- 1School of Food and Biological Engineering, Jiangsu University, Zhenjiang, China
- 2Guangzhou Institute of Energy Conversion, Chinese Academy of Sciences, Guangzhou, China
- 3Key Laboratory of Renewable Energy, Chinese Academy of Sciences, Guangzhou, China
- 4Vaasa Energy Institute, University of Vaasa, Yliopistonranta, Vaasa, Finland
- 5College of Engineering, China Agricultural University, Beijing, China
The complicated and changeable weather conditions and pest invasion increase difficulties in outdoor microalgae cultivation. In this paper, outdoor microalgae cultivation experiments were investigated in Foshan city, South China. During June and August when the temperature is high, the cooling system-water spray combined shade tarpaulin can effectively reduce the temperature to 4–7°C in the 40 L vertical tubular outdoor photobioreactors. Under 300 mg/L urea and 200 mg/L ammonium bicarbonate conditions, Chlorella zofingiensis G1 had the largest biomass accumulation. Addition of acetic acid to adjust the pH of the medium can effectively improve the C. zofingiensis G1 biomass in the photobioreactor, which was four times more than that only through air ventilation conditions. The biomass accumulation of C. zofingiensis G1 was essentially unchanged during night time.
Introduction
The lack of robust microalgae strains and the limitations on the cultivation conditions are two important factors that cause the exorbitant microalgae production cost. Due to the cost input into nutritive salts such as chemical fertilizers and energy consumption for microalgae harvesting, the microalgal biodiesel has not been successfully applied to commercial production yet (Sheehan et al., 1998; Chisti, 2007; Wang et al., 2015). Utilizing the sunlight resource to magnify the cultivation of microalgae under outdoor condition is an effective way to reduce the cost of microalgal biodiesel production. The current studies on energy microalgae are mainly carried out at indoor labs as there are many difficulties in outdoor cultivation (Miao and Wu, 2004; Xiong et al., 2008; Sebestyén et al., 2016). The main difficulties for sustainable outdoor cultivation of microalgae are pollutions from fungi, protozoa, bacteria and other hybrid algae and complex and changeable weather conditions (Rodolfi et al., 2009; Ouyang et al., 2010; Huo et al., 2011; Wang et al., 2018). Under these adverse conditions, the chosen strains must have a relatively strong ability in accumulating oil, and more importantly, the algal strain should have a very strong adaptability to the external environment. Because Chlorella have broader adaptability and better survivability to external environment, there are more studies about its cultivation in outdoor raceway pond (Bhowmick et al., 2014; Lu et al., 2015).
Some reports show that Chlorella zofingiensis can adapt to various cultivating conditions and it has a fast growth rate which can reach 0.769 d−1 (Rise et al., 1994; Feng et al., 2011). The oil content of C. zofingiensis accounted for 52% of the dry weight under indoor heterotrophic conditions (Lin and Chen, 1994; Liu et al., 2011). Now the cultivation of C. zofingiensis is mainly focused on the production of astaxanthin (Sheehan et al., 1998; Orosa et al., 2000; Ip et al., 2004; Ip and Chen, 2005). The studies about outdoor cultivation of C. zofingiensis aiming for bioenergy production are still relatively limited. Feng et al reported that the oil content of C. zofingiensis accounted for 65.8% of its dry weight under nitrogen deficiency condition when transferred from indoor to 60 L outdoor flat bio-reactor. Because the pollution was not obvious, the algal cells can adapt to outdoor environment very quickly (Feng et al., 2011). Up to now, there are few reports on the outdoor cultivation of C. zofingiensis during high temperature season and the pH regulation through acetic acid addition. This paper attempted to cultivate C. zofingiensis G1 using a self-made 40 L vertical tubular outdoor photobioreactor and study its feasibility for outdoor cultivation, and also investigate the impacts of different nitrogen sources and the impacts of adjusting pH by adding acetic acid (HAc) on the growth of C. zofingiensis G1.
