%) can be considered as a valuable byproduct from the electrolysis process, but is it not taken into account in the product revenues. If possible, O2 will be used in nearby chemical plants to avoid the high-cost transport needs. For the conventional steam cracking process the sale of other important products such as propylene, butadiene and BTX is also considered. The prices determined for March 2018, are summarized in Table 2, i.e., ethylene at 1,050 €/metric ton, propylene at 840 €/metric ton and naphtha at 500 €/metric ton. The gross margin is calculated as the difference between the revenue from the sale of products and the feedstock cost.
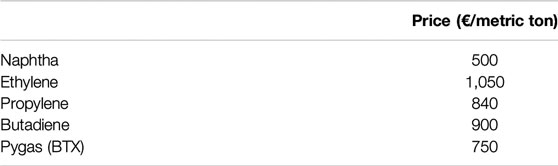
TABLE 2. Applied pricing (March 2018) level for the major materials in this study (ICIS Pricing Database; Platts Global Ethylene Price Index; Platts Global Propylene Price Index).
Five hypothetical cases were considered to assess the economic potential of this alternative ethylene production route compared to the base case, i.e., steam cracking of naphtha. These cases, with different values for the four critical parameters as shown in c.f. Table 3, are:
(1) Reference case: State-of-the-art electrolyzer performance based on Ogura et al. (2004) with a product selectivity of 70% and conversion of 50%, CO2 value of −30 €/metric ton and an industrial electricity price of 35 €/MW h (Haegel et al., 2017).
(2) High selectivity: Selectivity of 100% and conversion of 50%, CO2 value of −30 €/metric ton and an industrial electricity price of 35 €/MW h.
(3) High conversion: Selectivity of 70% and conversion of 100%, CO2 value of −30 €/metric ton and an industrial electricity price of 35 €/MW h.
(4) High CO2 cost: Selectivity of 70% and conversion of 50%, CO2 value of −100 €/metric ton and an industrial electricity price of 35 €/MW h.
(5) Free electricity: Selectivity of 70% and conversion of 50%, CO2 value of −30 €/metric ton and zero cost electricity.

TABLE 3. Values for the three input parameters, i.e., product selectivity (%), conversion (%), CO2 value (€/metric ton) and electricity price (€/MW h) for the five different cases.
Results and Discussion
Economic Evaluation
In Figure 6, the main energy input and material streams considered in the economic analysis are shown. Note that for the reference case, the high CO2 price case and the free electricity case, these values are identical, as the only difference between these three cases is caused by a change in CO2 and electricity price. For a product selectivity of 70%, a larger flow of CO2 is required to obtain the desired ethylene production capacity (105 metric ton per year), i.e., 4.48 × 105 metric ton CO2 per year compared to 3.14 × 105 metric ton CO2 per year in case of a product selectivity of 100%. This lower product selectivity leads to larger energy requirements for the CO2 capture step. The thermal energy required in the CO2 capture step is equal to approximately 87% of the total energy need. The thermal energy input in the CO2 conversion step is used in the recycle loop for the separation of unconverted CO2 from the gaseous product. In the case of complete conversion of CO2, there is no need for this separation step and hence the thermal energy input becomes negligible. The energy consumption for the CO2 conversion step is dominated by the electricity need. Taking into account that the plant runs for 8,440 h in one year (or 96% of the time), this corresponds to a continuous power requirement of 367 MW. If the product selectivity decreases to 70%, the required electrical power increases to 751 MW.
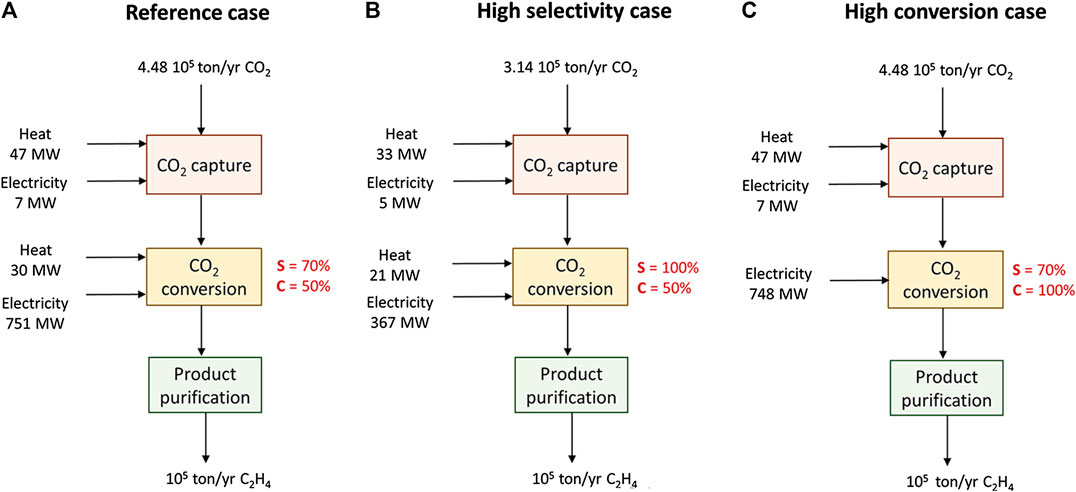
FIGURE 6. Black box representations of the electrochemical reduction of CO2 with the electrolyzer performance, i.e., conversion (C) and selectivity (S), energy input and material streams that have been considered in the economic analysis for the (A) reference, high CO2 cost and free electricity cases, (B) the high selectivity case, and (C) the high conversion case.
