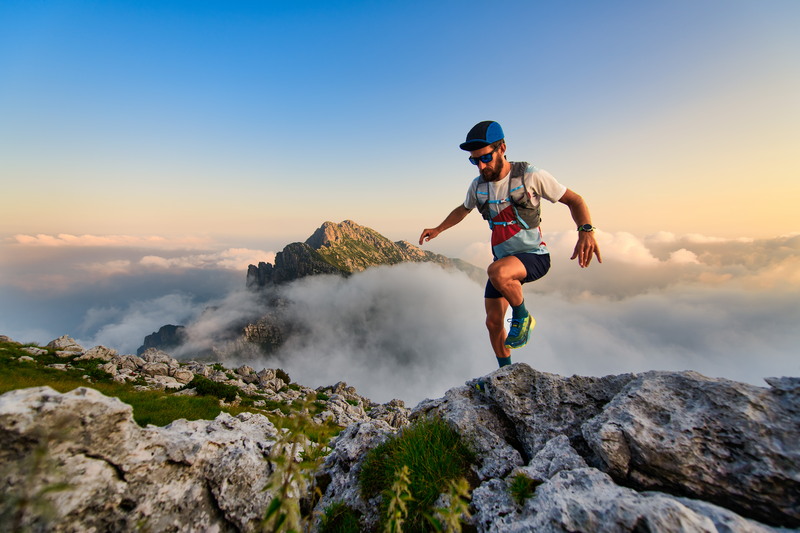
94% of researchers rate our articles as excellent or good
Learn more about the work of our research integrity team to safeguard the quality of each article we publish.
Find out more
ORIGINAL RESEARCH article
Front. Chem. , 25 October 2018
Sec. Chemical Physics and Physical Chemistry
Volume 6 - 2018 | https://doi.org/10.3389/fchem.2018.00525
This article is part of the Research Topic Nonferrous Nanomaterials & Composites for Energy Storage and Conversion View all 48 articles
The spherical-like and honeycomb structural Li0.1Ca0.9TiO3 particles are prepared by spray drying combined with following calcination confirmed by X-ray diffraction (XRD) and scanning electron microscopy (SEM) with energy dispersive X-ray spectrometer (EDS). The poly (vinylidene fluoride-co-hexafluoropropylene) (P(VDF-HFP))-based composite polymer electrolytes (CPEs) modified with the particles are fabricated by phase inversion and activation processes. The characterization results show that the as-prepared CPE membranes possess the smoothest surface and most abundant micropores with the lowest crystallinity with adding the particles into the polymer matrix, which results in high ionic conductivity (3.947 mS cm−1) and lithium ion transference number (0.4962) at ambient temperature. The interfacial resistance can be quickly stabilized at 508 Ω after 5 days storage and the electrochemical working window is up to 5.2 V. Moreover, the mechanical strength of the membranes gains significant improvement without lowering the ionic conductivity. Furthermore, the assembled coin cell can also deliver high discharge specific capacity and preserve steady cycle performance at different current densities. Those outstanding properties may be ascribed to the distinctive structure of the tailored spherical-like and honeycomb structural Li0.1Ca0.9TiO3 particles, which can guarantee the desirable CPEs as a new promising candidate for the polymer electrolyte.
At present, more and more attentions have been invested into the polymer electrolytes in the field of the lithium ion battery, which can not only realize the flexible assembly of the packed battery, but also effectively prevent the explosion and spontaneous combustion incidents of the assembled battery (Croce et al., 1998; Song et al., 1999; Scrosati, 2000; Wang et al., 2014; Wu et al., 2017b; He et al., 2018a). However, the solid polymer electrolytes (SPEs) are excluded from the practical use because of their quite low ionic conductivity of the assembled lithium ion battery (Murata et al., 2000; Xie et al., 2012; Kim et al., 2015; Zhang H. et al., 2017; Wu et al., 2018). The ionic conductivity at room temperature can gain noticeable improvement when the polymer electrolyte membranes adsorb some liquid electrolytes to form the novel gel polymer electrolytes (GPEs), which are mainly composed of the polymer matrix and the entrapped liquid electrolytes (Zhang et al., 2007; Hu et al., 2015; Zhang M. Y. et al., 2017; Wang et al., 2018c). However, the poor mechanical strength of the swollen GPEs cannot well maintain the separation between the positive and negative active materials during the long-term Li+ insertion-extraction behaviors (Rao et al., 2012; Liu et al., 2017; Luo et al., 2017). Therefore, some countermeasures have been taken to circumvent the obstacles. Adding inert inorganic nano-particles, such as TiO2 (Wu et al., 2011; Chen et al., 2015; Zhang et al., 2015; He et al., 2018b), Al2O3 (Lee et al., 2014; Liang et al., 2015; Wu et al., 2017a), and SiO2 (Park et al., 2010; Li et al., 2013; Huang et al., 2017; Shim et al., 2017), into the polymer matrix to fabricate the composite polymer electrolytes (CPEs) has been ever proved to be an available and appealing approach to balance the contradiction between the ionic conductivity and mechanical strength at room temperature (Costa et al., 2013; Wang et al., 2018b). However, the poor dispersibility of the added nano-inorganic particles into the polymer substrate is also the barrier for the as-fabricated CPEs. Perovskite structural ABO3 particles doped with metal ions can produce more vacancies, which can facilitate the ions transfer to enhance the ionic conductivity as well as improving the mechanical strength (Kay and Bailey, 1957; Mather et al., 2007). In the work, spherical-like and honeycomb perovskite structural Li0.1Ca0.9TiO3 particles are successfully synthesized by spray drying combined with sintering, and the desirable CPEs are prepared by traditional phase inversion method. The corresponding electrochemical and battery performance of the CPEs are also carefully studied.
