Introduction: Ti-29Nb-13Ta-4.6Zr (TNTZ), which is one of metastable beta-type Ti alloys, was recently developed as a representative biomedical Ti alloy for next generation[1]. As-solutionized TNTZ has a low elastic modulus less than 60 GPa close to that of cortical bone along with very low cytotoxicity and good bone biocompatibility. Solution treatment and aging (STA) is a typical heat treatment for improving the mechanical properties of alpha/beta- and beta-type Ti alloys. However, STA also drastically increases the elastic modulus. Therefore, this study investigated the effects of fine particle bombarding (FPB) or friction stir processing (FSP) on the mechanical properties of TNTZ in order to maintain a relatively low elastic modulus. The bone contact characteristics of TNTZ samples subjected to FPB along with mirror surface and cancellous bone were also compared.
Experimental Methods: This study used cold-swaged TNTZ bars (working ratio: around 94%), which was designated as TNTZSW. TNTZSW was solutionized at 1063 K for 3.6 ks in a vacuum followed by water quenching (WQ); it was designated as TNTZST. Some samples of TNTZSW were aged at 573 to 723 K in under aging conditions. Mechanical surface modification process by a fine particle bombarding (FPB) machine was applied to some samples of TNTZSW and TNTZST; these specimens were designated as TNTZSW/FPB and TNTZST/FPB, respectively. Another surface modification by a friction stir processing (FSP) was also done to some samples of TNTZST; these specimens were designated as TNTZST/FSP. Optical microscopy (OM), scanning electron microscopy (SEM), and X-ray diffraction (XRD) spectroscopy were carried out on each specimen to evaluate the microstructure. The Vickers hardness, elastic modulus, and the tensile and fatigue properties were investigated for each specimen to examine the mechanical properties. For the bone contact characteristics, some cylinder-type samples of TNTZSW/FPB and TNTZSW with mirror surface were implanted into the femurs of Japanese white rabbits. All samples were extracted 12 weeks after implantation. The bone contacts were evaluated by image analysis.
Results and Discussion: Figure 1 shows Vickers hardness and Young’s modulus profiles from very edge of samples of TNTZSW/FPB and TNTZST/FPB to around 300 μm in depth. The Vickers hardness of the very edges for TNTZSW/FPB and TNTZST/FPB shows much higher value, which is Hv 270 and Hv 235, respectively), and it tends to decrease drastically as a function of distance from the surface to a depth of around 20 μm. The trend was similar to that of Young’s modulus. The change in the Vickers hardness and Young’s modulus of TNTZST/FSP was almost similar to that of TNTZST/FPB, although the microstructure near specimen surface after FSP showed very fine single beta phase with some alpha precipitates.
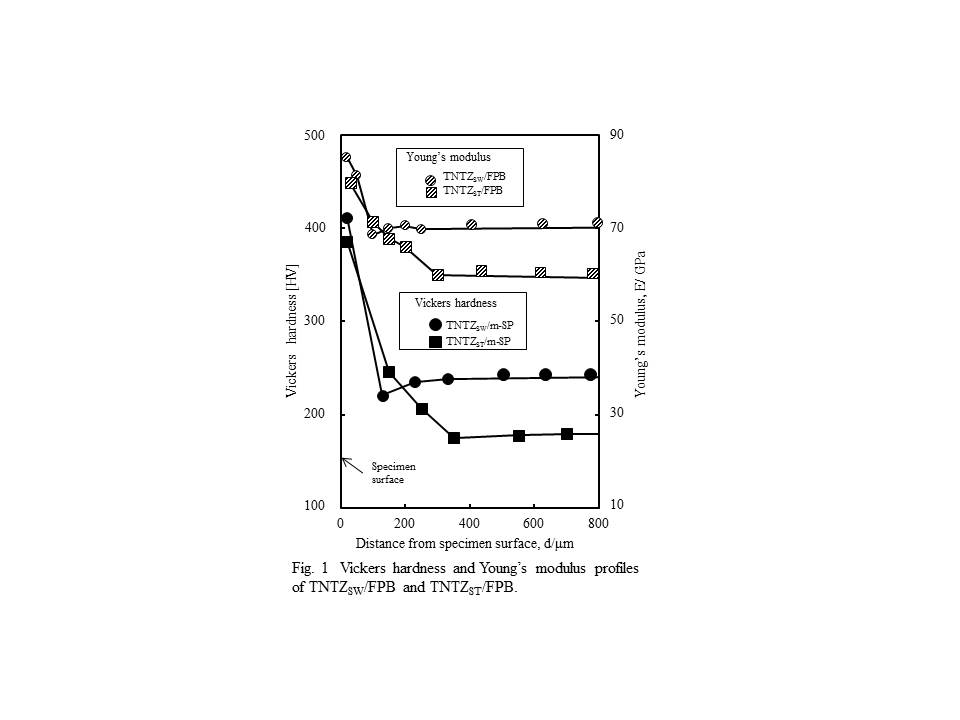
The fatigue strength of TNTZSW/FPB increases especially in the high cycle fatigue life region as shown in Fig. 2. The fatigue limit of TNTZSW/FPB is around 400 MPa and around 100 MPa higher than that of TNTZSW. The Vickers hardness near the surface of the TNTZSW/FPB specimen was around 200 Hv higher than that at the center of specimen, as noted above. As a result, the effect of residual compressive stress by FPB was marked in the high cycle fatigue life region.
