Introduction: Additive manufacturing via melt direct writing has limits on the dimensions of individual filaments due to the Barus effect. The diameter of the filament is largely defined by the nozzle diameter, so scaffolds tend to have uniform strut size when printed. Direct writing of significantly smaller struts (as small as 820nm)[1] is possible using melt electrospinning writing (MEW), which uses electrical forces to stretch the molten polymer onto a collection stage. Importantly, these fibers can be stacked accurately to form 3D scaffolds[2]. Since the mechanism of fiber production for MEW is considerably different from extrusion through an orifice, we investigated how instrument parameters, particularly mass flow rates, can influence the diameter of the filament during the print.
Materials and Methods: A custom-built, electrically heated MEW device was mounted above an x-y stage where poly(ε-caprolactone) (PCL PURASORB PC12, medical grade ) melt was direct written onto a titanium or glass collector. Using a "nozzle to stage" gap of 6 mm and a temperature of 85 °C, the melt was pushed to the 22 G nozzle using between 0.2 and 2 bar of pressure. A standard voltage of 5 kV and -1.5 kV were applied to the nozzle and collector throughout the experiments. The critical translation speed (CTS) was defined as the speed where the fiber transitions from coiled/buckled to straight.
Results: Consistent diameter fibers between 3 and 33 µm could be fabricated with a single nozzle, using changes in air pressure only, with no change in other parameters. For each fiber diameter generated, the CTS differed with the smaller diameter fibers requiring faster stage translation to generate a straight fiber. The maximum time required for the diameter to change from one pressure to the other was between seconds and minutes, depending on the magnitude change.
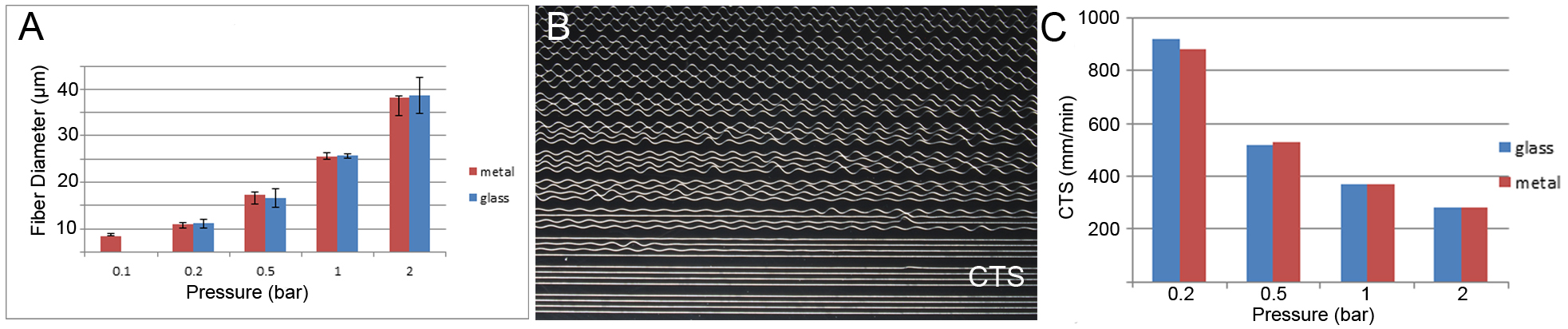
Figure 1: A) Effect of air pressure on fiber diameter; B) example of a CTS measurement with the line where CTS is reached indicated; C) Effect of pressure on the measured CTS.
Therefore, the variable micro-scale diameters of the filaments allowed continuous alterations during the printing process. No significant differences between glass and titanium on collection speeds indicated that information gathered from these two substrates are comparable to each other. When the diameters are changed during the print, fiber arrays such as those in Figure 2 can be fabricated for neural or general tissue engineering studies.
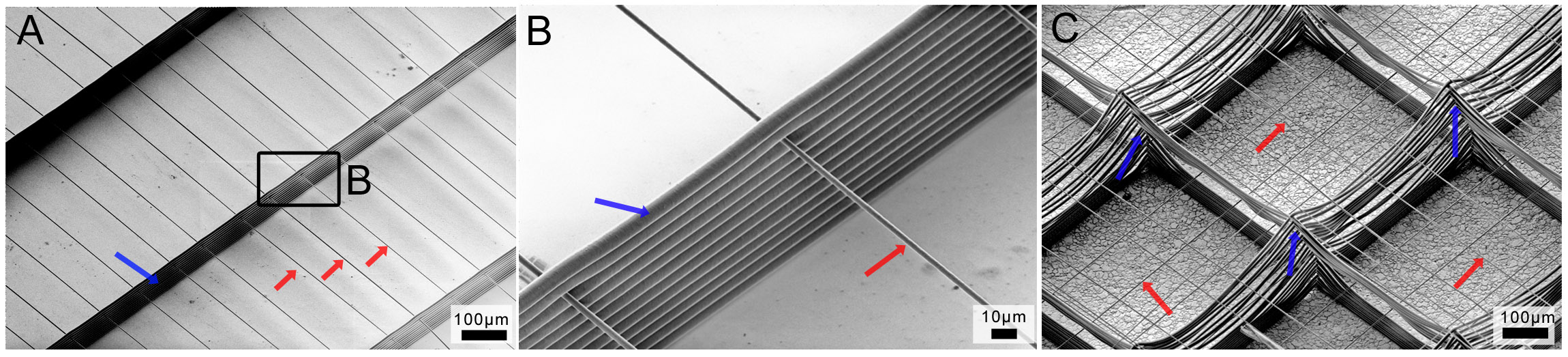
Figure 2: A-B) SEM images of small diameter (3µm) suspended fiber arrays (red arrows) where individual filaments are sandwiched between large diameter (8-10µm) frames (blue arrows). Small diameter fibers are suspended amongst large diameter fiber frames as part of a bimodal scaffold strategy.
Conclusions: The melt flow rate to the nozzle has a large impact on fiber diameter, so that filament diameters can be altered during the direct writing process using air pressure alone. Compared to other fiber fabrication techniques like solution electrospinning or fused deposition modeling, this phenomenon allows to change the fiber diameter during processing and enables to print zonal constructs with unique structural properties. The CTS was measured and was found to be inversely proportional to the diameter of the fiber. This opens up the potential to manufacture well-defined gradient, bimodal or multiphasic scaffolds from medical grade polymers in a solvent free approach.
We thank the European Research Council for funding under grant agreement no. 617989 (consolidator grant Design2Heal).
References:
[1] Brown TD, Dalton PD, Hutmacher DW. (2011) Direct Writing by Way of Melt Electrospinning. Adv Mater, 23, 5651-57.
[2] Hochleitner G, Jüngst T, Brown TD, Hahn K, Moseke C, Dalton PD, Groll J (2015) Additive Manufacturing with Sub-micron Melt Electrospun Filaments. Biofabrication. 7, 035002.