The spherical-like and honeycomb structural Li0.1Ca0.9TiO3 particles are prepared by spray drying combined with following calcination. At first, stoichiometric calcium acetate and lithium acetate are successively added into deionized water to form solution A, and the mixture of tetrabutyl titanate, acetylacetone, and absolute ethyl alcohol with the volume ratio of 4:1:4 is dropwise added into the solution A to obtain homogeneous solution B with continuous agitation at 40°C for 6 h. Secondly, the solution B is pumped into the spray drier machine (SD-2500) by peristaltic pump at 1,500 mL h−1 and atomized at 180°C with atomizing pressure of 0.2 MPa to product the precursor powders with conditions similar to the scheme (Yang et al., 2014; Su et al., 2018). The target product Li0.1Ca0.9TiO3 particles can be gained after the precursor powders are further calcined in air at 700°C for 6 h. All chemicals are purchased from Macklin Biochemical Co., Ltd. with analytical grade and used without any further purification.
The fabrication processes of the CPEs can be concisely summarized as fabrication and activation of the polymer electrolyte membranes. At first, a certain content of Li0.1Ca0.9TiO3, urea and poly (vinylidene fluoride-co-hexafluoropropylene) P(VDF-HFP) (Atofina, Kynar Flex, 12 wt.% HFP) are successively fed into the N, N-dimethylformamide (DMF) solvent to yield uniform coating solution under vigorous agitation at room temperature, in which Li0.1Ca0.9TiO3, urea and P(VDF-HFP) powders are used as dopant, pore-forming agent and polymer matrix, respectively, and the weight ratio is maintained at about 5:1:100. After that, the homogeneous casting solution is cast onto a pre-cleaned glass substrate with a doctor blade to prepare the wet membranes. Then, the wet membranes are immersed into deionized water for 12 h at room temperature to thoroughly fulfill phase transfer and the free-standing CPE membranes can be obtained by being dried for 24 h at 60°C to remove the residual solvent and then cut into a disk with a diameter about 16 mm for use (Wang et al., 2018b; Xiao et al., 2018). Secondly, the desirable CPEs can be acquired after immersing the as-prepared CPE membranes into 1.0 M LiPF6-EMC/EC/DMC (1:1:1, v/v/v) provided by Dongguan Shanshan Battery Materials Co., Ltd. for 0.5 h, which are labeled as CPE-LCT for convenience. The polymer electrolytes doped with commercial CaTiO3 and without inorganic particles are also fabricated using the same method for comparison and named as CPE-CT and CPE-0, respectively.
Scanning electron microscopy (SEM, JSM6301F) equipped with an energy dispersive X-ray spectrometer (EDS) and X-ray diffraction (XRD, Rint-2000) are used to investigate the micro-structure, chemical composition, and physical phase constitution of the as-prepared Li0.1Ca0.9TiO3 particles. The surface morphology and crystallinity of the as-fabricated CPE membranes are identified by SEM and XRD, respectively. The porosity (P) and liquid uptake rate (A) of the as-prepared CPE membranes are calculated according to the our previous work in the following Equations (1, 2), respectively, in which ρa and ρb are the density of n-butanol and the dry CPE membrane, ma (w1) and mb (w0) are the mass (weight) of the membranes with and without n-butanol, respectively (Xiao et al., 2016). The mechanical tensile strength (T) of the as-prepared CPE membranes is performed on an electronic universal testing machine (INSTRON-5500) at a crosshead speed of 100 mm min−1 at room temperature, which refers to the literature (Wang et al., 2018a). To reveal the electrochemical performance, the as-fabricated CPEs are packed in the simulated battery in the following three types. The first type is that the CPE is assembled between two stainless steel (SS) electrodes, i.e., SS/CPE/SS, which is employed to test the ionic conductivity at various temperatures (293–363 K) by electrochemical impedance spectroscopy (EIS) on the CHI660E electrochemical workstation with frequency range 105-1 Hz. The ionic conductivity can be calculated from the bulk resistance (R) according to Equation (3), where l is the thickness of the CPE, S is the effective contact area, R is obtained from the Nyquist impedance plots (Xiao et al., 2016). The second one is that the CPE is assembled between a lithium disk electrode and a SS electrode, i.e., Li/CPE/SS, which is utilized to evaluate the electrochemical working window of the CPE by the EIS from 2.50 to 6.65 V with a scanning rate of 5 mV s−1. The last one is that the CPE is packed between two lithium disk electrodes, i.e., Li/CPE/Li, which is used to monitor the interfacial resistance changes with different storage times at 30°C. The lithium ion transference number introduced by the literature (Bruce and Vincent, 1987; Xiao et al., 2016) of the symmetrical Li/CPE/Li cells is measured by the combination of Dc polarization and EIS techniques. The corresponding value can be calculated according to the reference in the following Equation (4), in which I0 and Iss are the initial and the steady current, R0 and Rss are the initial interfacial and the steady-state resistance, respectively, and ΔV is the potential difference (Xiao et al., 2016).
