Introduction: The electrospinning is a well-established technique widely used for the fabrication of fibrous mats for tissue engineering applications. A huge number and varieties of polymers could be processed by the electrospinning technique, but often the use of organic toxic solvents is required. Recently, the introduction of the “Green Electrospinning” concept[1] and the awareness about the disadvantages related to the use of toxic solvents have raised the interest in the use of less or not toxic solvents (benign solvents) for electrospinning[2]. In this framework, the aim of the present work has been the optimization of the electrospinning of poly(epsilon-caprolactone) (PCL) using acetic acid as solvent. The suitability of this solvent has been tested also for the fabrication of patterned mats and for the fabrication of composite electrospun mats, obtained with the addition of bioactive glass (BG) particles.
Materials and Methods: Electrospun mats were obtained starting from a 20% w/v PCL (80kDa, Sigma Aldrich) solution in acetic acid (VWR). For the composite mats BG particles (Schott Vitryxx®, size 2μm) have been homogeneously dispersed (20wt% respect to PCL) in the polymer solution before electrospinning. For the electrospinning process the solution was fed with a flow rate of 0.4 mL/h, the applied voltage was 15kV and the needle-target distance was 11cm. Samples morphology was assessed by SEM observations and ATR-FTIR analysis was used for the assessment of the influence of the solvent in the obtained mats chemical composition and for the evaluation of the presence of BG inside the sample. The mechanical characterization of selected fibrous mats was performed by uniaxial tensile strength test.
Results and Discussion: SEM micrographs showed an homogeneous beads-free fibrous structure, as reported in figure 1A, having an average fiber diameter of 1.2 ±0.1μm.
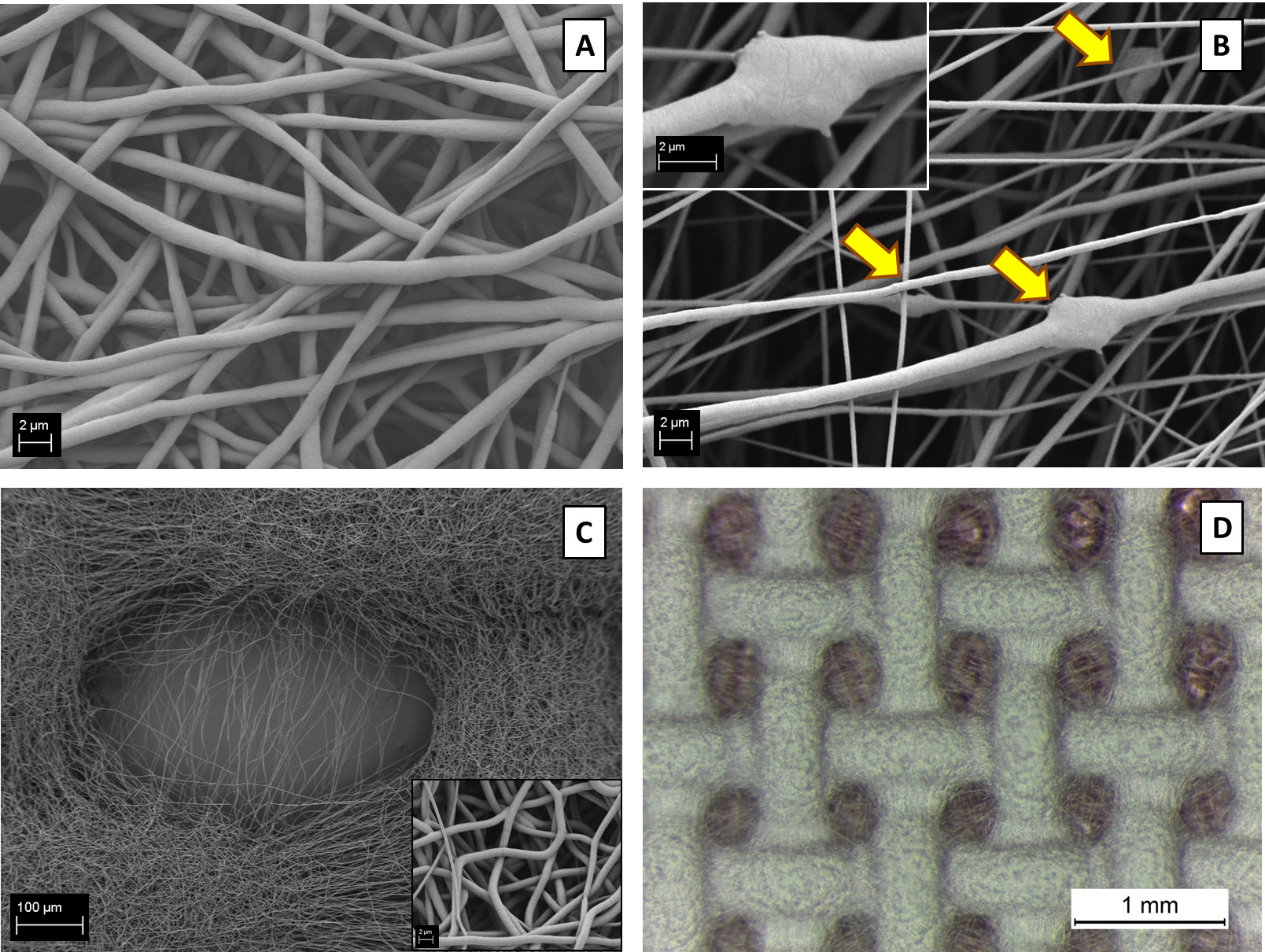
Figure 1: SEM micrographs of electrospun pure PCL random oriented mats (A), electrospun mats of PCL with BG particles (B), PCL electrospun macroporous pattern (C) and light microscope image of PCL macroporous pattern (D).
