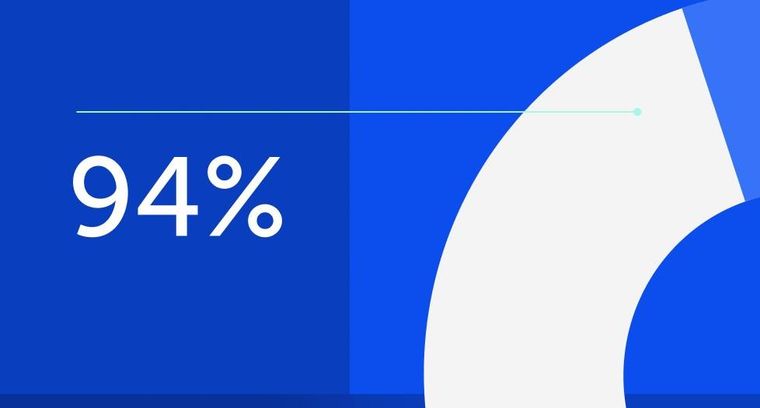
94% of researchers rate our articles as excellent or good
Learn more about the work of our research integrity team to safeguard the quality of each article we publish.
Find out more
REVIEW article
Front. Energy Res., 17 July 2019
Sec. Electrochemical Energy Storage
Volume 7 - 2019 | https://doi.org/10.3389/fenrg.2019.00065
This article is part of the Research TopicLithium Ion Battery Safety: Trends and DevelopmentsView all 4 articles
As the most widely used energy storage device in consumer electronic and electric vehicle fields, lithium ion battery (LIB) is closely related to our daily lives, on which its safety is of paramount importance. LIB is a typical multidisciplinary product. A tiny single cell is composed of both organic and inorganic materials in multi scale. In addition, its relatively closure property made it difficult to be studied on line, let alone in the battery pack or system level. Safety, often manifested by stability on abuse, including mechanical, electrical, and thermal abuses, is a quite complicated issue of LIB. Safety has to be guaranteed in large scale application. Here, safety issues related to key materials and cell design techniques will be reviewed. Key materials, including cathode, anode, electrolyte, and separator, are the fundamental of the battery. Cell design and fabrication techniques also have significant influence on the cell's electrochemical and safety performances. Here, we will summarize the thermal runaway process in single cell level, and some recent advances on battery materials and cell design.
The ever growing demands on high performance energy storage devices boost the development of high energy density lithium ion batteries, utilization of novel electrode materials with higher theoretical specific capacity (Jezowski et al., 2017; Johnson, 2018; Yoon et al., 2018) and thicker electrode design (Chen et al., 2016a; Zhao et al., 2016) is the most effective strategy to enhance the energy density (Liu et al., 2019). However, these novel materials, such as Ni rich cathodes (Sun et al., 2009; Noh et al., 2013; Lin et al., 2018b; Yang et al., 2019; Zheng et al., 2019) and Si based anodes (Park and Lee, 2011; Jeong et al., 2014; Liu et al., 2017c; Feng et al., 2018a), and electrode fabrication techniques (Ebner et al., 2014; Zhao et al., 2016) bring about some new safety concerns. Thermal runaway (TR) in single cell level would cause chain reactions and whole battery pack failure, resulting in catastrophic effect in electric vehicles or energy storage devices. Therefore, it's of vital importance to understand the factors which may potentially lead to TR in single cells.
Various publications reviewed the TR issue (Doughty and Roth, 2012; Kim et al., 2013; Feng et al., 2018b), and it's widely accepted that most TRs are caused by mechanical, electrical, or thermal abuses (Feng et al., 2018b), and all these abuse would cause short circuit in cell, which finally lead to TR. The TR process can be divided into 3 stages according to the degree of internal short or heat generation speed (Doughty and Roth, 2012; Feng et al., 2018b; Lin et al., 2018a), and it's depicted in Figure 1. The first stage is the onset of overheating, while it may possibly self-extinguished as the dendrite which caused micro-short can be by fused by the heat generated during the short in some cases (Lu et al., 2017). Otherwise, the solid electrolyte interphase (SEI) on anode would be decomposed if the heat continues to accumulate, which would lead to more side reactions between the electrode materials and electrolytes, thus adversely contribute to the heat generation and possibly melts the separator, and these are the typical characters of the second stage before TR. Large scale short eventually lead to uncontrollable overheat, typically, the TR is defined as a self-heating rate of 10°C/min or higher (Doughty and Roth, 2012), in this stage, the cell may explode for gas release and electrode material start to combustion.
Figure 1. Three stages in battery TR, Ts, safe work temperature (for battery); Te, temperature for people to escape; *SOC dependent.
Generally, the SEI tend to be decomposed firstly upon heating, both direct thermal decomposition and for the attack of PF5 (decomposition product of LiPF6) in the temperature range of 60~130°C (Kafle et al., 2018) depending on the state of charge (SOC). Polyolefin separator is the second matter to fail for its thermal shrinkage or melting when the heat continues to accumulate. Polypropylene (PP)-polyethylene (PE)-PP trilayer membrane was supposed to exhibit a shutdown function upon the melting of PE at 135°C, which would block the ion passage while PP could still act as a physical barrier to prevent short circuit (Yoo et al., 2015). Heat generation in anode material is also highly SOC dependent, although graphite or Si based materials all have good thermal stability even exposed to oxygen (Dong et al., 2018), while lithiated anodes are quite reactive as Li is always ready to donor an electron. Therefore, heat accumulation in air exposed anode is quite easy once the package material was ruptured by over pressure. In this step, temperature may rise to 200°C or even higher, thus cause other components in cell to combustion and start the TR.
In spite of various factors which may lead to the TR, materials including electrode materials as well as electrolytes, and battery design such as negative/positive capacity ratio, venting control, to name but a few, are the intrinsic approaches to enhance the battery safety. Although several comprehensive reviews have been published in the past 2 years (Feng et al., 2018b, 2019b; Lin et al., 2018a; Wang et al., 2019b), some new materials, such as Ni rich LiNixCoyMnzO2 (NCM) (Sun et al., 2009; Lin et al., 2018b; Yang et al., 2019; Zheng et al., 2019), Si based anodes (Jeong et al., 2014; Liu et al., 2017c; Feng et al., 2018a), have been proposed for the enhancement of electrochemical performances of high energy density LIB. They may bring about new safety concerns that needed to be fully recognized. Therefore, we will focus on materials and cell fabrication, and briefly summarize the recent developments in these aspects.
As the most vulnerable components in LIBs, electrolyte, and separator are mainly composed of organic compounds such as alkyl carbonates and polyolefin. Although usually considered as electrochemically inert, they may play important roles in LIB, such as ions transport throughout the whole cell to realize the charge/discharge process, hindering the direct contact between cathode and anode, to name but a few. Advanced electrolytes such as none flammable, shear thickening ones, and separators such as ceramic coated ones can significantly enhance the battery safety by ceasing the possible fire in stage 1, which make them quite important in battery safety study.
State-of-the-art electrolytes, whose safety operation temperature are usually below 80°C (Hammami et al., 2003), are composed of volatile and flammable organic solvents (including linear and cyclic alkyl carbonates), corrosive lithium salts (Kirchhofer et al., 2014), and additives. They are the most vulnerable parts in the battery. Herein, we will briefly review corresponding countermeasures from the following aspects: construction of a thermal stable SEI, flame retardant additive and shear thickening electrolytes.
As mentioned above, in the first stage of TR, SEI decomposition occurred persistently marks the onset of more side reactions and heat generation (Eshetu et al., 2013). Therefore, it is particularly important to construct a vigorous thermal stable SEI (Bhatt and O'Dwyer, 2015; Parimalam et al., 2017; Liu et al., 2018e). The major components of the SEI layer is lithium salt (e.g., ROCO2Li, Li2CO3, and LiF) and polycarbonate (Chen et al., 2007). Electrolyte additive can leave their chemical signatures in the SEI layer which make it the most effective strategy to manipulate the targeted SEI property (Xu et al., 2019). Martin's group (Zeng et al., 2018) adopted FEC and VC as additives for nano Si electrode, and it was found that they can form a robust and thermal stable SEI that was rich in polycarbonates species which contribute to an enhanced thermal stability of the lithiated silicon electrode, thus increase the exothermic temperature by about 50°C. Many other typical SEI-modifier additives, such as phosphorus (Mai et al., 2015; Song et al., 2016), nitrogen (Abu-Lebdeh and Davidson, 2009; Chen et al., 2016b), boron (Lee et al., 2014b; Kim et al., 2017), sulfur (Zuo et al., 2014), or silicon containing species (Chen et al., 2017b; Wang et al., 2017a), are widely studied in thermal stability enhancement of both SEI and CEI, some dual-functional-group additives, such as N,N-diallyic-diethyoxyl phosphamide (DADEPA) (Cao et al., 2013), tris(trimethylsilyl)phosphate (TMSP) (Rong et al., 2014), tris(trimethylsilyl)borate (TMSB) (Liu et al., 2013) are also intensively studied. Cao et al. found that the presence of 5% DADEPA can not only reduce the thermal reactivity between lithiated graphite and the electrolyte, but also remarkably enhance the thermal stability of bulk electrolytes (Cao et al., 2013). Figure 2 shows the differential scanning calorimetry (DSC) curves of fully charged graphite in reference electrolytes with and without DADEPA. It clearly demonstrated that the graphite electrodes lithiated in 5% DADEPA-containing electrolyte (labeled as SEI by DADEPA) exhibited a sharply by half heat generation compared with the reference, nevertheless, the onset exothermic peak shifts by 20°C to higher temperature.
Figure 2. DSC curves of fully charged graphite in reference electrolytes with and without DADEPA. Reprinted with permission from Cao et al. (2013). Copyright (2013) American Chemical Society.
Increasing the salt concentration is another effective strategy in building stable SEI/CEI layers (Suo et al., 2013; Yamada et al., 2014). The main advantage of concentrated electrolyte is that it can yield a robust inorganic passivation film on the cathode/anode surface which is thermally more stable compared with the organic–inorganic hybrid film, whose decomposition temperature is about 80°C (Hammami et al., 2003). Moreover, the volatility of the solvent decreased drastically owing to the stronger intra molecular interaction (Wang et al., 2018c). Lu's group used 1:2 (molar ratio) LiFSI+ triethyl phosphate (TEP) electrolyte in 18650 cells. No smoke or fire on nail penetration was found, demonstrating the ultra-stability of the SEI (Zeng et al., 2018). However, the high salt concentration result in an inevitably increase of the cost, the tradeoff between cost and performance must be considered. Otherwise, these techniques are hard to come into application.
Employment of flame retardant additive (FRA) is an effective strategy to reduce the flammability of electrolytes. Currently, the free radicals-trapping is the recognized mechanism of the FRA for safer LIB. The basic idea is that the FRA could release free radicals (usually P or halogen containing) with flame-retardant effects on thermal decompose. The radicals can scavenge the active radicals (such as H· and OH·) to suppress the free radical chain reaction of combustion (Lhomme et al., 1984). Typical organophosphates, including trimethyl phosphate (TMP) (Lhomme et al., 1984), TEP (Lalia et al., 2010), diethyl ethylphosphonate (DEEP) (Feng et al., 2013), have been used as FRAs. Once heated, phosphates will be evaporated into gas phase and decomposed into phosphorus-containing free radicals that are capable of scavenge the H· radicals, thus hinder the combustion chain reaction. Two important factors should be noted: (i) the content of gaseous FRA, as only FRA in gas phase release radicals which work in fire retardant; (ii) the ability of FRA breaks down to phosphorus-containing free radicals. Unfortunately, organophosphates exhibit lower flame retardant efficiency. Therefore, a content of above 40% will be needed to obtain the completely nonflammable electrolytes (Zhu et al., 2015). Moreover, it also comes at the poor stability with electrode materials (especially graphite anode). Phosphazene compounds have good electrochemical compatibility on carbonaceous anode. Such as triethoxyphosphazen-N-phosphoryldiethylester (PNP) (10%) (Wu et al., 2013). Nevertheless, the electrolytes with phosphazene compounds exhibit lower fire retardant efficiency in comparison with organophosphates.