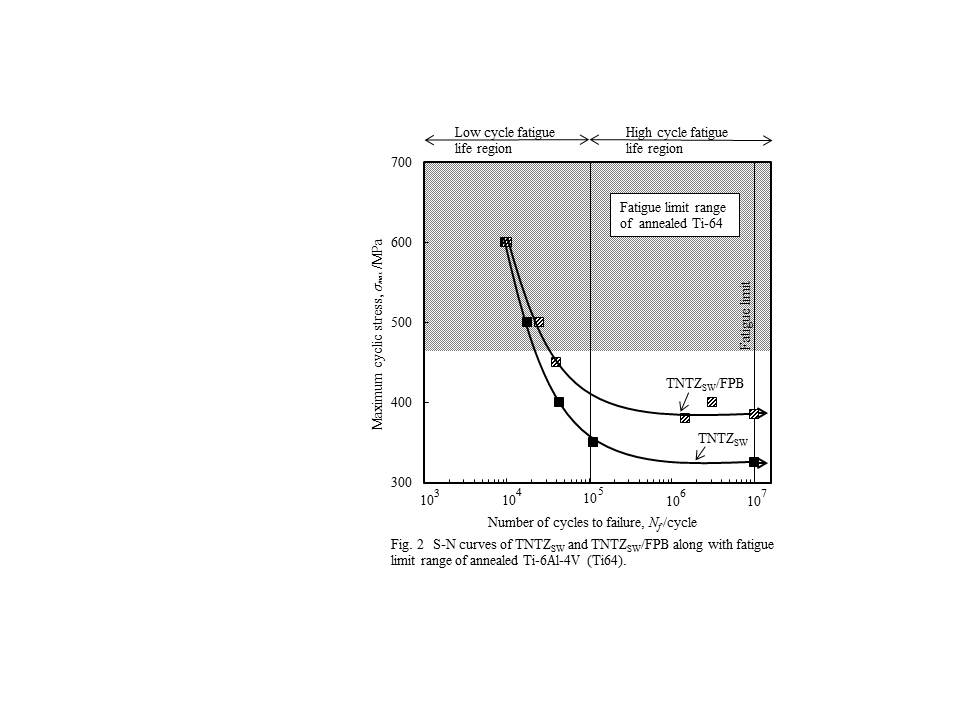
In animal tests, TNTZSW/FPB had the highest bone contact ratio among the three kinds of samples, although the bone formation ratios of the three were almost the same.
Conclusions: 1) The Vickers hardness of cold-swaged TNTZ subjected to fine particle bombarding (FPB) was significantly increased within 20 μm from the very edge of the specimen surface.
2) The fatigue strength of TNTZSW subjected to FPB increased espesially in the high cycle fatigue life region. The fatigue limit was around 400 MPa.
3) The bone contact ratio of TNTZ subjected toFPB was better than that of TNTZ with the mirror surface.
References:
[1] T. Akahori, M. Niinomi, H. Fukui, and A. Suzuki: Materials Transactions, Vol. 45, No. 5 (2004), 1540-1548.