ATR-FTIR analysis showed the absence of solvent in the electrospun mats, confirming the suitability of the solvent. A composite PCL-BG electrospun beads-free fibrous mat, having an average fiber diameter of 0.6±0.2μm was obtained as reported in figure 1B. A reduction in the average fiber diameter was observed possibly due to the presence of BG particles in the PCL solution. A patterned PCL electrospun mat, containing macroporosity, which could be useful to increase cell adhesion and infiltration inside the electrospun structure was successfully obtained, as showed in figures 1C and 1D, without relevant alteration in the fibers average diameter. It was also observed that when using a patterned target, the duration of the electrospinning process is crucial as it affects the macropore size, as reported in figure 2.
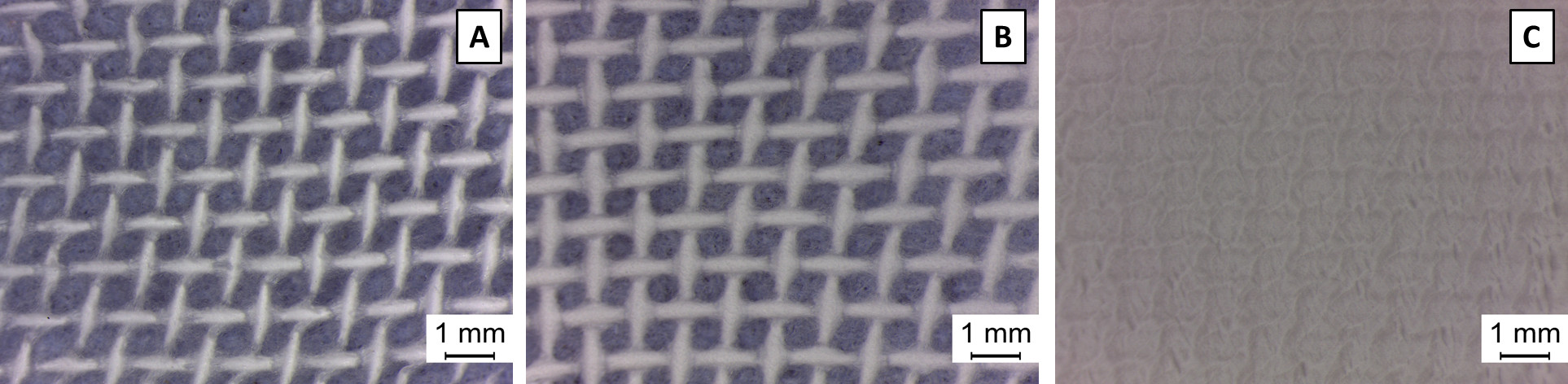
Figure 2: Light microscope images of the electrospun PCL patterned mats, varying the time of the electrospinning process: 15 minutes (A), 30 minutes (B) and 45 minutes (C).
Conclusions: Homogeneous electrospun PCL fibrous mats were obtained with a less toxic solvent. This system has been investigated also for the fabrication of electrospun composite mats and for obtaining electrospun patterned scaffolds. Further works will be focused on the use of the obtained mats as layers of complex multilayered structures with zonal incorporation of BG particles, which are intended for interface tissue engineering applications.
This project has received funding from the European Union’s Horizon 2020 research and innovation programme under the Marie Sklodowska-Curie grant agreement No 657264.
References:
[1] Agarwal S. Polym. Adv. Technol.2011, 22: 372–378
[2] Ferreira JL et al J. Appl. Polym. Sci. 2014, 131: 41068