Moreover, the addition of phosphazene compounds will lead to higher viscosity and lower ionic conductivity of the electrolytes (Haregewoin et al., 2016). Fluorinated phosphazene derivatives, such as pentafluoro(phenoxy)cyclotriphosphazene (FPPN) (Dagger et al., 2017) and ethoxy-(pentafluoro)-cyclotriphosphazene (PFN) (Wang et al., 2019a) are another kind of trade-off compound between the non-flammability and electrochemical stability as both F and P are fire retardant atoms. F atom can not only participate in the formation of a stable SEI or CEI, which will improve the electrochemical compatibility with electrode, but also reduce the viscosity of the electrolyte at low concentrations (5%).
Using FRA is one of the most effective method to reduce the TR risk, but might introduce other jeopardizing to cell performance. Therefore, developing FRA with higher flame retardant efficiency and enhanced electrode compatibility, or balancing non-flammability and battery performance are the recognized development trends.
Internal electrical shorts may occur in liquid electrolyte LIBs upon mechanical abuse (such as car crash), which may lead to TR and combustion. Shear thickening is an important behavior in fluid mechanics, which can be adopted into electrolyte to protect LIBs from impact damages. The electrolyte, which is liquid phase under normal operating conditions, will evolve into solid when it faces shear force. Thus, they can acts as a barrier to prevent short circuits and reduce the fire risk or catastrophic events. Ding et al. (2013) demonstrated outstanding resistance in crushing by adding commercial electrolyte [1M LiPF6 in ethylene carbonate (EC)/dimethyl carbonate (DMC)] with fumed silica particles. Stable sols can be achieved through the hydrogen bond formed between the silanols on the surface of fumed silica and the solvent. Under high shear stress, fumed silica particles will be transformed into clusters and impede the flow to prevent mechanical impacts. To protect the battery from shorting, shear thickening behaviors of the electrolytes will be highly expected when they are responsed to high impacts. Gabriel M. Veith et al. (2017) demonstrated Safe Impact Resistant Electrolytes (SAFIRE) by introducing silica into liquid electrolytes (1.2M LiPF6 3:7 wt% EC/DMC). Figure 3 shows that the viscosity increases with the increasing shear rate and it reaches the maximum at 30 wt% particles loading. Further impact test with steel ball also confirmed that the SAFIRE can improve the safety of the battery upon external force. The single-layer pouch cell with SAFIRE showed only slight fluctuations in voltage upon impact, whereas the battery using regular electrolyte was short circuited. It is noteworthy that not all kinds of silica are suitable for shear thickening response. The differences among various silicas are summarized and listed in Table 1.
Figure 3. Viscosity as a function of shear stress for various SAFIRE electrolytes. Reprinted with permission from Veith et al. (2017). Copyright (2017) American Chemical Society.
The shear thickening performances can only be found in the electrolytes with lower polydispersity (<0.01) silica particles. On the other hand, shear thinning response will happen when adding polydispersed particles (>0.1) in aprotic solvents. The abovementioned phenomena indicate that silica particle weight loading and species are the key factors for achieving SAFIRE. Moreover, the untreated silica tend to precipitate in the conventional electrolytes over times (days). Therefore, the same group (Shen et al., 2018) conducted a further study to reduce the aggregation and sedimentation by using silica nanoparticle modified with poly(methyl methacrylate) (PMMA). They hope that covalently bonds between inorganic particles and polymer can improve the long-term dispersion stability, which is beneficial to shear thickening electrolytes. Nonetheless, the crucial fact that the shear thickening electrolytes can only protect the battery upon high impact outside, but has little effect on the failure which caused by high temperature, nail penetrate, overcharging, and other abuse conditions. Furthermore, silica particles may reduce the ionic conductivity and compromise the high rate performance of the battery. Therefore, some additives are needed to compensate for them. These additives may introduce many other side reactions. Therefore, much more efforts should be made to avoid TR from the root way.
With a thickness of about 10~30 μm, separators are the only thing to cut the direct contact between electrodes. Their melt or thermal shrinkage may lead to cell shutdown (capacity dependent) (Golubkov et al., 2014) or short circuit, respectively. Many features, such as mechanical strength, thermal and dimensional stability, permeability, porosity, chemical structure, surface energy with both electrolyte and electrode material, of separators should be considered combinationally (Arora and Zhang, 2004; Cannarella et al., 2014; Lee et al., 2014a; Keyser et al., 2017). A good separator must realize a tradeoff between those properties to achieve the optimal performances in the battery. Considering their vital role in high performance LIBs, tremendous efforts have been devoted on them, either on thermal stability improvement (Mohanty et al., 2016; Jiang et al., 2017; Liu et al., 2017a, 2018b; Li et al., 2018b), or ion transport capability enhancement (low MacMullin number, Nm) (Jayaraman and Schweizer, 2009; Dahbi et al., 2012; Kirchhofer et al., 2014; Keyser et al., 2017; Ma et al., 2018). With the respect of safety performance, many works concentrated on ceramic coating (Mohanty et al., 2016; Shi et al., 2016; Jiang et al., 2017) or polymer matrix optimization (Jayaraman and Schweizer, 2009; Liu et al., 2017a, 2018b; Li et al., 2018b). Micro or nano sized Al2O3 and SiO2 are believed to be the optimal candidates for ceramic coating, not only for their thermal stability, HF scavenging ability, but also for their ease of mass production. Zhao's group coated Al2O3 onto polyethylene (PE) membranes by different binders and the separators come out with different thermal stability, thermal shrinkage temperature of the coated separators increased from 115°C to 130, 115, and 165°C, respectively when CMC+SBR, polyvinylidene fluoride-hexafluoropropylene (PVDF-HFP) and polyimide (PI) are adopted (Mohanty et al., 2016; Shi et al., 2016). In fact, the binders not only act as a bridge between the organic polymer matrix and inorganic ceramic, but also they can adjust the surface energy between separator and electrolyte/electrode, on which improved rate performance and dendrite suppression ability could be obtained (Dahbi et al., 2012; Kirchhofer et al., 2014). Recently, Liu's group developed a lyophilic battery separator from regenerated eggshell membrane (ESM), as shown in Figure 4. The abundant imine and triazine groups in the polymer matrix endow the separator with high mechanical strength, thermal stability, and electrode affinity. Therefore, it can display outstanding dendrite suppress ability and rate performance (Ma et al., 2018).
Figure 4. Preparation of the ESM separator. Reprinted from Ma et al. (2018). Copyright (2018), with permission from Elsevier.
Rationally designed separators can not only prevent the thermal induced short circuit, but also realize some special functions, such as dangerous warning (Wu et al., 2014) or even fire retardant (Liu et al., 2017a). Thus, they can provide longer time for people to escape or cease the TR from happening. Although gel polymer and solid state electrolytes are developing very fast, while in certain circumstances, such as low temperature or fast charging/discharging, the combination of liquid electrolyte, and polymer separator will still take the large share for quite a long time. Almost all state-of-the-art LIBs for electric vehicle application adopted electrolyte with fire retardant additive and ceramic coated separators, with which the safety performance could be greatly enhanced. Considering that many accidents are still associated with the battery TR, therefore, much more efforts are needed in relevant areas.
All typical anode materials, including graphite and silicon composites, show quite good thermal stability. It will be a quite different case when Li insert into the anode materials (Lin et al., 2018a; Liu et al., 2018e). Lithiated anodes become quite easy to be oxidized once the SEI decompose on heating. Furthermore, these side reactions may finally lead to the uncontrollable TR.
Zhao and coworkers conducted systematic works (Zhao et al., 2012; Fan et al., 2016) on thermal stability of lithiated graphite and SiO. They found that the crosstalk between electrolyte and electrode had significant influence on the thermal behavior of anodes, not only on exothermic temperature, but also on the heat generation quantity as shown in Figure 5. They also estimated that the specific heat valued around 290°C, Si/C (1,120 mAh/g) and SiO (2,083 mAh/g) is 5.8, 5.1, and 1.85 J/mAh, respectively, on which they believe that the SiO based anode is much safer. While we noticed that all their experiments were conducted in sealed pans, where neither air exposure nor the influence of oxygen or hydrogen was considered. Therefore, future works should take account of these factors.
Figure 5. DSC curves of (a) 0.5μL, 1 M LiPF6/EC-DMC (1:1, v/v) electrolyte and a mixture of 0.5μL electrolyte and 0.5 mg of (b) pristine Si/C electrode, (c) delithiated Si/C electrode, and (d) lithiated Si/C electrode. Reprinted from Zhao et al. (2012). Copyright (2012), with permission from Elsevier.
Jeong et al. studied the thermal behavior of these lithiated anodes in different SOC and larger temperature range (Jeong et al., 2012), they found that there's a sudden exothermic peak in the region of 350~400°C for both lithiated Si and SiO, and the reaction enthalpy in this temperature range was about 7 kJ/g for SiO, which was comparable with the one below 300°C (7.7 kJ/g). Therefore, the thermal stability of high specific capacity electrode materials must be carefully considered. They also found that thermal stability of the SiO material could be enhanced by carbon or TiO2 coating, in which carbon coating is just being effective under 300°C, while the TiO2 one is quite efficient in the whole test temperature range, the author attributed this phenomena to the blocking effect of either TiO2 or its lithiated product. They further reported a core-shell structured Si nanoparticles@TiO2/Carbon mesoporous microfiber composite (SiNPs@T/C) anode, the SiNPs@T/C remarkable suppress the exothermic behaviors than bare SiNPs and SiNPs@C, which is also attributed to the TiO2−x shell (Jeong et al., 2014).
Inspired by the thermal shutdown mechanism in separator, White's group developed a special anode architecture on which a thin spherical PE or paraffin was deposited (Baginska et al., 2012). PE and paraffin are solid in normal conditions, and their spherical structures have little influence on the ion transport. These polymers will be melted on heating and block the porous structure of electrode. Thus, the circuit can be cut off other than short, on which the safety can be guaranteed.
Besides, many factors, such as operate conditions (Belov and Yang, 2007; Larsson and Mellander, 2014; Li et al., 2019), cathode material (Inoue and Mukai, 2017), or even binder (Maleki et al., 2000; Park et al., 2014), may influence the safety performances of the anodes. Park et al. studied the effect of polymeric binder on the thermal stability of spherical natural graphite anodes, they found that the polyacrylic acid (PAA) binder showed better of the heat evolution of the lithiated electrodes than that of polyvinylidene fluoride(PVDF) or carboxymethyl cellulose/styrene butadiene (CMC/SBR) (Park et al., 2014) at low temperatures below 200°C. Citric acid (CA) is more heat resistant than CMC or PAA, Liu et al. improved the thermal stability of silicon-based anodes by incorporate CA with CMC to form a cross-linked polymer binder, with which the electrode lose no weight below 500°C (Liu et al., 2017c). Therefore, systematic works are hoped to enhance the safety of anode, and crosstalk between cell components must be considered carefully.
