Introduction: The successful fixation of non-cemented titanium femoral stems depends on the contact surface between the implant and the bone, so that proper porosity dimension and roughness are reported to stimulate the growth of the bone tissue into the implant treated surface[1],[2]. Titanium plasma spray is a consolidated coating technology for the deposition of a titanium dioxide layer aiming at the improvement of the osseointegration phenomenon[3]. However, there still are challenges in terms of the fatigue life of products submitted to surface modification[4]. In this sense, the purpose of this work is to evaluate the fatigue performance of a specific femoral stem geometry subjected to thermal plasma spray of titanium powder.
Materials and Methods: Ti-6Al-4V femoral stems developed by a Brazilian implant manufacturer with a specific geometry and with surface modified by the deposition of titanium powder through thermal plasma spray were employed in this evaluation. Fatigue tests were conducted according to the parameters and conditions specified in ISO 7206-4 standard[5], such as a maximum load of 2,300 N. The simulation of stress distribution through finite element analysis was performed using SolidWorks software.
Results and Discussion: The as received femoral stem with surface modified by thermal plasma spray of titanium powder is presented in Figure 1(a). The porosity of the coating aimed at the increase of the surface area in order to improve the osseointegration phenomenon and bone growth, without a major reduction in the fatigue performance. However, the standardized fatigue tests led to the failure of the stems at approximately 150.000 cycles. As observed in Figure 1(b), the fatigue crack nucleated in the coated surface and in the transition between the bone cement and the free portion of the stem.
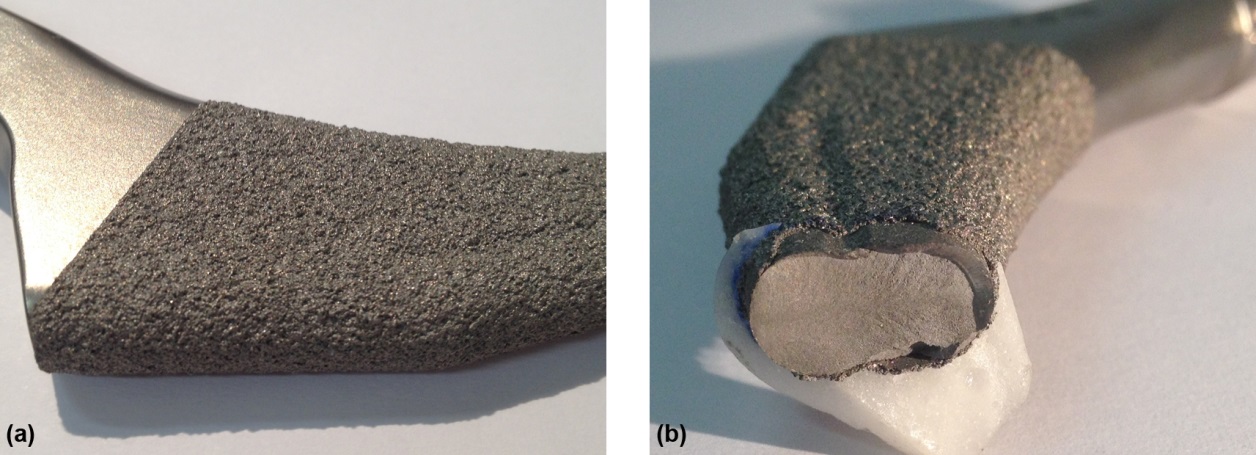
Figure 1 – Coated femoral stem: (a) as received and (b) after fatigue test.
Simulation of stress distribution presented in Figure 2 shows that the position of higher tensile stress is intuitively located in the back of the stem and is equal to 650 MPa, which corresponds to approximately 76% of the alloy yield strength. Under this condition, although the stem could be in the high cycle fatigue regime, the deleterious effect of the coating was sufficient to induce the failure of this femoral system geometry.
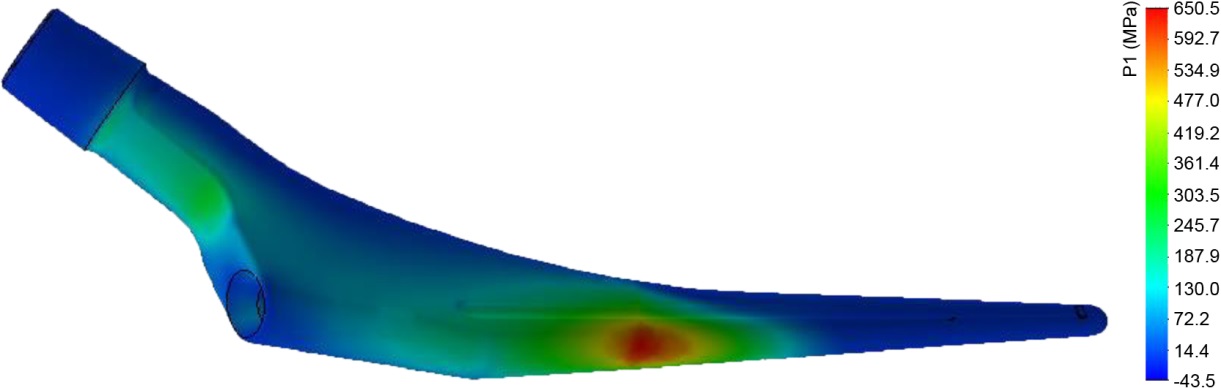
Figure 2 – Distribution of the main stress in the femoral stem.
Conclusions: The surface modification by the deposition of titanium powder through plasma spray led to the reduction in the fatigue performance and, for the studied geometry of the femoral system, to the failure of the coated stem.
FAPESP and FINEP
References:
[1] PILLIAR, R. M. Powder metal-made orthopaedic implants with porous surface for fixation by tissue ingrowth. Clinical Orthopaedics, v 176, p.42-51. 1983.
[2] BOBYN, J. D.; PILLIAR, R. M.; CAMERON H. U.; et al. The optimum pore size for the fixation of porous-surfaces metal implants by the ingrowth of bone. Clinical Orthopaedics, v 149. p.291-298. 1980.
[3] GARDON, M.; GUILEMANY J. M. Milestones in functional titanium dioxide thermal spray coatings: a review. Journal of Thermal Spray Technology. v 23, p. 577-595. 2014.
[4] RYAN, G.; PANDIT, A.; APATSIDIS, D. P. Fabrication methods of porous metals for use in orthopaedic applications. Biomaterials. v. 27, p. 2651-2670. 2006.
[5] INTERNATIONAL ORGANIZATION FOR STANDARDIZATION. ISO 7206-4:2010 Implants for surgery – Partial and total hip joint prostheses – Part 4: Determination of endurance properties and performance of stemmed femoral components.