Figure 7 summarizes the CAPEX, OPEX and gross margins, i.e., the difference between revenues and feedstock cost, for the five studied cases and the base case, i.e., naphtha-based steam cracking. It can be seen that currently the main disadvantage of the electrochemical process is the high CAPEX of the electrochemical reactor, which is a consequence of expensive electrode materials combined with limited economies of scale due to the modular character of the electrochemical cells. However, when considering the gross margin, the electrochemical process looks promising compared to the conventional steam cracking route, due to the lower feedstock cost. Hence, future R&D efforts should aim to develop highly active, selective, stable and low-cost electrocatalysts in order to decrease the reactor CAPEX. For each case, the CAPEX, OPEX, and gross margin of the different steps, i.e., CO2 capture, CO2 conversion, and product separation, can be found in the Supplementary Material.
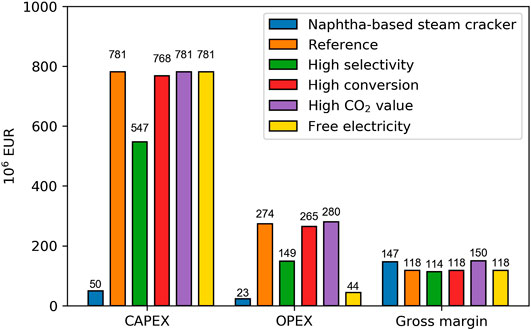
FIGURE 7. Capital expenditure, Operational expenditure, and gross margin (in 106 €) for the naphtha-based steam cracker, the reference electrochemical case, the high selectivity case, the high conversion case, the high CO2 cost case and the free electricity case.
Sensitivity Analysis
A global sensitivity analysis has been conducted in order to investigate the influence of the dominant parameters, i.e., selectivity, conversion, CO2 price, and electricity price, on the economics of the electrochemical process. The results for the sensitivity of the CAPEX, OPEX, and gross margin with respect to the reference electrochemical case are shown in Figure 8. As expected the selectivity to ethylene is the parameter with the largest influence on the CAPEX and the OPEX of the process. For a lower selectivity, more energy is lost in byproduct formation. More energy is thus required to obtain a desired production capacity of ethylene. A higher electricity consumption also increases the total electrolyzer area, resulting in a higher electrolyzer CAPEX. The conversion, which determines the required capacity of the recycle loop, has only a limited influence. This is also the case for the price of CO2, which is encouraging as it reduces the dependence of the process on a factor that is mainly determined by macro-economic and political factors (“CO2 tax” vs. capture costs). The electricity price is one of the main parameters influencing the economic feasibility of the process. Some people argue whether or not it would be beneficial to operate an electrochemical process only when the electricity price is below a certain threshold value, i.e., operate the production plant in a flexible manner according to the energy market. The mild operating conditions, i.e., ambient temperature, and the modular character of a world-scale plant would allow rapid changes in production rate. However, due to the extremely high CAPEX of the electrochemical process, we believe that it would be more beneficial to run the process continuously with a fluctuating energy price, rather than operating it as a discontinuous process. This is primarily motivated by the payback time and for the chemical industry this is typically in the order of a decade for large investments (Anderson and Fennell, 2013). Turning the installation on and off would result in an unacceptably high payback time. Also, the practical feasibility of ramping up or down such a large scale production unit should be considered and there is not a lot of published work on the start-up and shutdown of electrochemical reactors (Rousar et al., 1986; Bisang 1997).