Cathode materials play a key role on the thermal stability of LIBs (Schipper et al., 2016; Liu et al., 2018c), it's phase transformation and oxygen release in overcharge state usually accompanied by heat generation and oxidation of electrolyte and separator (Ma et al., 2016; Inoue and Mukai, 2017; Liu et al., 2018e), and possibly lead to the uncontrollable TR.
As the most promising candidate for the cathode of high energy density LIBs, NCM is now widely studied. Bak and Hu's team found that their thermal stability is highly affected by nickel content (Bak et al., 2014). They systematically studied the thermal properties of various charged NCM cathodes (NCM433, NCM523, NCM622, and NCM811), found that the higher Ni content is, the lower onset temperature and more oxygen released from charged cathode will be. The onset temperature was decreased from ~250°C to ca. 150°C for NCM433 and NCM811, respectively. As clearly shown in Figure 6, the oxygen evolution peaks coincide well with the phase transitions for these samples, for the NMC433, no clear O2 release peak was observed coupled with a relatively smaller proportion of rock-salt, which indicated good thermal stability, while when the Ni content climbed to the NCM811, the sharply increased of O2 released at lower temperatures and the percentage of spinel or rock salt phase increased remarkably. To improve the thermal stability and cycle performance of Ni-rich NCM cathodes, Sun's team proposed and developed a new tactic: compositionally graded cathode material, in which Ni and Mn concentrations are continuously decreased and increased from the inside core to the outer shell within the cathode particle respectively (Park et al., 2015; Kim et al., 2016). At the same time, they also investigated the influence of Al substitution on this full concentration gradient material (FCG). The DSC test showed the Al-substituted material (Al-FCG61) exhibited the highest exothermic reaction temperature and lowest heat generation compared with the traditional Ni-rich cathode and the untreated FCG, indicating the strategy of alien atom substitution combined with FCG method can effectively improve the thermal stability of Ni-rich cathodes. Additionally, researchers also discovered that the SOC can influence the thermal stability of cathode. The accelerating rate calorimetry (ARC) results of different NCM series showed that as the upper cut-off potential increased, which could contribute higher specific capacity, the self-heating rate was also accelerated, especially when the upper cut-off potential reached to 4.7 V (Ma et al., 2016). Therefore, in order to keep a balance between the high energy density and the thermal stability, the upper cut-off potential of NCM cathodes are usually restricted at 4.2~4.5 V(Vs Li+/Li). Other factors, such as the influence of particle size were also are studied. MacNeil's team studied the thermal stability of LiFePO4 with different morphologies by ARC (Khakani et al., 2016). The cathodes materials have different particle sizes (in the range of about 100 nm~3 μm) and surface areas (in the range of about 6~14 m2 g−1), they found that due to a more efficient contact between the electrode material and the electrolyte, the larger surface area of LiFePO4 is, the higher initial self-heating rate of the reaction will be. Considering the relatively poor rate capacity of NCM materials, the nanocrystallization of NCM cathode become an effective way to enhance its rate capacity. However, similar to LiFePO4, the smaller particle sizes and higher surface areas of NCM cathode would induce more side reactions, accelerating the self-heating rate, thus leading to an even worse thermal stability. Therefore, effective tactics such as surface coatings or preparing micron-sized single crystal NCM cathodes are proposed by different teams to enhance the thermal stability and cycle performance (Cho et al., 2013; Li et al., 2018a; Yang et al., 2019).
Figure 6. Mass spectroscopy profiles for the oxygen (O2, m/z = 32) collected simultaneously during measurement of TR-XRD and the corresponding temperature region of the phase transitions for NMC. Adapted with permission from Bak et al. (2014). Copyright (2014) American Chemical Society.
The complexity and enclosed property of LIBs make it very difficult to recognize the heat source during the TR process of a cell. It's commonly accepted that it is the cathode which lead to the TR as LIBs with different cathode materials shows totally different thermal stability (Doughty and Roth, 2012; Bak et al., 2014). While very recently, Mukai's group (Inoue and Mukai, 2017; Wang et al., 2018b) constructed an all-inclusive microcell (AIM) in a hermetically sealed pan of the DSC analyses. The AIM is designed to work as a battery by itself which not only comprises all the battery components, but also could analysis the thermal behavior of each single material (Wang et al., 2018b). Their study proves that it is the thermal release of artificial graphite (AG) lead to the TR in the NCM|LiPF6 (EC/DEC)|AG cell, while it is NCA that lead to TR in the NCA|LiPF6 (EC/DEC)|AG cell as shown in Figure 7. Combining ARC and DSC technique, the author concluded that the two cells fail for the oxidation of electrolyte and the formation of LiF, respectively. While as reported in many previous reports, LiF is an important component in the SEI (Wu et al., 2012; Yamada, 2017), moreover, SEI regeneration was also mentioned in several papers (Feng et al., 2018b), therefore, we consider that it is the crosstalk between cathode and anode which influenced the stability of SEI and further lead to this special phenomenon.
Figure 7. The reaction mechanism of TR for the (A) NCA|LiPF6(EC/DEC)|AG and (B) NCM|LiPF6(EC/DEC)|AG cells. Reprinted from Inoue and Mukai (2017). Copyright (2017), with permission from Elsevier.
Different from the traditional knowledge in which the internal short circuit of battery is thought to be the key factor to trigger the TR (Ouyang et al., 2015; Finegan et al., 2017). Ouyang's group found that the TR may occur without internal short, and they proposed another possibility: the chemical crosstalk between cathode and anode (Liu et al., 2018e). They did the in situ experiments on a pouch cell with a PET/ceramic non-woven membrane as the thermal stable separator to prevent internal short. As illustrated in Figure 8, when adding no electrolyte, the lithiated anode exhibited an exothermic peak at 292.5°C with heat flow and ΔH of 1.4 W/g and 304 J/g, respectively. The delithiated cathode alone exhibited two exothermic peaks at 279 and 444°C, with ΔH of 108 and 148 J/g, respectively. However, when mixing the cathode and anode, the heat generation increased tremendously to 770 J/g, which almost tripled the value of the anode alone and was seven times larger than the cathode alone. Hereafter, they did the same test with but adding the electrolyte into CE, the DSC results showed the similar tendency, shown in Figure 8B. They revealed the oxygen released from cathode was consumed by the anode by passing the thermal stable separator, then causing the serious overheat reaction even though the separator was not damaged, and eventually lead to the TR. It's worth noting that based on this new theory, the all-solid-state battery may not as safe as reported.
Figure 8. The heat generation of the charged battery components by DSC measurements. (A) Charged electrode (CE) without electrolyte. (B) Charged electrode with electrolyte. An, anode; Ca, cathode; Ele, electrolyte; CE, charged electrode. Reprinted from Liu et al. (2018e). Copyright (2018), with permission from Elsevier.
The fabrication techniques, including the design of the N/P ratio, porosity, tortuosity, electrode thickness, and the cell tab have significant influence on the temperature distribution (TD) of batteries. The uneven temperature distribution is caused by the different heat generation and heat dissipation conditions in the electrode. Also the local concentration of heat will lead to excessive local temperature rise, which is the factor to cause fast lithium growth and internal short circuit. As shown in Figure 9 (Chen et al., 2017a), different N/P ratio designs changes the open circuit voltages range of the electrode pair, and therefore vary the reversible heat. The decrease in porosity or the increase in electrode thickness can enhance the ion concentration and potential gradient, which can affect the joule heat generation. According to Mei et al. (2018), the heat of battery will be accumulated at the positive tab at high discharge rate, the optimized design of current collecting tab can significantly reduce the cell temperature and lead to more uniformity heat distribution (Waldmann et al., 2016). Recently, researchers did lots of work on thicker electrode design and fabrication to improve the energy density of the battery, but it will cause more uneven temperature distribution, which cause battery performance instability and safety problems (Zhao et al., 2016). When a local temperature reaches the critical value of thermal runaway, a chain reaction occurs at this point, which further results in a large area of heat accumulation. Hence in order to develop high-performance LIBs with guaranteed safety, better refined electrode structures are required.
Figure 9. Interaction between microstructure and heat generation (Chen et al., 2017a).
The safety problems of LIB are almost always manifest as local temperature rise when the rate of heat generation is greater than that of dissipation, on which the TD in the cell has a decisive impact on the battery safety. However, it is very difficult to detect the TD inside the cell, even though it is the most effective parameter to determine whether the cell is entering the dangerous places (Wang et al., 2016), therefore, various modeling works (Kim et al., 2007; Guo et al., 2010; Feng et al., 2015, 2018b; Ren et al., 2018) were conducted to simulate the thermal properties of Li-ion batteries.
Thermal properties, including heat generation and dissipation of the batteries must be addressed in a model that able to predict the behavior of the battery under different operational conditions. Kim et al. (2007) proposed a 3D thermal abuse model of Li-ion batteries which took the effects of geometrical features into account, this model is more suitable for the larger cells compared to the 1D model. Coupled with a variety of possible heat generation reactions within the LIB, temperature of the batteries could be stimulated in detail. Guo et al. (2010) further optimized the 3D thermal abused model by took the internal conduction and convection as well as external heat dissipation under abuse conditions into consideration, the model coupled with electrochemical reaction and thermal response to study the temperature distribution and evolution inside cell. Ren et al. (2018) recently developed a new thermal runaway model that emphasizes more on the kinetics analysis of cell components, which could well reflect the battery TR mechanism and predict battery safety performance without assembling a real battery. Therefore, the battery TR models are positive to analysis the battery safety. Besides, various models proposed the triggering events such as mechanical abuse and overheating, as well as overcharge, which would finally lead to battery TR. All of the above mentioned models have value of better theoretical research, which could be a theory frame that involving the study of heat generation, distribution, and dissipation of Li-ion batteries.
The capacity balancing of the negative electrode (NE) and positive electrode (PE) in LIBs has been considered to be a crucial point considering lifetime and safe operation for cell design. To minimize the risk of lithium plating at the surface of NE during charging, which is a severe aging and safety-deteriorating process, a geometrically oversized area (Dagger et al., 2018; Lewerenz et al., 2018), as well as a slight excess capacity (Xue et al., 1995; Appiah et al., 2016; Abe and Kumagai, 2018) of NE relative to PE are required for better safety. The N/P ratio is defined as the ratio of areal reversible capacity of NE and PE (QNE/QPE).
Where q is a specific capacity (mAh/g), and m is an area loading of active material (g/cm2) for NE and PE. A good cell design should ensure that the charging capacity is fully utilized in the voltage range without Li plating. Currently, the N/P ratio is generally controlled between 1.03 and 1.2 in commercial LIBs.
The N/P ratio has a very important impact on cell safety. On the one hand, a low N/P ratio will possibly reduce the anode potential to <0 V vs. Li/Li+ and result in lithium plating on the surface of anode electrode in the charging process. On the other hand, although the cell with high N/P ratio restrains lithium plating under a given charging cut-off voltage, while may cause overcharge of the cathode, which not only degrades the crystallographic structure of the cathode material, but also oxidizes the organic electrolyte solvents (Liu et al., 2018a). The plated lithium causes degradation in safety as demonstrated in Figure 10 (Feng et al., 2018a). The lithium dendrites can break and lose contact with the active material, leading to “dead lithium” in the full cell (Jin et al., 2017). More seriously, lithium plating brings about the formation of dendrite which may pierce the separator and induce the cell to an internal short circuit (Kasnatscheew et al., 2017) and catastrophic TR. Many researchers devoting to evaluate and predict the risk of Li plating risk by analyzing voltage plateau signals (Gao et al., 2019), measuring the cell thickness (Feng et al., 2014), and simulation models (Parhizi et al., 2017). However, the internal short circuit due to Li plating which can result in serious problems in reliability and safety of LIBs, is difficult to predict, making cell safety design more complex.
