- 1Department of Environmental Sciences, University of Peshawar, Peshawar, Pakistan
- 2Centre of Excellence in Environmental Studies, King Abdulaziz University, Jeddah, Saudi Arabia
- 3Department of Environmental Sciences, Faculty of Meteorology, Environment and Arid Land Agriculture, King Abdulaziz University, Jeddah, Saudi Arabia
- 4Central Metallurgical R&D Institute, Helwan, Egypt
- 5School of Chemical and Process Engineering, University of Leeds, Leeds, United Kingdom
Pyrolysis based biorefineries have great potential to convert waste such as plastic and biomass waste into energy and other valuable products, to achieve maximum economic and environmental benefits. In this study, the catalytic pyrolysis of different types of plastics wastes (PS, PE, PP, and PET) as single or mixed in different ratios, in the presence of modified natural zeolite (NZ) catalysts, in a small pilot scale pyrolysis reactor was carried out. The NZ was modified by thermal activation (TA-NZ) at 550°C and acid activation (AA-NZ) with HNO3, to enhance its catalytic properties. The catalytic pyrolysis of PS produced a higher liquid oil (70 and 60%) than PP (40 and 54%) and PE (40 and 42%), using TA-NZ and AA-NZ catalysts, respectively. The gas chromatography-mass spectrometry (GC-MS) analysis of oil showed a mixture of aromatics, aliphatic and other hydrocarbon compounds. The TA-NZ and AA-NZ catalysts showed a different effect on the wt% of catalytic pyrolysis products and liquid oil chemical compositions, with AA-NZ showing higher catalytic activity than TA-NZ. FT-IR results showed clear peaks of aromatic compounds in all liquid oil samples with some peaks of alkanes that further confirmed the GC-MS results. The liquid oil has a high heating value (HHV) range of 41.7–44.2 MJ/kg, close to conventional diesel. Therefore, it has the potential to be used as an alternative source of energy and as transportation fuel after refining/blending with conventional fuels.
Introduction
Plastic waste production and consumption is increasing at an alarming rate, with the increase of the human population, rapid economic growth, continuous urbanization, and changes in life style. In addition, the short life span of plastic accelerates the production of plastic waste on a daily basis. The global plastic production was estimated at around 300 million tons per year and is continuously increasing every year (Miandad et al., 2016a; Ratnasari et al., 2017). Plastics are made of petrochemical hydrocarbons with additives such as flame-retardants, stabilizer, and oxidants that make it difficult to bio-degrade (Ma et al., 2017). Plastic waste recycling is carried out in different ways, but in most developing countries, open or landfill disposal is a common practice for plastic waste management (Gandidi et al., 2018). The disposal of plastic waste in landfills provide habitat for insects and rodents, that may cause different types of diseases (Alexandra, 2012). Furthermore the cost of transportation, labor and maintenance may increase the cost of recycling projects (Gandidi et al., 2018). In addition, due to rapid urbanization, the land available for landfills, especially in cities, is reducing. Pyrolysis is a common technique used to convert plastic waste into energy, in the form of solid, liquid and gaseous fuels.
Pyrolysis is the thermal degradation of plastic waste at different temperatures (300–900°C), in the absence of oxygen, to produced liquid oil (Rehan et al., 2017). Different kinds of catalysts are used to improve the pyrolysis process of plastic waste overall and to enhance process efficiency. Catalysts have a very critical role in promoting process efficiency, targeting the specific reaction and reducing the process temperature and time (Serrano et al., 2012; Ratnasari et al., 2017). A wide range of catalysts have been employed in plastic pyrolysis processes, but the most extensively used catalysts are ZSM-5, zeolite, Y-zeolite, FCC, and MCM-41 (Ratnasari et al., 2017). The catalytic reaction during the pyrolysis of plastic waste on solid acid catalysts may include cracking, oligomerization, cyclization, aromatization and isomerization reactions (Serrano et al., 2012).
Several studies reported the use of microporous and mesoporous catalysts for the conversion of plastic waste into liquid oil and char. Uemichi et al. (1998) carried out catalytic pyrolysis of polyethylene (PE) with HZSM-5 catalysts. The use of HZSM-5 increased liquid oil production with the composition of aromatics and isoalkanes compounds. Gaca et al. (2008) carried out pyrolysis of plastic waste with modified MCM-41 and HZSM-5 and reported that use of HZSM-5 produced lighter hydrocarbons (C3–C4) with maximum aromatic compounds. Lin et al. (2004) used different kinds of catalysts and reported that even mixing of HZSM-5 with mesoporous SiO2-Al2O3 or MCM-41 led to the maximum production of liquid oil with minimal gas production. Aguado et al. (1997) reported the production of aromatics and aliphatic compounds from the catalytic pyrolysis of PE with HZSM-5, while the use of mesoporous MCM-41 decreased the aromatic compounds produced due to its low acid catalytic activity. The use of synthetic catalysts enhanced the overall pyrolysis process and improved the quality of produced liquid oil. However, the use of synthetic catalysts increased the cost of the pyrolysis process.
The NZ catalysts can be used to overcome the economic challenges of catalytic pyrolysis which comes with the use of expensive catalysts. In recent years, NZ has gained significant attention for its potential environmental applications. Naturally, NZ is found in Japan, USA, Cuba, Indonesia, Hungary, Italy, and the Kingdom of Saudi Arabia (KSA) (Sriningsih et al., 2014; Nizami et al., 2016). The deposit of NZ in KSA mostly lies in Harrat Shama and Jabbal Shama and mainly contain minerals of mordenite with high thermal stability, making it suitable as a catalyst in plastic waste pyrolysis. Sriningsih et al. (2014) modified NZ from Sukabumi, Indonesia by depositing transitional metals such as Ni, Co, and Mo and carried out pyrolysis of low-density polyethylene (LDPE). Gandidi et al. (2018) used NZ from Lampung, Indonesia for the catalytic pyrolysis of municipal solid waste.
This is the first study to investigate the effect of modified Saudi natural zeolite, on product quality and yield from catalytic pyrolysis of plastic waste. Saudi natural zeolite catalyst was modified via novel thermal activation (TA-NZ) at 550°C and acid activation (AA-NZ) with HNO3 to enhance its catalytic properties. The catalytic pyrolysis of different types of plastics waste (PS, PE, PP, and PET) as single or mixed in different ratios, in the presence of modified natural zeolite (NZ) catalysts in a small pilot scale pyrolysis reactor, was carried out for the first time. The quality and yield of pyrolysis products such as liquid oil, gas, and char were studied. The chemical composition of the liquid oil was analyzed by GC-MS. Furthermore, the potential and challenges of pyrolysis-based biorefineries have been discussed.
Materials and Methods
Feedstock Preparation and Reactor Start-Up
The plastic waste used as the feedstock in the catalytic pyrolysis process was collected from Jeddah and included grocery bags, disposable juice cups and plates, and drinking water bottles, which consist of polyethylene (PE), polypropylene (PP) polystyrene (PS), and polyethylene terephthalate (PET) plastics, respectively. The selection of these plastic materials was made based on the fact that they are the primary source of plastic waste produced in KSA. To obtain a homogenous mixture, all the waste samples were crushed into smaller pieces of around 2 cm2. The catalytic pyrolysis was carried out using an individual or mixture of these plastic wastes in different ratios (Table 1). 1000 g of feedstock was used, with 100 g of catalyst in each experiment. Saudi natural zeolite (NZ), collected from Harrat-Shama located in the northwest of Jeddah city, KSA (Nizami et al., 2016), was modified by thermal and acid treatment and used in these catalytic pyrolysis experiments. NZ was crushed into powder (<100 nm) in a ball-milling machine (Retsch MM 480) for 3 h using 20 Hz/sec, before modification and its usage in pyrolysis. For thermal activation (TA), NZ was heated in a muffle furnace at 550°C for 5 h, while for acidic activation (AA) NZ was soaked in a 0.1 M solution of nitric acid (HNO3) for 48 h and continuously shaken using an IKA HS 501 digital shaker with 50 rpm. Afterward, the sample was washed with deionized water until a normal pH was obtained.