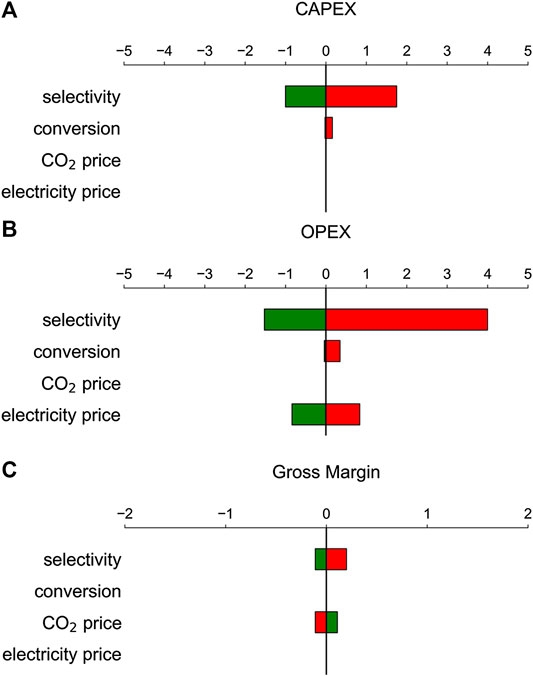
FIGURE 8. Sensitivity analysis of the (A) Capital expenditure (CAPEX), (B) Operational expenditure (OPEX), and (C) gross margin for a positive (green) or negative (red) change of the model parameters (selectivity, conversion, CO2 price and electricity price) for the reference electrochemical case.
Energy Considerations
If the CO2 reduction process results in an overall negative net CO2 balance, it can be considered a viable carbon recycling technology. This means that the amount of CO2 emitted during the complete process needs to be lower than the amount of CO2 converted. For naphtha-based steam cracking, the CO2 emissions are approximately 1 metric ton CO2 per metric ton ethylene (Ren et al., 2006). These emissions are the result of fuel combustion and utilities, both of which use fossil fuel. The main contributor is the furnace with over 90% of the CO2 emissions (Amghizar et al., 2020). Because the electrochemical reduction of CO2 to ethylene requires a significant amount of electrical power, it is clear that the electricity needs to come from low-carbon energy sources, such as wind and solar energy, to obtain an overall negative CO2 balance. Because of their intermittent nature, both solar and wind energy have a reduced capacity factor, which is not accounted for in the presented analysis. We assume that access to green electricity is continuous and steady state operation is possible. The CO2 emissions of the alternative ethylene production route are based on a Life Cycle Analysis, adopting a cradle-to-gate boundary, i.e., usage and end-of-life treatment are not included (von der Assen et al., 2013). In this analysis, the CO2 feedstock is considered as a regular feedstock with its own production emissions. The emission intensities for Northwestern Europe, expressed in kg CO2 equivalents per MW h for natural gas, solar and wind are equal to respectively 490, 48, and 12 kg CO2eq/MW h (Schlömer et al., 2015). In Figure 9, the CO2 emissions per metric ton of ethylene produced are compared between the base case, i.e., steam cracking of naphtha, and the electrochemical reduction of CO2 using gray electricity from a natural gas power plant, and green electricity from both solar and wind energy. The overall CO2 balance for the electrochemical route is based on an ideal electrolyzer, i.e., operating at a conversion and selectivity of 100%. The production of 1 metric ton of ethylene requires 3.14 metric ton of CO2 as carbon feed, while the electrolyzer uses approximately 10 MW h per metric ton CO2. The thermal energy demand for the CO2 capture step, i.e., 3.2 GJ/metric ton CO2 amounts to 0.56 metric ton CO2 per metric ton ethylene. The CO2 emissions related to the conversion step are equal to 1.50 and 0.37 metric ton CO2 per metric ton ethylene, using respectively solar and wind energy. The small difference in emission intensity between these two low-carbon energy sources leads to a significant difference in CO2 emissions per metric ton CO2 due to the large electricity demand. From Figure 9, it can be seen that this alternative production route of ethylene can potentially lead to a reduction of CO2 emissions. Note that the CO2 emissions related to the product separation and purification steps are not taken into account in this calculation.
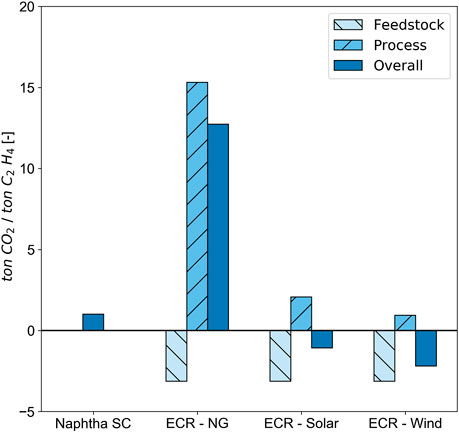
FIGURE 9. CO2 emissions per metric ton of ethylene produced: Comparison between steam cracking (SC) of naphtha and the electrochemical reduction (ECR) of CO2 using electricity from natural gas (NG), solar and wind energy. For the ECR process, both the CO2 used as feedstock as well as the CO2 emitted during the complete process is considered.