Figure 10. General overview effect of plated Li on the safety for LIBs. Reprinted from Waldmann et al. (2018). Copyright (2018), with permission from Elsevier.
Overcharge on cathode caused by high potential of the positive electrode will also seriously affect the safety performance. More lithium ions are extracting from the cathode materials in overcharge, aggravating the instability of cathode material (Gao et al., 2019), which further reduces TR temperature, resulting in the deterioration of battery stability. Once the cathode materials decompose and release a large amount of oxygen, the heat release rate rises sharply due to the strong reactions between oxygen and electrode materials. Besides, the decomposition of electrolyte and side reactions on the interface produce HF (Yang et al., 2018) which will further destroy the structure stability of cathode materials. These problems not only lead to the increase of the internal resistance, but also ruin the interfacial stability and bring security risks.
When designing the LIBs, the N/P ratio is usually calculated based on the testing results of the Li half-cell. Theoretically, the N/P ratio in the full cell should be a value under the same operating conditions as half-cell for the NE and PE. However, the actual N/P ratio in practical application is often not sure, as irreversible specific capacity and/or AM loss on each electrode during charge/discharge cycling lead to continuous variations of N/P ratio (Kasnatscheew et al., 2017). Hence, the N/P ratio is a dynamic value in full cell, which are greatly affected by the charging conditions such as the cutoff voltage range (Kim et al., 2015; Ahmed et al., 2018), the charging current (Mao et al., 2018), the ambient temperature, the degree of cell degradation such as calendar aging or charge/discharge cycle aging (Kleiner et al., 2016), and so on. The adjustment of charge cutoff voltage in full cell could change the potentials of the positive and negative electrodes, thus changing the specific capacity, further resulting in N/P ratio variety. For example, the LiCoO2|graphite cell's results showed that the actual N/P ratios became gradually reduced as an increase in the charging voltage because the capacity of cathode increased with increasing the charging voltage (Kim et al., 2015). Generally, an increase in C-rate or the low ambient temperature cause a decrease in capacity, and an N/P ratio change occurs when the capacity fade rates of cathode and anode are different. Mao et al. (2018) reported that the graphite anodes exhibited a faster capacity decline as the lithiation rate exceeded 1C. In contrast, the NMC811 cathode exhibited less capacity loss as the charging rate increased from C/10 to 4C. At a low rate of C/10, the N/P ratio was 1.15. However, the rapid capacity fade of graphite at high rates caused the N/P ratio to drop to 1.0 at 3C and to 0.5 at 4C, leading to severe Li plating on the anode. For nickel-rich cathode and graphite-based anode materials system, the cathode material tends to decay more quickly due to collapse of crystal structure and dissolution of metal ions in electrolyte (Lin et al., 2018b; Zheng et al., 2019), so the N/P ratio usually getting higher in cycling. However, in the case of Si-based anode, the anode material decays faster due to material shedding and continuous cracking and reformation of SEI caused by volume expansion and pulverization (Jin et al., 2017; Feng et al., 2018a; Liu et al., 2018a), resulting in a lower and lower N/P ratio.
In summary, the N/P ratio is an important and complex parameter in cell safety design. Before designing the N/P ratio in full cell, we must fully understand the characteristics of the cathode and anode materials, including irreversible capacity, rate performance, temperature dependent performance, fatigue mechanism, etc. Considering the dynamic change of N/P ratio, a reasonable, and safe ratio needs to be set carefully.
The electrolytes containing lithium bis (trifluoromethanesulfonyl) imide (LiTFSI) are highly corrosive against Al foil that may lead to micro-short-circuit of LIB and the dissolution of Cu foil will occur when the cell over discharges, causing the safety problems (Farag et al., 2017). In addition, mechanical abuse leads to serious distortion of the battery and the cell cannot withstand the damage resulting in the occurrence of safety accident. So developing freestanding electrodes, which is realized by integrating active materials into the 3D conductive framework of carbon material, is of vital significance.
Nano sized carbon materials, such as carbon nanotubes (CNTs), graphene (GR), are the most commonly used agent in free standing electrode for their strong binding ability and conductivity. Park et al. (2017) reported a highly flexible free-standing electrode by casting slurry on a glass substrate and detaching the film after drying. It has better mechanical strength and endurance against bending or folding which PVDF-HFP and CNT as binder and conductive agents, respectively. However, the optimized free-standing electrode exhibit lower energy density and inferior rate capability than conventional electrode. Kuang et al. (2018) prepared a nanopaper electrode with compact structure and high mass loading (up to 60 mg/cm2), in which conductive nanofiber (CNF) network is designed with decoupled electron and ion transfer pathways via electrostatic assembly of neutral CB particles on negatively charged CNF. Wang et al. (2018a) made a folded GR high areal capacity composite electrode by a water-facilitated folding method. The electrode remains a continuous structure at each fold and it shows stable cycling over 500 cycles and excellent rate capability compared to the traditional electrode with the same mass loading.
Generally speaking, freestanding electrodes do guarantee the safety of the battery on account of strong toughness and resistance to corrosion. Nevertheless, some drawbacks such as higher resistance of the electrodes and complicated fabrication process should be conquered prior to use for high-performance Li-ion energy storage devices.
Energy storage and conversion is a complex process of energy-chemical energy conversion, mass transfer and heat transfer between the positive and negative electrodes in battery cells, so the generation and dissipation of heat in batteries are strongly influenced by the electrode structure, including its thickness, porosity, tortuosity, specific surface area, and so on. These structural parameters are closely related to the transport of both electrons and lithium ions, as well as the reaction kinetics of the electrode, thus affecting the distribution of current density and temperature. The unequal levels of electrode degradation due to non-uniform current flow and temperature should be given more attention because it occurs on a longer timescale and the effects on safety are more unpredictable. Large quantity of joule heat generated in the charge-discharge process may lead to the TR and safety hazard of batteries, so reducing the joule heat is crucial. Based on the Joule's law equation (Q = I2Rt), there exist two primary ways to lessen the joule heat and to reinforce the security capability of Li-ion batteries: (i) reducing the equivalent series resistance (ESR, or R in the equation) of cell and (ii) cutting off the current (I) before the onset of thermal runaway.
It's well known that ESR of a cell is composed of three segments, which are interfacial resistance for electrode/current collector, ionic, and electrical impedance in the electrode as shown in Figure 11. Plenty of efforts are made to design low resistance electrode in these aspects, such as current collector (CC) optimization (Wang et al., 2017b,c; Lin et al., 2018a; Feng et al., 2019a), electrode porous structure design (Chen et al., 2016a; Fritsch et al., 2018), and so on. Although most works on CC optimization focuses on ESR reduction and rate performance improvement by surface roughening (Wang et al., 2017c) or 3D metal foam adopting (Fritsch et al., 2018), while it also has direct effect on the safety performance. Qiao's group found that upon external loading, heat generation of damaged LIB is heavily dependent on the failure mode of the CC, therefore, by efficient surface notch design on the CC, short circuit of the cell could be effectively eliminated (Wang et al., 2017b).
Porous structure of electrodes has significant influence on both ion and electron transport, thus an express passage could reduce the ESR and joule heat effectively. Delicate pore structures in the electrode can be obtained both in the process of coating and calendaring (Bae et al., 2013; Wang et al., 2014; Liu et al., 2018d; Cheng et al., 2019), or by physical/chemical etch after the electrode was prepared (Pröll et al., 2014; Mangang et al., 2016; Park et al., 2019). Multi-scale pore structures (Liu et al., 2017b, 2018d; Cheng et al., 2019) in the electrode is expected to enlarge the passageway of Li-ion diffusion and reducing the internal resistance. Employing iterative co-extrusion and sintering technique, Chiang's group fabricated electrodes with dual-scale pore structure and maximized the battery power density (Bae et al., 2013). Cheng's group prepared electrode with gradient pore structure through the whole thickness direction by a layer-by-layer spray printing method, compared with electrode with mean pore size distribution, both C-rate and capacity degradation performance of the graded electrodes are significantly improved for the better Li+ transport property (Cheng et al., 2019).
Laser is an effective tool in porous structure constructing in electrode as it do no harms to the CC or other electrode materials. Kim et al. (2018) designed a highly ordered and hierarchical (HOH) graphite anode through the laser ablation, the HOH electrode has a porosity up to 50% which promotes ionic transport throughout the cell and mitigated the concentration polarization. Recently, Park et al. (2019) made laser structuring thick electrode with a porosity of 26% which lead to the enhancement of the power and energy densities simultaneously. The femtosecond laser creates uniformly spaced micro-grooves on the electrode, which greatly improves the Li+ kinetics and decreases the joule heat especially at high current density. While, it's worth noting that the long-term stability of these special porous structures still need to be enhanced.
Reasonable porous structure could facilitate the transport of Li+, while the electron transfer depends on the conductive network between electrode material and CC. Similar to the case in free standing electrodes, CNT (Welna et al., 2011; Sendek et al., 2018), and GR (Hassoun et al., 2014; Cai et al., 2017) are the most common used agents to build the express way for electron. Jusef's group (Hassoun et al., 2014) fabricated full cells based on LiFePO4 and GN, the cell demonstrated an initial capacity of 165 mAh/g based on the weight of LiFePO4 and an energy density of 190 Wh/kg, while the author did not mentioned electrolyte dosage or other details in energy density calculation, GN now still generally considered as just suitable for the additive application.
Single conductive cannot satisfy the requirement of the cells, thus composite conductive agents appear on the scene. Li1.2Mn0.54Ni0.13Co0.13O2 (LMNCO) based cathode was prepared by using combinatory conductive agents, GR, and CNTs. The combinatory 3D conductive network is much more effectual in accelerating electron transport than that of CNTs or GN only (Li et al., 2018c). Some conducting polymers, such as polyaniline (PANI) and polypyrrole (PPy) were also used to facilitate electron transport. One dimensional coaxial PANI@SnO2@MWCNT composite was designed as conductive-additive-free anode material (Wang et al., 2018d), in which quite stable performance was obtained. Although the nanostructured conductive work is beneficial to the conductivity of the battery, while it causes more side reactions for its large specific surface area and consumes much electrolyte, thus may reduce the energy or power density of the cell. Therefore, the trade-off between nanostructured additives and parasitic reactions should be emphasized in the future advanced LIB development.
Above all, low resistance electrode has access to notably restraint of joule heating and ensures battery safety in a way. Although the design of electrode structure has little effect on the safety performance under mechanical abuse conditions such as needling and extrusion, but it strongly influences the electrical abuse tolerance of batteries. By reducing the electrode resistance, the joule heat of the battery under electric abusive conditions can also be reduced, thus improving the safety and stability. Meantime, there's still a big challenge in developing low resistance thick electrodes to increase the energy density of LIBs, especially when the high specific capacity electrode materials such as Ni rich NCM or Si are adopted.