The experiments were carried out in a small pilot-scale pyrolysis reactor at 450°C, using a heating rate of 10°C/min and reaction time of 75 min (Figure 1). The obtained yield of each pyrolysis product was calculated based on weight, after the completion of each experiment. The produced liquid oil characterization was carried out to investigate the effect of feedstock composition on the quality of liquid oil produced in the presence of modified NZ. TGA was carried out on feedstock to obtain the optimal process conditions such as temperature and reaction time (75 min) under controlled conditions. In TGA, a 10 μg of each type of plastic waste was taken and heated with a rate of 10°C from 25 to 900°C under a continuous flow of nitrogen (50 ml/min). The authors of this study have recently published work on the effect of feedstock composition and natural and synthetic zeolite catalysts without catalyst modification on different types of plastic waste (Miandad et al., 2017b; Rehan et al., 2017).

Figure 1. Small pilot scale pyrolysis reactor (Miandad et al., 2016b).
Experimental Setup
The small pilot scale reactor has the capability to be used as both a thermal and catalytic pyrolysis, using different feedstocks such as plastic and biomass materials (Figure 1). In this study, modified NZ catalysts were added in the reactor with the feedstock. The pyrolysis reactor can hold up to 20 L of feedstock and the maximum working safe temperature of up to 600°C can be achieved with the desired heating rates. Detailed parameters of the pyrolysis reactor were published earlier (Miandad et al., 2016b, 2017b). As the temperature increases above certain values, the plastic waste (organic polymers) converts into monomers that are transferred to the condenser, where these vapors are condensed into liquid oil. A continuous condensation system using a water bath and ACDelco Classic coolant was used to ensure the condensation temperature was kept below 10°C, and to ensure the maximum condensation of vapor to liquid oil. The produced liquid oil was collected from the oil collection tank, and further characterization was carried out to uncover its chemical composition and characteristics for other potential applications.
Analytical Methods
The pyrolysis oil was characterized using different techniques such as gas chromatography coupled with mass spectrophotometry (GC-MS), Fourier transform infrared spectroscopy (FT-IR),
Bomb Calorimeter and TGA (Mettler Toledo TGA/SDTA851) by adopting the standard ASTM methods. The functional groups in pyrolysis oil was analyzed by a FT-IR, Perkin Elmer's, UK instrument. The FT-IR analysis was conducted using a minimum of 32 scans with an average of 4 cm−1 IR signals within the frequency range of 500–4,000 cm−1.
The chemical composition of oil was studied using a GC-MS (Shimadzu QP-Plus 2010) with FI detector. A capillary GC 30 m long and 0.25 mm wide column coated with a 0.25 μm thick film of 5% phenyl-methylpolysiloxane (HP-5) was used. The oven was set at 50°C for 2 min and then increased up to 290°C using a 5°C/min heating rate. The temperature of the ion source and transfer line were kept at 230, and 300°C and splitless injection was applied at 290°C. The NIST08s mass spectral data library was used to identify the chromatographic peaks, and the peak percentages were assessed for their total ion chromatogram (TIC) peak area. The high heating values (HHV) of produced liquid oil obtained from different types of plastic waste were measured following the standard ASTM D 240 method with a Bomb Calorimeter (Parr 6200 Calorimeter) instrument, while production of gas was estimated using the standard mass balance formula, considering the difference of weights of liquid oil and char.
Results and Discussion
TGA Analysis of Feedstock
TGA was carried out for each type of plastic waste on an individual basis to determine the optimum temperature for thermal degradation. All types of plastic waste show similar degradation behavior with the rapid loss of weight of hydrocarbons within the narrow range of temperature (150–250°C) (Figure 2). The maximum degradation for each type of plastic waste was achieved within 420–490°C. PS and PP showed single step decomposition, while PE and PET showed a two-stage decomposition under controlled conditions. The single step decomposition corresponds to the presence of a carbon-carbon bond that promotes the random scission mechanism with the increase in temperature (Kim et al., 2006). PP degradation started at a very low temperature (240°C) compared to other feedstocks. Half of the carbon present in the chain of PP consists of tertiary carbon, which promotes the formation of carbocation during its thermal degradation process (Jung et al., 2010). This is probably the reason for achieving maximum PP degradation at a lower temperature. The PS initial degradation started at 330°C and maximum degradation was achieved at 470°C. PS has a cyclic structure, and its degradation under the thermal condition involves both random chain and end-chain scission, which enhances its degradation process (Demirbas, 2004; Lee, 2012).
PE and PET showed a two-stage decomposition process; the initial degradation started at lower temperatures followed by the other degradation stage at a higher temperature. PEs initial degradation started at 270°C and propagated slowly but gradually until the temperature reached 385°C. After that temperature, a sharp degradation was observed, and 95% degradation was achieved with a further increase of around 100°C. A similar two-stage degradation pattern was observed for PET plastic and the initial degradation started at 400°C with a sharp decrease in weight loss. However, the second degradation started at a slightly higher temperature (550°C). The initial degradation of PE and PET may be due to the presence of some volatile impurities such as the additive filler used during plastic synthesis (Dimitrov et al., 2013).
Various researchers have reported that PE and PET degradation requires higher temperatures compared to other plastics (Dimitrov et al., 2013; Rizzarelli et al., 2016). Lee (2012) reported that PE has a long chain branched structure and that its degradation occurs via random chain scission, thus requiring a higher temperature, while PET degradation follows the ester link random scission which results in the formation oligomers (Dziecioł and Trzeszczynski, 2000; Lecomte and Liggat, 2006). The initial degradation of PET was perhaps due to the presence of some volatile impurities such as diethylene glycol (Dimitrov et al., 2013). Literature reports that the presence of these volatile impurities further promotes the degradation process of polymers (McNeill and Bounekhel, 1991; Dziecioł and Trzeszczynski, 2000). The difference in TGA curves of various types of plastics could be due to their mesoporous structure (Chandrasekaran et al., 2015). In addition, Lopez et al. (2011) reported that the use of catalysts decreases the process temperature. Therefore, 450°C could be taken as the optimum temperature, in the presence of activated NZ, for catalytic pyrolysis of the aforementioned plastic waste.
Effect of Feedstock and Catalysts on Pyrolysis Products Yield
The effect of thermal and acid activation of NZ on the product yield of the pyrolysis process was examined (Figure 3). The catalytic pyrolysis of individual PS plastic using TA-NZ and AA-NZ catalysts showed the highest liquid oil yields of 70 and 60%, respectively, compared to all other types of individual and combined plastic waste studied. The high yield of liquid oil from catalytic pyrolysis of PS was also reported in several other studies (Siddiqui and Redhwi, 2009; Lee, 2012; Rehan et al., 2017). Siddiqui and Redhwi (2009) reported that PS has a cyclic structure, which leads to the high yield of liquid oil from catalytic pyrolysis. Lee (2012) reported that PS degradation occurred via both random-chain and end chain scissions, thus leading to the production of the stable benzene ring structure, which enhances further cracking and may increase liquid oil production. Furthermore, in the presence of acid catalysts, PS degradation followed a carbenium mechanism, which further underwent hydrogenation (inter/intramolecular hydrogen transfer) and β-scission (Serrano et al., 2000). In addition, PS degradation occurred at a lower temperature, compared to other plastics such as PE, due to its cyclic structure (Wu et al., 2014). On the other hand, the catalytic pyrolysis of PS produced a higher amount of char (24.6%) with AA-NZ catalyst than with TA-NZ (15.8%) catalyst. Ma et al. (2017) also reported the high production of char from the catalytic pyrolysis of PS with an acidic zeolite (Hβ) catalyst. The high char production numbers were due to the high acidity of the catalyst, which favors char production via intense secondary cross-linking reactions (Serrano et al., 2000).
The catalytic pyrolysis of PP produced higher liquid oil (54%) with the AA-NZ catalyst than the TA-NZ catalyst (40%) (Figure 3). On the other hand, the TA-NZ catalyst produced large amounts of gas (41.1%), which may be due to the lower catalytic activity of the TA-NZ catalyst. According to Kim et al. (2002) catalyst with low acidity and BET surface areas with microporous structures, favor the initial degradation of PP which may lead to the maximum production of gases. Obali et al. (2012) carried out pyrolysis of PP with an alumina-loaded catalyst and reported the maximum production of gas. Moreover, formation of carbocation during PP degradation, due to the presence of tertiary carbon in its carbon chain, may also favor gas production (Jung et al., 2010). Syamsiro et al. (2014) also reported that catalytic pyrolysis of PP and PS with an acid (HCL) activated natural zeolite catalyst produced more gases than the process with a thermally activated natural zeolite catalyst, due to its high acidity and BET surface area.