As stated before, it is clear that the electroreduction of CO2 needs to be powered by green electricity in order to obtain an overall negative net CO2 balance. The fact that reducing CO2 emissions through CCU processes will only be possible if the electricity (and in some cases the thermal energy) inputs are from renewable sources has been included in earlier studies (Bennett et al., 2014; Jouny et al., 2018; Spurgeon and Kumar, 2018; Mohsin et al., 2020). One of the challenges for electrolyzers powered by renewable energy is the operation at strongly fluctuating power inputs and with frequent interruptions due to low input (Mergel et al., 2013). The dynamic behavior of the electrochemical reactor as well as the downstream system components, (e.g., electrolyte circuit, gas separator) needs to be analyzed such that load changes do not present any problems over a large power input range. For water electrolysis, systems have been developed which allow for a large partial load range (5–100%) and can accommodate extreme overloads. Operating the electrolyzer at a very low level (i.e., at 10% of peak load) avoids the need to shut down the chemical plant completely and the associated energy losses during start-up (Brauns and Turek, 2020). In case the electrolyzer has been designed for constant conditions, the occurring power fluctuations can be damped by additional energy storage devices, which are charged when excess renewable energy is available. Overall, it can be concluded that more theoretical and experimental work is needed to better understand the dynamic behavior of CO2 electrolyzers powered by intermittent renewable energy.
Instead of considering the amount of CO2 emitted or avoided per metric ton ethylene, one can also look at the amount of CO2 avoided per energy unit of green electricity. In other words, what is the most efficient way to reduce CO2 emissions with 1 MW h of green electricity? With an electrical energy of 1 MW h, approximately 0.032 metric ton ethylene can be produced, assuming again an ideal electrolyzer performance. This ethylene formation converts 0.10 metric ton of CO2, but also leads to 0.030 metric ton of CO2 emitted using wind power as renewable energy source. The production of 0.032 metric ton ethylene via the traditional steam cracking route results in approximately 0.058 metric ton of CO2 emitted. Thus, by producing this ethylene via the alternative electrochemical route instead of the fossil-fuel based process, there is a potential of lowering the emitted CO2 by 0.13 metric ton per MW h. Using the emission intensities, 1 MW h of electricity generated from coal and natural gas, leads to respectively 0.82 and 0.49 metric ton CO2 emitted per MW h (Schlömer et al., 2015). This implies that from an energy point of view, it is more beneficial to use 1 MW h green electricity to replace 1 MW h gray electricity than use it to convert CO2 electrochemically in ethylene.
A key performance indicator often used to compare different CCU processes is the cost of CO2 avoided, i.e., the cost to avoid the emission of 1 metric ton of CO2 relative to a reference case. The production cost for fossil ethylene considering a plant located in Europe, is dominated by the feedstock cost and equal to approximately 700 € per metric ton of ethylene. For CO2-based ethylene, the production cost is equal to 1,950 € per metric ton of ethylene, assuming again an ideal electrolyzer, and an electricity price of 35 €/MW h. This value is in agreement with the study of Jouny et al. (2018), in which they report a production cost of approximately 2000 € per metric ton of ethylene, for their “optimistic case,” using the same electricity price of 35 €/MW h and a faradaic efficiency of 90%. The net CO2 emissions for the CO2 reduction process using solar and wind energy are equal to respectively −1.08 and −2.20 metric ton CO2 per metric ton ethylene. Based on these values, the CO2 avoidance cost amounts to 602 and 391 € per metric ton CO2 avoided. Note that these values are significantly higher than the recent prices of the CO2 allowances envisioned by the European Emission Trading Scheme, i.e., 28 €/metric ton CO2 in 2030 and 43 €/metric ton CO2.
Conclusions
Electrochemical conversion of CO2 to ethylene could be of interest to the chemical industry, but several breakthroughs are needed to make this competitive with the current state of the art under current market conditions. Without a substantial decrease of the electricity price and large capacity increases in renewable electricity production (to become a reliable provider at continuous low prices), this alternative ethylene production route seems infeasible for the chemical industry. Due to high capital costs for the electrochemical technology, it makes no sense to run these installations only in times when renewable power would be abundantly available and hence cheap. Turning large scale chemical processes “on” and “off” is today economically unfavorable, not even when assuming that safety would be guaranteed and an instantaneous shut down would be feasible. When combined with green electricity, e.g., wind and solar, the electrochemical reduction of CO2 can lead to a negative overall CO2 balance. However, from an energy point of view, using green electricity to replace gray electricity, has a larger CO2 avoidance potential, compared to using it for the electrochemical production of ethylene.
Data Availability Statement
The raw data supporting the conclusions of this article will be made available by the authors, without undue reservation.
Author Contributions
CP: conceptualization, formal analysis, investigation, writing—original draft, visualization, writing—review and editing. MR: conceptualization, data curation, writing—review and editing. M-FR: writing—review and editing. KG: conceptualization, supervision, writing—review and editing, and funding acquisition.
