Introduction: Laser microcutting is the most widely used method for stent manufacturing in the industry[1]. It is by now an established process for more common permanent stent materials, namely stainless steel and Co-Cr alloys[2]. Concerning Mg alloys, the process yields different limitations due to low melting point, high reactivity and viscosity in the molten phase[3]. Resultantly, maintaining correct mesh geometry, surface quality and chemical integrity becomes critical. In this work, conventional and novel stent manufacturing methods are evaluated for biodegradable Mg stent.
Materials and Methods: Tubular and flat specimens of AZ31 Mg alloy were used. Laser stent cutting was employed using conventional method involving a proximity head with a process gas (e.g. Ar, He, N2) using continuous wave (CW), nanosecond and femtosecond lasers with emission wavelengths in near infrared region (λ=1064-1550 nm). As novel cutting methods submerged and remote cutting methods were employed. Submerged cutting was applied with a ns-pulsed laser with green emission wavelength (λ=532 nm) and different cutting liquids namely pure water, water-ethanol solution and lubricant oil. Remote cutting was applied with a galvanometric scanner coupled to ps-pulsed laser with emission wavelength that could be regulated in visible and UV range (λ=355-532 nm). Results were compared in terms of dross formation, kerf width and geometry.
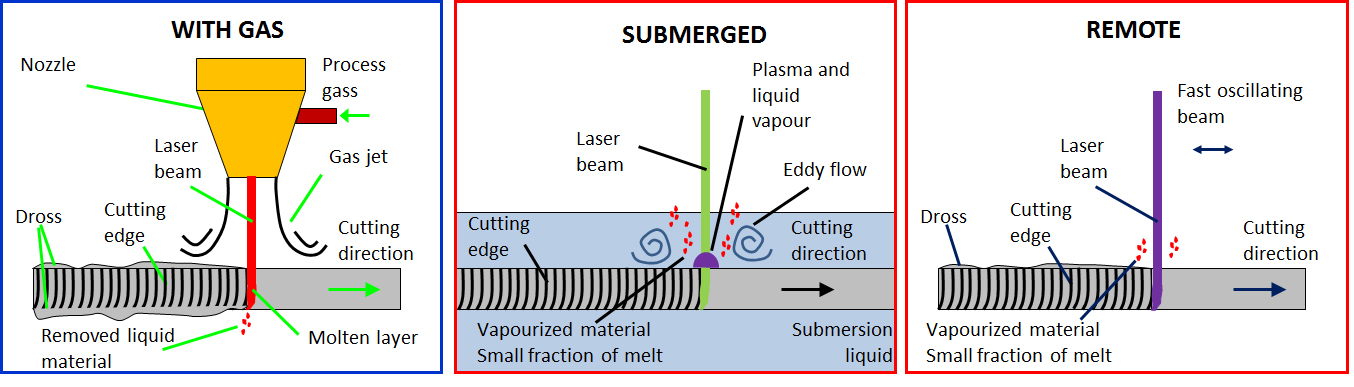
Fig.1. Schematic representation of different laser microcutting methods.
Results: In conventional laser microcutting, the results show that CW lasers generate a large amount of dross that is difficult to remove via a consecutive chemical etching process. The cut quality of ns-pulsed laser is at an acceptable level, whereas the fs-pulsed source shows the best cut quality. Using water-ethanol solution submerged cutting with the ns-pulsed laser produced cut quality comparable to fs-pulsed cutting. Finally, remote cutting provided clean but larger kerfs.
Discussion: Within conventional cutting options, fs-pulsed laser stands out as the best option. This is due to the fact that this option provides ease of cleaning in the consecutive chemical and electrochemical processes, despite lower productivity compared to CW laser. Both submerged and remote cutting option require more developments in order to be able to cut stably on tubular precursors.
Conclusions: This work provides an extended view of different laser microcutting strategies on Mg alloys. The laser microcutting quality can be further improved through the control of pulse profile and pulse train shaping. The combination of laser cutting method to new stent design strategies (e.g. origami and flat) should be further investigated to explore new possibilities in manufacturing sequences.
The authors would like to acknowledge a prestigious NSERC PostDoctoral Fellowship awarded to Agung Purnama.
References:
[1] A.K. Dubey, V. Yadava, Laser beam machining—A review, International Journal of Machine Tools & Manufacture 48 (2008) 609–628
[2] A. Raval, A. Choubey, C. Engineer, D. Kothwala, Development and assessment of 316LVM cardiovascular stents, Materials Science and Engineering A 386 (2004) 331–343
[3] A.G. Demir, B. Previtali, C.A. Biffi, Fibre Laser Cutting and Chemical Etching of AZ31 for Manufacturing Biodegradable Stents, Advances in Materials Science and Engineering 2013 (2013) 692635, 11 pp