The catalytic pyrolysis of PE with TA-NZ and AA-NZ catalysts produced similar amounts of liquid oil (40 and 42%). However, the highest amounts of gases (50.8 and 47.0%) were produced from PE, using AA-NZ and TA-NZ respectively, compared to all other types of plastic studied. The char production was lowest in this case, 7.2 and 13.0% with AA-NZ and TA-NZ, respectively. Various studies also reported the lower production of char from the catalytic pyrolysis of PE (Xue et al., 2017). Lopez et al. (2011) reported that catalysts with high acidity enhanced the cracking of polymers during the catalytic pyrolysis. The increase in cracking, in the presence of a high acidic catalyst, promotes the production of gases (Miandad et al., 2016b, 2017a). Zeaiter (2014) carried out catalytic pyrolysis of PE with HBeta zeolite and reported 95.7% gas production due to the high acidity of the catalyst. Batool et al. (2016) also reported the maximum production of gas from catalytic pyrolysis of PE, with highly acidic ZSM-5 catalyst. According to Lee (2012) and Williams (2006), PE has a long chain carbon structure, and its degradation occurs randomly into smaller chain molecules via random chain scission, which may promote gas production. During the pyrolysis of PE, which holds the C-H and C-C bonds only, initially, macromolecule backbone breaking occurred and produced stable free-radicals. Further, the hydrogenation steps occurred, leading to the synthesis of secondary free-radicals (new stable C-H bond), which resulted into β-scission and produced an unsaturated group (Rizzarelli et al., 2016).
The catalytic pyrolysis of PP/PE (50/50% ratio) did not show any significant difference in the overall product yields when using both AA-NZ and TA-NZ. The liquid oil produced from the catalytic pyrolysis of PP/PE was 44 and 40% from TA-NZ and AA-NZ catalysts, respectively. A slight decrease in the liquid oil yield from AA-NZ could be due to its high acidity. Syamsiro et al. (2014) reported that AA-NZ with HCl has high acidity compared to TA-NZ, produced less liquid oil yield and had high production of gases. Overall catalytic pyrolysis of PP/PE produced the maximum amount of gas with low amounts of char. The high production of gas may be due to the presence of PP. The degradation of PP enhances the carbocation process due to the presence of tertiary carbon in its carbon chain (Jung et al., 2010). Furthermore, the degradation of PE in the presence of catalyst also favors the production of gas with a low yield of liquid oil. However, when PP and PE catalytic pyrolysis was carried out separately with PS, a significant difference was observed in the product yield.
There was a significant difference in the liquid oil yield of 54 and 34% for catalytic pyrolysis of PS/PP (50/50% ratio) with TA-NZ and AA-NZ catalysts, respectively. Similarly, a significant difference in the char yield of 20.3 and 35.2% was observed, whereas the high yield of gases were 25.7 and 30.8% using TA-NZ and AA-NZ catalysts, respectively. Lopez et al. (2011) and Seo et al. (2003) reported that a catalyst with high acidity promotes the cracking process and produces maximum gas production. Furthermore, the presence of PP also enhances gas production due to the carbocation process during degradation (Jung et al., 2010). Kim et al. (2002) reported that PP degradation produces maximum gas in the presence of acid catalysts.
The catalytic pyrolysis of PS with PE (50/50% ratio) in the presence of TA-NZ catalyst produced 44% liquid oil, however 52% liquid oil was obtained using the AA-NZ catalyst. Kiran et al. (2000) carried out pyrolysis of PS with PE at different ratios and reported that an increase in the concentration of PE decreased the liquid oil concentration with the increase in gas. The presence of PS with PE promotes the degradation process due to the production of an active stable benzene ring from PS (Miandad et al., 2016b). Wu et al. (2014) carried out TGA of PS with PE and observed two peaks, the first one for PS at a low temperature, followed by PE degradation at a high temperature. Moreover, PE degradation follows a free radical chain process and hydrogenation process, while PS follows a radical chain process including various steps (Kiran et al., 2000). Thus, even when considering the degradation phenomena, PS resulted in higher degradation compared to PE and produced stable benzene rings (McNeill et al., 1990).
Catalytic pyrolysis of PS/PE/PP (50/25/25% ratio) showed slightly lower liquid oil yields as compared to catalytic pyrolysis of all individual plastic types. The oil yield from both catalysts, TA-NZ and AA-NZ, in this case, is similar, 44 and 40%, respectively. The char production was higher (29.7%) with the AA-NZ catalyst than (19.0%) with the TA-NZ catalyst, which may be due to polymerization reactions (Wu and Williams, 2010). Furthermore, the addition of PET with PS, PE and PP (20/40/20/20% ratio) reduced the liquid oil yields down to 28 and 30% overall, using TA-NZ and AA-NZ catalysts, respectively, with higher fractions of char and gas. Demirbas (2004) carried out pyrolysis of PS/PE/PP and reported similar results for the product yield. Adnan et al. (2014) carried out catalytic pyrolysis of PS and PET using he Al-Al2O3 catalyst with ratios of 80/20% and reported only 37% liquid oil. Moreover, Yoshioka et al. (2004) reported the maximum production of gas and char with negligible liquid oil production from catalytic pyrolysis of PET. In addition, maximum char production was also reported when PET catalytic pyrolysis was carried out with other plastics (Bhaskar et al., 2004). The higher production of char from PET pyrolysis was due to the carbonization and condensation reactions during its pyrolysis at a high temperature (Yoshioka et al., 2004). In addition, the presence of the oxygen atom also favors the high production of char from catalytic pyrolysis of PET (Xue et al., 2017). Thilakaratne et al. (2016) reported that production of benzene-free radicals, with two activated carbons, is the precursor of catalytic coke from PET degradation.
Effect of Catalysts on the Composition of Liquid Oil
The chemical composition of liquid oil produced by the catalytic pyrolysis of different plastic waste using TA-NZ and AA-NZ catalysts were characterized by GC-MS (Figures 4, 5). The produced liquid oil composition is affected by different types of feedstock and catalysts used in the pyrolysis process (Miandad et al., 2016a,b,c). The liquid oil produced from the individual plastic types such as PS, PP and PE contained a mixture of aromatics, aliphatic and other hydrocarbon compounds. The aromatic compounds found in oil, from PS and PE, were higher than PP using the TA-NZ catalyst. The aromatic compounds increased in oil from PS and PP but reduced in PE when using the AA-NZ catalyst. The mesoporous and acidic catalyst leads to the production of shorter chain hydrocarbon due to its high cracking ability (Lopez et al., 2011). However, microporous and less acidic catalysts favor the production of long chain hydrocarbons as the cracking process occurred only on the outer surface of the catalysts. Overall, in the presence of catalysts, PE and PP follow the Random-chain scission mechanism, while PS follows the unzipping or end chain scission mechanism (Cullis and Hirschler, 1981; Peterson et al., 2001). The end-chain scission results in monomer production while random chain scission produces oligomers and monomers (Peterson et al., 2001).
The liquid oil produced from the catalytic pyrolysis of PE, when using both catalysts, produced mainly Naphthalene, Phenanthrene, Naphthalene, 2-ethenyl-, 1-Pentadecene, Anthracene, 2-methyl-, Hexadecane and so on (Figures 4A, 5A). These results agree with several other studies (Lee, 2012; Xue et al., 2017). The production of a benzene derivate reveals that TA-NZ enhances the process of aromatization compared to AA-NZ. Xue et al. (2017) reported that intermediate olefins produced from catalytic pyrolysis of PE, further aromatized inside the pores of catalysts. Nevertheless, the aromatization reaction further leads to the production of hydrogen atoms that may enhance the aromatization process. Lee (2012) reported that ZSM-5 produced more aromatic compounds compare to the mordenite catalyst, due to its crystalline structure.