Conflict of Interest
Author MR was employed by the company Dow Benelux BV.
The remaining authors declare that the research was conducted in the absence of any commercial or financial relationships that could be construed as a potential conflict of interest.
Funding
CP acknowledges financial support from a doctoral fellowship from the Research Foundation—Flanders (FWO). The research leading to these results has also received funding from the European Research Council under the European Union’s Horizon 2020 research and innovation program (ERC Grant Agreement No. 818607).
Acknowledgments
Kees Biesheuvel, Ronald Wevers, Hanne Schatteman, Hannes Saeid Bakhsh, and Thomas Vandeputte are thanked for their valuable contributions.
Supplementary Material
The Supplementary Material for this article can be found online at: https://www.frontiersin.org/articles/10.3389/fenrg.2020.557466/full#supplementary-material
Abbreviations
CCS, carbon capture and sequestration; CCU, carbon capture and utilization; FE, Faradaic efficiency; EE, energy efficiency; CAPEX, capital expenditure; OPEX, operational expenditure; MEA, monoethanolamine; HVC, high-value chemical; BTX, benzene, toluene, xylene
References
Agarwal, A. S., Zhai, Y., Hill, D., and Sridhar, N. (2011). The electrochemical reduction of carbon dioxide to formate/formic acid: engineering and economic feasibility. ChemSusChem 4, 1301–1310. doi:10.1002/cssc.201100220
Amghizar, I., Vandewalle, L. A., Van Geem, K. M., and Marin, G. B. (2017). New trends in olefin production. Engineering 3, 171–178. doi:10.1016/j.eng.2017.02.006
Amghizar, I., Dedeyne, J. N., Brown, D. J., Marin, G. B., and Van Geem, K. M. (2020). Sustainable innovations in steam cracking: CO2 neutral olefin production. React. Chem. Eng 5, 239–257. doi:10.1039/c9re00398c
Anderson, J., and Fennell, A. (2013). Calculate financial indicators to guide investments. Chem. Eng. Prog 109, 34–40.
Banholzer, W. F., and Jones, M. E. (2013). Chemical engineers must focus on practical solutions. AIChE J 59, 2708–2720. doi:10.1002/aic.14172
Banholzer, W. F. (2012). Practical limitations and recognizing hype. Energy Environ. Sci 5, 5478–5480. doi:10.1039/c2ee03146a
Bard, A. J., Parsons, R., and Jordan, J.International Union of Pure and Applied Chemistry (1985). Standard potentials in aqueous solution. New York, NY: M. Dekker.
Bennett, S. J., Schroeder, D. J., and Mccoy, S. T. (2014). Towards a Framework for discussing and assessing CO2 utilisation in a climate context. Energy Procedia 63, 7976–7992. doi:10.1016/j.egypro.2014.11.835
Betts, R. A., Jones, C. D., Knight, J. R., Keeling, R. F., and Kennedy, J. J. (2016). El Niño and a record CO2 rise. Nat. Clim. Change 6, 806. doi:10.1038/nclimate3063
Bisang, J. M. (1997). Modelling the startup of a continuous parallel plate electrochemical reactor. J. Appl. Electrochem 27, 379–384. doi:10.1023/a:1018401418261
Brauns, J., and Turek, T. (2020). Alkaline water electrolysis powered by renewable energy: a review. Processes 8, 248. doi:10.3390/pr8020248
Dominguez-Ramos, A., Singh, B., Zhang, X., Hertwich, E. G., and Irabien, A. (2015). Global warming footprint of the electrochemical reduction of carbon dioxide to formate. J. Clean. Prod 104, 148–155. doi:10.1016/j.jclepro.2013.11.046
Endrődi, B., Bencsik, G., Darvas, F., Jones, R., Rajeshwar, K., and Janáky, C. (2017). Continuous-flow electroreduction of carbon dioxide. Prog. Energy Combust. Sci 62, 133–154.
Engelbrecht, A., Hämmerle, M., Moos, R., Fleischer, M., and Schmid, G. (2016). Improvement of the selectivity of the electrochemical conversion of CO2 to hydrocarbons using cupreous electrodes with in-situ oxidation by oxygen. Electrochim. Acta 224, 642–648. doi:10.1016/j.electacta.2016.12.059
Eurostat (2019). Natural gas price statistics [Online]. Available: https://ec.europa.eu/eurostat/statistics-explained/index.php/Natural_gas_price_statistics (Accessed February 15, 2019).