Materials and Methods
Microalgal Strain and Culture Conditions
C. zofingiensis G1 was observed at Guangzhou Institute of Energy Conversion, Chinese Academy of Sciences (Guangzhou, Guangdong, China). BG11 medium (Rippka et al., 1979) was used. About 100 mL pre-culture broths mentioned above were inoculated into a vertical tubular photobioreactor containing 1.0 L medium. The vertical tubular photobioreactor consisted of glass tubes of 70.0 cm heights and 5.0 cm outside diameters. Light was supplied by cool white fluorescent lamps at the single side of the photobioreactor [light intensity: 200 ± 50 μE/(m2 s)]. Aeration and mixing were achieved by the sparging air enriched with 6.0% CO2 through a glass-filter, which was inserted to the bottom of the reactor and the flow rate of gas was 0.5 vvm regulated by the gas flow meter (Model G, Aalborg Instruments and Controls, Inc., Orange-burg, NY, USA). The temperature of the culture media was 25 ± 1°C regulated by the room air conditioner (Gree Electric Appliances Inc., Zhuhai, Guangdong, China). After 6 days of cultivation, the cultures were used for outdoor experiment.
The outdoor microalgae cultivation experiment in this paper was carried out in Foshan, Guangdong, China, which belongs to subtropical and south subtropical oceanic monsoon climate areas. The work was carried out between June and August, which was the most scorching season of a year in South China region. The experiment used 40 L vertical tubular outdoor photobioreactor (8.7 cm × 160 cm = diameter × height) to cultivate the above mentioned C. zofingiensis G1. The reactor was composed by organic glass base and glass tube, having an organic glass cover on the top and a vent-hole in the base (Figure 1). Before the cultivation start, the internal walls should be washed with cleanser and clean water. The water used during the test was local mountain spring water, whose components could be found in Table 1. The water quality could basically meet the required elements for microalgae growth, and it contained comparatively more Si, Mg, and Ca.
The following nutritive salts was replenished during the experiment: 300 mg/L of urea (CO(NH2)2), 60 mg/L of KH2PO4, 60 mg/L of MgSO4•7H2O and 1 mg/L of FeSO4•7H2O. 3 mL of NaClO solution was added at dusk (18:00 local time) to make the final concentration of available chlorine reach 7.5 ppm and disinfect overnight. The air compressor was used in the whole cultivation process to ensure constant ventilation and avoid the sedimentation of C. zofingiensis G1. The pH, temperature and light intensity of the culture condition was tested and recorded four times a day (8:00, 11:00, 14:00, 17:00), and the pH was adjusted to 7.5 ± 0.3 by using acetic acid and the quantity of acetic acid added was recorded every time . Samples of each tube should be taken at 17:00 every day to test the OD680 value.
Chemical Fertilizer and Reagents
The urea was produced by Sichuan Meifeng Agricultural Chemical Co., Ltd, the NH4HCO3 was produced by Hunan Yizhang Chemical Fertilizer Co., Ltd, the KH2PO4 was produced by Wuhan Nanqing Science & Technology Development Co., Ltd, the MgSO4•7H2O was bought at Guangzhou Chemical Co., Ltd, the FeSO4•7H2O was produced by Guangzhou Chemical Reagent Factory, and the acetic acid whose purity exceeds 99% was produced by Jiangsu Sopo (Group) Chemical Co., Ltd.
Sunshade Net and Atomization Spray System
The top of vertical tubular outdoor photobioreactor was covered with a sunshade net. The sunshade net was made of high density polyethylene fire-retardant materials, with a shading rate of 40–55%. The water pressure of the atomization spray was 250 KPa, its water flow rate was 9.0 L/h and its flow distance was 1.5 m. The equipment was used for observing the sun block and temperature reduction effects of the cooling system - water spray combined shade tarpaulin on the growth of C. zofingiensis G1 under outdoor environment of the most scorching season in South China.
Results and Discussion
Sun Block and Temperature Reduction Effects of Cooling System—Water Spray Combined Shade Tarpaulin
If microalgae was cultivated under high temperature environment, the CO2 fixation rate would be restrained and the O2 release rate would be limited (Kanno and Uyama, 2005). In June-August of South China, it was very hot and the temperature can exceed 40°C. As the algae cells absorb light, the temperature in the vertical tubular outdoor photobioreactor would be even higher than 45°C, which would greatly limit the algae growth rate. The combination of polyethylene materials and atomization spray can reduce the photobioreactor temperature effectively at noon by 4–7°C (Figure 2). There was a linear relation between the column temperature after reduction and the external temperature (as Figure 2 shows). The temperature in the morning was relatively low itself, so the cooling effect was not as obvious as at noon. This combining method can keep the photobioreactor temperature below 35°C, therefore the growing rate of algae would not be limited.