There are two possible mechanisms which may involve the degradation of PE in the presence of a catalyst; hybrid ion abstraction due to the presence of Lewis sites or, due to the carbenium ion mechanism via the addition of a proton (Rizzarelli et al., 2016). Initially, degradation starts on the external surface of the catalysts and later proceeds with further degradation in the inner pores of the catalysts (Lee, 2012). However, microporous catalysts hinder the entrance of larger molecules and thus higher carbon chain compounds are produced from catalytic pyrolysis of PE with microporous catalysts. In addition, in the presence of acidic catalysts, due to carbenium mechanism, the formation of aromatic and olefin compound production may increase (Lee, 2012). Lin et al. (2004) reported highly reactive olefin production, as intermediate products during the catalytic pyrolysis of PE, that may favor the production of paraffin and aromatic compounds in produced liquid oil. Moreover, the presence of an acidic catalyst and free hydrogen atom may lead to alkylation of toluene and benzene, converting intermediate alkylated benzene to the production of naphthalene due to aromatization (Xue et al., 2017).
The liquid oil produced from catalytic pyrolysis of PS with TA-NZ and AA-NZ, contains different kinds of compounds. Alpha-Methylstyrene, Benzene, 1,1′-(2-butene-1,4-diyl)bis-, Bibenzyl, Benzene, (1,3-propanediyl), Phenanthrene, 2-Phenylnaphthalene and so on were the major compounds found in the produced liquid oil (Figures 4A, 5A). The liquid oil produced from catalytic pyrolysis of PS, with both activated catalysts, mainly contains aromatic hydrocarbons with some paraffins, naphthalene and olefin compounds (Rehan et al., 2017). However, in the presence of a catalyst, the maximum production of aromatic compounds was achieved (Xue et al., 2017). Ramli et al. (2011) also reported the production of olefins, naphthalene with aromatic compounds from catalytic pyrolysis of PS with Al2O3, supported with Cd and Sn catalysts. PS degradation starts with cracking on the outer surface of the catalyst and is then followed by reforming inside the pores of the catalyst (Uemichi et al., 1999). Initially, the cracking of polymer is carried out by the Lewis acid site on the surface of catalysts to produce carbocationic intermediates, which further evaporates or undergoes reforming inside the pores of the catalyst (Xue et al., 2017).
The catalytic pyrolysis of PS mainly produces styrene and its derivate as the major compounds in the produced liquid oil (Siddiqui and Redhwi, 2009; Rehan et al., 2017). Conversion of styrene into its derivate was increased in the presence of protonated catalysts due to hydrogenation (Kim et al., 2002). Shah and Jan (2015) and Ukei et al. (2000) reported that hydrogenation of styrene increased with the increase of the reaction temperature. Ogawa et al. (1982) carried out pyrolysis of PS with the alumina-silica catalyst at 300°C and found the hydrogenation of styrene to its derivate. Ramli et al. (2011) reported the possible degradation mechanism of PS on acid catalysts that may occur due to the attack of a proton associated with Bronsted acidic sites, resulting in the carbenium ion mechanism, which further undergoes β-scission and is later followed by hydrogen transfer. Moreover, cross-linking reaction was favored by strong Bronsted acidic sites and when this reaction occurred the completing cracking may decrease to some extent and enhance the production of char (Serrano et al., 2000). Furthermore, silica-alumina catalysts do not have strong Bronsted acidic sites, though it may not improve the cross-linking reaction but favor the hydrogenation process. Thus, it may be the reason that styrene was not found in the liquid oil, however, its derivate was detected at high quantities (Lee et al., 2001). Xue et al. (2017) also reported the dealkylation of styrene, due to the delay in evaporation inside the reactor, which may lead to an enhanced reforming process and result in the production of a styrene derivate. TA-NZ and AA-NZ contain a high amount of alumina and silica that leads to the hydrogenation of styrene to its derivate, resulting in the production of styrene monomers instead of styrene.
The catalytic pyrolysis of PP produced a complex mixture of liquid oil containing aromatics, olefins and naphthalene compounds. Benzene, 1,1′-(2-butene-1,4-diyl)bis-, benzene, 1,1′-(1,3-propanediyl)bis-, anthracene, 9-methyl-, naphthalene, 2-phenyl-, 1,2,3,4-tetrahydro-1-phenyl-, naphthalene, phenanthrene etc. were the major compounds found in the liquid oil (Figures 4A, 5A). These findings are in line with other studies that carried out catalytic pyrolysis of PP with various catalysts (Marcilla et al., 2004). Furthermore, degradation of PP with AA-NZ resulted in the maximum production of phenol compounds. The higher production was perhaps due to the presence of high acidic sites, as it favors phenol compound production. Moreover, the presence of a high acidic site on catalysts enhanced the oligomerization, aromatization and deoxygenation mechanism that led to the production of poly-aromatic and naphthalene compounds. Dawood and Miura (2002) also reported the high production of these compounds from the catalytic pyrolysis of PP with a high acidic modified HY-zeolite.
The composition of oil from the catalytic pyrolysis of PP with PE contains compounds found in the oil from both individual plastic type feedstocks. Miandad et al. (2016b) reported that feedstock composition also affects the quality and chemical composition of the oil. The produced liquid oil from catalytic pyrolysis of PE/PP contains aromatic, olefin, and naphthalene compounds. The major compounds found were; benzene, 1,1′-(1,3-propanediyl)bis-, mono(2-ethylhexyl) ester, 1,2-benzenedicarboxylic acid, anthracene, pentadecane, phenanthrene, 2-phenylnaphthalene and so on (Figures 4B, 5B). Jung et al. (2010) reported that the aromatic production from PP/PE catalytic pyrolysis might follow the Diels–Alder reaction mechanism and is then followed by dehydrogenation. Furthermore, catalytic pyrolysis of PP and PE carried out individually with PS, mainly produced aromatic compounds due to the presence of PS. The produced liquid oil from PS/PP contains benzene, 1,1′-(1,3-propanediyl)bis, 1,2-benzenedicarboxylic acid, disooctyl ester, bibenzyl, phenanthrene, 2-phenylnaphthalene, benzene, (4-methyl-1-decenyl)- and so on (Figures 4A, 5A). PS catalytic pyrolysis with PE mainly produced liquid oil with major compounds of azulene, naphthalene, 1-methyl-, naphthalene, 2-ethenyl, benzene, 1,1′-(1,3-propanediyl)bis-, phenanthrene, 2-phenylnaphthalene, benzene, 1,1′-(1-methyl-1,2-ethanediyl)bis- and some other compounds as well (Figures 4B, 5B). Miskolczi et al. (2006) carried out pyrolysis of PS with PE with a ratio of 10 and 90%, respectively, and reported the maximum production of aromatics even at a very low ratio of PS. Miandad et al. (2016b) reported that thermal pyrolysis of PE with PS without a catalyst, resulted in the conversion of PE into liquid oil with a high composition of aromatics. However thermal pyrolysis of the only PE without a catalyst converted it into wax instead of liquid oil due to its strong long chain branched structure (Lee, 2012; Miandad et al., 2016b). Wu et al. (2014) carried out TGA of PS with PE and reported that the presence of PS favors the degradation of PE, due to the production of stable benzene rings.
The chemical composition of pyrolysis oil, by different functional groups, was studied using FT-IR. The obtained data revealed the presence of aromatics and aliphatic functional groups in the oil (Figures 6, 7). A very strong peak at 696 cm−1 was observed in most of the liquid oils obtained using both catalysts, which corresponds to the high concentration of aromatic compounds. Two more peaks, that are obvious, were visible at around 1,456 and 1,495 cm−1 for C-C with single and double bonds, corresponding to aromatic compounds. Furthermore, at the end of the spectrum, strong peaks at 2,850, 2,923, and 2,958 cm−1 were observed in all types of liquid oils except the PS, corresponding to the C-H stretch of alkanes compounds. Overall, the liquid oil obtained from catalytic pyrolysis of different plastic waste using the AA-NZ catalyst, showed more peaks than the samples from the TA-NZ catalysts. These extra peaks corresponded to aromatics, alkanes and alkene compounds. This indicates that, as expected, the AA-NZ had better catalytic properties than the TA-NZ. Various researchers have reported similar results, that liquid oil produced from PS was dominant with aromatics. Tekin et al. (2012) and Panda and Singh (2013) also reported the presence of aromatics with some alkanes and alkenes from catalytic pyrolysis of PP. Kunwar et al. (2016) carried out the thermal and catalytic pyrolysis of PE and reported that produced liquid oil contained alkanes and alkenes as a major functional group. Overall, the FT-IR analysis provided more insight into the chemical composition of liquid oil produced, from catalytic pyrolysis of different plastic waste, using modified NZ catalysts and further confirmed our GC-MS results.