Gani, R., Bałdyga, J., Biscans, B., Brunazzi, E., Charpentier, J.-C., Drioli, E., et al. (2020). A multi-layered view of chemical and biochemical engineering. Chem. Eng. Res. Des 155, A133–A145. doi:10.1016/j.cherd.2020.01.008
Gao, J., Zhang, H., Guo, X., Luo, J., Zakeeruddin, S. M., Ren, D., et al. (2019). Selective C-C coupling in carbon dioxide electroreduction via efficient spillover of intermediates as supported by operando Raman spectroscopy. J. Am. Chem. Soc 141, 18704–18714. doi:10.1021/jacs.9b07415
Haegel, N. M., Margolis, R., Buonassisi, T., Feldman, D., Froitzheim, A., Garabedian, R., et al. (2017). Terawatt-scale photovoltaics: trajectories and challenges. Science 356, 141–143. doi:10.1126/science.aal1288
Hara, K., Kudo, A., and Sakata, T. (1997). Electrochemical CO2 reduction on a glassy carbon electrode under high pressure. J. Electroanal. Chem 421, 1–4. doi:10.1016/s0022-0728(96)01028-5
Hori, Y., Kikuchi, K., and Suzuki, S. (1985). Production of Co and CH4 in electrochemical reduction of CO2 at metal electrodes in aqueous hydrogencarbonate solution Chem. Lett 14, 1695–1698. doi:10.1246/cl.1985.1695
Hori, Y. (2008). “Electrochemical CO2 reduction on metal electrodes,” in Modern aspects of electrochemistry. Editors C. G. Vayenas, R. E. White and M. E. Gamboa-Aldeco (New York, NY: Springer New York), 89–189.
ICIS Pricing Database. Available at: https://www.icis.com/explore/commodities/energy/gas/europe/(Accessed February 15, 2019).
Jhong, H.-R. M., Ma, S., and Kenis, P. J. (2013). Electrochemical conversion of CO2 to useful chemicals: current status, remaining challenges, and future opportunities. Curr. Opin. Chem. Eng 2, 191–199. doi:10.1016/j.coche.2013.03.005
Jouny, M., Luc, W., and Jiao, F. (2018). General techno-economic analysis of CO2 electrolysis systems. Ind. Eng. Chem. Res 57, 2165–2177. doi:10.1021/acs.iecr.7b03514
Kaneco, S., Iiba, K., Suzuki, S.-K., Ohta, K., and Mizuno, T. (1999). Electrochemical reduction of carbon dioxide to hydrocarbons with high faradaic efficiency in LiOH/methanol. J. Phys. Chem. B 103, 7456–7460. doi:10.1021/jp990021j
Karl, M., Wright, R. F., Berglen, T. F., and Denby, B. (2011). Worst case scenario study to assess the environmental impact of amine emissions from a CO2 capture plant. Int. J. Greenh. Gas Con 5, 439–447. doi:10.1016/j.ijggc.2010.11.001
Ke, F.-S., Liu, X.-C., Wu, J., Sharma, P. P., Zhou, Z.-Y., Qiao, J., et al. (2017). Selective formation of C2 products from the electrochemical conversion of CO2 on CuO-derived copper electrodes comprised of nanoporous ribbon arrays. Catal. Today 288, 18–23. doi:10.1016/j.cattod.2016.10.001
Koper, M., and Roldan, B. (2019). Research needs towards sustainable production of fuels and chemicals (EnergyX). Available: https://energy-x.eu/wp-content/uploads/2019/10/Energy-X-Research-needs-report.pdf (Accessed February 10, 2019).
Kortlever, R., Shen, J., Schouten, K. J. P., Calle-Vallejo, F., and Koper, M. T. M. (2015). Catalysts and reaction pathways for the electrochemical reduction of carbon dioxide. J. Phys. Chem. Lett 6, 4073–4082. doi:10.1021/acs.jpclett.5b01559
Kortlever, R., Peters, I., Balemans, C., Kas, R., Kwon, Y., Mul, G., et al. (2016). Palladium-gold catalyst for the electrochemical reduction of CO2 to C1–C5 hydrocarbons. Chem. Commun 52, 10229–10232. doi:10.1039/c6cc03717h
Kuhl, K. P., Hatsukade, T., Cave, E. R., Abram, D. N., Kibsgaard, J., and Jaramillo, T. F. (2014). Electrocatalytic conversion of carbon dioxide to methane and methanol on transition metal surfaces. J. Am. Chem. Soc 136, 14107–14113. doi:10.1021/ja505791r
Kuramochi, T., Ramírez, A., Turkenburg, W., and Faaij, A. (2011). Techno-economic assessment and comparison of CO2 capture technologies for industrial processes: preliminary results for the iron and steel sector. Energy Procedia 4, 1981–1988. doi:10.1016/j.egypro.2011.02.079