While reducing the photobioreactor temperature effectively, the sunshade net could also reduce the light intensity. The actual shaded effects were shown as Figure 3. The angle of sun incidence changed during day time, as a result the actual shaded effects were changing which caused the sunlight to be in-homogeneous during the algae cultivation cycle. Excessively strong sunlight would result in the photo-inhibition phenomenon, which would affect the efficiency of photosynthesis or even cause cell oxidation. As was shown in Figure 3, the light intensity at sunny noon could exceed 2,000 μmol/ (m2•s), while the proper light intensity range for most microalgae was between 36 and 180 μmol/ (m2•s) (Feng et al., 2011). There was also a linear relation between the sun light intensity after block and the external light intensity (as Figure 3 shows). It is suggested that the proper light intensity range was between 100 and 1,600 μmol/ (m2•s) and the light saturation point was around 500 μmol/ (m2•s) (Rise et al., 1994). The appropriate light intensity of C. zofingiensis XQ−200419 was found at 150 μmol/ (m2•s), and it could reach its maximum growth speed when the concentration of KNO3 reached 0.5 mg/mL. Constant increase of sunlight or KNO3 concentration would limit the split and growth of algae (Rise et al., 1994). In the initial stage of experiment, the sunshade net could reduce the light intensity to some extent which could avoid the photo-inhibition phenomenon in the early growth stage of algae, and would not affect the necessary light intensity needed for photosynthesis after the microalgae concentration increase.
Confirmation of Cheap Nitrogenous Fertilizer
Among all the fertilizers used in the cultivation of microalgae, the consumption of nitrogenous fertilizer was the highest. The experiment studied the use of cheap nitrogenous fertilizer, urea and ammonium bicarbonate replacing traditional nitrate nitrogen such as potassium nitrate on the growth of C. zofingiensis G1. The results were shown in Figure 4, and the weather conditions during cultivation were shown as Table 2. When the concentration of urea and NH4HCO3 are 300 and 200 mg/L, respectively, it grew slowly in the first 2 days after inoculation but it had the biggest algae biomass cumulation 4 days later.
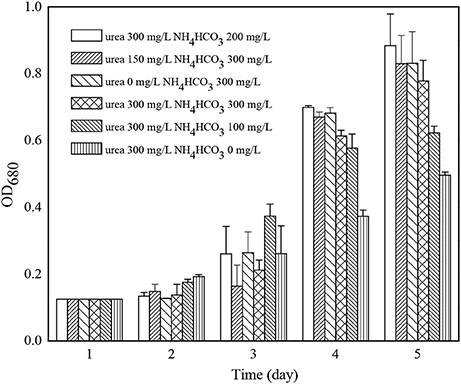
Figure 4. The effects of different nitrogenous fertilizer on the growth of Chlorella zofingiensis G1.