The charge-discharge cycling performance of the assembled Li/CPEs/LiCoO2 coin cells are performed on a Land Battery Test System (Wuhan Land Electronic Corporation, China) at different current densities (0.1, 0.2, 0.5, 1.0, and 2.0 C) with cut-off voltages of 2.75–4.25 V at room temperature, in which the working electrode is fabricated by casting the mixed slurry of 80 wt.% LiCoO2 as active material, 10 wt.% acetylene black as conductive agent and 10 wt.% polyvinylidene fluoride as binder onto aluminum foils with mass loading of 2–3 mg cm−2, and the thickness of the as-fabricated CPEs is about 120 μm (Xiao et al., 2016, 2018; Wang et al., 2018b).
Figure 1 displays the micro-structure, chemical composition, and physical phase constitution of the as-prepared Li0.1Ca0.9TiO3 particles. It can be clearly seen from Figures 1A,B that the SEM images present homo-dispersed spherical-like particles with the average diameter of 250 nm, which can be confirmed by the enlarged SEM image of the area 1 demonstrated in Figure 1C. It is worth noting that the Li0.1Ca0.9TiO3 particles show coarse and damaged surface in Figure 1C. It can be observed from the enlarged SEM image of the area 2 demonstrated in Figure 1D that the coarse and damaged surface of the as-prepared particles has abundant honeycomb structures. Therefore, we can speculate that the inside of the as-prepared Li0.1Ca0.9TiO3 particles may possess well-developed interpenetrating porous network structures. Those results indicate that the as-prepared Li0.1Ca0.9TiO3 particles can not only absorb and retain more liquid electrolytes, but also provide more extra passages for lithium ions transfer, which can markedly improve the battery performance. Figure 1E demonstrates the EDS results of the selected area 2 in Figure 1C. It can be obviously found that the as-synthesized nano-inorganic fillers are composed of Ca, Ti, and O elements and the percentage of Ca and Ti atoms is about 0.902:1, which is in accord with the predetermined stoichiometric ratio. The Li element cannot be detected in the EDS plots because of its less content and lighter weight (Sabiha et al., 2017). As demonstrated in Figure 1F, the XRD patterns of the as-synthesized Li0.1Ca0.9TiO3 particles are well indexed to the perovskite structural CaTiO3 (JCPDS#82-0228), which would benefit the lithium ions transfer. Moreover, few impurities corresponding to Li2TiO3 (JCPDS#51-0050) can be detected due to the excessive added lithium salt. Those results suggest that the spherical-like and honeycomb structural Li0.1Ca0.9TiO3 particles are successfully synthesized by spray drying combined with following calcination.
The SEM images of the polymer electrolyte membranes doped with different kinds of inorganic particles are displayed in Figure 2. The surface of the as-fabricated CPE membranes presents significant differences with adding the inorganic particles into the polymer substrate, where the surface gets smoother and the pore-size distribution becomes more uniform compared with the pure polymer electrolyte membrane. Although the added particles are obviously discovered in the CPE-CT and CPE-LCT membranes, few aggregations appear on the surface of the CPE-CT membrane displayed in Figure 2B, which can be ascribed to the high specific surface energy of the added commercial nano-CaTiO3 powders. The as-synthesized Li0.1Ca0.9TiO3 particles can be uniformly dispersed into the polymer matrix demonstrated in Figure 2C because of their unique spherical-like and honeycomb structure, which can be confirmed by the partial enlarged SEM image of the selected area 1 displayed in Figure 2D. The added Li0.1Ca0.9TiO3 particles well dispersed into the polymer electrolyte membranes with abundant micro-pore structures can not only enhance the mechanical properties by providing more physical crosslinking sites, but also improve the ionic conductivity by retaining more liquid electrolytes at the same time, which can be proved by the results listed in Table 1. As listed in Table 1, the porosity, uptake rate and tensile strength of the as-prepared CPE membranes gain remarkable improvements with doping the inorganic fillers into the polymer substrate, in which the values of the CPE-LCT membrane can reach to the highest value of about 92.73, 168.5%, and 27.32 Mpa, respectively. Clearly, these results can be mainly to the unique spherical-like and honeycomb structural of the added Li0.1Ca0.9TiO3 particles, in which the external honeycomb structure can provide more space to store liquid electrolytes and transfer lithium ions and the inert spherical-like structure can maintain the mechanical properties of the membranes.
Figure 2. SEM images of the different CPE membranes (A, CPE-0; B, CPE-CT; C, CPE-LCT) and the partial enlarged SEM image of area 1 (D).
Table 1. Porosity, uptake rate, tensile strength, ionic conductivity, activation energy, and lithium ion transference number of different CPE membranes at room temperature.
