Introduction: Biomaterials engineering in bone implant and osseointegration is one of the most demanding fields in medical and surgical industries; facing a critical challenge with biocompatibility of materials used[1]. This research investigates the creation of nano porous structures across surface of titanium using Nd:YAG Pulsed laser system, specifically for biocompatibility enhancement purposes. Using laser surface nano texturing, biocompatibility of titanium is enhanced by induction of pre-designed patterns across the surface, and creation of porous structures with nano roughness outside the irradiated areas.
Materials and Methods: Titanium is the most commonly used material in implant applications; hence, this study uses thin sheets of titanium. Pre-designed line patterns are induced upon the surface of the titanium using laser pulses with varying frequencies, and constant power of 10 W. Effects of laser frequency upon creation of nano porous structures on untreated area are closely examined using scanning electron microscopy (SEM).
The treated samples are next immersed in simulated body fluid (SBF) for two weeks. The effects of these structures on biocompatibility of titanium are then investigated by comparing the bone-like apatite inducing ability across various sections of titanium surface. Using energy dispersive x-ray (EDX), appearance of key elements responsive to biocompatibility of titanium is inspected.
Results and Discussion: Fig. 1(a, b, c) displays the nano porous structure created outside of ablated zone of titanium sheets.
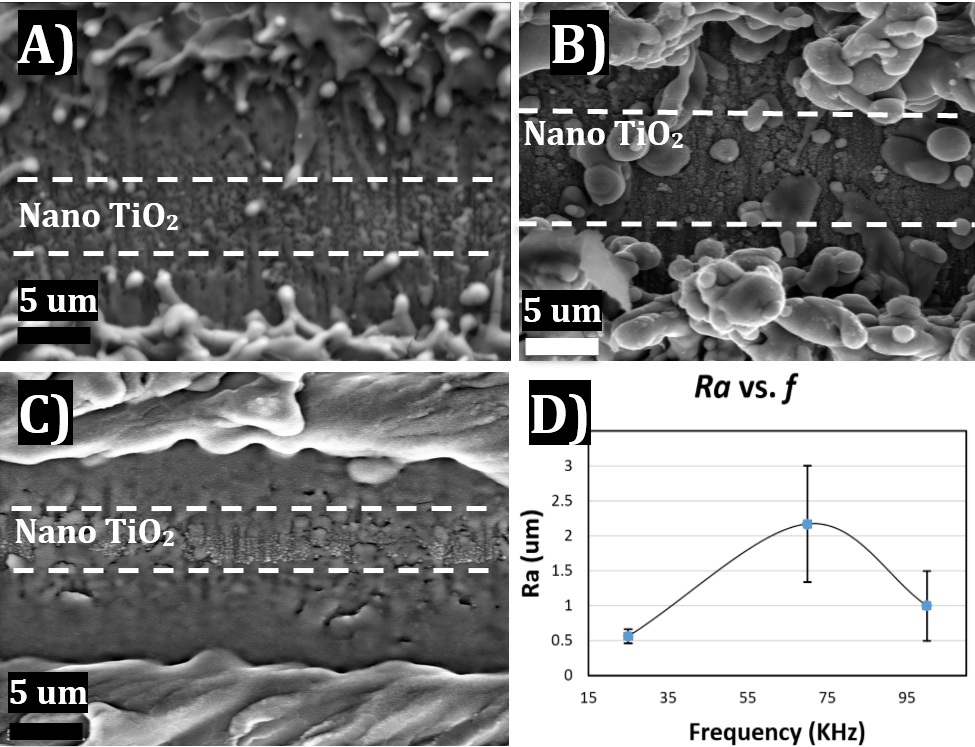
Comparing the three frequencies, the nano porous structures appear more developed at frequency of 70 KHz (higher roughness), while frequency of 25 KHz results in smallest areas of this structure (Fig. 1 (d))
During laser irradiation, a plume with radial surface tension caused by the temperature gradient, is created. The plume is consisted of nanoparticles, ions, and clusters[2]. Following the irradiation, a high cooling rate caused by extreme temperature difference between laser plume and the titanium causes rapid re-solidification of the ablated material. As a result, the tension within the laser plume causes shooting of nanoparticles to periphery of irradiated zones. Re-solidification of the deposited nanoparticles creates the nano porous structures observed[3].