Potential Applications of Pyrolysis Products
The liquid oil produced from the catalytic pyrolysis of different types of plastic feedstock has a high number of aromatic, olefin, and naphthalene compounds that are found in petroleum products. Moreover, the HHV of the produced liquid oil has been found in the range of 41.7–44.2 MJ/kg (Table 2) which is very close to the energy value of conventional diesel. The lowest HHV of 41.7 MJ/ kg was found in liquid oil obtained from PS using the TA-NZ catalyst, whereas the highest HHV of 44.2 MJ/kg was from PS/PE/PP using the AA-NZ catalyst. Thus, the pyrolysis liquid oil produced from various plastic wastes has the potential to be used as an alternative source of energy. According to Lee et al. (2015) and Rehan et al. (2016), the production of electricity is achievable using pyrolysis liquid oil in a diesel engine. Saptoadi and Pratama (2015) successfully used pyrolytic liquid oil as an alternative in a kerosene stove. Moreover, the produced aromatic compounds can be used as raw material for polymerization in various chemical industries (Sarker and Rashid, 2013; Shah and Jan, 2015). Furthermore, various researchers utilized the produced liquid oil as transportation fuel after blending with conventional diesel at different ratios. The studies were carried out to explore the potential of produced liquid oil in the context of engine performance and vehicle exhaust emission. Nileshkumar et al. (2015) and Lee et al. (2015) reported that 20:80% blend ratio of pyrolytic liquid oil and conventional diesel, respectively, gave similar engine performance results than conventional diesel. Moreover, at the same blended ratio the exhaust emissions were also similar, however the exhaust emissions increased with the increase in the blended amount of pyrolysis oil (Frigo et al., 2014; Mukherjee and Thamotharan, 2014).
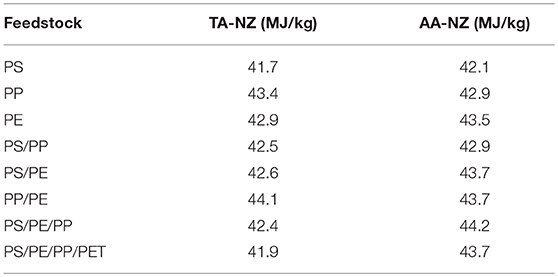
Table 2. High Heating Values (HHV) of pyrolysis oil from various feedstocks using TA-NZ and AA-NZ catalysts.
The residue (char) left after the pyrolysis process can be utilized for several environmental applications. Several researchers activated the char via steam and thermal activation (Lopez et al., 2009; Heras et al., 2014). The activation process increased the BET surface area and reduced the pore size of the char (Lopez et al., 2009). Furthermore, Bernando (2011) upgraded the plastic char with biomaterial and carried out the adsorption (3.6–22.2 mg/g) of methylene blue dye from wastewater. Miandad et al. (2018) used the char obtained from pyrolysis of PS plastic waste to synthesize a novel carbon-metal double-layered oxides (C/MnCuAl-LDOs) nano-adsorbent for the adsorption of Congo red (CR) in wastewater. Furthermore, the char can be used as a raw material for the production of activated carbon as well.
Limitations of GC-MS Analysis of Pyrolysis Oil
There are some limitations in conducting the accurate quantitative analysis of chemical components in pyrolysis oil using GC-MS. In this study, we used the mass percentage of different chemicals found in oil samples, calculated based on the peak areas identified by a normal phase DP5-MS column and FID. The identified peaks were matched with the NIST and mass bank spectra library. The compounds were chosen based on the similarity index (SI > 90%). Further comparison with known (CRM) standards enabled confirmation of the identified compounds. The used column and detectors were limited only with hydrocarbons. In reality however, oil from most plastic waste has a complex chemical structure and may contain other groups of unidentified chemicals such as sulfur, nitrogen, and oxygen-containing hydrocarbons. This is why a more in-depth and accurate qualitative chemical analysis is needed to fully understand the chemistry of pyrolysis oil, using advanced calibration and standardization and using different MS detectors like SCD and NCD as well as different GC columns.
The Potential and Challenges of Pyrolysis Based Biorefineries
Waste biorefineries are attracting tremendous attention as a solution to convert MSW and other biomass waste into a range of products such as fuels, power, heat and other valuable chemicals and materials. Different types of biorefineries, such as an agriculture-based biorefinery, animal waste biorefinery, wastewater biorefinery, algae-based biorefinery, plastic waste refinery, forestry-based biorefinery, industrial waste biorefinery, and Food waste biorefinery etc., can be developed depending on the type and source of waste (Gebreslassie et al., 2013; De Wild et al., 2014; Nizami et al., 2017a,b; Waqas et al., 2018). These biorefineries can play a significant role to reduce waste-related environmental pollution and GHG emissions. Furthermore, they generate substantial economic benefits and can help achieve a circular economy in any country.
A pyrolysis based biorefinery can be developed to treat a range of biomass waste and plastic waste to produce liquid and gas fuels, energy, biochar, and other higher value chemicals using an integrated approach. The integrated approach helps to achieve maximum economic and environmental benefits with minimal waste production. There are many challenges and room for improvement in pyrolysis-based biorefineries, that need to be addressed and optimized to ensure maximum benefits. Although pyrolysis oil holds more energy than coal and some other fuels, pyrolysis itself is an energy-intensive process, and the oil product requires more energy to be refined (Inman, 2012). This means that pyrolysis oil may not be much better than conventional diesel or other fossil-based fuels in terms of GHG emissions, though much detailed research studies on mass and energy balance across the whole process's boundaries are needed to confirm this. To overcome these process energy requirements, more advanced technologies can be developed using the integration of renewable energies such as solar or hydro with pyrolysis-based biorefineries, to achieve maximum economic and environmental benefits.
The availability of plastic and biomass waste streams as feedstocks for pyrolysis based biorefineries, is another major challenge, since recycling is not currently very efficient, especially in the developing countries. The gases produced from pyrolysis of some plastic waste such as PVC are toxic, and therefore pyrolysis emission treatment technology has to be further refined to achieve maximum environmental benefits. The pyrolysis oil obtained from various plastic types need to be cleaned significantly before it is used in any application, to ensure minimal environmental impact. The high aromatic contents of the pyrolysis oil is good and some aromatic compounds such as benzene, toluene, and styrene can be refined and sold in an already established market. However, some of the aromatic hydrocarbons are known carcinogens and can cause serious human health and environmental damage. Serious consideration is therefore needed in this regard.
Other aspects for optimization of pyrolysis based biorefineries, such as new emerging advanced catalysts including nano-catalysts, have to be developed and applied in pyrolysis processes in order to increase the quality and yield of products, and to optimize the overall process. The market for pyrolysis based biorefinery products should be created/ expanded to attract further interest and funding, in order to make this concept more practical and successful. Similarly, more focus is needed to conduct further research and development work on enriching the biorefinery concept and to tap into its true potential. Furthermore, it is vital to conduct a detailed economic and environmental impact assessment of biorefineries during a design stage, using specialized tools such as the life-cycle assessment (LCA). The LCA can analyze the environmental impact of the biorefinery and all products by conducting detailed energy and material balances of all life stages including raw material extraction and processing, manufacturing, product distribution, use, maintenance, and disposal/recycling. The outcomes of LCA will help to determine the sustainability of biorefineries, which is crucial in making the right decision.