C. zofingiensis utilized the reduced nitrogen such as ammonia nitrogen and urea better than nitrate nitrogen (Yun et al., 1996; Converti et al., 2006). As a nitrogen source, the nitrate nitrogen is reduced to sub-nitrite nitrogen using nitrate reductase first, and then would be reduced to ammoniacal nitrogen using nitrite reductase again before it was absorbed and utilized by microalgae cell (Converti et al., 2006). Under alkaline conditions, the urea is decomposed into ammonia by algal metabolism (Torre et al., 2003), so it could be absorbed. In the chlorophyceae, the urea was catalyzed and degraded by amido lyase, and the amidogen produced during the process would enter the nitrogen metabolism of amino acid. The reaction equation was as follows (Lee, 2008):
Walker reported that urea was the best nitrogen nutrition to get the highest microalgae biomass accumulation (Walker, 1953). High concentration urea would not have toxic restrains to the algal cell as ammonia nitrogen and nitrate nitrogen, but excessively high concentration would lead to the denaturation of protein. During the use of urea, the pH had no big changes. Ammonium bicarbonate was a physiological and neutral nitrogen fertilizer, and Xun et al found that Prorocentrum donghaiense more compatible to the use of than urea (Xu et al., 2012). When the concentration of NH4HCO3 reached 200 mg/L, it showed restrains on the algal growth. When the concentration of NH4HCO3 reached 300 mg/L, which meant that the concentration of reached 68.1 mg/L, the restrains were very obvious. The growth rate was still very slow on the second day, and became quick on the third day. The restrains of the ammonia nitrogen concentration to algae are closely related to the cultivating conditions (Tarn and Wong, 1996). It is reported that when the concentration of ammonia nitrogen exceeded 2 mM (~36 mg/L) and pH exceeded 8.0, it would restrain the photosynthesis of Scenedesmus obliquus and affect the growth of algal cells (Abeliovich and Azov, 1976). There were also similar reports on the cultivation of Scenedesmus sp. in anaerobic digestion effluent, showing that the concentration of ammonia nitrogen would not have restrains to the growth of algae when it was 100 mg/L, but would reduce 70% of the algal growth when the concentration of ammonium was in the range of 200–500 mg/L (Park et al., 2010). The quantity of free ammonium NH3 and free ammonia depends on the pH value of the solution. Under low pH conditions, the alga cell might not be restrained by free ammonia, but the increase of free ammonium under high pH values above 9.0 would restrain the growth of alga cell very obviously (Konig et al., 1987). The ammonium would be totally ionized when the pH value was lower than 8.0 under 25°C and almost half ammonium would not be ionized when the pH value was 9. With the increase of temperature, the toxicity of ammonium would increase. Although the pH of cultivated solution was adjusted, and it would have restrains to the growth of C. zofingiensis G1 when the pH of the culture medium of the solution increases to 9.0 after 3 h (Wurts, 2003). We could see from the results that the concentration of urea had no obvious impact on C. zofingiensis G1 growth under this concentration range.
Effects of Ventilating and Adding Acetic Acid on Growth of Algae
Figure 5 indicated that the growth rate of C. zofingiensis G1 can be increased effectively by adding acetic acid. On the third day of outdoor cultivation, the concentration of C. zofingiensis G1 after adding acetic acid was 4.1 times of that in the case of ventilating only. The conclusion confirmed to the results of Lin, who found that the C. pyrenoidosa had the fastest growing speed when adding acetic acid and in-letting CO2 at the same time (Lin and Chen, 1994).
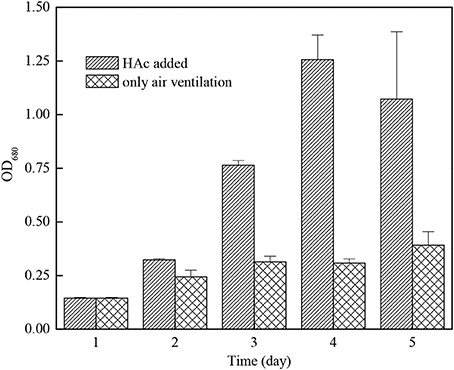
Figure 5. The growth effect of Chlorella zofingiensis G1 under air ventilation only or HAc addition.
As Table 3 shows, during the cultivation period, the average temperature in the photobioreactor and light intensity had no big changes until the fourth day when the light intensity decreased because of cloudy weather, so the growth rate of the group adding acetic acid slowed down. The light intensity reached its maximum [450–561 μmol/ (m2•s)] at 11:00 a.m. every day, and it was comparatively low in the morning and afternoon. The temperature in photobioreactor was comparatively low at 21.2–23.5°C at 8:00 a.m., and it would increase to 34.2–36.9°C gradually with the increase of light intensity in this season. As what had shown on Figure 6 that if we did not adjust the pH value, then it would increase gradually from 8:00 a.m. because of the photosynthesis of C. zofingiensis G1, and the rate of increase slowed down to 9.7–9.9 in the afternoon. There was no photosynthesis in the night time, and the respiration and release of CO2 would cause the pH value to drop back to 8.9–9.0. It is reported that the increase of pH would lead to the precipitation of phosphate and the blowing off of ammonia nitrogen (Gonzalez et al., 2008). We could not add too much acetic acid when the concentration of microalgae was low in the early stage of cultivation, otherwise it would lead to low pH value and produce foams during the cultivation, which was not good to the growth of algae. As the increase of microalgal concentration, we needed to increase the quantity of acetic acid. The temperature, light intensity and photosynthesis were comparatively strong at 11:00 and 14:00 every day, we needed to add more acid to adjust pH value. The adding of acetic acid could increase the growth rate and biomass accumulation of microalgae obviously, but adding acetic acid could not achieve this effect in the night time because there was no light.