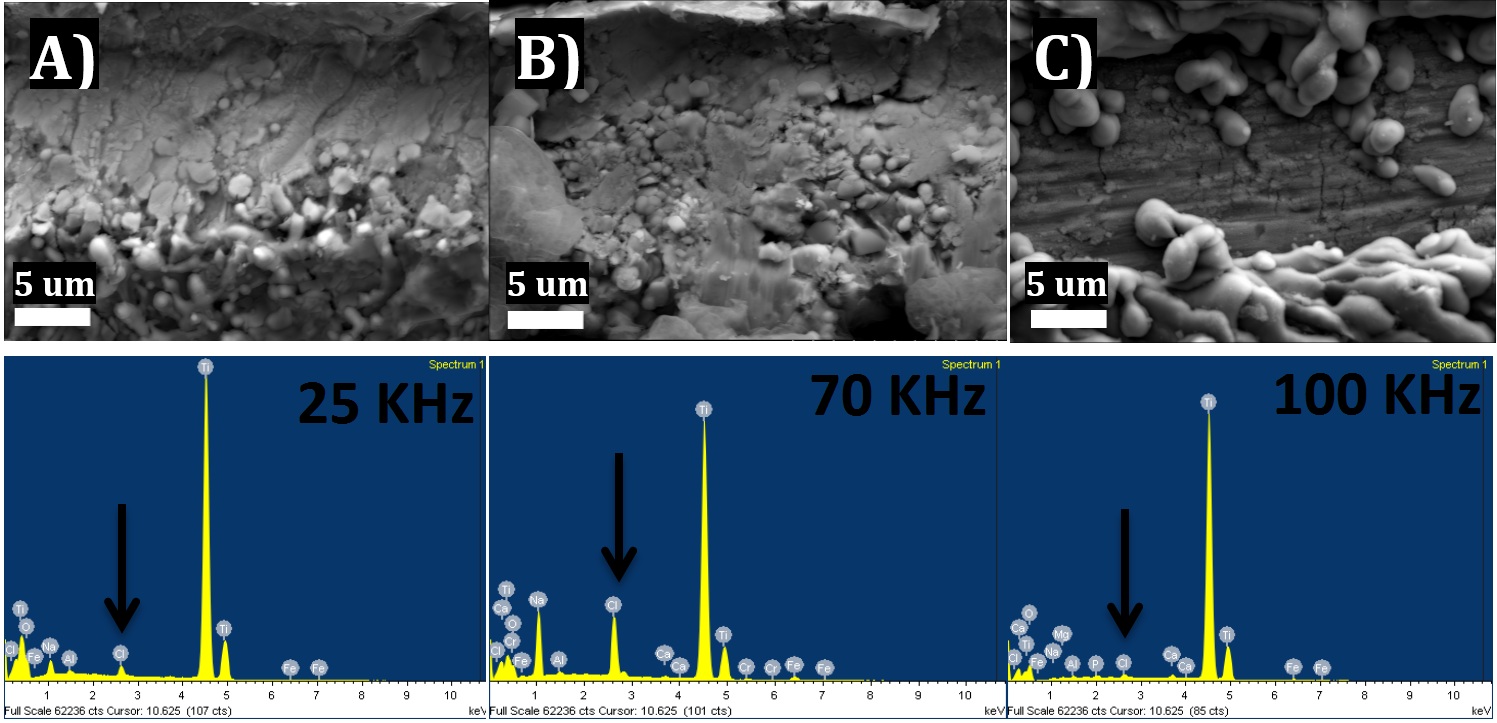
In Figure 2, the effects of these structures on the biocompatibility of the titanium are examined. According to the EDX maps, the amount of bone-type apatite elements is highest at frequency of 70 KHz. Although more ablation occurs at 100 KHz, less apatite is induced at this frequency. Due to the extreme surface temperature at a frequency of 100 KHz, upon bonding to the surface, the deposited nanoparticles go through fusion process and re-solidify as different structures, and hence less nano porous structure is observed at this frequency. Consequently, this causes a lower cell attachment rate[4].
Conclusion: In this study, the effects of frequency on creation of nano porous structures outside of irradiation zone on surface of titanium are investigated. Upon completion of experiments, it is observed that frequency of 70 KHz creates the most optimum condition for creation of these structures; which in return increases the cell attachment rate and biocompatibility of titanium.
Natural Sciences & Engineering research Council of Canada (NSERC); New Brunswick Innovation Foundation (NBIF)
References:
[1] E. Saiz, E. A. Zimmermann, J. S. Lee, U. G. K. Wegst, and A. P. Tomsia. “Perspective on the Role of Nanotechnology in Bone Tissue Engineering”. Dental Materials, Vol. 29, pp. 103-115. 2013
[2] A. Y. Vorobyev, and C. Guo. “Direct Femtosecond Laser Surface Nano/Micro structuring and its Applications”. Laser Photonics Reviews, Vol. 3, Issue 3. pp. 385-407. 2013.
[3] T. H. Qazi, D. J. Mooney, M. Pumberger, S. Geibler, and G. Duda. “Biomaterials Based Strategies for Skeletal Muscle Tissue Engineering: Existing technologies and Future Trends. Biomaterials. Vol. 53, pp. 502-521. 2015
[4] M. Trtica, B. Gakovic, D. Batani, T. Desai, P. Panjan, B. Radak, Applied Surface Sciences. 2006