As the currently most widely used power battery, LIBs have an even larger market in energy storage applications, which require better safety performances in system level. Key materials, electrode and cell design, as well as mechanical, electrical, and thermal effects during the charge/discharge cycles, coupled together in the whole TR process and have significant mutual influence on each other, therefore, all these factors must take into account to settle the safety issues even in single cell level. Moreover, in larger scale applications such as electric vehicle or energy storage devices, battery thermal management systems (BTMS) are indispensable. Researchers made lots of efforts in the past decade and the overall performances of LIBs, including safety, have been greatly increased, while further enhancement is still needed especially for high energy density LIB and lithium metal batteries. Electrolyte is no doubt the most effective method to settle the safety issues, solid state electrolyte (not in the scope of this review) offers a promising prospect for dendrite suppression, but it's not omnipotent. Future study should pay more attention to the crosstalk among the battery materials (including active materials, electrolytes, conductive agents, and so on), the cell design (such as active material area loading, porosity, N/P ratio, et al.), as well as battery work conditions, to name but a few, only a systematic design from material to battery and cooperate between scientists and engineers could finally guarantee the safety of LIBs.
The raw data supporting the conclusions of this manuscript will be made available by the authors, without undue reservation, to any qualified researcher.
All persons who meet authorship criteria are listed as authors, and all authors certify that they have participated sufficiently in the work to take public responsibility for the content, including participation in the concept, design, analysis, writing, or revision of the manuscript. Furthermore, each author certifies that this material or similar material has not been and will not be submitted to or published in any other publication before its appearance in the Frontiers in Energy Research. The specific contributions made by each author are listed as follow. HZ, LZ, and XW: conception or design of the work. XW, KS, XZ, NH, LL, WL, and LZ: drafting the article. HZ and LZ: critical revision of the article. XW, KS, XZ, NH, LL, WL, LZ, and HZ: final approval of the version to be published.
This work was financially supported by the National Key Research and Development Program of China (2016YFB0100303), National Natural Science Foundation of China (No. 21706261 and No. 21706262), Beijing Natural Science Foundation (No. L172045), Beijing-Tianjin-Hebei Cooperative Innovation Community Construction Project (18244409D).
HZ was employed by Hebei IPI Science and Technology Development Co., Ltd.
The remaining authors declare that the research was conducted in the absence of any commercial or financial relationships that could be construed as a potential conflict of interest.
Abe, Y., and Kumagai, S. (2018). Effect of negative/positive capacity ratio on the rate and cycling performances of LiFePO4/graphite lithium-ion batteries. J. Energy Storage 19, 96–102. doi: 10.1016/j.est.2018.07.012
Abu-Lebdeh, Y., and Davidson, I. (2009). High-voltage electrolytes based on adiponitrile for Li-ion batteries. J. Electrochem. Soc. 156, A60–A65. doi: 10.1149/1.3023084
Ahmed, S., Trask, S. E., Dees, D. W., Nelson, P. A., Lu, W., Dunlop, A. R., et al. (2018). Cost of automotive lithium-ion batteries operating at high upper cutoff voltages. J. Power Sourc. 403, 56–65. doi: 10.1016/j.jpowsour.2018.09.037
Appiah, W. A., Park, J., Song, S., Byun, S., Ryou, M.-H., and Lee, Y. M. (2016). Design optimization of LiNi0.6Co0.2Mn0.2O2/graphite lithium-ion cells based on simulation and experimental data. J. Power Sourc. 319, 147–158. doi: 10.1016/j.jpowsour.2016.04.052
Arora, P., and Zhang, Z. M. (2004). Battery separators. Chem. Rev. 104, 4419–4462. doi: 10.1021/Cr020738u
Bae, C. J., Erdonmez, C. K., Halloran, J. W., and Chiang, Y. M. (2013). Design of battery electrodes with dual-scale porosity to minimize tortuosity and maximize performance. Adv. Mater. 25, 1254–1258. doi: 10.1002/adma.201204055
Baginska, M., Blaiszik, B. J., Merriman, R. J., Sottos, N. R., Moore, J. S., and White, S. R. (2012). Autonomic shutdown of lithium-ion batteries using thermoresponsive microspheres. Adv. Energy Mater. 2, 583–590. doi: 10.1002/aenm.201100683
Bak, S. M., Hu, E., Zhou, Y., Yu, X., Senanayake, S. D., Cho, S. J., et al. (2014). Structural changes and thermal stability of charged LiNixMnyCozO2 cathode materials studied by combined in situ time-resolved XRD and mass spectroscopy. ACS Appl. Mater. Interfaces 6, 22594–22601. doi: 10.1021/am506712c
Belov, D., and Yang, M.-H. (2007). Failure mechanism of Li-ion battery at overcharge conditions. J. Solid State Electr. 12, 885–894. doi: 10.1007/s10008-007-0449-3
Bhatt, M. D., and O'Dwyer, C. (2015). Solid electrolyte interphases at Li-ion battery graphitic anodes in propylene carbonate (PC)-based electrolytes containing FEC, LiBOB, and LiDFOB as additives. Chem. Phys. Lett. 618, 208–213. doi: 10.1016/j.cplett.2014.11.018
Cai, X., Lai, L., Shen, Z., and Lin, J. (2017). Graphene and graphene-based composites as Li-ion battery electrode materials and their application in full cells. J. Mater. Chem. A 5, 15423–15446. doi: 10.1039/C7TA04354F
Cannarella, J., Liu, X. Y., Leng, C. Z., Sinko, P. D., Gor, G. Y., and Arnold, C. B. (2014). Mechanical properties of a battery separator under compression and tension. J. Electrochem. Soc. 161, F3117–F3122. doi: 10.1149/2.0191411jes
Cao, X., Li, Y., Li, X., Zheng, J., Gao, J., Gao, Y., et al. (2013). Novel phosphamide additive to improve thermal stability of solid electrolyte interphase on graphite anode in lithium-ion batteries. ACS Appl. Mater. Interfaces 5, 11494–11497. doi: 10.1021/am4024884
Chen, C.-F., Verma, A., and Mukherjee, P. P. (2017a). Probing the role of electrode microstructure in the lithium-ion battery thermal behavior. J. Electrochem. Soc. 164, E3146–E3158. doi: 10.1149/2.0161711jes
Chen, L., Wang, K., Xie, X., and Xie, J. (2007). Effect of vinylene carbonate (VC) as electrolyte additive on electrochemical performance of Si film anode for lithium ion batteries. J. Power Sourc. 174, 538–543. doi: 10.1016/j.jpowsour.2007.06.149
Chen, L. C., Liu, D., Liu, T. J., Tiu, C., Yang, C. R., Chu, W. B., et al. (2016a). Improvement of lithium-ion battery performance using a two-layered cathode by simultaneous slot-die coating. J. Energy Storage 5, 156–162. doi: 10.1016/j.est.2015.12.008
Chen, R., Liu, F., Chen, Y., Ye, Y., Huang, Y., Wu, F., et al. (2016b). An investigation of functionalized electrolyte using succinonitrile additive for high voltage lithium-ion batteries. J. Power Sourc. 306, 70–77. doi: 10.1016/j.jpowsour.2015.10.105
Chen, R., Zhao, Y., Li, Y., Ye, Y., Li, Y., Wu, F., et al. (2017b). Vinyltriethoxysilane as an electrolyte additive to improve the safety of lithium-ion batteries. J. Mater. Chem. A 5, 5142–5147. doi: 10.1039/c6ta10210g
Cheng, C., Drummond, R., Duncan, S. R., and Grant, P. S. (2019). Micro-scale graded electrodes for improved dynamic and cycling performance of Li-ion batteries. J. Power Sourc. 413, 59–67. doi: 10.1016/j.jpowsour.2018.12.021
Cho, Y., Oh, P., and Cho, J. (2013). A new type of protective surface layer for high-capacity Ni-based cathode materials: nanoscaled surface pillaring layer. Nano Lett. 13, 1145–1152. doi: 10.1021/nl304558t
Dagger, T., Kasnatscheew, J., Vortmann-Westhoven, B., Schwieters, T., Nowak, S., Winter, M., et al. (2018). Performance tuning of lithium ion battery cells with area-oversized graphite based negative electrodes. J. Power Sourc. 396, 519–526. doi: 10.1016/j.jpowsour.2018.06.043
Dagger, T., Lürenbaum, C., Schappacher, F. M., and Winter, M. (2017). Electrochemical performance evaluations and safety investigations of pentafluoro(phenoxy)cyclotriphosphazene as a flame retardant electrolyte additive for application in lithium ion battery systems using a newly designed apparatus for improved self-extinguishing time measurements. J. Power Sourc. 342, 266–272. doi: 10.1016/j.jpowsour.2016.12.007
Dahbi, M., Violleau, D., Ghamouss, F., Jacquemin, J., Francois, T. V., Lemordant, D., et al. (2012). Interfacial properties of LiTFSI and LiPF6-based electrolytes in binary and ternary mixtures of alkylcarbonates on graphite electrodes and celgard separator. Ind. Eng. Chem. Res. 51, 5240–5245. doi: 10.1021/ie203066x
Ding, J., Tian, T., Meng, Q., Guo, Z., Li, W., Zhang, P., et al. (2013). Smart multifunctional fluids for lithium ion batteries: enhanced rate performance and intrinsic mechanical protection. Sci. Rep. 3:2485. doi: 10.1038/srep02485
Dong, X., Guo, Z., Guo, Z., Wang, Y., and Xia, Y. (2018). Organic batteries operated at −70°C. Joule 2, 902–913. doi: 10.1016/j.joule.2018.01.017
Doughty, D. H., and Roth, E. P. (2012). A general discussion of li ion battery safety. Electrochem. Soc. Interface 21, 37–44. doi: 10.1149/2.F03122if
Ebner, M., Chung, D.-W., García, R. E., and Wood, V. (2014). Tortuosity anisotropy in lithium-ion battery electrodes. Adv. Energy Mater. 4:1301278. doi: 10.1002/aenm.201301278
Eshetu, G. G., Grugeon, S., Gachot, G., Mathiron, D., Armand, M., and Laruelle, S. (2013). LiFSI vs. LiPF6 electrolytes in contact with lithiated graphite: comparing thermal stabilities and identification of specific SEI-reinforcing additives. Electrochim. Acta 102, 133–141. doi: 10.1016/j.electacta.2013.03.171
Fan, H., Li, X., He, H., Peng, N., Han, Y., Liu, Z., et al. (2016). Electrochemical properties and thermal stability of silicon monoxide anode for rechargeable lithium-ion batteries. Electrochemistry 84, 574–577. doi: 10.5796/electrochemistry.84.574