Leung, D. Y. C., Caramanna, G., and Maroto-Valer, M. M. (2014). An overview of current status of carbon dioxide capture and storage technologies. Renew. Sustain. Energy Rev 39, 426–443. doi:10.1016/j.rser.2014.07.093
Li, K., Cousins, A., Yu, H., Feron, P., Tade, M., Luo, W., et al. (2016). Systematic study of aqueous monoethanolamine-based CO2 capture process: model development and process improvement. Energy Sci. Eng 4, 23–39. doi:10.1002/ese3.101
Ma, S., Sadakiyo, M., Luo, R., Heima, M., Yamauchi, M., and Kenis, P. J. A. (2016). One-step electrosynthesis of ethylene and ethanol from CO2 in an alkaline electrolyzer. J. Power Sources 301, 219–228. doi:10.1016/j.jpowsour.2015.09.124
Mao, X., and Hatton, T. A. (2015). Recent advances in electrocatalytic reduction of carbon dioxide using metal-free catalysts. Ind. Eng. Chem. Res 54, 4033–4042. doi:10.1021/ie504336h
Martín, A. J., Larrazábal, G. O., and Pérez-Ramírez, J. (2015). Towards sustainable fuels and chemicals through the electrochemical reduction of CO2: lessons from water electrolysis. Green Chem 17, 5114–5130. doi:10.1039/c5gc01893e
Mergel, J., Carmo, M., and Fritz, D. (2013). “Status on technologies for hydrogen production by water electrolysis,” in Transition to renewable energy systems. (Weinheim, Germany: Wiley‐VCH Verlag GmbH & Co. KGaA), 423–450.
Mistry, H., Varela, A. S., Bonifacio, C. S., Zegkinoglou, I., Sinev, I., Choi, Y.-W., et al. (2016). Highly selective plasma-activated copper catalysts for carbon dioxide reduction to ethylene. Nat. Commun 7, 12123. doi:10.1038/ncomms12123
Mohsin, I., Al-Attas, T. A., Sumon, K. Z., Bergerson, J., Mccoy, S., and Kibria, M. G. (2020). Economic and environmental assessment of integrated carbon capture and utilization. Cell Rep. Phys. Sci 1, 100104. doi:10.1016/j.xcrp.2020.100104
Ogura, K., Yano, H., and Tanaka, T. (2004). Selective formation of ethylene from CO2 by catalytic electrolysis at a three-phase interface. Catal. Today 98, 515–521. doi:10.1016/j.cattod.2004.09.006
Oloman, C., and Li, H. (2008). Electrochemical processing of carbon dioxide. ChemSusChem 1, 385–391. doi:10.1002/cssc.200800015
Pander, III, J. E., Ren, D., and Yeo, B. S. (2017). Practices for the collection and reporting of electrocatalytic performance and mechanistic information for the CO2 reduction reaction. Catal. Sci. Technol 7, 5820–5832. doi:10.1039/c7cy01785e
Peng, Y., Wu, T., Sun, L., Nsanzimana, J. M. V., Fisher, A. C., and Wang, X. (2017). Selective electrochemical reduction of CO2 to ethylene on nanopores-modified https://www.spglobal.com/platts/en/our-methodology/price-assessments/petrochemicals/pgpi-propylene copper electrodes in aqueous solution. ACS Appl. Mater. Interfaces 9, 32782–32789. doi:10.1021/acsami.7b10421
Peterson, A. A., and Nørskov, J. K. (2012). Activity descriptors for CO2 electroreduction to methane on transition-metal catalysts. J. Phys. Chem. Lett 3, 251–258. doi:10.1021/jz201461p
Platts Global Ethylene Price. Index. Available at: https://www.spglobal.com/platts/en/our-methodology/price-assessments/petrochemicals/pgpi-ethylene(Accessed February 15, 2019).
Platts Global Propylene Price. Index. Available at: https://www.spglobal.com/platts/en/our-methodology/price-assessments/petrochemicals/pgpi-propylene(Accessed February 15, 2019).
Qiao, J., Liu, Y., Hong, F., and Zhang, J. (2014). A review of catalysts for the electroreduction of carbon dioxide to produce low-carbon fuels. Chem. Soc. Rev 43, 631–675. doi:10.1039/c3cs60323g
Rakowski Dubois, M., and Dubois, D. L. (2009). Development of molecular electrocatalysts for CO2 reduction and H2 production/oxidation. Acc. Chem. Res 42, 1974–1982. doi:10.1021/ar900110c
Ren, T., Patel, M., and Blok, K. (2006). Olefins from conventional and heavy feedstocks: energy use in steam cracking and alternative processes. Energy 31, 425–451. doi:10.1016/j.energy.2005.04.001
Ren, T., Patel, M. K., and Blok, K. (2008). Steam cracking and methane to olefins: energy use, CO2 emissions and production costs. Energy 33, 817–833.