Table 3. The fluctuation of irradiance and air temperature of each day under outdoor conditions with only air ventilation or HAc addition.
Under the condition of adjusting pH by adding acetic acid, C. zofingiensis G1 not only utilized the sunlight to fix the CO2 in the daytime, but also utilize the organic carbon source such as acetic acid by mixotrophic cultivation. Under the condition of no light at night, the algae were heterotrophic cultivation, the rate of metabolism slowed down and the temperature was between 26 and 32°C (Figures 7, 8). A small quantity of acetic acid would be burned off, the pH value would increase within 3 h, the changes of biomass concentration was limited, and at the same time the respiration would consume the saccharides and other organics of microalgae, which would cause the decrease of the biomass accumulation of C. zofingiensis G1. The concentration of microalgae biomass of this experiment had no obvious changes, however Torzillo et al used tubular outdoor photobioreactor to cultivate Spirulina platensis in Florence, Italy showed that the rate loss of biomass at night is about 7.6% under 25°C, and the rate loss was 5.0% under 35°C (Torzillo et al., 1991).
Conclusion
Adopting sunshade net and atomization spray combined system can effectively reduce the photobioreactor temperature in the scorching summer of sub-tropical South China areas. When the concentration urea and NH4HCO3 were 300 and 200 mg/L respectively, the concentration of C. zofingiensis G1 reached its maximum. C. zofingiensis G1 had the comparatively strong adapting ability in outdoor photobioreactor. The biomass accumulation of C. zofingiensis G1 by adding acetic acid was four times more than that only through air ventilation conditions. The biomass accumulation of C. zofingiensis G1 at night was not obvious changed by adding acetic acid.
Author Contributions
SH wrote the main part of the paper and together with QS, LZ, LQ, WZ, and PF performed the experiments. ZW, RD, and ZY conceived the experiments. SZ and FZ revised the paper.
Conflict of Interest Statement
The authors declare that the research was conducted in the absence of any commercial or financial relationships that could be construed as a potential conflict of interest.
Acknowledgments
This research was funded by the National Natural Science Foundation of China (21506084), the China Postdoctoral Science Foundation (2015T80502), the Senior Talent Scientific Research Initial Funding Project of Jiangsu University (14JDG024). A Project Funded by the Priority Academic Program Development of Jiangsu Higher Education Institutions (PAPD) and the Training Project of the Young Core Instructor of Jiangsu University.
References
Abeliovich, A., and Azov, Y. (1976). Toxicity of ammonia to algae in sewage oxidation ponds. Appl. Environ. Microbiol. 31, 801–806.
