- 1Catalonia Institute for Energy Research, Sant Adrià de Besòs, Spain
- 2Department of Material and Environmental Chemistry, Stockholm University, Stockholm, Sweden
- 3ISIS Neutron and Muon Source, STFC Rutherford Appleton Laboratory, Didcot, United Kingdom
Batteries with air electrodes are gaining interest as Energy Storage Systems (ESSs) for Electrical Vehicles (EVs) because of their high specific energy density. The electrochemical performance of these batteries is limited by the metallic electrode, which suffers structural transformations and corrosion during cycling that reduces the cycle life of the battery. In this context, relevant information on the discharge products may be obtained by in-situ neutron diffraction, a suitable technique to study electrodes that contain light elements or near neighbor elements in the periodic table. Case studies of MH-air and Fe-air batteries are highlighted.
Introduction
Air cathode-based batteries are promising energy storage systems for Electrical Vehicles (EVs) because they are lighter and, theoretically, may store higher electrochemical capacity than Li-ion batteries. This, in turn, maximizes the specific energy density (kWkg−1) of the battery and may lead to a substantial increase of the range capability of EVs beyond the present limit of ~300 Km (Science and Technology, 2017). Tesla has recently obtained patent(s) on this technology (Herman et al., 2017), with the aim of developing new chemistries and optimizing the existing ones which, unfortunately, are not yet competitive enough to replace current technology, especially in terms of cycle life.
An air cathode battery is a hybrid system that falls into two technologies; fuel cells and rechargeable batteries. The positive electrode or cathode is a light electrode that requires a continuous source of fuel or gaseous reactant to release the stored energy, as in Solid Oxide Fuel Cells (SOFCs) (Singhal, 2000). The anode is a metallic electrode which usually contains additives to improve its electrochemical performance and it is immersed in the electrolyte, typically an aqueous one. This hybrid configuration overcomes some of the problems associated with fuel cells and rechargeable batteries, when considered individually. For instance, air cathode batteries do not rely on H2 gas, so safety issues and costs associated with hydrogen storage using highly-pressurized cylinders are not a limitation in Metal-air batteries. Or the electrochemical capacity of a rechargeable Nickel-Metal Hydride battery (NiMH) may be significantly increased by the use of an air-electrode instead of Ni(OH)2 (Dong et al., 2010), hence a MH-air battery.
Half-cell reactions in an aqueous air cathode battery are presented below. For the positive air electrode, oxygen or air is supplied during discharge and the oxygen reduction reaction takes place giving 2 hydroxide molecules. It is difficult to develop air-electrodes able to withstand the electrochemical evolution and reduction of oxygen (OER and ORR) at high current rates (Jörissen, 2006). For our work investigating phase formation and transformations during charge/discharge using in-situ powder diffraction methods, Ni mesh may be used at the anode. The use of nickel mesh is motivated by its relatively simple diffraction pattern, which minimizes the number of Bragg reflections contaminating the neutron diffraction patterns collected in-situ. Concerning half-cell reactions at the metallic electrode, two reactions are presented which generally describe the chemistry at this electrode, which is the limiting one in terms of battery electrochemical capacity. In the case where the metallic electrode is a hydrogen-absorbing metal or metal-hydride as in MH-air batteries, reaction 2, protons diffuse to the particle surface and recombine with OH- at the interface with the electrolyte during discharge, forming H2O and releasing electrons (Young and Nei, 2013; Yartys et al., 2016). Or, alternatively, the metallic electrode oxidizes forming hydroxides and/or oxide compounds, depending on the depth-of-discharge, reaction 3. In this category, Al-air, Mg-air, Zn-air or Fe-air batteries are included (Rahman Md et al., 2013).