Figure 3 demonstrates the XRD patterns of the as-prepared Li0.1Ca0.9TiO3 powders and different CPE membranes. It can be observed from Figure 3 that the XRD patterns of the doped CPE membranes present distinct differences compared to the pristine P(VDF-HFP) one, in which the characteristic diffraction peaks of the polymer matrix P(VDF-HFP) at around 18.3 and 26.6° disappear and the one at 20.0° gets weak. Those results suggest that adding inorganic particles into the polymer matrix can impair the crystallinity of the polymer electrolyte membranes and release more amorphous areas for lithium ions transfer, which are the same as our previous results (Wang et al., 2018c). What is noteworthy is that the CPE-LCT membrane demonstrated in Figure 3 presents the weakest intensity, and we have reasons to speculate that the CPE-LCT may have high ionic conductivity at room temperature, which can be partly attributed to the Lewis acid-base interactions between the doped particles and the polymer chains, and partly to the increasing amorphous areas (Xiao et al., 2014a). Moreover, the new peak can be observed at 32.6° in the doped CPE membranes, which can be ascribed to the characteristic diffraction peak of the as-synthesized perovskite Li0.1Ca0.9TiO3 inorganic particles that are well indexed to the JCPDS#82-0228.
To further investigate the ionic conductivity of the as-prepared CPEs, we have tested the EIS pots of the assembled SS/CPE/SS battery at different temperatures and the corresponding curves on reciprocal temperature dependence of ionic conductivity are demonstrated in Figure 4A. It can be distinctly discovered that the curve of the SS/CPE-LCT/SS battery is always above the other ones, which indicates the CPE doped with Li0.1Ca0.9TiO3 powders may possess the highest ionic conductivity. The ionic conductivity at room temperature of the various CPEs is demonstrated in Table 1, in which the value of the CPE-0, CPE-CT, and CPE-LCT is about 1.954, 2.818, and 3.947 mS cm−1, respectively. As displayed in Figure 4A, the plots of the reciprocal temperature vs. ionic conductivity can well fitted by the Arrhenius equation, which indicates that the lithium ions transfer in the CPEs system is mainly attributed to the free diffusions rather than the hopping movements elaborated in our previous work (Xiao et al., 2014b, 2016, 2018; Wang et al., 2018a). The lithium ions can easily migrate from the inside of the spherical-like and honeycomb structural Li0.1Ca0.9TiO3 particles to the interface between the electrodes and the as-prepared CPEs to participate into the intercalation and deintercalation processes in the CPEs system. The corresponding threshold energy of the lithium ions transfer for the different CPEs is calculated and listed in Table 1. As demonstrated in Table 1, the CPE-LCT has the lowest activation energy of about 4.019 KJ mol−1. The highest ionic conductivity with the lowest activation energy at room temperature of the as-prepared CPE-LCT can be explained as the following reasons. Firstly, the appropriate size and uniform distribution of the micropores in the as-fabricated CPE-LCT membrane can adsorb and hold more liquid electrolytes, which can significantly promote the ionic conductivity of the system. Secondly, the Lewis acid-base interactions between the added inorganic particles and the polymer matrix can release more amorphous areas for lithium ions transfer (Xiao et al., 2018). Moreover, the lithium ions can migrate in the extra passageways provided by the abundant and interpenetrated micropores in the as-prepared honeycomb structural Li0.1Ca0.9TiO3 particles. The as-synthesized Li0.1Ca0.9TiO3 particles can not only dramatically enhance the ionic conductivity, but also improve the mechanical strength of the corresponding doped CPE membranes at the same time, which are principally ascribed to the excellent mechanical performance of the unique spherical-like and honeycomb structure. As displayed in Figure 4B, the mechanical strength is sharply enhanced from 18.84 MPa of the CPE-0 membrane, to 26.87 MPa of the CPE-CT one, and to 27.32 MPa of the CPE-LCT one. Moreover, the elongations of the CPE-CT and CPE-LCT membranes are also apparently greater than the one of the CPE-0 membrane, in which the elongation at the critical point is about 19.7 and 21.4% for the CPE-CT and CPE-LCT membranes, respectively, and the value is only 13.1% for the pure one. Those results can be ascribed to the more crosslinking sites provided by the doped particles, which can well improve the flexibility of the as-prepared polymer electrolyte membranes to enhance the battery performance.
Figure 4. Fitting curves on reciprocal temperature dependence of ionic conductivity (A) and the relation of stress and strain (B) of the different CPE membranes.
Figure 5 displays the LSV plots of the different CPE membranes. The electrochemical working window of the assembled SS/CPEs/Li cell with inorganic particles is much wider than the one of the cell with the CPE-0, in which the value of the steady electrochemical working window is about 4.3, 5.0, and 5.2 V for the CPE-0, CPE-CT, and CPE-LCT membrane, respectively. The dramatically enhanced working voltage of the doped CPE membranes can be resulted from the gelatinization of the entrapped liquid electrolytes and the added inert nano-particles. The gelation enhances the stability of the CPE membranes due to the interactions between the entrapped liquid electrolytes and the polymer matrix, which can restrict the free movement and the activity of the liquid electrolytes in the as-prepared CPEs (Wang et al., 2018a). The results can be ulteriorly reinforced by adding the as-synthesized Li0.1Ca0.9TiO3 particles into the polymer matrix because of their intrinsic chemical inertness and unique spherical-like and honeycomb structure. Based on the analysis mentioned above, it is creditable to conclude that the CPEs doped with the as-prepared spherical-like and honeycomb structural Li0.1Ca0.9TiO3 particles can provide high lithium ion transference number. Therefore, we design experiments to calculate the lithium ion transference number. The Dc polarization plots of the assembled Li/CPE-LCT/Li battery are demonstrated in Figure 6 and the corresponding results calculated to Equation (4) are displayed in Table 1. It can be observed from Table 1 that the lithium ion transference number increases from 0.1623 of the CPE-0, to 0.2764 and 0.4962 of the CPE-CT and CPE-LCT, respectively, which can perfectly verify the above suppositions. Those results can be mainly ascribed to the added spherical-like and honeycomb structural Li0.1Ca0.9TiO3 particles, which can not only provide more passageways for ion transfer, but also release more lithium ions to increase the carrier concentration.