Rockström, J., Gaffney, O., Rogelj, J., Meinshausen, M., Nakicenovic, N., and Schellnhuber, H. J. (2017). A roadmap for rapid decarbonization. Science 355, 1269–1271. 10.1126/science.aah3443
Rousar, I., Micka, K., and Kimla, A. (1986). Electrochemical engineering. Amsterdam, Netherlands: Elsevier.
Schlömer, S., Bruckner, T., Fulton, L., Hertwich, E., Mckinnon, A., Perczyk, D., et al. (2015). “Technology-specific cost and performance parameters,” in Climate change 2014: mitigation of climate change: working group III contribution to the IPCC fifth assessment report. Editor Schlömer, S. (Cambridge, UK: Cambridge University Press), 1329–1356.
Schneider, J., Jia, H., Muckerman, J. T., and Fujita, E. (2012). Thermodynamics and kinetics of CO2, CO, and H+ binding to the metal centre of CO2 reductioncatalysts. Chem. Soc. Rev 41, 2036–2051. doi:10.1039/c1cs15278e
Schouten, K. J. P., Calle-Vallejo, F., and Koper, M. T. M. (2014). A step closer to the electrochemical production of liquid fuels. Angew. Chem. Int. Ed 53, 10858–10860. doi:10.1002/anie.201406174
Spigarelli, B. P., and Kawatra, S. K. (2013). Opportunities and challenges in carbon dioxide capture. J. CO2 Util 1, 69–87. doi:10.1016/j.jcou.2013.03.002
Spurgeon, J. M., and Kumar, B. (2018). A comparative technoeconomic analysis of pathways for commercial electrochemical CO2 reduction to liquid products. Energy Environ. Sci 11, 1536–1551. doi:10.1039/c8ee00097b
Tans, P. (2019). Trends in atmospheric carbon dioxide. NOAA/ESRL. Available: www.esrl.noaa.gov/gmd/ccgg/trends/ (Accessed February 10, 2019).
Tao, M., Qun, F., Hengcong, T., Zishan, H., Mingwen, J., Yunnan, G., et al. (2017). Heterogeneous electrochemical CO2 reduction using nonmetallic carbon-based catalysts: current status and future challenges. Nanotechnology 28, 472001.
Van Geem, K. M., Galvita, V. V., and Marin, G. B. (2019). Making chemicals with electricity. Science 364, 734. doi:10.1126/science.aax5179
Voltachem (2016). Empowering the chemical industry: opportunities for electrification. Den Haag, Netherlands: TNO.
Von Der Assen, N., Jung, J., and Bardow, A. (2013). Life-cycle assessment of carbon dioxide capture and utilization: avoiding the pitfalls. Energy Environ. Sci 6, 2721–2734. doi:10.1039/c3ee41151f
Whipple, D. T., and Kenis, P. J. A. (2010). Prospects of CO2 Utilization via direct heterogeneous electrochemical reduction. J. Phys. Chem. Lett 1, 3451–3458. doi:10.1021/jz1012627
Wu, J., Ma, S., Sun, J., Gold, J. I., Tiwary, C., Kim, B., et al. (2016). A metal-free electrocatalyst for carbon dioxide reduction to multi-carbon hydrocarbons and oxygenates. Nat. Commun 7, 13869. doi:10.1038/ncomms13869
Zhai, Y., Chiachiarelli, L., and Sridhar, N. (2019). Effect of gaseous impurities on the electrochemical reduction of CO2 on copper electrodes. ECS Trans 19, 1–13. doi:10.1149/1.3220175
Keywords: carbon capture and utilization, CO2 conversion, electrocatalysis, renewable and sustainable energy, ethylene
Citation: Pappijn CAR, Ruitenbeek M, Reyniers M-F and Van Geem KM (2020) Challenges and Opportunities of Carbon Capture and Utilization: Electrochemical Conversion of CO2 to Ethylene. Front. Energy Res. 8:557466. doi: 10.3389/fenrg.2020.557466
Received: 30 April 2020; Accepted: 27 August 2020;
Published: 28 September 2020.
Edited by:
Francois M. A. Marechal, École Polytechnique Fédérale de Lausanne, SwitzerlandReviewed by:
Thomas Alan Adams, McMaster University, CanadaUmberto Desideri, University of Pisa, Italy
Copyright © 2020 Pappijn, Ruitenbeek, Reyniers and Van Geem. This is an open-access article distributed under the terms of the Creative Commons Attribution License (CC BY). The use, distribution or reproduction in other forums is permitted, provided the original author(s) and the copyright owner(s) are credited and that the original publication in this journal is cited, in accordance with accepted academic practice. No use, distribution or reproduction is permitted which does not comply with these terms.
*Correspondence: Kevin M. Van Geem, a2V2aW4udmFuZ2VlbUBVR2VudC5iZQ==