Bhowmick, G. D., Subramanian, G., Mishra, S., and Sen, R. (2014). Raceway pond cultivation of a marine microalga of Indian origin for biomass and lipid production: a case study. Algal Research. 6, 201–209. doi: 10.1016/j.algal.2014.07.005
Chisti, Y. (2007). Biodiesel from microalgae. Biotechnol. Adv. 25, 294–306. doi: 10.1016/j.biotechadv.2007.02.001
Converti, A., Scapazzoni, S., Lodi, A., and Carvalho, J. C. (2006). Ammonium and urea removal by Spirulina platensis. J. Ind. Microbiol. Biotechnol. 33, 8–16. doi: 10.1007/s10295-005-0025-8
Feng, P., Deng, Z., Hu, Z., and Lu, F. (2011). Lipid accumulation and growth of Chlorella zofingiensis in flat plate photobioreactors outdoors. Bioresour. Technol. 102, 10577–10584. doi: 10.1016/j.biortech.2011.08.109
Gonzalez, C., Marciniak, J., Villaverde, S., Leon, C., Garcia, P. A., and Mufioz, R. (2008). Efficient nutrient removal from swine manure in a tubular biofilm photobioreactor using algae–bacteria consortia. Water Sci. Technol. 58, 95–102. doi: 10.2166/wst.2008.655
Huo, S., Dong, R., Wang, Z., Pang, C., Yuan, Z., Zhu, S., et al. (2011). Available resources for Algal biofuel development in China. Energies 4, 1321–1335. doi: 10.3390/en4091321
Ip, P. F., and Chen, F. (2005). Production of astaxanthin by the green microalga Chlorella zofingiensis in the dark. Process Biochem. 40, 733–738. doi: 10.1016/j.procbio.2004.01.039
Ip, P. F., Wong, K. H., and Chen, F. (2004). Enhanced production of astaxanthin by the green microalga Chlorella zofingiensis in mixotrophic culture. Process Biochem. 39, 1761–1766. doi: 10.1016/j.procbio.2003.08.003
Kanno, T., and Uyama, K. (2005). Chlorella Vulgaris: The Powerful Japanese Medicinal Green Algae as a Biological Response Modifier. Salt Lake City, UT: Woodland Publishing.
Konig, A., Pearson, H. W., and Silva, S. A. (1987). Ammonia toxicity to algal growth in waste stabilization ponds. Water Sci. Technol. 19, 115–122.
Lin, L. P., and Chen, T. (1994). Factors affecting the mixotrophic maximum growth of Chlorella pyrenoidosa. J. Chin. Agric. Chem. Soc. 32, 91–102.
Liu, J., Huang, J., Sun, Z., Zhong, Y., Jiang, Y., and Chen, F. (2011). Differential lipid and fatty acid profiles of photoautotrophic and heterotrophic Chlorella zofingiensis : assessment of algal oils for biodiesel production. Bioresour. Technol. 102, 106–110. doi: 10.1016/j.biortech.2010.06.017
Lu, W., Wang, Z., and Yuan, Z. (2015). Characteristics of lipid extraction from Chlorella sp. cultivated in outdoor raceway ponds with mixture of ethyl acetate and ethanol for biodiesel production. Bioresour. Technol. 191, 433–437. doi: 10.1016/j.biortech.2015.02.069
Miao, X., and Wu, Q. (2004). High yield bio–oil production from fast pyrolysis by metabolic controlling of Chlorella protothecoides. J. Biotechnol. 110, 85–93. doi: 10.1016/j.jbiotec.2004.01.013
Orosa, M., Torres, E., Fidalgo, P., and Abalde, J. (2000). Production and analysis of secondary carotenoids in green algae. J. Appl. Phycol. 12, 553–556. doi: 10.1023/A:1008173807143
Ouyang, Z. R., Wen, X. B., and Geng, Y. H. (2010). The effects of light intensities, temperatures, pH and salinities on photosynthesis of Chlorella. J. Wuhan Bot. Res. 28, 49–55. doi: 10.3724/SP.J.1142.2010.10049
Park, J., Jin, H. F., Lim, B. R., Park, K. Y., and Lee, K. (2010). Ammonia removal from anaerobic digestion effluent of livestock waste using green alga Scenedesmus sp. Bioresour. Technol. 101, 8649–8657. doi: 10.1016/j.biortech.2010.06.142
Rippka, R., Deruelles, J., Waterbury, J., Herdman, M., and Stanier, R. (1979). Generic assignments, strain histories and properties of pure cultures of cyanobacteria. J. Gen. Microbiol. 111, 1–61. doi: 10.1099/00221287-111-1-1
Rise, M., Cohen, E., Vishkautsan, M., and Arad, S. (1994). Accumulation of secondary carotenoids in Chlorella zofingiensis. J. Plant Phys. 144, 287–292. doi: 10.1016/S0176-1617(11)81189-2
Rodolfi, L., Zittelli, G., Bassi, N., Padovani, G., Biondi, N., Bonini, G., et al. (2009). Microalgae for oil: strain selection, induction of lipid synthesis and outdoor mass cultivation in a low–cost photobioreactor. Biotechnol. Bioeng. 102, 100–112. doi: 10.1002/bit.22033
Sebestyén, P., Blanken, W., Bacsa, I., Tóth, G., Martin, A., Tasneem, B., et al. (2016). Upscale of a laboratory rotating disk biofilm reactor and evaluation of its performance over a half-year operation period in outdoor conditions. Algal Res. 266–272. doi: 10.1016/j.algal.2016.06.024
Sheehan, J., Dunahay, T., Benemann, J., and Roessler, P. (1998). A Look Back at the U.S. Department of Energy's Aquatic Species Program: Biodiesel from Algae; NREL Report No. TP−580–24190. Golden, CO: NREL.