Figure 6. Dc polarization plots of the assembled Li/CPE-LCT/Li battery and the insert are Nyquist plots before and after polarization.
Interface stability is a key parameter for the practical polymer electrolytes in the lithium ion battery because it can seriously exert an effect on the initial charge-discharge and rate performance of the as-assembled battery (Zhang M. Y. et al., 2017). Therefore, the EIS variations of the Li/CPEs/Li simulated cells with the CPEs for different storage times at 30°C are investigated and the corresponding plots are displayed in Figure 7. It can be easily found from Figure 7 that the shape of the curves of the assembled Li/CPEs/Li simulated cells with three kinds of polymer electrolytes show significant differences, in which the plots of the Li/CPE-CT/Li and Li/CPE-LCT/Li simulated batteries are composed of a semicircle at high and medium frequency range originated from the bulk resistance (Rb) of polymer electrolyte and a compressed arc at low frequency range derived from the interfacial resistance (Ri), while the one of the Li/CPE-0/Li simulated cell simply contains a semicircle in the whole tested frequency range. Those differences can be mainly ascribed to the different interfacial performance of the as-assembled simulated cells with different CPEs. To further reveal the mechanism of the interfacial performance, the EIS plots are fitted by the corresponding equivalent circuit displayed in the insert for the each plot, in which we decompose interfacial resistance (Ri) into interfacial reaction resistance (Rct) and the resistance of charge transfer (Rf) in the electronic double-layer for convenience (Xiao et al., 2012). Apparently, the fitting curves are well-matched with the experimental data for the different CPEs shown in Figure 7. The Rb value in each plot keeps constant and the Rct value increases firstly and then reaches a stable value, in which the Rct values of the CPE-CT and CPE-LCT can stabilize at around 943 and 508 Ω after being monitored for 5 days at room temperature, while the Rct value of the CPE-0 keeps growing. The results suggest that the battery assembled with the CPEs may present excellent interfacial performance, especially with the CPE-LCT, which can be mainly ascribed to the added spherical-like and honeycomb structural Li0.1Ca0.9TiO3 particles that can markedly improve the compatibility between the electrodes and the as-prepared CPEs by entrapping any impurities such as water and trace organic solvent to inhibit the destructive reaction on the electrodes (Xiao et al., 2016).
Figure 7. Nyquist plots of the assembled Li/CPEs/Li simulated cells with different CPEs for various storage times at 30°C (A, CPE-0; B, CPE-CT; C, CPE-LCT), where the insert shows the corresponding equivalent circuit.
Initial charge-discharge curves of the assembled Li/CPE-LCT/LiCoO2 cell at different current densities (0.1, 0.2, 0.5, 1.0, and 2.0 C) are shown in Figure 8A. There is no difference between the cells assembled with the as-prepared CPE membranes and the commercial polyolefin membrane in terms of the shape of the curves, which suggests that the charge-discharge mechanism of the battery cannot be affected when the as-fabricated CPEs are assembled into the coin cell. As found in Figure 8A, the discharge specific capacity slowly declines from 145.7 mAh g−1 at 0.1 C, to 139.5 and 132.4 mAh g−1 at 0.2 and 0.5 C, respectively, and maintains at 116.8 mAh g−1 even at 2.0 C, which indicate that the battery assembled with the CPE-LCT presents excellent charge-discharge performance. Figure 8B demonstrates the cycle and coulombic efficiency curves of the Li/CPE-LCT/LiCoO2 coin cell at different current densities (0.1, 0.2, 0.5, 1.0, and 2.0 C). It can be obviously observed that the coulombic efficiency of the assembled battery is ~100% except for the first two cycles, which can be mainly ascribed to the formation of steady solid electrolyte interphase films on the surface of the electrodes (Reddy et al., 2013). The discharge capacity gently fades with increasing the current density during the repetitive cycles, in which the battery can deliver about 125.7 mAh g−1 discharge specific capacity at 1.0 C after 100 cycles with 86.32% capacity retention ratio. Moreover, the discharge specific capacity of the battery can rebound back to 136.4 mAh g−1 when the current density drops down to 0.1 C again after 190 cycles. Those results suggest that the Li/CPE-LCT/LiCoO2 coin cell shows outstanding rate cycle performance with approaching 100% coulombic efficiency.
Figure 8. Initial charge-discharge (A) and cycle and coulombic efficiency (B) curves of the assembled Li/CPE-LCT/LiCoO2 coin cell at different current densities.
The CPEs doped with the spherical-like and honeycomb structural Li0.1Ca0.9TiO3 particles synthesized by spray drying combined with following calcination are successfully fabricated by the classical phase inversion processes. The investigation results show that the CPEs present excellent physicochemical properties, such as improved ionic conductivity and lithium ion transference number, enhanced interfacial stability, and mechanical strength and so on. The assembled Li/CPE-LCT/LiCoO2 coin cell can also deliver high initial discharge specific capacity and steady rate cycle performance. Those excellent results indicate that the as-prepared CPEs modified with the spherical-like and honeycomb structural Li0.1Ca0.9TiO3 particles can be developed as a new kind of practical polymer electrolyte.