Farag, M., Sweity, H., Fleckenstein, M., and Habibi, S. (2017). Combined electrochemical, heat generation, and thermal model for large prismatic lithium-ion batteries in real-time applications. J. Power Sourc. 360, 618–633. doi: 10.1016/j.jpowsour.2017.06.031
Feng, H., Chen, Y., and Wang, Y. (2019a). Electrochemical performance of a lithium ion battery with different nanoporous current collectors. Batteries 5:21. doi: 10.3390/batteries5010021
Feng, J., Ma, P., Yang, H., and Lu, L. (2013). Understanding the interactions of phosphonate-based flame-retarding additives with graphitic anode for lithium ion batteries. Electrochim. Acta 114, 688–692. doi: 10.1016/j.electacta.2013.10.104
Feng, K., Li, M., Liu, W., Kashkooli, A. G., Xiao, X., Cai, M., et al. (2018a). Silicon-based anodes for lithium-ion batteries: from fundamentals to practical applications. Small 14:1702737. doi: 10.1002/smll.201702737
Feng, X., He, X., Ouyang, M., Lu, L., Wu, P., Kulp, C., et al. (2015). Thermal runaway propagation model for designing a safer battery pack with 25 Ah LiNixCoyMnzO2 large format lithium ion battery. App. Energ. 154, 74–91. doi: 10.1016/j.apenergy.2015.04.118
Feng, X., Ouyang, M., Liu, X., Lu, L., Xia, Y., and He, X. (2018b). Thermal runaway mechanism of lithium ion battery for electric vehicles: a review. Energy Storage Mater. 10, 246–267. doi: 10.1016/j.ensm.2017.05.013
Feng, X., Zheng, S., Ren, D., He, X., Wang, L., Cui, H., et al. (2019b). Investigating the thermal runaway mechanisms of lithium-ion batteries based on thermal analysis database. App. Energ. 246, 53–64. doi: 10.1016/j.apenergy.2019.04.009
Feng, X. N., Fang, M., He, X. M., Ouyang, M. G., Lu, L. G., Wang, H., et al. (2014). Thermal runaway features of large format prismatic lithium ion battery using extended volume accelerating rate calorimetry. J. Power Sourc. 255, 294–301. doi: 10.1016/j.jpowsour.2014.01.005
Finegan, D. P., Darcy, E., Keyser, M., Tjaden, B., Heenan, T. M. M., Jervis, R., et al. (2017). Characterising thermal runaway within lithium-ion cells by inducing and monitoring internal short circuits. Energy Environ. Sci. 10, 1377–1388. doi: 10.1039/c7ee00385d
Fritsch, M., Standke, G., Heubner, C., Langklotz, U., and Michaelis, A. (2018). 3D-cathode design with foam-like aluminum current collector for high energy density lithium-ion batteries. J. Energy Storage 16, 125–132. doi: 10.1016/j.est.2018.01.006
Gao, S., Feng, X., Lu, L., Kamyab, N., Du, J., Coman, P., et al. (2019). An experimental and analytical study of thermal runaway propagation in a large format lithium ion battery module with NCM pouch-cells in parallel. Int. J. Heat Mass Transfer 135, 93–103. doi: 10.1016/j.ijheatmasstransfer.2019.01.125
Golubkov, A. W., Fuchs, D., Wagner, J., Wiltsche, H., Stangl, C., Fauler, G., et al. (2014). Thermal-runaway experiments on consumer Li-ion batteries with metal-oxide and olivin-type cathodes. RSC Adv. 4, 3633–3642. doi: 10.1039/c3ra45748f
Guo, G., Long, B., Cheng, B., Zhou, S., Xu, P., and Cao, B. (2010). Three-dimensional thermal finite element modeling of lithium-ion battery in thermal abuse application. J. Power Sourc. 195, 2393–2398. doi: 10.1016/j.jpowsour.2009.10.090
Hammami, A., Raymond, N., and Armand, M. (2003). Lithium-ion batteries: runaway risk of forming toxic compounds. Nature 424, 635–636. doi: 10.1038/424635b
Haregewoin, A. M., Wotango, A. S., and Hwang, B.-J. (2016). Electrolyte additives for lithium ion battery electrodes: progress and perspectives. Energy Environ. Sci. 9, 1955–1988. doi: 10.1039/c6ee00123h
Hassoun, J., Bonaccorso, F., Agostini, M., Angelucci, M., Betti, M. G., Cingolani, R., et al. (2014). An advanced lithium-ion battery based on a graphene anode and a lithium iron phosphate cathode. Nano Lett. 14, 4901–4906. doi: 10.1021/nl502429m
Inoue, T., and Mukai, K. (2017). Roles of positive or negative electrodes in the thermal runaway of lithium-ion batteries: accelerating rate calorimetry analyses with an all-inclusive microcell. Electrochem. Commun. 77, 28–31. doi: 10.1016/j.elecom.2017.02.008
Jayaraman, A., and Schweizer, K. S. (2009). Effective interactions and self-assembly of hybrid polymer grafted nanoparticles in a homopolymer matrix. Macromolecules 42, 8423–8434. doi: 10.1021/ma901631x
Jeong, G., Kim, J.-G., Park, M.-S., Seo, M., Hwang, S. M., Kim, Y.-U., et al. (2014). Core–shell structured silicon nanoparticles@TiO2−−x/carbon mesoporous microfiber composite as a safe and high-performance lithium-ion battery anode. ACS Nano 8, 2977–2985. doi: 10.1021/nn500278q
Jeong, G., Kim, J.-H., Kim, Y.-U., and Kim, Y.-J. (2012). Multifunctional TiO2 coating for a SiO anode in Li-ion batteries. J. Mater. Chem. A 22, 7999. doi: 10.1039/c2jm15677f
Jezowski, P., Crosnier, O., Deunf, E., Poizot, P., Béguin, F., and Brousse, T. (2017). Safe and recyclable lithium-ion capacitors using sacrificial organic lithium salt. Nat. Mater. 17:167. doi: 10.1038/nmat5029
Jiang, X., Zhu, X., Ai, X., Yang, H., and Cao, Y. (2017). Novel ceramic-grafted separator with highly thermal stability for safe lithium-ion batteries. ACS Appl. Mater. Interfaces 9, 25970–25975. doi: 10.1021/acsami.7b05535
Jin, Y., Zhu, B., Lu, Z., Liu, N., and Zhu, J. (2017). Challenges and recent progress in the development of Si anodes for lithium-ion battery. Adv. Energy Mater. 7:17. doi: 10.1002/aenm.201700715
Johnson, C. S. (2018). Charging up lithium-ion battery cathodes. Joule 2, 373–375. doi: 10.1016/j.joule.2018.02.020
Kafle, J., Harris, J., Chang, J., Koshina, J., Boone, D., and Qu, D. (2018). Development of wide temperature electrolyte for graphite/ LiNiMnCoO2 Li-ion cells: high throughput screening. J. Power Sourc. 392, 60–68. doi: 10.1016/j.jpowsour.2018.04.102
Kasnatscheew, J., Placke, T., Streipert, B., Rothermel, S., Wagner, R., Meister, P., et al. (2017). A tutorial into practical capacity and mass balancing of lithium ion batteries. J. Electrochem. Soc. 164, A2479–A2486. doi: 10.1149/2.0961712jes
Keyser, M., Pesaran, A., Li, Q., Santhanagopalan, S., Smith, K., Wood, E., et al. (2017). Enabling fast charging–Battery thermal considerations. J. Power Sourc. 367, 228–236. doi: 10.1016/j.jpowsour.2017.07.009
Khakani, S. E. L., Rochefort, D., and MacNeil, D. D. (2016). ARC study of LiFePO4 with different morphologies prepared via three synthetic routes. J. Electrochem. Soc. 163, A1311–A1316. doi: 10.1149/2.0801607jes
Kim, C. S., Jeong, K. M., Kim, K., and Yi, C. W. (2015). Effects of capacity ratios between anode and cathode on electrochemical properties for lithium polymer batteries. Electrochim. Acta 155, 431–436. doi: 10.1016/j.electacta.2014.12.005
Kim, G.-H., Pesaran, A., and Spotnitz, R. (2007). A three-dimensional thermal abuse model for lithium-ion cells. J. Power Sourc. 170, 476–489. doi: 10.1016/j.jpowsour.2007.04.018
Kim, H., Boysen, D. A., Newhouse, J. M., Spatocco, B. L., Chung, B., Burke, P. J., et al. (2013). Liquid metal batteries: past, present, and future. Chem. Rev. 113, 2075–2099. doi: 10.1021/cr300205k
Kim, K., Park, I., Ha, S.-Y., Kim, Y., Woo, M.-H., Jeong, M.-H., et al. (2017). Understanding the thermal instability of fluoroethylene carbonate in LiPF6-based electrolytes for lithium ion batteries. Electrochim. Acta 225, 358–368. doi: 10.1016/j.electacta.2016.12.126
Kim, U.-H., Lee, E.-J., Yoon, C. S., Myung, S.-T., and Sun, Y.-K. (2016). Compositionally graded cathode material with long-term cycling stability for electric vehicles application. Adv. Energy Mater. 6:22. doi: 10.1002/aenm.201601417
Kim, Y., Drews, A., Chandrasekaran, R., Miller, T., and Sakamoto, J. (2018). Improving Li-ion battery charge rate acceptance through highly ordered hierarchical electrode design. Ionics 24, 2935–2943. doi: 10.1007/s11581-018-2502-x
Kirchhofer, M., von Zamory, J., Paillard, E., and Passerini, S. (2014). Separators for Li-ion and Li-metal battery including ionic liquid based electrolytes based on the TFSI- and FSI- anions. Int. J. Mol. Sci. 15, 14868–14890. doi: 10.3390/ijms150814868
Kleiner, K., Jakes, P., Scharner, S., Liebau, V., and Ehrenberg, H. (2016). Changes of the balancing between anode and cathode due to fatigue in commercial lithium-ion cells. J. Power Sourc. 317, 25–34. doi: 10.1016/j.jpowsour.2016.03.049
Kuang, Y., Chen, C., Pastel, G., Li, Y., Song, J., Mi, R., et al. (2018). Conductive cellulose nanofiber enabled thick electrode for compact and flexible energy storage devices. Adv. Energy Mater. 8:1802398. doi: 10.1002/aenm.201802398
Lalia, B. S., Yoshimoto, N., Egashira, M., and Morita, M. (2010). A mixture of triethylphosphate and ethylene carbonate as a safe additive for ionic liquid-based electrolytes of lithium ion batteries. J. Power Sourc. 195, 7426–7431. doi: 10.1016/j.jpowsour.2010.05.040
Larsson, F., and Mellander, B.-E. (2014). Abuse by external heating, overcharge and short circuiting of commercial lithium-ion battery cells. J. Electrochem. Soc. 161, A1611–A1617. doi: 10.1149/2.0311410jes
Lee, H., Yanilmaz, M., Toprakci, O., Fu, K., and Zhang, X. (2014a). A review of recent developments in membrane separators for rechargeable lithium-ion batteries. Energy Environ. Sci. 7, 3857–3886. doi: 10.1039/c4ee01432d
Lee, S. J., Han, J.-G., Lee, Y., Jeong, M.-H., Shin, W. C., Ue, M., et al. (2014b). A bi-functional lithium difluoro(oxalato)borate additive for lithium cobalt oxide/lithium nickel manganese cobalt oxide cathodes and silicon/graphite anodes in lithium-ion batteries at elevated temperatures. Electrochim. Acta 137, 1–8. doi: 10.1016/j.electacta.2014.05.136
Lewerenz, M., Fuchs, G., Becker, L., and Sauer, D. U. (2018). Irreversible calendar aging and quantification of the reversible capacity loss caused by anode overhang. J. Energy Storage 18, 149–159. doi: 10.1016/j.est.2018.04.029