Air electrode: 2OH− ↔ 1/2O2 + H2O + 2e− reaction 1
MH -electrode: 2M + 2H2O + 2e− ↔ 2MH + 2OH−
reaction 2
Metallic electrode 2M(OH)x + 2e− ↔ 2M + 2OH−
reaction 3
The cycle life of an air cathode battery is limited by the reactions taking place at the metallic electrode. In MH-air batteries, the stored electrochemical capacity is high (~300 mAhg−1 for AB5-type alloys) and may be increased if superlattice A2B7-type alloys are used, which also show lower self-discharge (Yartys et al., 2016). However, these materials corrode in alkaline solutions, forming insulating phases such as La(OH)2 at the particle/electrolyte interface, which reduce the diffusivity of protons to the bulk and, as the electrochemical reaction proceeds, capacity rapidly decreases. Corrosion also affects Metal-air batteries. In Li-Air batteries (Aurbach et al., 2016), the chemical interaction between Li metal and the electrolyte is critical to avoid formation of irreversible phases, and aprotic electrolytes have shown better performance than aqueous ones. Critically, the latter one needs passivation of the metallic lithium in order to operate safely. The highly irreversible formation of discharge products at the metallic electrodes in Al-air, Zn-air, Fe-air and Mg-air batteries affect their performance and, in addition, H2 gas evolution occurs at the discharge potentials, which reduces the efficiency of the batteries (Rahman Md et al., 2013). In the case of Fe-air, addition of K2SnO3 to the aqueous electrolyte improves the electrochemical performance of the battery (Chamoun et al., 2017).
Powder diffraction experiments are a fundamental method of determining phase composition and structures in multi-component systems such as batteries, of which the metallic compounds contained inside, are one example. However, corrosion products in Li and Na-based batteries may be difficult to characterize using X-rays due to the low atomic number elements contained in them. In a similar way there is very little contrast between elements adjacent to each other in the periodic table, e.g., transition metals, when X-ray radiation is used, so limiting the structural information that can be obtained from Rietveld refinement of the crystal structure(s). With neutron diffraction, however, the scattering power of nuclei can vary dramatically between elements of similar atomic number, and also between isotopes of the same element. Furthermore, neutrons are highly penetrating compared to X-rays, meaning that information is gained from the bulk of a sample rather than near-surface regions. Consequently in-situ neutron diffraction is the ideal technique to obtain accurate structural information on the phases commonly found in air cathode batteries in real time as they are charged and discharged in the neutron beam. However, air cathode electrodes have additional requirements compared to rechargeable batteries which need to be implemented into cell design e.g. O2 or H2 evolution.
In this manuscript, the use of in-situ neutron diffraction to characterize Metal-air batteries is highlighted in two case studies, MH-air and Fe-air, using a customized electrochemical cell for air cathode.
Methods
In-situ neutron diffraction data were collected at the Polaris diffractometer (Hull et al., 1992) at ISIS, and diffraction data were analyzed by the Rietveld method using GSAS least-squares refinement software (Larson and Von Dreele, 1990). Neutron diffraction data were collected using the backscattering detector (135° ≤ 2θ ≤ 168°, dmax = 2.7 Å). Further information of cell design and components may be found in (Biendicho et al., 2014, 2015; Chamoun et al., 2017).
Results and Discussion
The electrochemical cell originally constructed to conduct in-situ studies in a NiMH battery (Biendicho et al., 2014, 2015), may be easily adapted to other energy storage systems due to its modular and flexible configuration. As presented in previous publications, the cell is based in a planar design stacking the components on top of each other, as in coin cells used in a laboratory to characterize electrode materials ex-situ. However, the dimensions of the in-situ cell are significantly larger compared to standard coin cells to maximize the amount of electrode material exposed to the neutron beam; the outer cell diameter of the cell is 84 mm and usually accommodates rectangular-shaped electrodes of 1–2 g. Figures 1A,B show an expanded view of the in-situ cell and a sketch of the cell components and their position with respect to the incident neutron beam, respectively. Further details of the cell components and materials used to collect neutron diffraction patterns with an increased peak-to-background ratio may be found in previous publications (Roberts et al., 2013; Biendicho et al., 2014, 2015).