Conclusions
Catalytic pyrolysis is a promising technique to convert plastic waste into liquid oil and other value-added products, using a modified natural zeolite (NZ) catalyst. The modification of NZ catalysts was carried out by novel thermal (TA) and acidic (AA) activation that enhanced their catalytic properties. The catalytic pyrolysis of PS produced the highest liquid oil (70 and 60%) compared to PP (40 and 54%) and PE (40 and 42%), using the TA-NZ and AA-NZ catalysts, respectively. The chemical composition of the pyrolysis oil was analyzed using GC-MS, and it was found that most of the liquid oil produced a high aromatic content with some aliphatic and other hydrocarbon compounds. These results were further confirmed by the FT-IR analysis showing clear peaks corresponding to aromatic and other hydrocarbon functional groups. Furthermore, liquid oil produced from different types of plastic waste had higher heating values (HHV) in the range of 41.7–44.2 MJ/kg similar to that of conventional diesel. Therefore, it has the potential to be used in various energy and transportation applications after further treatment and refining. This study is a step toward developing pyrolysis-based biorefineries. Biorefineries have a great potential to convert waste into energy and other valuable products and could help to achieve circular economies. However, there are many technical, operational, and socio-economic challenges, as discussed above, that need to be overcome in order to achieve the maximum economic and environmental benefits of biorefineries.
Data Availability
All datasets generated for this study are included in the manuscript and/or the supplementary files.
Author Contributions
RM performed the pyrolysis experiments and helped in manuscript write up. HK, JD, JG, and AH have carried out the detailed characterization of the process products. MR and ASA have analyzed the data and written parts of the manuscript. MAB, MR, and A-SN have corrected and edited the manuscript. ASA and IMII supported the project financially and technically.
Conflict of Interest Statement
The authors declare that the research was conducted in the absence of any commercial or financial relationships that could be construed as a potential conflict of interest.
Acknowledgments
MR and A-SN acknowledge the Center of Excellence in Environmental Studies (CEES), King Abdulaziz University (KAU), Jeddah, KSA and the Ministry of Education, KSA for financial support under Grant No. 2/S/1438. Authors are also thankful to Deanship of Scientific Research (DSR) at KAU for their financial and technical support to CEES.
References
Adnan, A., Shah, J., and Jan, M. R. (2014). Polystyrene degradation studies using Cu supported catalysts. J. Anal. Appl. Pyrol. 109, 196–204. doi: 10.1016/j.jaap.2014.06.013
Aguado, J., Sotelo, J. L., Serrano, D. P., Calles, J. A., and Escola, J. M. (1997). Catalytic conversion of polyolefins into liquid fuels over MCM-41: comparison with ZSM-5 and amorphous SiO2–Al2O3. Ener fuels 11, 1225–1231. doi: 10.1021/ef970055v
Alexandra, L. C. (2012). Municipal Solid Waste: Turning a Problem Into Resourceewaste: The Challenges Facing Developing Countries, Urban Specialist. World Bank. 2–4 p.
Batool, M., Shah, A. T., Imran Din, M., and Li, B. (2016). Catalytic pyrolysis of low density polyethylene using cetyltrimethyl ammonium encapsulated monovacant keggin units and ZSM-5. J. Chem. 2016:2857162. doi: 10.1155/2016/2857162
Bernando, M. (2011). “Physico-chemical characterization of chars produced in the co-pyrolysis of wastes and possible routes of valorization,” in Chemical Engineering (Lisboa: Universidade Nova de Lisboa), 27–36.
Bhaskar, T., Kaneko, J., Muto, A., Sakata, Y., Jakab, E., Matsui, T., et al. (2004). Pyrolysis studies of PP/PE/PS/PVC/HIPS-Br plastics mixed with PET and dehalogenation (Br, Cl) of the liquid products. J. Anal. Appl. Pyrolysis 72, 27–33. doi: 10.1016/j.jaap.2004.01.005
Chandrasekaran, S. R., Kunwar, B., Moser, B. R., Rajagopalan, N., and Sharma, B. K. (2015). Catalytic thermal cracking of postconsumer waste plastics to fuels. 1. Kinetics and optimization. Energy Fuels 29, 6068–6077. doi: 10.1021/acs.energyfuels.5b01083
Cullis, C. F., and Hirschler, M. M. (1981). The Combustion of Organic Polymers. Vol. 5. London: Oxford University Press.
Dawood, A., and Miura, K. (2002). Catalytic pyrolysis of c-irradiated polypropylene (PP) over HY-zeolite for enhancing the reactivity and the product selectivity. Polym. Degrad. Stab. 76, 45–52. doi: 10.1016/S0141-3910(01)00264-6
De Wild, P. J., Huijgen, W. J., and Gosselink, R. J. (2014). Lignin pyrolysis for profitable lignocellulosic biorefineries. Biofuels Bioprod. Biorefining 8, 645–657. doi: 10.1002/bbb.1474
Demirbas, A. (2004). Pyrolysis of municipal plastic wastes for recovery of gasoline-range hydrocarbons. J. Anal. Appl. Pyrolysis 72, 97–102. doi: 10.1016/j.jaap.2004.03.001
Dimitrov, N., Krehula, L. K., Siročić, A. P., and Hrnjak-Murgić, Z. (2013). Analysis of recycled PET bottles products by pyrolysis-gas chromatography. Polym. Degrad. Stab. 98, 972–979. doi: 10.1016/j.polymdegradstab.2013.02.013
Dziecioł, M., and Trzeszczynski, J. (2000). Volatile products of poly (ethylene terephthalate) thermal degradation in nitrogen atmosphere. J. Appl. Polym. Sci. 77, 1894–1901. doi: 10.1002/1097-4628(20000829)77:9<1894::AID-APP5>3.0.CO;2-Y
Frigo, S., Seggiani, M., Puccini, M., and Vitolo, S. (2014). Liquid fuel production from waste tyre pyrolysis and its utilisation in a Diesel engine. Fuel 116, 399–408. doi: 10.1016/j.fuel.2013.08.044
Gaca, P., Drzewiecka, M., Kaleta, W., Kozubek, H., and Nowinska, K. (2008). Catalytic degradation of polyethylene over mesoporous molecular sieve MCM-41 modified with heteropoly compounds. Polish J. Environ. Stud. 17, 25–35.
Gandidi, I. M., Susila, M. D., Mustofa, A., and Pambudi, N. A. (2018). Thermal–Catalytic cracking of real MSW into Bio-Crude Oil. J. Energy Inst. 91, 304–310. doi: 10.1016/j.joei.2016.11.005
Gebreslassie, B. H., Slivinsky, M., Wang, B., and You, F. (2013). Life cycle optimization for sustainable design and operations of hydrocarbon biorefinery via fast pyrolysis, hydrotreating and hydrocracking. Comput. Chem. Eng. 50, 71–91. doi: 10.1016/j.compchemeng.2012.10.013
Heras, F., Jimenez-Cordero, D., Gilarranz, M. A., Alonso-Morales, N., and Rodriguez, J. J. (2014). Activation of waste tire char by cyclic liquid-phase oxidation. Fuel Process. Technol. 127, 157–162. doi: 10.1016/j.fuproc.2014.06.018
Jung, S. H., Cho, M. H., Kang, B. S., and Kim, J. S. (2010). Pyrolysis of a fraction of waste polypropylene and polyethylene for the recovery of BTX aromatics using a fluidized bed reactor. Fuel Process. Technol. 91, 277–284. doi: 10.1016/j.fuproc.2009.10.009