WX, PM, and JL contributed conception and design of the study. CM organized the database. XY and MT performed the statistical analysis. ZW wrote the first draft of the manuscript. XY, YZ, YJ, and MT wrote sections of the manuscript.
This work was financially supported by the National Natural Science Foundation of China (No. 51404038, 51874046, and 51503020), the Educational Commission of Hubei Province Foundation of China (No. B2016040), and the Yangtze Youth Talents Fund (No. 2016cqr05).
The authors declare that the research was conducted in the absence of any commercial or financial relationships that could be construed as a potential conflict of interest.
Bruce, P. G., and Vincent, C. A. (1987). Steady state current flow in solid binary electrolyte cells. J. Electroanal. Chem. Interfac. Electrochem. 225, 1–17. doi: 10.1016/0022-0728(87)80001-3
Chen, W., Liu, Y., Ma, Y., and Yang, W. (2015). Improved performance of lithium ion battery separator enabled by co-electrospinnig polyimide/poly(vinylidene fluoride-co-hexafluoropropylene) and the incorporation of TiO2-(2-hydroxyethyl methacrylate). J. Power Sources 273, 1127–1135. doi: 10.1016/j.jpowsour.2014.10.026
Costa, C. M., Silva, M. M., and Lanceros-Mendez, S. (2013). Battery separators based on vinylidene fluoride (VDF) polymers and copolymers for lithium ion battery applications. RSC Adv. 3, 11404–11417. doi: 10.1039/c3ra40732b
Croce, F., Appetecchi, G. B., Persi, L., and Scrosati, B. (1998). Nanocomposite polymer electrolytes for lithium batteries. Nature 394:456. doi: 10.1038/28818
He, Z., Jiang, Y., Zhu, J., Wang, H., Li, Y., Zhou, H., et al. (2018a). N-doped carbon coated LiTi2(PO4)3 as superior anode using PANi as carbon and nitrogen bi-sources for aqueous lithium ion battery. Electrochim. Acta 279, 279–288. doi: 10.1016/j.electacta.2018.05.096
He, Z., Li, M., Li, Y., Zhu, J., Jiang, Y., Meng, W., et al. (2018b). Flexible electrospun carbon nanofiber embedded with TiO2 as excellent negative electrode for vanadium redox flow battery. Electrochim. Acta 281, 601–610. doi: 10.1016/j.electacta.2018.06.011
Hu, P., Duan, Y., Hu, D., Qin, B., Zhang, J., Wang, Q., et al. (2015). Rigid-flexible coupling high ionic conductivity polymer electrolyte for an enhanced performance of LiMn2O4/graphite battery at elevated temperature. ACS Appl. Mater. Interfaces 7, 4720–4727. doi: 10.1021/am5083683
Huang, W., Liao, Y., Li, G., He, Z., Luo, X., and Li, W. (2017). Investigation on polyethylene supported poly(butyl methacrylate-acrylonitrile-styrene) terpolymer based gel electrolyte reinforced by doping nano-SiO2 for high voltage lithium ion battery. Electrochim. Acta 251, 145–154. doi: 10.1016/j.electacta.2017.08.095
Kay, H. F., and Bailey, P. C. (1957). Structure and properties of CaTiO3. Acta Crystallogr. 10, 219–226. doi: 10.1107/S0365110X57000675
Kim, J. G., Son, B., Mukherjee, S., Schuppert, N., Bates, A., Kwon, O., et al. (2015). A review of lithium and non-lithium based solid state batteries. J. Power Sources 282, 299–322. doi: 10.1016/j.jpowsour.2015.02.054
Lee, J., Lee, C.-L., Park, K., and Kim, I.-D. (2014). Synthesis of an Al2O3-coated polyimide nanofiber mat and its electrochemical characteristics as a separator for lithium ion batteries. J. Power Sources 248, 1211–1217. doi: 10.1016/j.jpowsour.2013.10.056
Li, W., Xing, Y., Xing, X., Li, Y., Yang, G., and Xu, L. (2013). PVDF-based composite microporous gel polymer electrolytes containing a novelsingle ionic conductor SiO2(Li+). Electrochim. Acta 112, 183–190. doi: 10.1016/j.electacta.2013.08.179
Liang, X., Yang, Y., Jin, X., Huang, Z., and Kang, F. (2015). The high performances of SiO2/Al2O3-coated electrospun polyimide fibrous separator for lithium-ion battery. J. Memb. Sci. 493, 1–7. doi: 10.1016/j.memsci.2015.06.016
Liu, J., Wu, X., He, J., Li, J., and Lai, Y. (2017). Preparation and performance of a novel gel polymer electrolyte based on poly(vinylidene fluoride)/graphene separator for lithium ion battery. Electrochim. Acta 235, 500–507. doi: 10.1016/j.electacta.2017.02.042
Luo, X., Liao, Y., Zhu, Y., Li, M., Chen, F., Huang, Q., et al. (2017). Investigation of nano-CeO2 contents on the properties of polymer ceramic separator for high voltage lithium ion batteries. J. Power Sources 348, 229–238. doi: 10.1016/j.jpowsour.2017.02.085