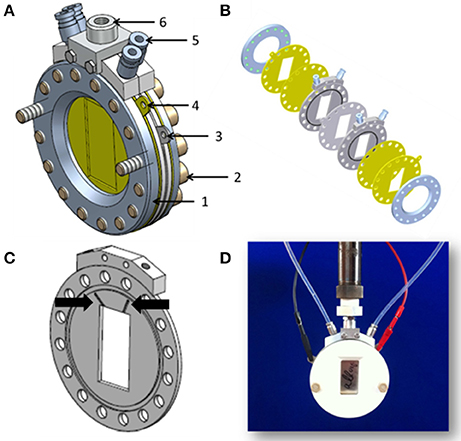
Figure 1. (A) Expanded view of the in-situ cell; 1 and 2 correspond to the alloy clamp rings and PEEK screws used to seal the cell after assembly, 3 and 4 are the two windows which hold the thin Ni metal sheets used as positive and negative electrodes, 5 are inlet/outlet connections for the tubing to pump in gas fuel or electrolyte and 6 is the threaded block used to mount the cell on the diffractometer; (B) sketch of the cell components and their position with respect to the incident neutron beam; (C) close-up detail of the separator module; the two apertures that connect the inner compartment of the battery with the cell exterior (indicated by the black arrows); (D) assembled cell with tubing connections prior in-situ experiment.
As discussed above, the positive electrode in a metal-air battery requires a constant source of fuel to release the stored energy. It is necessary, therefore, to take into account this requirement at the cell design stage, especially if long-term stability studies are considered. A special separator module was designed and is presented in Figure 1C. The upper part of the separator module has two apertures, indicated by black arrows, which connect the inner compartment of the battery to the cell exterior, allowing either gas fuel or electrolyte to be pumped in and out of the cell during in-situ diffraction measurements. These apertures are also used to avoid cell over-pressure during discharge at the positive electrode (H2 evolution). Figure 1D shows the assembled in-situ cell with inlet and outlet connections, which was constructed prior to one of the experiments conducted at the ISIS neutron spallation source. Considering the positive electrode, a nickel mesh is preferred since it is the same material as current collector. Other catalytic materials could be used as electrodes but they would either add extra Bragg peaks to the neutron diffraction patterns or increase the background, potentially masking reflections from the negative electrode.
Two examples are presented in the following paragraphs i.e., MH-air and Fe-air, to show the quality of diffraction patterns obtained by the customized electrochemical cell, and the type of structural information that may be extracted by in-situ measurements, respectively.
Figure 2A shows neutron diffraction patterns of the cell assembled with an AB5-type alloy as anode as a function of discharge state using a current of ~30 mA. Because the incoherent neutron scattering from hydrogen atoms would produce a large background signal, deuterated 6 M KOD electrolyte was used instead during battery construction. The most intense sharp diffraction peaks correspond to nickel from the thin current collectors and Ni mesh used as counter electrode, and the small background contribution is related to a Polypropylene membrane. The cell was loaded with 1.8 gr of alloy with composition MmNi3.6Al0.4Mn0.3Co0.7 where Mm denotes Misch metals. Additional information of cell assembly, cycling conditions and components may be found in Biendicho et al. (2014, 2015).
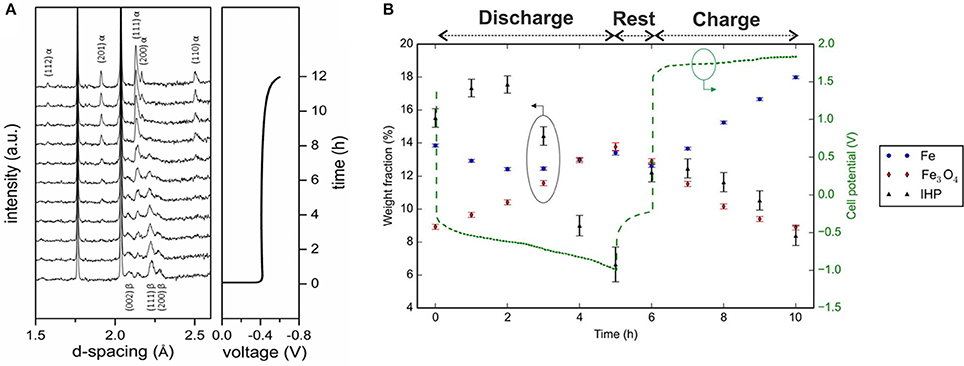
Figure 2. (A) Neutron diffraction patterns from the cell collected in-situ using an MH electrode (AB5-type alloy) and Ni mesh as negative and positive electrodes, respectively. The cell potential vs O2/H2 measured during the in-situ experiment is also presented, (B) Plot showing weight fraction and the cell potential vs. O2/H2 as a function of time using a Fe electrode and Ni mesh as anode and cathode, respectively.
