Introduction: Optimization of the integration of metal with bone is important in a number of clinical applications, including joint replacements and fracture repair. In some situations, it can be difficult to develop a strong bond between bone and metal (i.e. osseointegration), leading to the need for revision surgery. During research to improve osseointegration, it is useful to test new procedures in animal models, and small animals (such as the rat) are ideal in the initial stages of research [1]. In previous works we describe the first rat-specific load-bearing hip joint replacements, created through the use of three-dimensional image analysis, computer-aided design (CAD), and selective laser melting [2]. Although we have our implants to be feasible, several areas for optimization have been identified. Thus, we describe recent advances to our prototypes, particularly in implant stability following installation.
Materials and Methods: A pilot study of partial hip replacement to install components into live rats (n=2; 900g and 500g) was performed. Micro-computed tomography (micro-CT) and X-ray fluoroscopy were performed post-operatively at 1 day, 3 weeks and 12 weeks to evaluate the position of each component within the bone. Imaging revealed evidence of implant migration in one of the two animals, indicating the need for improved press-fit of components into the bone at the time of surgery. A set of eight broaches was created in CAD software (SolidWorks) to allow for incremental widening of the inner femoral cortex. A collar was added to CAD files of our prototype components to improve implant stability post-operatively. New components were printed in 316L stainless steel on a commercial system for 3D additive manufacturing in metal ( AM 125, Renishaw plc). A dental hand tool was used with several polishing stones, rubber wheels and buffing cloths to remove the inherent surface texturing in specific regions of components.
Results: Polishing of the articulating surface of components was improved substantially using dental hand tools over previous hand-polishing methods (Figure 1). Broaches were also selectively polished to leave a rough surface at the bone-metal interface, which can allow for better cutting through the bone (Figure 2).
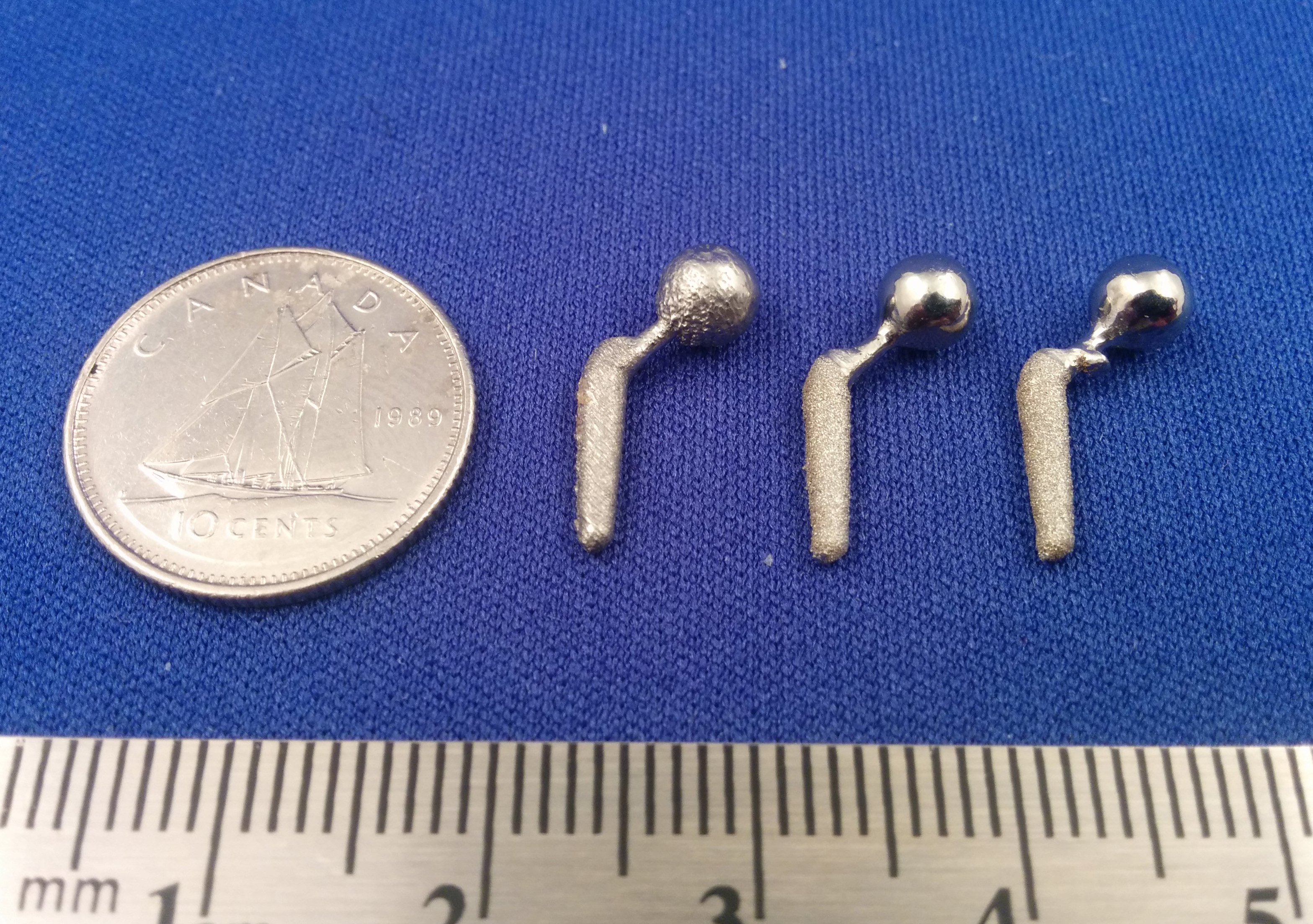
Figure 1: Prototype components showing old and new polishing methods and new collared design.