Mather, G. C., Islam, M. S., and Figueiredo, F. M. (2007). Atomistic study of a CaTiO3-based mixed conductor: defects, nanoscale clusters, and oxide-ion migration. Adv. Funct. Mater. 17, 905–912. doi: 10.1002/adfm.200600632
Murata, K., Izuchi, S., and Yoshihisa, Y. (2000). An overview of the research and development of solid polymer electrolyte batteries. Electrochim. Acta 45, 1501–1508. doi: 10.1016/S0013-4686(99)00365-5
Park, J.-H., Cho, J.-H., Park, W., Ryoo, D., Yoon, S.-J., Kim, J. H., et al. (2010). Close-packed SiO2/poly(methyl methacrylate) binary nanoparticles-coated polyethylene separators for lithium-ion batteries. J. Power Sources 195, 8306–8310. doi: 10.1016/j.jpowsour.2010.06.112
Rao, M., Geng, X., Liao, Y., Hu, S., and Li, W. (2012). Preparation and performance of gel polymer electrolyte based on electrospun polymer membrane and ionic liquid for lithium ion battery. J. Memb. Sci. 399–400, 37–42. doi: 10.1016/j.memsci.2012.01.021
Reddy, M. V., Subba Rao, G. V., and Chowdari, B. V. (2013). Metal oxides and oxysalts as anode materials for Li ion batteries. Chem. Rev. 113, 5364–5457. doi: 10.1021/cr3001884
Sabiha, S., Mohammad Saleem, K., Imran, R., Kamran, R., Noor-ul, A., Muhammad, H., et al. (2017). Morphological, mechanical and thermo-kinetic characterization of coal ash incorporated high performance PEO/PMMA thin film electrolyte composites. Mater. Res. Express 4:115304. doi: 10.1088/2053-1591/aa9757
Scrosati, B. (2000). Recent advances in lithium ion battery materials. Electrochim. Acta 45, 2461–2466. doi: 10.1016/S0013-4686(00)00333-9
Shim, J., Kim, H. J., Kim, B. G., Kim, Y. S., Kim, D.-G., and Lee, J.-C. (2017). 2D boron nitride nanoflakes as a multifunctional additive in gel polymer electrolytes for safe, long cycle life and high rate lithium metal batteries. Energy Environ. Sci. 10, 1911–1916. doi: 10.1039/c7ee01095h
Song, J. Y., Wang, Y. Y., and Wan, C. C. (1999). Review of gel-type polymer electrolytes for lithium-ion batteries. J. Power Sources 77, 183–197. doi: 10.1016/S0378-7753(98)00193-1
Su, M., Wan, H., Liu, Y., Xiao, W., Dou, A., Wang, Z., et al. (2018). Multi-layered carbon coated Si-based composite as anode for lithium-ion batteries. Powder Technol. 323, 294–300. doi: 10.1016/j.powtec.2017.09.005
Wang, J., Zhang, Q., Li, X., Xu, D., Wang, Z., Guo, H., et al. (2014). Three-dimensional hierarchical Co3O4/CuO nanowire heterostructure arrays on nickel foam for high-performance lithium ion batteries. Nano Energy 6, 19–26. doi: 10.1016/j.nanoen.2014.02.012
Wang, Z., Miao, C., Xiao, W., Zhang, Y., Mei, P., Yan, X., et al. (2018a). Effect of different contents of organic-inorganic hybrid particles poly(methyl methacrylate)-ZrO2 on the properties of poly(vinylidene fluoride-hexafluoroprolene)-based composite gel polymer electrolytes. Electrochim. Acta 272, 127–134. doi: 10.1016/j.electacta.2018.04.040
Wang, Z., Miao, C., Zhang, Y., Fang, R., Yan, X., Jiang, Y., et al. (2018b). Preparation of monodispersed ZrO2 nanoparticles and their applications in poly[(vinylidene fluoride)-co-hexafluoropropylene]-based composite polymer electrolytes. Polym. Int. 67, 894–900. doi: 10.1002/pi.5576
Wang, Z., Xiao, W., Miao, C., Mei, P., Yan, X., Jiang, Y., et al. (2018c). Enhanced thermal and electrochemical properties of poly(vinylidene fluoride-co-hexafluoropropylene)-based composite polymer electrolytes doped with CaTiO3 dielectric ceramics. Solid State Ionics 324, 176–182. doi: 10.1016/j.ssi.2018.07.008
Wu, D., Deng, L., Sun, Y., Teh, K. S., Shi, C., Tan, Q., et al. (2017a). A high-safety PVDF/Al2O3 composite separator for Li-ion batteries via tip-induced electrospinning and dip-coating. RSC Adv. 7, 24410–24416. doi: 10.1039/c7ra02681a
Wu, L., Hu, Y., Zhang, X., Liu, J., Zhu, X., and Zhong, S. (2018). Synthesis of carbon-coated Na2MnPO4F hollow spheres as a potential cathode material for Na-ion batteries. J. Power Sources 374, 40–47. doi: 10.1016/j.jpowsour.2017.11.029
Wu, N., Cao, Q., Wang, X., Li, S., Li, X., and Deng, H. (2011). In situ ceramic fillers of electrospun thermoplastic polyurethane/poly(vinylidene fluoride) based gel polymer electrolytes for Li-ion batteries. J. Power Sources 196, 9751–9756. doi: 10.1016/j.jpowsour.2011.07.079
Wu, X., Xiang, Y., Peng, Q., Wu, X., Li, Y., Tang, F., et al. (2017b). Green-low-cost rechargeable aqueous zinc-ion batteries using hollow porous spinel ZnMn2O4 as the cathode material. J. Mater. Chem. A 5, 17990–17997. doi: 10.1039/c7ta00100b