Kim, H. S., Kim, S., Kim, H. J., and Yang, H. S. (2006). Thermal properties of bio-flour-filled polyolefin composites with different compatibilizing agent type and content. Thermochim. Acta 451, 181–188. doi: 10.1016/j.tca.2006.09.013
Kim, J. R., Yoon, J. H., and Park, D. W. (2002). Catalytic recycling of the mixture of polypropylene and polystyrene. Polym. Degrad. Stab. 76, 61–67. doi: 10.1016/S0141-3910(01)00266-X
Kiran, N., Ekinci, E., and Snape, C. E. (2000). Recyling of plastic wastes via pyrolysis. Resour. Conserv. Recycl. 29, 273–283. doi: 10.1016/S0921-3449(00)00052-5
Kunwar, B., Moser, B. R., Chandrasekaran, S. R., Rajagopalan, N., and Sharma, B. K. (2016). Catalytic and thermal depolymerization of low value post-consumer high density polyethylene plastic. Energy 111, 884–892. doi: 10.1016/j.energy.2016.06.024
Lecomte, H. A., and Liggat, J. J. (2006). Degradation mechanism of diethylene glycol units in a terephthalate polymer. Polym. Degrad. Stab. 91, 681–689. doi: 10.1016/j.polymdegradstab.2005.05.028
Lee, K. H. (2012). Effects of the types of zeolites on catalytic upgrading of pyrolysis wax oil. J. Anal. Appl. Pyrol. 94, 209–214. doi: 10.1016/j.jaap.2011.12.015
Lee, S., Yoshida, K., and Yoshikawa, K. (2015). Application of waste plastic pyrolysis oil in a direct injection diesel engine: For a small scale non-grid electrification. Energy Environ. Res. 5:18. doi: 10.5539/eer.v5n1p18
Lee, S. Y., Yoon, J. H., Kim, J. R., and Park, D. W. (2001). Catalytic degradation of polystyrene over natural clinoptilolite zeolite. Polym. Degrad. Stab. 74, 297–305. doi: 10.1016/S0141-3910(01)00162-8
Lin, Y. H., Yang, M. H., Yeh, T. F., and Ger, M. D. (2004). Catalytic degradation of high density polyethylene over mesoporous and microporous catalysts in a fluidised-bed reactor. Polym. Degrad. Stab. 86, 121–128. doi: 10.1016/j.polymdegradstab.2004.02.015
Lopez, A., Marco d, I., Caballero, B. M., Laresgoiti, M. F., Adrados, A., and Torres, A. (2011). Pyrolysis of municipal plastic waste II: influence of raw material composition under catalytic conditions. Waste Manag. 31, 1973–1983. doi: 10.1016/j.wasman.2011.05.021
Lopez, G., Olazar, M., Artetxe, M., Amutio, M., Elordi, G., and Bilbao, J. (2009). Steam activation of pyrolytic tyre char at different temperatures. J. Anal. Appl. Pyrol. 85, 539–543. doi: 10.1016/j.jaap.2008.11.002
Ma, C., Yu, J., Wang, B., Song, Z., Xiang, J., Hu, S., et al. (2017). Catalytic pyrolysis of flame retarded high impact polystyrene over various solid acid catalysts. Fuel Process. Technol. 155, 32–41. doi: 10.1016/j.fuproc.2016.01.018
Marcilla, A., Beltrán, M. I., Hernández, F., and Navarro, R. (2004). HZSM5 and HUSY deactivation during the catalytic pyrolysis of polyethylene. Appl. Catal. A Gen. 278, 37–43. doi: 10.1016/j.apcata.2004.09.023
McNeill, I. C., and Bounekhel, M. (1991). Thermal degradation studies of terephthalate polyesters: 1. Poly (alkylene terephthalates). Polymer Degrad. Stab. 34, 187–204. doi: 10.1016/0141-3910(91)90119-C
McNeill, I. C., Zulfiqar, M., and Kousar, T. (1990). A detailed investigation of the products of the thermal degradation of polystyrene. Polym. Degrad. Stab. 28, 131–151. doi: 10.1016/0141-3910(90)90002-O
Miandad, R., Barakat, M. A., Aburiazaiza, A. S., Rehan, M., Ismail, I. M. I., and Nizami, A. S. (2017b). Effect of plastic waste types on pyrolysis liquid oil. Int. Biodeterior. Biodegrad. 119, 239–252. doi: 10.1016/j.ibiod.2016.09.017
Miandad, R., Barakat, M. A., Aburiazaiza, A. S., Rehan, M., and Nizami, A. S. (2016a). Catalytic pyrolysis of plastic waste: a review. Process Safety Environ. Protect. 102, 822–838. doi: 10.1016/j.psep.2016.06.022
Miandad, R., Barakat, M. A., Rehan, M., Aburiazaiza, A. S., Ismail, I. M. I., and Nizami, A. S. (2017a). Plastic waste to liquid oil through catalytic pyrolysis using natural and synthetic zeolite catalysts. Waste Manag. 69, 66–78. doi: 10.1016/j.wasman.2017.08.032
Miandad, R., Kumar, R., Barakat, M. A., Basheer, C., Aburiazaiza, A. S., Nizami, A. S., et al. (2018). Untapped conversion of plastic waste char into carbon-metal LDOs for the adsorption of Congo red. J Colloid Interface Sci. 511, 402–410. doi: 10.1016/j.jcis.2017.10.029
Miandad, R., Nizami, A. S., Rehan, M., Barakat, M. A., Khan, M. I., Mustafa, A., et al. (2016b). Influence of temperature and reaction time on the conversion of polystyrene waste to pyrolysis liquid oil. Waste Manag. 58, 250–259. doi: 10.1016/j.wasman.2016.09.023
Miandad, R., Rehan, M., Nizami, A. S., Barakat, M. A. E. F., and Ismail, I. M. (2016c). “The energy and value- added products from pyrolysis of waste plastics,” in Recycling of Solid Waste for Biofuels and Bio- Chemicals, eds O. P. Karthikeyan, K. H. Subramanian, and S. Muthu (Singapore: Springer), 333–355.
Miskolczi, N., Bartha, L., and Deak, G. (2006). Thermal degradation of polyethylene and polystyrene from the packaging industry over different catalysts into fuel-like feed stocks. Polym. Degrad. Stab. 91, 517–526. doi: 10.1016/j.polymdegradstab.2005.01.056
Mukherjee, M. K., and Thamotharan, P. C. (2014). Performance and emission test of several blends of waste plastic oil with diesel and ethanol on four stroke twin cylinder diesel engine. IOSR J. Mech. Civil Eng. 11, 2278–1684. doi: 10.9790/1684-11214751
Nileshkumar, K. D., Jani, R. J., Patel, T. M., and Rathod, G. P. (2015). Effect of blend ratio of plastic pyrolysis oil and diesel fuel on the performance of single cylinder CI engine. Int. J. Sci. Technol. Eng. 1, 2349–2784.
Nizami, A. S., Ouda, O. K. M., Rehan, M., El-Maghraby, A. M. O., Gardy, J., Hassanpour, A., et al. (2016). The potential of Saudi Arabian natural zeolites in energy recovery technologies. Energy 108, 162–171. doi: 10.1016/j.energy.2015.07.030
Nizami, A. S., Rehan, M., Waqas, M., Naqvi, M., Ouda, O. K. M., Shahzad, K., et al. (2017a). Waste biorefineries: enabling circular economies in developing countries. Bioresour. Technol. 241, 1101–1117. doi: 10.1016/j.biortech.2017.05.097
Nizami, A. S., Shahzad, K., Rehan, M., Ouda, O. K. M., Khan, M. Z., Ismail, I. M. I., et al. (2017b). Developing waste biorefinery in makkah: a way forward to convert urban waste into renewable energy. Appl. Energy. 186, 189–196. doi: 10.1016/j.apenergy.2016.04.116
Obali, Z., Sezgi, N. A., and Doğu, T. (2012). Catalytic degradation of polypropylene over alumina loaded mesoporous catalysts. Chem. Eng. J. 207, 421–425. doi: 10.1016/j.cej.2012.06.146
Ogawa, T., Kuroki, T., Ide, S., and Ikemura, T. (1982). Recovery of indan derivatives from polystyrene waste. J. Appl. Polym. Sci. 27, 857–869. doi: 10.1002/app.1982.070270306
Panda, A. K., and Singh, R. K. (2013). Experimental optimization of process for the thermo-catalytic degradation of waste polypropylene to liquid fuel. Adv. Energy Eng. 1, 74–84.