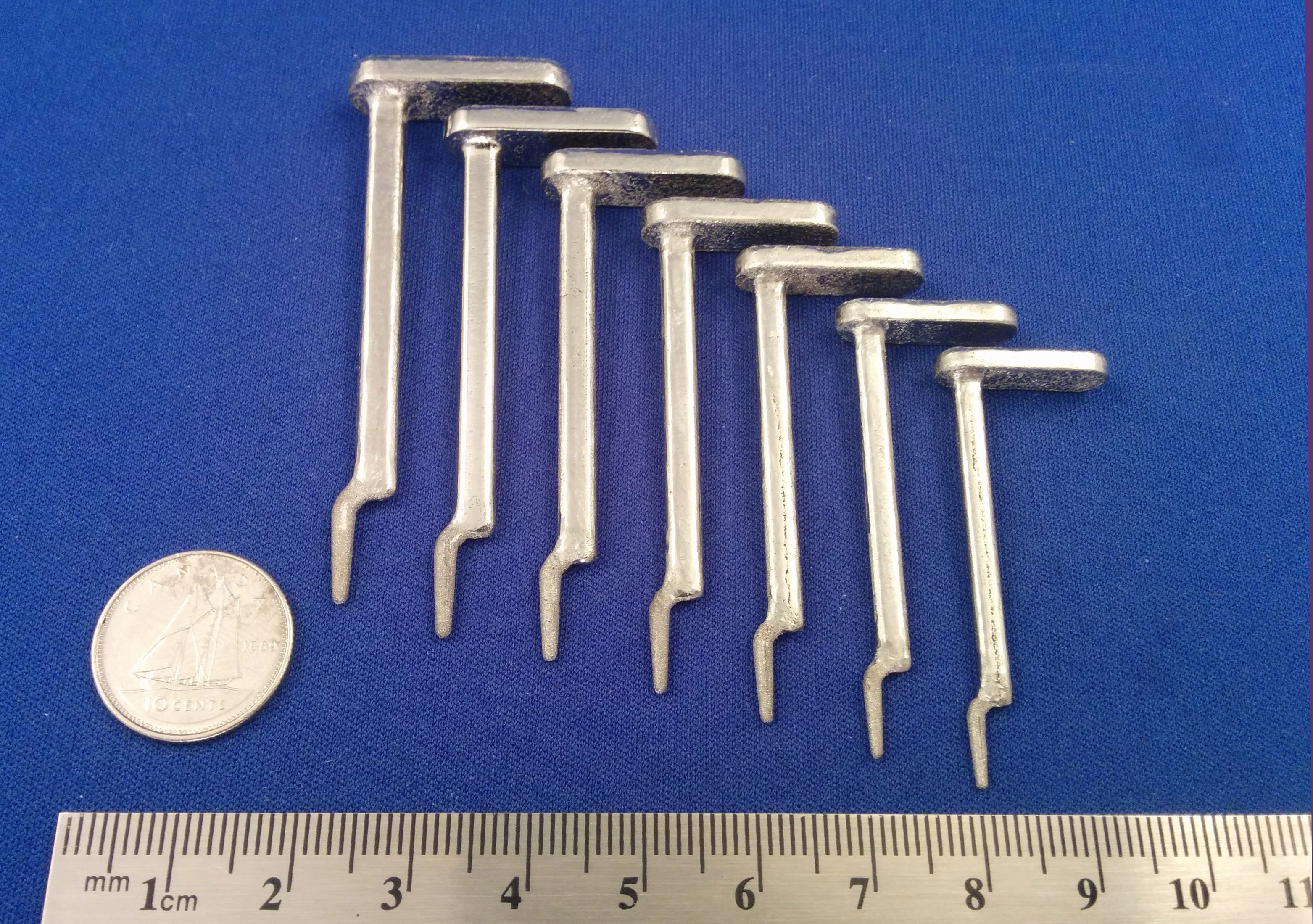
Figure 2: New broaches designed for incrementally widening the rat inner femoral cortex before implants are press-fit into the bone.
Discussion: We expect that our new collared prototype rat hip implant will increase implant stability post-operatively compared to the non-collared component, since the collar can prevent migration of the implant into the femur. However, a live animal study will be needed to determine whether a collar will allow implant position to be maintained longitudinally with greater stability than non-collared components. The effectiveness of the press-fit approach using our custom broaches must also be determined via live animal studies. Future works will also include studies that investigate different surface preparations and porosities on the stem of implants, to optimize osseointegration at the bone-metal interface.
We would like to thank Milko Lamos for his assistance with implant and broach polishing.; We would like to thank Alexander J Kopacz for his assistance with CAD modelling.; This project was supported in part by a Transdisciplinary Bone & Joint Training Award from the Collaborative Training Program in Musculoskeletal Health Research at Western University.; Funding for this project was provided in part through the Internal Research Fund at the Lawson Health Research Institute.; This project was supported in part by a Strategic Training Initiative in Health Research Award through the Canadian Institutes of Health Research and the Joint Motion Program (JuMP).
References:
[1] Powers, D.L., B. Claassen, and J. Black, The rat as an animal model for total hip replacement arthroplasty. J Invest Surg, 1995. 8(5): p. 349-62.
[2] Adam D.M. Paish H.N. Nikolov, I.D. Welch, D.W. Holdsworth. Image-based design of a rat hip prosthesis. Canadian Student Health Research Forum. 2015-06-03.