Lhomme, V., Bruneau, C., Soyer, N., and Brault, A. (1984). Thermal-behavior of some organic-phosphates. Ind. Eng. Chem. Prod. Rd. 23, 98–102. doi: 10.1021/I300013a021
Li, H., Li, J., Ma, X., and Dahn, J. R. (2018a). Synthesis of single crystal LiNi0.6Mn0.2Co0.2O2with enhanced electrochemical performance for lithium ion batteries. J. Electrochem. Soc. 165, A1038–A1045. doi: 10.1149/2.0951805jes
Li, H., Zhang, B., Liu, W., Lin, B., Ou, Q. Q., Wang, H., et al. (2018b). Effects of an electrospun fluorinated poly(ether ether ketone) separator on the enhanced safety and electrochemical properties of lithium ion batteries. Electrochim. Acta 290, 150–164. doi: 10.1016/j.electacta.2018.08.075
Li, W., Asl, H. Y., Xie, Q., and Manthiram, A. (2019). Collapse of LiNi1−−x−−yCoxMnyO2 lattice at deep charge irrespective of nickel content in lithium-ion batteries. J. Am. Chem. Soc. 141, 5097–5101. doi: 10.1021/jacs.8b13798
Li, X., Zheng, L., Zang, Z., Liu, T., Cao, F., Sun, X., et al. (2018c). Multiply depolarized composite cathode of Li1.2Mn0.54Ni0.13Co0.13O2 embedded in a combinatory conductive network for lithium-ion battery with superior overall performances. J. Alloy. Compd. 744, 41–50. doi: 10.1016/j.jallcom.2018.02.067
Lin, D., Yuen, P. Y., Liu, Y., Liu, W., Liu, N., Dauskardt, R. H., et al. (2018a). A silica-aerogel-reinforced composite polymer electrolyte with high ionic conductivity and high modulus. Adv. Mater 30:e1802661. doi: 10.1002/adma.201802661
Lin, Q. Y., Guan, W. H., Meng, J., Huang, W., Wei, X., Zeng, Y. W., et al. (2018b). A new insight into continuous performance decay mechanism of Ni-rich layered oxide cathode for high energy lithium ion batteries. Nano Energy 54, 313–321. doi: 10.1016/j.nanoen.2018.09.066
Liu, C., Qian, K., Lei, D. N., Li, B. H., Kang, F. Y., and He, Y. B. (2018a). Deterioration mechanism of LiNi0.8Co0.15Al0.05O2/graphite-SiOx power batteries under high temperature and discharge cycling conditions. J. Mater. Chem. A 6, 65–72. doi: 10.1039/c7ta08703a
Liu, J., Bao, Z., Cui, Y., Dufek, E. J., Goodenough, J. B., Khalifah, P., et al. (2019). Pathways for practical high-energy long-cycling lithium metal batteries. Nat. Energy. 4, 180–186. doi: 10.1038/s41560-019-0338-x
Liu, J. C., Yang, K., Mo, Y. D., Wang, S. J., Han, D. M., Xiao, M., et al. (2018b). Highly safe lithium-ion batteries: high strength separator from polyformaldehyde/cellulose nanofibers blend. J. Power Sourc. 400, 502–510. doi: 10.1016/j.jpowsour.2018.08.043
Liu, K., Liu, W., Qiu, Y., Kong, B., Sun, Y., Chen, Z., et al. (2017a). Electrospun core-shell microfiber separator with thermal-triggered flame-retardant properties for lithium-ion batteries. Sci. Adv. 3:e1601978. doi: 10.1126/sciadv.1601978
Liu, K., Liu, Y., Lin, D., Pei, A., and Cui, Y. (2018c). Materials for lithium-ion battery safety. Sci. Adv. 4:eaas9820. doi: 10.1126/sciadv.aas9820
Liu, L., Guan, P. J., and Liu, C. H. (2017b). Experimental and simulation investigations of porosity graded cathodes in mitigating battery degradation of high voltage lithium-ion batteries. J. Electrochem. Soc. 164, A3163–A3173. doi: 10.1149/2.1021713jes
Liu, T., Li, X. C., Sun, S. M., Sun, X. L., Cao, F. T., Ohsaka, T., et al. (2018d). Analysis of the relationship between vertical imparity distribution of conductive additive and electrochemical behaviors in lithium ion batteries. Electrochim. Acta 269, 422–428. doi: 10.1016/j.electacta.2018.03.038
Liu, X., Ren, D., Hsu, H., Feng, X., Xu, G.-L., Zhuang, M., et al. (2018e). Thermal runaway of lithium-ion batteries without internal short circuit. Joule 2, 2047–2064. doi: 10.1016/j.joule.2018.06.015
Liu, Y., Tai, Z., Zhou, T., Sencadas, V., Zhang, J., Zhang, L., et al. (2017c). An all-integrated anode via interlinked chemical bonding between double-shelled-yolk-structured silicon and binder for lithium-ion batteries. Adv. Mater. 29:44. doi: 10.1002/adma.201703028
Liu, Y. B., Tan, L., and Li, L. (2013). Tris(trimethylsilyl) borate as an electrolyte additive to improve the cyclability of LiMn2O4 cathode for lithium-ion battery. J. Power Sourc. 221, 90–96. doi: 10.1016/j.jpowsour.2012.08.028
Lu, D., Tao, J., Yan, P., Henderson, W. A., Li, Q., Shao, Y., et al. (2017). Formation of reversible solid electrolyte interface on graphite surface from concentrated electrolytes. Nano Lett. 17, 1602–1609. doi: 10.1021/acs.nanolett.6b04766
Ma, L., Chen, R., Hu, Y., Zhang, W., Zhu, G., Zhao, P., et al. (2018). Nanoporous and lyophilic battery separator from regenerated eggshell membrane with effective suppression of dendritic lithium growth. Energy Storage Mater. 14, 258–266. doi: 10.1016/j.ensm.2018.04.016
Ma, L., Nie, M., Xia, J., and Dahn, J. R. (2016). A systematic study on the reactivity of different grades of charged Li[NixMnyCoz]O2 with electrolyte at elevated temperatures using accelerating rate calorimetry. J. Power Sourc. 327, 145–150. doi: 10.1016/j.jpowsour.2016.07.039
Mai, S., Xu, M., Liao, X., Xing, L., and Li, W. (2015). Improving cyclic stability of lithium nickel manganese oxide cathode at elevated temperature by using dimethyl phenylphosphonite as electrolyte additive. J. Power Sourc. 273, 816–822. doi: 10.1016/j.jpowsour.2014.09.171
Maleki, H., Deng, G., Kerzhner-Haller, I., Anani, A., and Howard, J. N. (2000). Thermal stability studies of binder materials in anodes for lithium-ion batteries. J. Electrochem. Soc. 147, 4470–4475. doi: 10.1149/1.1394088
Mangang, M., Seifert, H. J., and Pfleging, W. (2016). Influence of laser pulse duration on the electrochemical performance of laser structured LiFePO4 composite electrodes. J. Power Sourc. 304, 24–32. doi: 10.1016/j.jpowsour.2015.10.086
Mao, C. Y., Ruther, R. E., Li, J. L., Du, Z. J., and Belharouak, I. (2018). Identifying the limiting electrode in lithium ion batteries for extreme fast charging. Electrochem. Commun. 97, 37–41. doi: 10.1016/j.elecom.2018.10.007
Mei, W., Chen, H., Sun, J., and Wang, Q. (2018). Numerical study on tab dimension optimization of lithium-ion battery from the thermal safety perspective. Appl. Therm. Eng. 142, 148–165. doi: 10.1016/j.applthermaleng.2018.06.075
Mohanty, P. S., Nöjd, S., Bergman, M. J., Nägele, G., Arrese-Igor, S., Alegria, A., et al. (2016). Dielectric spectroscopy of ionic microgel suspensions. Soft Matter 12, 9705–9727. doi: 10.1039/c6sm01683a
Noh, H. J., Youn, S., Yoon, C. S., and Sun, Y. K. (2013). Comparison of the structural and electrochemical properties of layered Li[NixCoyMnz]O2 (x = 1/3, 0.5, 0.6, 0.7, 0.8 and 0.85) cathode material for lithium-ion batteries. J. Power Sourc. 233, 121–130. doi: 10.1016/j.jpowsour.2013.01.063
Ouyang, M., Zhang, M., Feng, X., Lu, L., Li, J., He, X., et al. (2015). Internal short circuit detection for battery pack using equivalent parameter and consistency method. J. Power Sourc. 294, 272–283. doi: 10.1016/j.jpowsour.2015.06.087
Parhizi, M., Ahmed, M. B., and Jain, A. (2017). Determination of the core temperature of a Li-ion cell during thermal runaway. J. Power Sourc. 370, 27–35. doi: 10.1016/j.jpowsour.2017.09.086
Parimalam, B. S., MacIntosh, A. D., Kadam, R., and Lucht, B. L. (2017). Decomposition reactions of anode solid electrolyte interphase (SEI) components with LiPF6. J. Phys. Chem. C 121, 22733–22738. doi: 10.1021/acs.jpcc.7b08433
Park, J., Hyeon, S., Jeong, S., and Kim, H.-J. (2019). Performance enhancement of Li-ion battery by laser structuring of thick electrode with low porosity. J. Ind. Eng. Chem. 70, 178–185. doi: 10.1016/j.jiec.2018.10.012
Park, K.-J., Lim, B.-B., Choi, M.-H., Jung, H.-G., Sun, Y.-K., Haro, M., et al. (2015). A high-capacity Li[Ni0.8Co0.06Mn0.14]O2 positive electrode with a dual concentration gradient for next-generation lithium-ion batteries. J. Mater. Chem. A 3, 22183–22190. doi: 10.1039/c5ta05657h
Park, Y., Park, G., Park, J., and Lee, J. (2017). Robust free-standing electrodes for flexible lithium-ion batteries prepared by a conventional electrode fabrication process. Electrochim. Acta 247, 371–380. doi: 10.1016/j.electacta.2017.07.032
Park, Y.-S., Oh, E.-S., and Lee, S.-M. (2014). Effect of polymeric binder type on the thermal stability and tolerance to roll-pressing of spherical natural graphite anodes for Li-ion batteries. J. Power Sourc. 248, 1191–1196. doi: 10.1016/j.jpowsour.2013.10.076
Park, Y. S., and Lee, S. M. (2011). Thermal stability of lithiated silicon anodes with electrolyte. B. Korean Chem. Soc. 32, 145–148. doi: 10.5012/bkcs.2011.32.1.145
Pröll, J., Kim, H., Piqué, A., Seifert, H. J., and Pfleging, W. (2014). Laser-printing and femtosecond-laser structuring of LiMn2O4 composite cathodes for Li-ion microbatteries. J. Power Sourc. 255, 116–124. doi: 10.1016/j.jpowsour.2013.12.132
Ren, D. S., Liu, X., Feng, X. N., Lu, L. G., Ouyang, M. G., Li, J. Q., et al. (2018). Model-based thermal runaway prediction of lithium-ion batteries from kinetics analysis of cell components. App. Energ. 228, 633–644. doi: 10.1016/j.apenergy.2018.06.126
Rong, H., Xu, M., Xing, L., and Li, W. (2014). Enhanced cyclability of LiNi0.5Mn1.5O4 cathode in carbonate based electrolyte with incorporation of tris(trimethylsilyl)phosphate (TMSP). J. Power Sourc. 261, 148–155. doi: 10.1016/j.jpowsour.2014.03.032
Schipper, F., Erickson, E. M., Erk, C., Shin, J.-Y., Chesneau, F. F., and Aurbach, D. (2016). Review—recent advances and remaining challenges for lithium ion battery cathodes. J. Electrochem. Soc. 164, A6220–A6228. doi: 10.1149/2.0351701jes
Sendek, A. D., Cubuk, E. D., Antoniuk, E. R., Cheon, G., Cui, Y., and Reed, E. J. (2018). Machine learning-assisted discovery of solid li-ion conducting materials. Chem. Mater. 31, 342–352. doi: 10.1021/acs.chemmater.8b03272