As discharge proceeds, the intensity of the reflections corresponding to the β-phase with lattice parameters a ~5.26 Å and c ~4.17 Å decrease and other reflections appear that can be indexed using a smaller unit cell corresponding to the α-phase, with a ~5.00 Å and c ~4.04 Å. Because of the good signal-to-noise ratio of the in-situ neutron diffraction patterns, it is also possible to observe differences in diffraction line widths between the charged phase and the discharged one. Bragg Peaks of β-phase are broader than the ones corresponding to the α-phase, demonstrating a substantial disorder of the deuterium atoms in the crystal structure of the charged material. For this alloy composition, an intermediate an intermediate phase (γ-phase) has been detected, in addition to the β- and α- phases, during charge and its appearance has been related to an improved stability of the electrode to corrosion and, in turn, to a better cycle life (Latroche et al., 1999).
Figure 2B shows phase fraction (weight %) as a function of cell potential for a Fe-air battery. Blue, red and black markers correspond to Fe, Fe3O4 and a new intermediate hydride phase that was identified during in-situ measurements. The electrolyte composition was deuterated 6 KOD and 0.1 M K2SO3 which was used as additive to reduce H2 evolution and no membrane was used to separate the Fe and Ni mesh electrodes. Instead, physical separation with a 5 mm distance between the electrodes was provided. The total weight of the Fe electrode was 1.25 g. Additional information of cell assembly, cycling conditions and components may be found in Chamoun et al. (2017).
Structural refinements of the new phase observed in the Fe electrode showed a good agreement between observed and calculated data (see Chamoun et al., 2017). The new metastable phase was refined using a tetragonal unit cell and with composition being a solid solution of Fe, Sn, Bi, and C. its weight fraction was then monitored in-situ, as for the other phases. In-situ structural information, which may also involve lattice or atomic displacement parameters, are interesting because they give in-deep understanding of the redox chemistry in the electrode, otherwise inaccessible by ex-situ techniques.
Conclusions
In-situ neutron diffraction is, therefore, a technique that contributes to a better understanding of charge/discharge mechanism in the metallic alloys presently used in many battery systems. Such knowledge is vital in allowing the development of new materials and compositions having improved capacity retention, fewer irreversible side-reaction and better efficiency.
The updated electrochemical cell presented in this paper provides the requirements to characterize the structure of metallic electrodes in an air cathode battery in-situ. The specially designed separator module, the choice of Ni mesh as cathode and the use of deuterated aqueous electrolyte are key components to obtain neutron diffraction patterns with good signal-to-noise ratio, which may be used to extract relevant structural information such as phase stability or phase fraction as highlighted for an MH-air and a Fe-air battery, respectively.
Author Contributions
Cell design and construction were conducted at ISIS and Stockholm university. For this task, JJ, SH, GS, and CO contributed equally. Material preparation and ex-situ battery testing were conducted at Stockholm University by JJ and DN. In-situ experiments presented in the paper were obtained at ISIS neutron and Muon source by JJ, SH, and RS.
Conflict of Interest Statement
The authors declare that the research was conducted in the absence of any commercial or financial relationships that could be construed as a potential conflict of interest.