Tarn, N. F. Y., and Wong, Y. S. (1996). Effect of ammonia concentrations on growth of Chlorella vulgaris and nitrogen removal from media. Bioresour. Technol. 57, 45–50. doi: 10.1016/0960-8524(96)00045-4
Torre, P., Sassano, C. E. N., Sato, S., Converti, A., Gioielli, L. A., and Carvalho, J. C. M. (2003). Fed–batch addition of urea for Spirulina platensis cultivation—thermodynamics and material and energy balances. Enzyme Microb. Technol. 33, 698–707. doi: 10.1016/S0141-0229(03)00217-5
Torzillo, G., Sacchi, A., Materassi, R., and Richmond, A. (1991). Effect of temperature on yield and night biomass loss in Spirulina platensis grown outdoors in tubular photobioreactors. J. Appl. Phycol. 3, 103–109.
Walker, J. B. (1953). Inorganic micronutrient requirements of Chlorella. I. Requirements for calcium(or strontium), copper, and molybdenum. Arch. Biochem. Biophys. 46, 1–11.
Wang, T. H., Chu, S. H., Tsai, Y. Y., Lin, F. C., and Lee, W. C. (2015). Influence of inoculum cell density and carbon dioxide concentration on fed-batch cultivation of Nannochloropsis oculata. Biomass Bioenergy. 77, 9–15. doi: 10.1016/j.biombioe.2015.03.014
Wang, Y., Gong, Y. C., Dai, L. L., Sommerfeld, M., Zhang, C. W., and Hu, Q. (2018). Identification of harmful protozoa in outdoor cultivation of Chlorella and the use of ultrasonication to control contamination. Algal Res. 31, 298–310. doi: 10.1016/j.algal.2018.02.002
Xiong, W., Li, X., Xiang, J., and Wu, Q. (2008). High–density fermentation of microalga Chlorella protothecoides in bioreactor for microbio-diesel production. Appl. Microbiol. Biotechnol. 78, 29–36. doi: 10.1007/s00253-007-1285-1
Xu, N., Qin, J. L., and Sun, S. G. (2012). Uptake kinetics and utilization characteristics of Prorocentrum donghaiense for urea. J. Shenzhen University. 29, 455–460. doi: 10.3724/SP.J.1249.2012.05455
Keywords: Chlorella zofingiensis, outdoor cultivation, photobioreactor, biomass cumulation, cooling system
Citation: Huo S, Wang Z, Zhu S, Shu Q, Zhu L, Qin L, Zhou W, Feng P, Zhu F, Yuan Z and Dong R (2018) Biomass Accumulation of Chlorella Zofingiensis G1 Cultures Grown Outdoors in Photobioreactors. Front. Energy Res. 6:49. doi: 10.3389/fenrg.2018.00049
Received: 03 April 2018; Accepted: 28 May 2018;
Published: 14 June 2018.
Edited by:
Qiang Wang, Institute of Hydrobiology (Chinese Academy of Sciences), ChinaReviewed by:
Richen Lin, University College Cork, IrelandGopalakrishnan Kumar, Yonsei University, South Korea
Copyright © 2018 Huo, Wang, Zhu, Shu, Zhu, Qin, Zhou, Feng, Zhu, Yuan and Dong. This is an open-access article distributed under the terms of the Creative Commons Attribution License (CC BY). The use, distribution or reproduction in other forums is permitted, provided the original author(s) and the copyright owner are credited and that the original publication in this journal is cited, in accordance with accepted academic practice. No use, distribution or reproduction is permitted which does not comply with these terms.
*Correspondence: Zhongming Wang, wangzm@ms.giec.ac.cn