Xiao, W., Li, X., Guo, H., Wang, Z., Li, Y., and Yang, B. (2014a). Preparation and physicochemical performances of poly[(vinylidene fluoride)-co-hexafluoropropylene]-based composite polymer electrolytes doped with modified carbon nanotubes. Polym. Int. 63, 307–314. doi: 10.1002/pi.4506
Xiao, W., Li, X., Guo, H., Wang, Z., Zhang, Y., and Zhang, X. (2012). Preparation of core-shell structural single ionic conductor SiO2@Li+ and its application in PVDF-HFP-based composite polymer electrolyte. Electrochim. Acta 85, 612–621. doi: 10.1016/j.electacta.2012.08.120
Xiao, W., Miao, C., Yin, X., Zheng, Y., Tian, M., Li, H., et al. (2014b). Effect of urea as pore-forming agent on properties of poly(vinylidene fluoride-co-hexafluoropropylene)-based gel polymer electrolyte. J. Power Sources 252, 14–20. doi: 10.1016/j.jpowsour.2013.11.110
Xiao, W., Wang, Z., Miao, C., and Yan, X. (2016). Preparation of Si/Ti mesoporous molecular sieve and its application in P(VDF-HFP)-based composite polymer electrolytes. Electrochim. Acta 216, 467–474. doi: 10.1016/j.electacta.2016.09.057
Xiao, W., Wang, Z., Zhang, Y., Fang, R., Yuan, Z., Miao, C., et al. (2018). Enhanced performance of P(VDF-HFP)-based composite polymer electrolytes doped with organic-inorganic hybrid particles PMMA-ZrO2 for lithium ion batteries. J. Power Sources 382, 128–134. doi: 10.1016/j.jpowsour.2018.02.012
Xie, K., Lu, Z., Huang, H., Lu, W., Lai, Y., Li, J., et al. (2012). Iron supported C@Fe3O4 nanotube array: a new type of 3D anode with low-cost for high performance lithium-ion batteries. J. Mater. Chem. 22, 5560–5567. doi: 10.1039/c2jm15955d
Yang, S., Huang, G., Hu, S., Hou, X., Huang, Y., Yue, M., et al. (2014). Improved electrochemical performance of the Li1.2Ni0.13Co0.13Mn0.54O2 wired by CNT networks for lithium-ion batteries. Mater. Lett. 118, 8–11. doi: 10.1016/j.matlet.2013.11.071
Zhang, H., Li, C., Piszcz, M., Coya, E., Rojo, T., Rodriguez-Martinez, L. M., et al. (2017). Single lithium-ion conducting solid polymer electrolytes: advances and perspectives. Chem. Soc. Rev. 46, 797–815. doi: 10.1039/c6cs00491a
Zhang, H. P., Zhang, P., Li, Z. H., Sun, M., Wu, Y. P., and Wu, H. Q. (2007). A novel sandwiched membrane as polymer electrolyte for lithium ion battery. Electrochem. commun. 9, 1700–1703. doi: 10.1016/j.elecom.2007.03.021
Zhang, M. Y., Li, M. X., Chang, Z., Wang, Y. F., Gao, J., Zhu, Y. S., et al. (2017). A sandwich PVDF/HEC/PVDF gel polymer electrolyte for lithium ion battery. Electrochim. Acta 245, 752–759. doi: 10.1016/j.electacta.2017.05.154
Keywords: Li0.1Ca0.9TiO3, composite polymer electrolyte, spherical-like, honeycomb, lithium ion battery
Citation: Xiao W, Wang Z, Miao C, Mei P, Zhang Y, Yan X, Tian M, Jiang Y and Liu J (2018) High Performance Composite Polymer Electrolytes Doped With Spherical-Like and Honeycomb Structural Li0.1Ca0.9TiO3 Particles. Front. Chem. 6:525. doi: 10.3389/fchem.2018.00525
Received: 26 August 2018; Accepted: 11 October 2018;
Published: 25 October 2018.
Edited by:
Jiexi Wang, Central South University, ChinaReviewed by:
Shaohua Luo, Northeastern University, United StatesCopyright © 2018 Xiao, Wang, Miao, Mei, Zhang, Yan, Tian, Jiang and Liu. This is an open-access article distributed under the terms of the Creative Commons Attribution License (CC BY). The use, distribution or reproduction in other forums is permitted, provided the original author(s) and the copyright owner(s) are credited and that the original publication in this journal is cited, in accordance with accepted academic practice. No use, distribution or reproduction is permitted which does not comply with these terms.
*Correspondence: Wei Xiao, eHd5bHlxMjAwNkAxMjYuY29t
Jingjing Liu, bGpqc3gyMDA3QDE2My5jb20=
Disclaimer: All claims expressed in this article are solely those of the authors and do not necessarily represent those of their affiliated organizations, or those of the publisher, the editors and the reviewers. Any product that may be evaluated in this article or claim that may be made by its manufacturer is not guaranteed or endorsed by the publisher.
Research integrity at Frontiers
Learn more about the work of our research integrity team to safeguard the quality of each article we publish.