References
Aurbach, D., McCloskey, B. D., Nazar, L. F., and Bruce, P. G. (2016). Advances in understanding mechanism underpinning lithium-air batteries. Nat. Energy 1:16128. doi: 10.1038/NENERGY.2016.128
Biendicho, J. J., Roberts, M., Noréus, D., Lagerqvist, U., Smith, R. I., Svensson, G., et al. (2015). In situ investigation of commercial Ni(OH)2 and LaNi5-baesed electrodes by neutron powder diffraction. J. Mater. Res. 30, 407–215. doi: 10.1557/jmr.2014.317
Biendicho, J. J., Roberts, M., Offer, C., Noréus, D., Widenkvist, E., Smith, R. I., et al. (2014). New in-situ neutron diffraction cell for electrode materials. J. Power Sour. 248, 900–904. doi: 10.1016/j.jpowsour.2013.09.141
Chamoun, M., Skarman, B., Vidarsson, H., Smith, R. I., Hull, S., Lelis, M., et al. (2017). Stannate increases hydrogen evolution overpotential on rechargeable alkaline iron electrodes. J. Electrochem. Soc. 164, A1251–A1257. doi: 10.1149/2.1401706jes
Dong, H., Kiros, Y., and Noréus, D. (2010). An air-metal hydride battery using MmNi3.6Mn0.4Al0.3Co0.7 in the anode and a perovskite in the cathode. Int. J. Hydrogen Energy 35, 4336–4341. doi: 10.1016/j.ijhydene.2010.02.007
Herman, W. A., Straubel, J. B., and Beck, D. G. (2017). Charge Rate Modulation of Metal-Air Cells as a Function of Ambient Oxygen Concentration. Patent no: US 9559532 B2
Hull, S., Smith, R. I., David, W. I. F., Hannon, A. C., Mayers, J., Cywinski, R., et al. (1992). The polaris powder diffractometer at ISIS. Physica B 180–181, 1000–1002. doi: 10.1016/0921-4526(92)90533-X
Jörissen, L. (2006). Bifunctional oxygen/air electrodes. J. Power Sour. 155, 23–32. doi: 10.1016/j.jpowsour.2005.07.038
Larson, A. C., and Von Dreele, R. B. (1990). Report LA-UR-86-748. Los Alamos, NM: Los Alamos National Laboratory, NM87545.
Latroche, M., Percheron-Guégan, A., and Chabre, Y. (1999). Influence of cobalt in MmNi4.3-xMn0.3Al0.4Cox alloy (x = 0.36 and 0.69) on its electrochemical behavior studied by in situ neutron diffraction. J. Alloys Compd. 293–295, 637–642.
Rahman Md, A., Wang, X., and Wen, C. (2013). High energy density metal-air batteries: a review. J. Electrochem. Soc. 160, A1759–A1771. doi: 10.1149/2.062310jes
Roberts, M., Biendicho, J. J., Hull, S., Beran, P., Gustafsson, T., Svensson, G., et al. (2013). Design of a new lithium ion battery test cell for in-situ neutron diffraction measuraments. J. Power Sour. 226, 249–255. doi: 10.1016/j.jpowsour.2012.10.085
Science and Technology (2017) (September 2017). Electric vehicles powered by fuel-cells get a second look. The Economist p. 25.
Singhal, S. C. (2000). Advances in solid oxide fuel cell technology. Solid State Ionics 135, 305–313. doi: 10.1016/S0167-2738(00)00452-5
Yartys, V., Noréus, D., and Latroche, M. (2016). Metal hydrides as negative electrode materials for Ni-MH batteries. Appl. Phys. A 122, 43. doi: 10.1007/s00339-015-9538-9
Keywords: metal-air battery, metal hybrid air battery, in-situ neutron diffraction, rechargeable batteries, fuel cells
Citation: Jacas Biendicho J, Noréus D, Offer C, Svensson G, Smith RI and Hull S (2018) New Opportunities for Air Cathode Batteries; in-Situ Neutron Diffraction Measurements. Front. Energy Res. 6:69. doi: 10.3389/fenrg.2018.00069
Received: 19 March 2018; Accepted: 25 June 2018;
Published: 12 July 2018.
Edited by:
Verónica Palomares, University of the Basque Country (UPV/EHU), SpainReviewed by:
Branimir Nikola Grgur, University of Belgrade, SerbiaWei Kong Pang, University of Wollongong, Australia
Copyright © 2018 Jacas Biendicho, Noréus, Offer, Svensson, Smith and Hull. This is an open-access article distributed under the terms of the Creative Commons Attribution License (CC BY). The use, distribution or reproduction in other forums is permitted, provided the original author(s) and the copyright owner(s) are credited and that the original publication in this journal is cited, in accordance with accepted academic practice. No use, distribution or reproduction is permitted which does not comply with these terms.
*Correspondence: Jordi Jacas Biendicho, amphY2FzQGlyZWMuY2F0