Peterson, J. D., Vyazovkin, S., and Wight, C. A. (2001). Kinetics of the thermal and thermo-oxidative degradation of polystyrene, polyethylene and poly (propylene). Macromol. Chem. Phys. 202, 775–784. doi: 10.1002/1521-3935(20010301)202:6<775::AID-MACP775>3.0.CO;2-G
Ramli, M. R., Othman, M. B. H., Arifin, A., and Ahmad, Z. (2011). Cross-link network of polydimethylsiloxane via addition and condensation (RTV) mechanisms. Part I: synthesis and thermal properties. Polym. Degrad. Stab. 96, 2064–2070. doi: 10.1016/j.polymdegradstab.2011.10.001
Ratnasari, D. K., Nahil, M. A., and Williams, P. T. (2017). Catalytic pyrolysis of waste plastics using staged catalysis for production of gasoline range hydrocarbon oils. J. Anal. Appl. Pyrolysis 124, 631–637. doi: 10.1016/j.jaap.2016.12.027
Rehan, M., Miandad, R., Barakat, M. A., Ismail, I. M. I., Almeelbi, T., Gardy, J., et al. (2017). Effect of zeolite catalysts on pyrolysis liquid oil. Int. Biodeterior. Biodegrad. 119, 162–175. doi: 10.1016/j.ibiod.2016.11.015
Rehan, M., Nizami, A. S., Shahzad, K., Ouda, O. K. M., Ismail, I. M. I., Almeelbi, T., et al. (2016). Pyrolytic liquid fuel: a source of renewable energy in Makkah. Energy Sources A 38, 2598–2603. doi: 10.1080/15567036.2016.1153753
Rizzarelli, P., Rapisarda, M., Perna, S., Mirabella, E. F., La Carta, S., Puglisi, C., et al. (2016). Determination of polyethylene in biodegradable polymer blends and in compostable carrier bags by Py-GC/MS and TGA. J. Anal. Appl. Pyrolysis 117,72–81. doi: 10.1016/j.jaap.2015.12.014
Saptoadi, H., and Pratama, N. N. (2015). Utilization of plastics waste oil as partial substitute for kerosene in pressurized cookstoves. Int. J. Environ. Sci. Dev. 6, 363–368. doi: 10.7763/IJESD.2015.V6.619
Sarker, M., and Rashid, M. M. (2013). Waste plastics mixture of polystyrene and polypropylene into light grade fuel using Fe2O3 catalyst. Int. J. Renew. Energy Technol. Res. 2, 17–28.
Seo, Y. H., Lee, K. H., and Shin, D. H. (2003). Investigation of catalytic degradation of high density, polyethylene by hydrocarbon group type analysis. J. Anal. Appl. Pyrol. 70, 383–398. doi: 10.1016/S0165-2370(02)00186-9
Serrano, D. P., Aguado, J., and Escola, J. M. (2000). Catalytic conversion of polystyrene over HMCM-41, HZSM-5 and amorphous SiO2–Al2O3: comparison with thermal cracking. Appl. Catal. B:Environ. 25, 181–189. doi: 10.1016/S0926-3373(99)00130-7
Serrano, D. P., Aguado, J., and Escola, J. M. (2012). Developing advanced catalysts for the conversion of polyolefinic waste plastics into fuels and chemicals. ACS Catal. 2, 1924–1941. doi: 10.1021/cs3003403
Shah, J., and Jan, M. R. (2015). Effect of polyethylene terephthalate on the catalytic pyrolysis of polystyrene: Investigation of the liquid products. J. Taiwan Inst. Chem. Eng. 51, 96–102. doi: 10.1016/j.jtice.2015.01.015
Siddiqui, M. N., and Redhwi, H. H. (2009). Pyrolysis of mixed plastics for the recovery of useful products. Fuel Process. Technol. 90, 545–552. doi: 10.1016/j.fuproc.2009.01.003
Sriningsih, W., Saerodji, M. G., Trisunaryanti, W., Armunanto, R., and Falah, I. I. (2014). Fuel production from LDPE plastic waste over natural zeolite supported Ni, Ni-Mo, Co and Co-Mo metals. Proc. Environ. Sci. 20, 215–224. doi: 10.1016/j.proenv.2014.03.028
Syamsiro, M., Cheng, S., Hu, W., Saptoadi, H., Pratama, N. N., Trisunaryanti, W., et al. (2014). Liquid and gaseous fuel from waste plastics by sequential pyrolysis and catalytic reforming processes over indonesian natural zeolite catalysts. Waste Technol. 2, 44–51. doi: 10.12777/wastech.2.2.44-51
Tekin, K., Akalin, M. K., Kadi, C., and Karagöz, S. (2012). Catalytic degradation of waste polypropylene by pyrolysis. J. Energy Ins. 85, 150–155. doi: 10.1179/1743967112Z.00000000029
Thilakaratne, R., Tessonnier, J. P., and Brown, R. C. (2016). Conversion of methoxy and hydroxyl functionalities of phenolic monomers over zeolites. Green Chem. 18, 2231–2239. doi: 10.1039/c5gc02548f
Uemichi, Y., Hattori, M., Itoh, T., Nakamura, J., and Sugioka, M. (1998). Deactivation behaviors of Zeolite and Silica– Alumina catalysts in the degradation of polyethylene. Ind. Eng. Chem. Res. 37, 867–872. doi: 10.1021/ie970605c
Uemichi, Y., Nakamura, J., Itoh, T., Sugioka, M., Garforth, A. A., and Dwyer, J. (1999). Conversion of polyethylene into gasoline-range fuels by two-stage catalytic degradation using Silica–Alumina and HZSM-5 Zeolite. Ind. Eng. Chem. Res. 38, 385–390. doi: 10.1021/ie980341+
Ukei, H., Hirose, T., Horikawa, S., Takai, Y., Taka, M., Azuma, N., et al. (2000). Catalytic degradation of polystyrene into styrene and a design of recyclable polystyrene with dispersed catalysts. Catal. Today 62, 67–75. doi: 10.1016/S0920-5861(00)00409-0
Waqas, M., Rehan, M., Aburiazaiza, A. S., and Nizami, A. S. (2018). “Chapter 17-Wastewater Biorefinery based on the microbial electrolysis cell: opportunities and challenges,” in Progress and Recent Trends in Microbial Fuel Cells, eds K. Dutta and P. Kundu (New York, NY: Elsevier Inc.), 347–374. doi: 10.1016/B978-0-444-64017-8.00017-8
Williams, P. T. (2006). “Yield and composition of gases and oils/waxes from the feedstock recycling of waste plastic.” In Feeds Tock Recycling and Pyrolysis of Waste Plastics: Converting Waste Plastics into Diesel and Other Fuels, eds J. Scheirs and W. Kaminsky (West Sussex: John Wiley & Sons Press), 285–309.
Wu, C., and Williams, P. T. (2010). Pyrolysis–gasification of plastics, mixed plastics and real-world plastic waste with and without Ni–Mg–Al catalyst. Fuel 89, 3022–3032. doi: 10.1016/j.fuel.2010.05.032
Wu, J., Chen, T., Luo, X., Han, D., Wang, Z., and Wu, J. (2014). TG/FTIR analysis on co-pyrolysis behavior of PE, PVC and PS. Waste Manag. 34, 676–682. doi: 10.1016/j.wasman.2013.12.005
Xue, Y., Johnston, P., and Bai, X. (2017). Effect of catalyst contact mode and gas atmosphere during catalytic pyrolysis of waste plastics. Energy Conv. Manag. 142, 441–451. doi: 10.1016/j.enconman.2017.03.071
Yoshioka, T., Grause, G., Eger, C., Kaminsky, W., and Okuwaki, A. (2004). Pyrolysis of poly (ethylene terephthalate) in a fluidised bed plant. Polym. Degrad. Stab. 86, 499–504. doi: 10.1016/j.polymdegradstab.2004.06.001
Keywords: catalytic pyrolysis, pyrolysis based biorefineries, natural zeolite, plastic waste, aromatic compounds, modified natural zeolite, catalyst
Citation: Miandad R, Rehan M, Barakat MA, Aburiazaiza AS, Khan H, Ismail IMI, Dhavamani J, Gardy J, Hassanpour A and Nizami A-S (2019) Catalytic Pyrolysis of Plastic Waste: Moving Toward Pyrolysis Based Biorefineries. Front. Energy Res. 7:27. doi: 10.3389/fenrg.2019.00027
Received: 15 November 2018; Accepted: 22 February 2019;
Published: 19 March 2019.
Edited by:
Wei-Hsin Chen, National Cheng Kung University, TaiwanReviewed by:
Gopalakrishnan Kumar, University of Stavanger, NorwayTzu-Hsien Hsieh, CPC Corporation, Taiwan
Copyright © 2019 Miandad, Rehan, Barakat, Aburiazaiza, Khan, Ismail, Dhavamani, Gardy, Hassanpour and Nizami. This is an open-access article distributed under the terms of the Creative Commons Attribution License (CC BY). The use, distribution or reproduction in other forums is permitted, provided the original author(s) and the copyright owner(s) are credited and that the original publication in this journal is cited, in accordance with accepted academic practice. No use, distribution or reproduction is permitted which does not comply with these terms.
*Correspondence: Mohammad Rehan, ZHIubW9oYW1tYWRfcmVoYW5AeWFob28uY28udWs=