Shen, B. H., Armstrong, B. L., Doucet, M., Heroux, L., Browning, J. F., Agamalian, M., et al. (2018). Shear thickening electrolyte built from sterically stabilized colloidal particles. ACS Appl. Mater. Interfaces 10, 9424–9434. doi: 10.1021/acsami.7b19441
Shi, C., Dai, J. H., Shen, X., Peng, L. Q., Li, C., Wang, X., et al. (2016). A high-temperature stable ceramic-coated separator prepared with polyimide binder/Al2O3 particles for lithium-ion batteries. J. Membrane. Sci. 517, 91–99. doi: 10.1016/j.memsci.2016.06.035
Song, Y.-M., Kim, C.-K., Kim, K.-E., Hong, S. Y., and Choi, N.-S. (2016). Exploiting chemically and electrochemically reactive phosphite derivatives for high-voltage spinel LiNi0.5Mn1.5O4 cathodes. J. Power Sourc. 302, 22–30. doi: 10.1016/j.jpowsour.2015.10.043
Sun, Y. K., Myung, S. T., Park, B. C., Prakash, J., Belharouak, I., and Amine, K. (2009). High-energy cathode material for long-life and safe lithium batteries. Nat. Mater. 8, 320–324. doi: 10.1038/nmat2418
Suo, L., Hu, Y. S., Li, H., Armand, M., and Chen, L. (2013). A new class of Solvent-in-Salt electrolyte for high-energy rechargeable metallic lithium batteries. Nat. Commun. 4:1481. doi: 10.1038/ncomms2513
Veith, G. M., Arrnstrong, B. L., Wang, H., Kalnaus, S., Tenhaeff, W. E., and Patterson, M. L. (2017). Shear thickening electrolytes for high impact resistant batteries. ACS Energy Lett. 2, 2084–2088. doi: 10.1021/acsenergylett.7b00511
Waldmann, T., Geramifard, G., and Wohlfahrt-Mehrens, M. (2016). Influence of current collecting tab design on thermal and electrochemical performance of cylindrical Lithium-ion cells during high current discharge. J. Energy Storage 5, 163–168. doi: 10.1016/j.est.2015.12.007
Waldmann, T., Hogg, B.-I., and Wohlfahrt-Mehrens, M. (2018). Li plating as unwanted side reaction in commercial Li-ion cells – A review. J. Power Sourc. 384, 107–124. doi: 10.1016/j.jpowsour.2018.02.063
Wang, B., Ryu, J., Choi, S., Song, G., Hong, D., Hwang, C., et al. (2018a). Folding graphene film yields high areal energy storage in lithium-ion batteries. ACS Nano 12, 1739–1746. doi: 10.1021/acsnano.7b08489
Wang, H., Li, Y., Li, Y., Liu, Y., Lin, D., Zhu, C., et al. (2019a). Wrinkled graphene cages as hosts for high-capacity li metal anodes shown by cryogenic electron microscopy. Nano Lett 19, 1326–1335. doi: 10.1021/acs.nanolett.8b04906
Wang, H., Sun, D., Li, X., Ge, W., Deng, B., Qu, M., et al. (2017a). Alternative multifunctional cyclic organosilicon as an efficient electrolyte additive for high performance lithium-ion batteries. Electrochim. Acta 254, 112–122. doi: 10.1016/j.electacta.2017.09.111
Wang, J., Cui, Y., and Wang, D. (2018b). Design of hollow nanostructures for energy storage, conversion and production. Adv Mater 2018:e1801993. doi: 10.1002/adma.201801993
Wang, J., Yamada, Y., Sodeyama, K., Watanabe, E., Takada, K., Tateyama, Y., et al. (2018c). Fire-extinguishing organic electrolytes for safe batteries. Nat. Energy 3, 22–29. doi: 10.1038/s41560-017-0033-8
Wang, M., Le, A. V., Noelle, D. J., Shi, Y., Meng, Y. S., and Qiao, Y. (2017b). Internal-short-mitigating current collector for lithium-ion battery. J. Power Sourc. 349, 84–93. doi: 10.1016/j.jpowsour.2017.03.004
Wang, M., Le, A. V., Shi, Y., Noelle, D. J., Wu, D., Fan, J., et al. (2017c). Sigmoidal current collector for lithium-ion battery. J. Appl. Phys. 121:015303. doi: 10.1063/1.4973585
Wang, M.-S., Wang, Z.-Q., Chen, Z., Yang, Z.-L., Tang, Z.-L., Luo, H.-Y., et al. (2018d). One dimensional and coaxial polyaniline@tin dioxide@multi-wall carbon nanotube as advanced conductive additive free anode for lithium ion battery. Chem. Eng. J. 334, 162–171. doi: 10.1016/j.cej.2017.07.106
Wang, P. D., Zhang, X. Y., Yang, L., Zhang, X. Y., Yang, M., Chen, H. S., et al. (2016). Real-time monitoring of internal temperature evolution of the lithium-ion coin cell battery during the charge and discharge process. Extreme Mech. Lett. 9, 459–466. doi: 10.1016/j.eml.2016.03.013
Wang, Q., Jiang, L., Yu, Y., and Sun, J. (2019b). Progress of enhancing the safety of lithium ion battery from the electrolyte aspect. Nano Energy 55, 93–114. doi: 10.1016/j.nanoen.2018.10.035
Wang, X., Susantyoko, R. A., Fan, Y., Sun, L., Xiao, Q., and Zhang, Q. (2014). Vertically aligned CNT-supported thick Ge films as high-performance 3D anodes for lithium ion batteries. Small 10, 2826–2829. doi: 10.1002/smll.201400003
Welna, D. T., Qu, L., Taylor, B. E., Dai, L., and Durstock, M. F. (2011). Vertically aligned carbon nanotube electrodes for lithium-ion batteries. J. Power Sourc. 196, 1455–1460. doi: 10.1016/j.jpowsour.2010.08.003
Wu, B. B., Pei, F., Wu, Y., Mao, R. J., Ai, X. P., Yang, H. X., et al. (2013). An electrochemically compatible and flame-retardant electrolyte additive for safe lithium ion batteries. J. Power Sourc. 227, 106–110. doi: 10.1016/j.jpowsour.2012.11.018
Wu, H., Zhuo, D., Kong, D., and Cui, Y. (2014). Improving battery safety by early detection of internal shorting with a bifunctional separator. Nat. Commun. 5:5193. doi: 10.1038/ncomms6193
Wu, Z.-S., Xue, L., Ren, W., Li, F., Wen, L., and Cheng, H.-M. (2012). A LiF nanoparticle-modified graphene electrode for high-power and high-energy lithium ion batteries. Adv. Energy Mater. 22, 3290–3297. doi: 10.1002/adfm.201200534
Xu, Z., Yang, J., Li, H., Nuli, Y., and Wang, J. (2019). Electrolytes for advanced lithium ion batteries using silicon-based anodes. J. Mater. Chem. A 7, 9432–9446. doi: 10.1039/c9ta01876j
Xue, R. J., Huang, H., Li, G. B., and Chen, L. Q. (1995). Effect of cathode anode mass-ratio in lithium-ion secondary cells. J. Power Sourc. 55, 111–114. doi: 10.1016/0378-7753(94)02165-Y
Yamada, Y. (2017). Developing new functionalities of superconcentrated electrolytes for lithium-ion batteries. Electrochemistry 85, 559–565. doi: 10.5796/electrochemistry.85.559
Yamada, Y., Furukawa, K., Sodeyama, K., Kikuchi, K., Yaegashi, M., Tateyama, Y., et al. (2014). Unusual stability of acetonitrile-based superconcentrated electrolytes for fast-charging lithium-ion batteries. J. Am. Chem. Soc. 136, 5039–5046. doi: 10.1021/ja412807w
Yang, H., Wu, H. H., Ge, M., Li, L., Yuan, Y., Yao, Q., et al. (2019). Simultaneously dual modification of Ni-rich layered oxide cathode for high-energy lithium-ion batteries. Adv. Funct. Mater. 29:13. doi: 10.1002/adfm.201808825
Yang, X. G., Ge, S. H., Liu, T., Leng, Y. J., and Wang, C. Y. (2018). A look into the voltage plateau signal for detection and quantification of lithium plating in lithium-ion cells. J. Power Sourc. 395, 251–261. doi: 10.1016/j.jpowsour.2018.05.073
Yoo, K., Deshpande, A., Banerjee, S., and Dutta, P. (2015). Electrochemical model for ionic liquid electrolytes in lithium batteries. Electrochim. Acta 176, 301–310. doi: 10.1016/j.electacta.2015.07.003
Yoon, C. S., Ryu, H.-H., Park, G.-T., Kim, J.-H., Kim, K.-H., and Sun, Y.-K. (2018). Extracting maximum capacity from Ni-rich Li[Ni0.95Co0.025Mn0.025]O2 cathodes for high-energy-density lithium-ion batteries. J. Mater. Chem. A 6, 4126–4132. doi: 10.1039/C7TA11346C
Zeng, Z., Murugesan, V., Han, K. S., Jiang, X., Cao, Y., Xiao, L., et al. (2018). Non-flammable electrolytes with high salt-to-solvent ratios for Li-ion and Li-metal batteries. Nat. Energy 3, 674–681. doi: 10.1038/s41560-018-0196-y
Zhao, H., Yang, Q., Yuca, N., Ling, M., Higa, K., Battaglia, V. S., et al. (2016). A convenient and versatile method to control the electrode microstructure toward high-energy lithium-ion batteries. Nano Lett. 16, 4686–4690. doi: 10.1021/acs.nanolett.6b02156
Zhao, L., Han, S.-H., Okada, S., Na, B.-K., Takeno, K., and Yamaki, J. (2012). Thermal stability of silicon negative electrode for Li-ion batteries. J. Power Sourc. 203, 78–83. doi: 10.1016/j.jpowsour.2011.11.068
Zheng, S. Y., Hong, C. Y., Guan, X. Y., Xiang, Y. X., Liu, X. S., Xu, G. L., et al. (2019). Correlation between long range and local structural changes in Ni-rich layered materials during charge and discharge process. J. Power Sourc. 412, 336–343. doi: 10.1016/j.jpowsour.2018.11.053
Zhu, X. M., Jiang, X. Y., Ai, X. P., Yang, H. X., and Cao, Y. L. (2015). Bis(2,2,2-Trifluoroethyl) ethylphosphonate as novel high-efficient flame retardant additive for safer lithium-ion battery. Electrochim. Acta 165, 67–71. doi: 10.1016/j.electacta.2015.02.247
Keywords: lithium ion battery, safety, abuse, internal short circuit, thermal runaway
Citation: Wu X, Song K, Zhang X, Hu N, Li L, Li W, Zhang L and Zhang H (2019) Safety Issues in Lithium Ion Batteries: Materials and Cell Design. Front. Energy Res. 7:65. doi: 10.3389/fenrg.2019.00065
Received: 23 April 2019; Accepted: 04 July 2019;
Published: 17 July 2019.
Edited by:
Qingsong Wang, University of Science and Technology of China, ChinaCopyright © 2019 Wu, Song, Zhang, Hu, Li, Li, Zhang and Zhang. This is an open-access article distributed under the terms of the Creative Commons Attribution License (CC BY). The use, distribution or reproduction in other forums is permitted, provided the original author(s) and the copyright owner(s) are credited and that the original publication in this journal is cited, in accordance with accepted academic practice. No use, distribution or reproduction is permitted which does not comply with these terms.
*Correspondence: Lan Zhang, emhhbmdsQGlwZS5hYy5jbg==; Haitao Zhang, aHR6aGFuZ0BpcGUuYWMuY24=
Disclaimer: All claims expressed in this article are solely those of the authors and do not necessarily represent those of their affiliated organizations, or those of the publisher, the editors and the reviewers. Any product that may be evaluated in this article or claim that may be made by its manufacturer is not guaranteed or endorsed by the publisher.
Research integrity at Frontiers
Learn more about the work of our research integrity team to safeguard the quality of each article we publish.